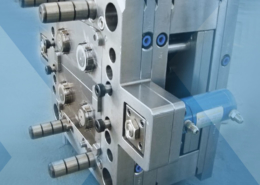
How to manage risks and opportunities during maybe the worst-ever PP
Author:gly Date: 2024-09-30
Timely Delivery: Committing to efficient project management to meet delivery schedules supporting clients’ production timelines.
With a portfolio that includes 240 precision injection molds and operations spanning four countries, Marlee – Texen is equipped to handle diverse project requirements. The company emphasizes collaboration and customization, working closely with clients to develop products that meet rigorous medical standards.
Stephen has been with PlasticsToday and its preceding publications Modern Plastics and Injection Molding since 1992, throughout this time based in the Asia Pacific region, including stints in Japan, Australia, and his current location Singapore. His current beat focuses on automotive. Stephen is an avid folding bicycle rider, often taking his bike on overseas business trips, and is a proud dachshund owner.
Marlee – Texen’s capabilities span various project sizes and complexities. The company’s facilities are designed to accommodate the manufacture of detailed components, specialized medical devices, and customized plastic parts. This flexibility is supported by a rigorous process that includes:
The material, which is reinforced with 20 percent micro glass beads, exhibits isotropic shrinkage and a minimized tendency to warpage. This means that the fuel filler flap fits in perfectly with the rear fender. “This gives it the edge over polyamide blends, which are less dimensionally stable due to the tendency of polyamide to absorb water,” says Theiler.
Fitchburg, Massachusetts, Feb. 06, 2024 (GLOBE NEWSWIRE) -- Marlee – Texen, recognized for its expertise in plastic injection molding, announces its continued focus on providing specialized services for the Healthcare/Medical sector. As a provider of injection-molded plastics and medical devices, Marlee – Texen combines technical precision with a deep understanding of the healthcare industry’s needs to offer solutions that address specific challenges.
Manufacturing Precision: Utilizing state-of-the-art equipment and strict quality control measures to maintain high production standards.
The PBT compound was given preference over a blend of polyphenylene ether and polyamide (PPE+PA). “Our material is less expensive and exhibits comparable performance when it comes to surface quality, paintability, and mechanical properties. In addition, it is suitable for electrostatic painting. It is also paintable online, which means that it can pass through all painting steps together with the vehicle body without any further outlay. This also contributes to cost-effective production,” says Dr. Stefan Theiler, who is an expert in plastic exterior parts in application development in the Lanxess High Performance Materials (HPM) business division. The plastic vehicle body component was jointly developed by Skoda, a Tier 1 parts supplier and Lanxess.
Customized compounds based on polybutylene terephthalate (PBT) can be a cost-effective alternative to high-performance thermoplastics in the production of fuel filler flaps. This can be seen in the new Skoda Scala, for example, whose fuel filler flap is made from Pocan B5221XF from materials supplier Lanxess.
Design Collaboration: Working with clients to refine product designs, ensuring they meet functional and regulatory requirements.
The toughness of the PBT compound from Lanxess is yet another advantage, making the fuel filler flap highly robust against mechanical deformation (e.g. in the event of vandalism). Theiler: “Gasoline and diesel thieves will find it really hard to prise the flap open, even if they use force.”
Pocan B5221XF can be processed at lower temperatures than (PPE+PA) blends. Its high flowability makes it easier to realize complex or large component geometries. “In addition to fuel filler flaps, we also envisage our material being used for exterior body parts such as spoilers and other components designed to improve vehicle aerodynamics as well as in antenna covers, flaps for electric vehicles and mirror housings,” says Theiler.
For additional information about Marlee – Texen and its injection molding services for the healthcare sector, visit https://www.marlee-texen.com/.
Another advantage of the PBT material is its high resistance to short-term temperatures. The heat distortion temperature as per ISO 75-1,-2 (HDT/B, 0.45 MPa) is 165°C, which means that the fuel filler flap can withstand the high temperatures that arise during both cathodic dip coating of the vehicle body and the drying steps of the painting process. As a result, the component can pass through the entire painting line together with the vehicle body (online painting). “This helps to cut costs during painting and in the logistics processes,” says Theiler. By contrast, mineral-filled PBT or PA compounds – which are also used for manufacturing fuel filler flaps – are not compatible with cathodic dip coating processes.
Pocan B5221XF (Xtreme Flow) has been optimized to ensure good paintability and paint adhesion. Depending on the tool, smooth surfaces without unsightly sink marks can be achieved (Class A surface). The material is also suitable for electrostatic painting. When it comes to paint adhesion, standard OEM requirements – such as those defined in delivery regulations TL 211 from Volkswagen and DBL5416 from Daimler – are fulfilled. The paint layers adhere firmly to the plastic surface and can withstand the usual adhesion tests such as the cross-cut test to DIN EN ISO 2409 and steam-jet test to DIN EN ISO 16925.
Marlee – Texen’s approach to injection molding in the healthcare sector is rooted in its commitment to technical excellence and innovation. The company’s engineers and technicians utilize advanced technology to achieve high precision and quality, which is critical for medical device manufacturing.
Customization is at the core of Marlee – Texen’s services. By engaging in a collaborative process with clients, the company ensures that the final products are technically sound and aligned with the client’s specific needs. This partnership approach allows for the development of tailored solutions, from initial concept to production.
Class A-surface, outstanding mechanical properties, and a cost-effective alternative to high-performance thermoplastics.
Efficiency and Cost Management: Optimizing production processes to reduce waste and control costs without compromising quality.
Marlee – Texen’s product range reflects its commitment to the Healthcare/Medical industry, offering surgical instruments, diagnostic equipment, and other medical devices. Each product is developed to emphasize functionality, durability, and patient safety.
Through its engineering service HiAnt, Lanxess provided Skoda with comprehensive support in the development of the fuel filler flap. Under this brand, HPM has combined its expertise in material, application, process and technological development. For the fuel filler flap, for example, HPM conducted mold flow and warpage simulations in order to achieve the best-possible tool design and optimize the production process. Theiler: “Our aims here included correctly positioning the cooling ducts in the injection molding tool, defining the ideal parameters for tool tempering and calculating the optimum melting temperature.” In addition, HPM simulated critical load cases during component testing, such as the forceful opening of a sealed fuel filler flap in a body drop test. During the sampling process and start of series production, processing experts from HPM went directly to the injection molders and gave them recommendations for process parameters, reworking the tool (e.g. regarding gating and cooling system) and ventilation.
GETTING A QUOTE WITH LK-MOULD IS FREE AND SIMPLE.
FIND MORE OF OUR SERVICES:
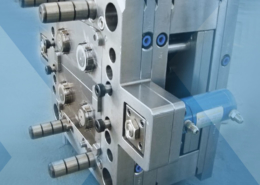
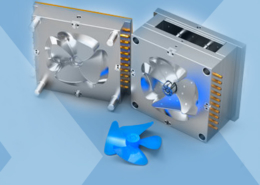
Plastic Molding

Rapid Prototyping
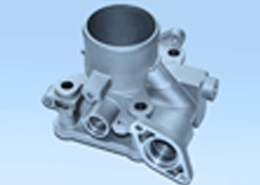
Pressure Die Casting
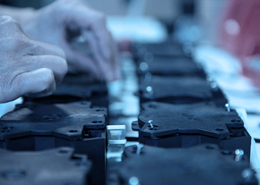
Parts Assembly
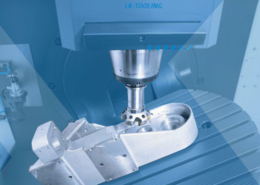