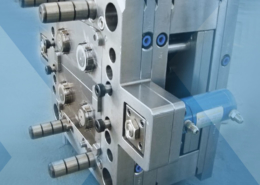
How To Make Custom Silicone Ear Molds for Your In-Ear Monitors - custom soft pla
Author:gly Date: 2024-09-30
84 countries and 60k+ stakeholders strong, SPE unites plastics professionals worldwide – helping them succeed and strengthening their skills through networking, events, training, and knowledge sharing. For more information, visit www.4spe.org.
3Dnatives is the largest international online media platform on 3D printing and its applications. With its in-depth analysis of the market, 3Dnatives gets over 1 million unique visitors per month and is currently available in English, French, Spanish, German, Italian. 3Dnatives works with key Additive Manufacturing market players and offers a variety of services such as a 3D printing price comparison engine, B2B consulting and B2B brand content, event management and much more!
SPE Middle East Office N. ESO:14, Desk 34 Sheikh Rashid Tower, Seventh Floor Dubai World Trade Center P.O. Box 9204 Dubai, UAE
Dave Rheinheimer has 40 years of experience in thermoforming, working in all aspects of the industry including sales, production, product design, operations management, mold shop management and more. Throughout his career, Dave’s focus has been on improving designs and processing of thermoformed tooling and parts. Dave started his own thermoforming company, Majestic Formed Plastics, which was acquired by Duo Form in 2009. Dave currently leads the development of new products and improved products at Duo Form.
At the blackboard in school - the large one-metre ruler in hand: many have already had contact with the products of Wissner GmbH. The company is also a technological innovation and has created its own recycling material, Re-Wood. It is processed on injection moulding machines from the KraussMaffei CX series with standard plasticising.
Clay Guillory is a mechanical engineer with extensive experience in additive manufacturing, pellet extrusion 3D printing and CNC machining. Clay founded Titan Robotics in 2014, specializing in large-format 3D printer manufacturing and launching the Titan pellet extrusion and hybrid additive and subtractive systems. After the acquisition of Titan Robotics by 3D Systems in April 2022, Clay now leads the Titan branch of 3D Systems’ Application Innovation Group, expanding and developing new solutions for production additive manufacturing for industrial customers.
As a direct result, there has been a growing interest in adopting local, flexible manufacturing. Which is why more and more manufacturers are turning to additive manufacturing (AM) to create quality, cost-efficient products faster. One notable example is plastic thermoforming companies like Duo Form who have discovered how to leverage large-format extrusion 3D printing using low-cost plastic pellets to gain a competitive edge. They are producing medium-to-large-sized thermoforming molds in less than half the time, and at a fraction of the cost compared to traditional mold-making methods.
To learn more about this, join the next SPE live webinar “Reduce Costs And Lead Times For Large Thermoforming Molds With Ext Titan Pellet 3D Printers” on 3D printing large production molds for thermoforming with experts from 3D Systems and Duo Form on October 24 at 9:00 AM-10:00 AM EDT. Attendees will be able to learn more about how Duo Form has integrated AM into their manufacturing process, gaining agility by 3D printing production molds, tools and representative samples for thermoforming and vacuum forming.
Due to its 80% wood content, Re-Wood has different physical properties than pure plastics. Nevertheless, it can be processed in a standard plasticising process without any adjustments to the screw geometry or non-return valve. One thing in particular should be noted for the injection parameters: Re-Wood does not shrink - so care should be taken when reprinting.
Over the past few years, we have seen a number of growing supply chain pressures. Starting of course with the COVID-19 pandemic wherein suddenly not only were crucial products running out quickly due to increased demand, but there were also a number of shortages just due to the nature of the crisis. Indeed, it has continued through 2023 notably due to exacerbations related to the Russian Invasion of Ukraine with some statistics showing that up to 80% of companies experienced at least one disruption. This is equally the case in the United States.
Compare Desktop 3D Printers Compare Professional 3D Printers Compare 3D Scanners 3D Printing Directory Choose a 3D printer 3D Printing Directory Event Board Job Board Newsletter Advertising
Bradley Mount is a 25-year veteran of additive manufacturing, including multiple plastic and metal AM solutions. Brad, as a technology sales and operations executive, has worked with hundreds of companies, enabling their successful adoption of additive manufacturing to address specific business, engineering, and manufacturing challenges. He now leads 3D Systems – Titan business development as Global Director.
Nino Pecina is a robotics programmer and CAD engineer at Duo Form with 10 years of experience in the thermoforming industry. With three years of experience working with 3D printers and five years in tool and mold making, Nino currently operates the Titan pellet extrusion 3D printer at Duo Form to 3D print large molds and other parts as part of Duo Form’s manufacturing process.
Unlike real wood, Re-Wood building blocks can withstand cleaning in the dishwasher, they are very strong, almost infinitely durable and, if they do wear out, can be recycled again and again. Wissner even takes back Re-Wood products that are no longer needed. Building blocks & co. can be coated using drum coating, for example, and printing is also possible. Wissner also processes Re-Plastic, which consists of 100% recycled post-consumer waste.
German SMEs are family-run, think in terms of generations and are committed to sustainability. This coincides with the interests of parents. They want their children's products to be natural, durable and, above all, safe to use. Wissner GmbH (Bensheim, Germany) combines everything: its teaching materials and games are mainly made from Re-Wood, a recycled material developed in-house. No additional trees have to be felled for it, as it is based on regional wood flour. Combined with a binder, either recycled plastic or biopolymer, Wissner brings it to granulate size and to the injection moulding machines - all CX from KraussMaffei with clamping forces of 500 to 1,300 kN.
In addition to its own products, such as the number game “Hexagon”, Wissner also offers its expertise to major players in the games industry. The industry as a whole is currently endeavouring to relocate production processes from South East Asia back to Europe. For example, the well-known Halma men are now available in Re-Wood in the special colors purple and natural. A total of 80% of Wissner's turnover comes from abroad. The pricing must therefore also be attractive for less affluent regions. The efficient processing of the future material Re-Wood on the CX machines is the prerequisite for this.
When the company began developing Re-Wood around ten years ago, the focus was on regional raw materials, environmentally friendly production, freedom from harmful substances and durability. It also had to be stable and saliva-proof - after all, the products are also intended for small children. Given the company's history, combining wood and plastic was an almost logical step, as Wissner started out as a joinery in 1976, followed later by plastics processing, and in 2007 the first CX machines from KraussMaffei moved in. Around 25 employees produce items such as geometric solids, slide rules and peg cubes. The traditional focus is on teaching materials for schools and kindergartens, with the games sector becoming increasingly important.
GETTING A QUOTE WITH LK-MOULD IS FREE AND SIMPLE.
FIND MORE OF OUR SERVICES:
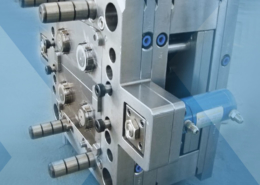
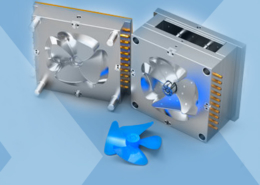
Plastic Molding

Rapid Prototyping
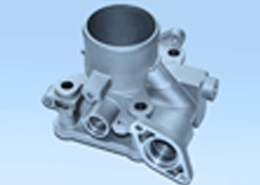
Pressure Die Casting
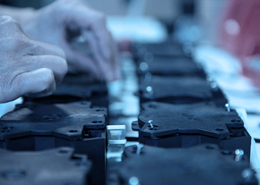
Parts Assembly
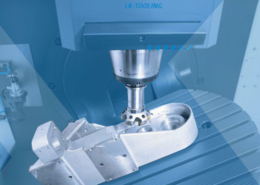