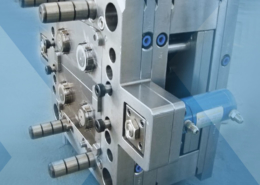
How to Build Your Own Injection Molding Machine - plastic molding electrical
Author:gly Date: 2024-09-30
"Expertise in tool design is fundamental to our core competences within Trelleborg Sealing Solutions," emphasizes Jarno. "Developing the two-color process required additional considerations during the design and construction of the tool to make sure the flow of the clear and the colored material portions must be kept strictly separated.
Toray Advanced Materials Korea Inc. plans to increase annual production capacity for Torelina polyphenylene sulfide (PPS) resin by 5,000 tonnes at a plant in Gunsan, Korea, from December 2024. The Toray Group’s combined PPS manufacturing capacity at this facility and the Tokai Plant in Aichi Prefecture, Japan, will thereby rise to a world-leading 32,600 tonnes/year.
Ursula Nollenberger, Product Line Director for LSR Components at Trelleborg Sealing Solutions, says: "Our first application of this revolutionary technology is for a leading automotive tier-one supplier. The company was looking for a solution to visually differentiate geometrically identical parts that Trelleborg produces off a single tool for various vehicle platforms, without impacting the overall aesthetics of the finished product. This new process offered an ideal solution that was both practical and cost-effective."
Toray Advanced Materials Korea will supply PPS resin not consumed domestically to Toray Group compounding sites in the United States, China, Europe, Southeast Asia, and other regions as part of an effort to expand its global business.
Toray Industries and Idemitsu Kosan are teaming up to produce biomass-derived styrenic resin, while Toray is adding capacity for PPS engineering resin.
A concurrent move will be to expand production of sodium hydrogen sulfide, a key raw material for PPS resin. Toray would thereby solidify its position as a cost-competitive, integrated manufacturer of everything from raw materials through resins.
Stephen has been with PlasticsToday and its preceding publications Modern Plastics and Injection Molding since 1992, throughout this time based in the Asia Pacific region, including stints in Japan, Australia, and his current location Singapore. His current beat focuses on automotive. Stephen is an avid folding bicycle rider, often taking his bike on overseas business trips, and is a proud dachshund owner.
The process involves the two components of LSR raw material being mixed in a ratio of 1:1. On the way into the injection tool, this homogenous mass is then divided. Color is added via an additional mixing unit to one part of the volume stream and injected into the tool cavity via a proprietary valve design. Simultaneously, the colorless material is being injected via a second stream.
Jarno Burkhardt, General Manager of the Trelleborg Sealing Solutions European center of excellence for LSR component solutions in Stein am Rhein, Switzerland, comments: "The advantage of the two-colored LSR components to our customer, as well as to the OEM they supply, is that it gives, without adding significant extra cost, product traceability. The beauty of the novel tool design is that it will allow an unlimited number of color combinations from a single machine, in a single tool and in one single shot."
"This novel technology can be applied to any size and number of cavities per tool. Depending on part geometry and size as well as production capacity needed, we construct tools anywhere between 1 and 128 cavities with possibilities even beyond," adds Nollenberger.
Toray Group is a comprehensive manufacturer of PPS not just for compounds but also for films and fibers. It is the world’s largest player in this field.
The two-color injection molding process has been simplified through a development at Trelleborg Sealing Solutions (Stuttgart, Germany) that employs a single shot and a single tool to manufacture partially colored liquid silicone rubber (LSR) components. Utilizing an innovative and proprietary tool construction, the process has the capability to add color pigment to part of the transparent silicone material stream just prior to its injection into the tool cavity.
Japan’s Toray Industries and Idemitsu Kosan plan to develop a supply chain for acrylonitrile-butadiene-styrene (ABS) resin based on biomass styrene monomer derived from biomass naphtha. Idemitsu will leverage the mass balance method to manufacture biomass styrene monomer that will be fed to Toray’s Chiba plant for polymerization of biomass-derived ABS resin starting in October this year. Both Idemitsu and Toray are striving to achieve carbon neutrality by 2050.
The two-color injection molding process has been simplified through a development at Trelleborg Sealing Solutions (Stuttgart, Germany) that employs a single shot and a single tool to manufacture partially colored liquid silicone rubber (LSR) components. Utilizing an innovative and proprietary tool construction, the process has the capability to add color pigment to part of the transparent silicone material stream just prior to its injection into the tool cavity.
Toray’s ABS resin is used in a variety of industries such as automotive, consumer electronics, and medical devices, for which it offers transparent grades.
PPS resin is a high-performance engineering plastic. Key benefits are heat and chemical resistance, mechanical strength, and flame retardance. Applications include electrical components, electric vehicles, electrical and electronic devices, and housing-related parts. Applications continue to broaden. Toray decided to boost capacity at Toray Advanced Materials Korea to cater to a projected 6% growth in annual global demand for PPS resin compounds.
GETTING A QUOTE WITH LK-MOULD IS FREE AND SIMPLE.
FIND MORE OF OUR SERVICES:
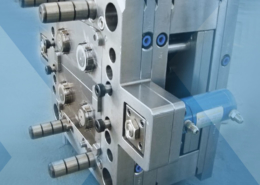
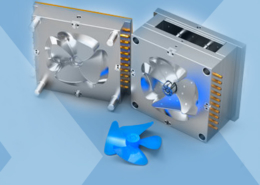
Plastic Molding

Rapid Prototyping
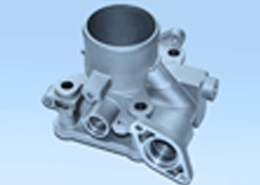
Pressure Die Casting
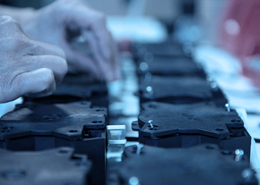
Parts Assembly
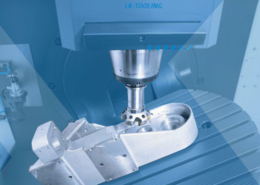