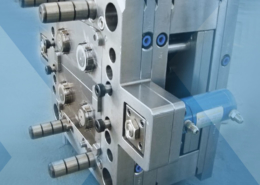
How to Achieve Quality ABS Parts at Scale With Additive Manufacturing? - large s
Author:gly Date: 2024-09-30
The compatibility of the two resins had some challenges due to their similar melting temperatures. They bonded well with each other, but the second resin could melt and blend into the first resin, leaving a marbled look which we did not want. Working with the resin manufacturer’s and adjusting the molding process we were able to overcome that. Another issue to keep in mind when matching a part to a two-shot press is considering barrel sizes. The amount of each resin must match the barrel size for each injection unit. This makes it hard to match multiple parts to the same press. This is a reason using a side unit with an existing press is sometimes more economical and gives you more options when trying to utilize your press capacity.
One solution to the automation challenge facing moulders today could be production cells like this one, but they will require a highly integrated control system.
Process data gathered through these connections can be used support the machine learning that is necessary for simplified no-code programming discussed previously. But there’s more to it than that. Collecting and analysing huge amounts of process and performance data from all components in the cell – including IMMs – regardless of the type of device or its manufacturer. This makes it possible to recognise patterns and predict equipment and process events and outcomes. Eventually, this will enable robots to actually adjust themselves and optimise process behavior and outcomes automatically. These kinds of capabilities will prove essential as moulders work to maximise equipment and plant effectiveness, leading to increased productivity and profitability.
Machine Design reached out to John Hanninen, senior engineer of new business development at C&J Industries, to learn about the process, its advantages and its challenges.
A robot (or more than one) makes it possible to do more value-additive operations right at the moulding machine, placing inserts before moulding, enabling efficient overmoulding and retaining control of parts through post-mould operations and even into final packaging. With everything done in one manufacturing cell, there is no need to ship parts to and from warehouses for secondary processing. Automation limits processing variables and decreases errors and defects too.
Various resin manufacturers have developed materials specifically for two-shot molding to achieve an adhesive or chemical bond between the rigid and soft resins. Working with them would be an important step for a successful design. If two resin are needed that are not meant to chemically bond to each other, then you must design in a mechanical bond feature to be able to mold a successful part.
MD: Can you provide examples of real-world applications or case studies where this process resulted in significant improvements or innovations for your customer(s)?
Robotic automation is also important in the production of parts that have delicate surface features, are comprised of softer materials, and/or have critical dimensions that must be maintained during the moulding process. Any uncontrolled interaction with humans can damage a part or decrease its quality. Many medical or high-end electronic parts are particularly susceptible to contamination through human interaction, so automation is essential.
The Sepro stand (Hall 12, stand A36) at Messe Dusseldorf will feature three operating moulding machines, five robots and a range of other peripheral equipment, all operating in cells that highlight advances that injection moulders can use to overcome today’s toughest challenges. The moulding cells will employ a new modular software architecture that enables the control of multiple pieces of robotic and auxiliary equipment via a single central control system. They will be interactive and visitors will be encouraged to take control of Sepro robots and see for themselves how easy-to-use these systems can be. At the same time, Sepro engineers will be watching carefully to see how people respond and react to these technical novelties so that this feedback can be used to help focus development efforts as they continue in the years to come.
As Machine Design’s technical editor, Sharon Spielman produces content for the brand’s focus audience—design and multidisciplinary engineers. Her beat includes 3D printing/CAD; mechanical and motion systems, with an emphasis on pneumatics and linear motion; automation; robotics; and CNC machining.
For all of the benefits that robotic automation offers injection moulders – including, but not limited to, those delineated above -- there have been some impediments that have limited more widespread implementation. Chief among these is the fact that programming and operating a robot can be technically complicated. Some 20 years ago, Sepro pioneered easier robot programming with its Visual controller, which includes a Simple Pick & Place feature. Even a relatively new employee with limited training could use this system to set up a basic mould-release cycle.
If there is a bright side to this situation, it is almost certainly this: not since the Industrial Revolution – the so-called Industry 3.0 – has technology brought to bear such a large arsenal of weapons to overcome these challenges. The automation weapons of today (Industry 4.0) are digital and they allow moulders an unprecedented level of control over their equipment, their process and their operational efficiency. Best of all, this same technology is getting much easier to implement, meaning that the lack of skilled technicians need not be an impediment.
Secondary assembly operations or separate over-molding or insert molding of the first part can be eliminated. It also reduces handling of parts like you would have with over molding, which increases WIP and potential of part damage or contamination that you avoid with two-shot molding.
JH: The initial resin or first shot is usually a rigid material such as ABS, polypropylene, nylon, etc. The second resin is usually soft resin like a thermoplastic elastomer or silicone-type material. Common items like hand tools with soft grips and even toothbrushes all take advantage of the two-shot process. It can also combine two rigid resins allowing multiple-colored parts like a headlight or taillight with opaque, clear and amber or red variations all in one component.
MD: Does the two-shot process enhance the quality and durability of the final product compared to other molding techniques? If so, how?
JH: The upfront tooling costs for two-shot molding can be significantly more than conventional molding, so an analysis of the return on investment (ROI) would be important. Does the product require a second resin? The part design must fit within one of the several methods used for two-shot molding, so before a design is started you need to know the difference between them. Are the resins compatible? Do you need them to bond together or are you creating an assembly? Depending on the resins you select, some resins chemically bond well together while other resins may require that mechanical bonds are designed in to better hold the two different resins together.
JH: The tooling and equipment can be much more complex, so the setup takes longer. You are dealing with basically two molds with one side attached to a rotary platen. A robot will come in and pick and place the first shot into the second side. Does the mold have an internal core pull, a shuttle action or maybe a lift and rotate mechanism built in? Do you need air, hydraulics or servos tied into the press controls? The presses have the software built in to integrate the injection units together, so the actual injection set up is the same as a single component mold but with separate screens for each injection unit.
The human-machine interface will be getting simpler too, borrowing from smartphones, video-game controllers and other devices that the current generation of operators and technicians are already familiar and comfortable with.
Automation, a word that was coined by Ford Motor Company in 1948, will a major theme when K 2022 opens its doors in Dusseldorf in October. For injection moulders, the industrial robot, the icon of automation, will be front and center. They won’t look much different than they did at the global plastics trade show three years ago, or even ten years ago, but what they can do and how they can interface with moulding machines and peripheral equipment of all kinds will be wonderful to behold.
MD: Tell me about the resin materials used in two-shot injection molding, and how does the selection of materials impact the overall product design?
JH: The primary advantage is cost savings from producing a completed two-shot or two-component product every machine cycle. You can usually get better quality with better adhesion between the two resins and better matching of the second core or cavity to the first part since it stays in the mold, so the aesthetics are improved. More than one color is possible.
Injection moulders today face more serious challenges to success than ever in recent memory. There is heightened pressure to ramp up production levels to meet rising demand even as the resources to do so are limited. The shortage of even non-skilled workers, not to mention those with technical knowledge and experience, became especially acute during the Covid-19 pandemic, and has not improved much since. Supply-chain issues have made it difficult and/or expensive for moulders to increase production capacity even as plant-floor space constraints limit their potential to expand. All this, while profitability concerns place a premium on increased quality and efficiency.
JH: Our press uses parallel injection units and a rotary machine platen. Our design had to consider the part staying on the core and rotating 180 deg. over to the other side. The product design needed to allow gate locations that are on top of each other. The shut-off surfaces between the first-shot part and the second cavity had to be considered. The second cavity must squeeze an area of the first part with enough pressure to prevent the second shot resin from leaking out creating flash. That contact area can leave a visible mark on the part that needed to be considered.
Machine Design: I understand that two-shot molding is something C&J Industries has recently taken on. Can you tell me about that decision, including how the company went about selecting its 220-ton Nissei two-shot press?
Going forward we will buy a unit(s) that fits the application we are awarded. There are various options depending on the program whether we buy another two-shot press or buy a side unit that can be used on our existing presses to do two-shot molding. Two-shot molding is very dependent on the part size and shot size required for each material and matching the part to the press size required.
MD: Can you explain the key considerations to keep in mind when designing parts for a two-shot injection molding process?
JH: It has eliminated secondary assembly and bonding of the parts together, saving costs and improving the overall part quality. It has helped with part consolidation resulting in reduced cost and lead time to market.
JH: With so many variables in design and materials it is very important if you are thinking about designing a part that could potentially be molded as a two-shot part to have your molder in design discussions from the very beginning.
MD: In what ways does the two-shot injection molding process contribute to cost-efficiency and sustainability in manufacturing?
John Hanninen: Over the years we have had many instances of having to turn jobs away that required two-shot capabilities. To gain experience, management decided to pursue an internal project and after searching around, it was decided a good used press would be purchased. The Nissei was selected to match up with our two-shot coaster.
As part of our Pre-K pull-out special in the latest edition of British Plastics & Rubber, Charles de Forges, CEO of Sepro Group, discusses how robotics for injection moulding will be a huge attraction to visitors to K 2022 - and beyond.
Think about the current labour issues. For moulders having difficulty finding skilled operators, process engineers, or maintenance technicians, automation can almost certainly help increase productivity, efficiency and quality. Automation almost always works faster and occupies less floor space than a manual operation. Robotic systems also can operate 24/7 and can offer a consistency that manual operation cannot. The added consistency in cycle time not only improves product quality, but also can help more accurately identify operating costs and forecast production output. Automation can help moulders become more competitive in almost any market.
Sepro Group, a leader in injection moulding automation for over 40 years, is again breaking new ground in the area of robot and automation control. Their work in recent years and their vision for the future of robotics focus, in particular, on two areas that have the potential to help moulders meet their current challenges. They are:
JH: Instead of paying for two separate injection molding processes run sequentially, you pay for two injection molding processes run in parallel. Each time the mold cycles you get a complete part, cutting the manufacturing process time nearly in half saving man and machine hours.
Sepro began connecting its controls with other systems more than ten years ago, when it started partnering with major injection-machine makers to allow virtually seamless integration of the robot and IMM. This connectivity has been improved and extended so that, today, Sepro Visual controls readily communicate with moulding machines and also manage the operation of all the other peripheral equipment (mentioned above) that comprise a truly integrated moulding cell.
Spielman has more than three decades of experience as a writer and editor for a range of B2B brands, including those that cover machine design; electrical design and manufacturing; interconnection technology; food and beverage manufacturing; process heating and cooling; finishing; and package converting.
MD: Does the tooling and equipment setup differ for two-shot injection molding compared to conventional molding processes? Please explain.
MD: What challenges or limitations did you encounter when implementing a two-shot molding approach? How were these overcome?
The decision to invest in a 220-ton Nissei two-shot press was a strategic move made by C&J Industries, Meadville, Pa., to expand its capabilities. The selection of this press was a deliberate internal project aimed at gaining experience in this specialized process. By matching the press with its two-shot coaster, the company addressed the growing demand for products that require two-shot capabilities.
Today, Sepro engineers are working toward what they call “no-code” programming, with the robot controller using artificial intelligence (AI) to recognise process details and help fill in the blanks to complete a final operational sequence. The controller will be able to communicate with all the equipment in a production cell including the IMM, robot(s) and peripherals that perform secondary functions like assembly, marking, packaging, and so on.
JH: While the final quality of a two-shot part compared to an over-molded part can be similar, the benefit comes from scrap rates and machine capacity. You may run through more parts in the over-molding process to get the same amount of quality parts that you would get with two-shot molding.
GETTING A QUOTE WITH LK-MOULD IS FREE AND SIMPLE.
FIND MORE OF OUR SERVICES:
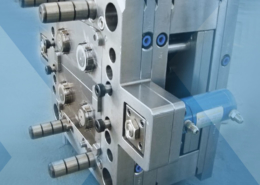
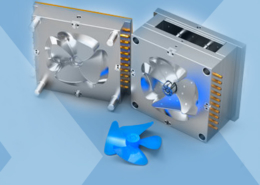
Plastic Molding

Rapid Prototyping
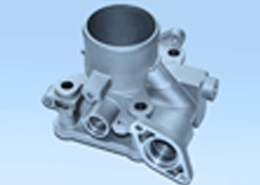
Pressure Die Casting
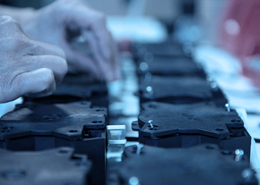
Parts Assembly
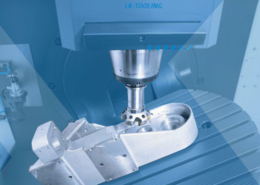