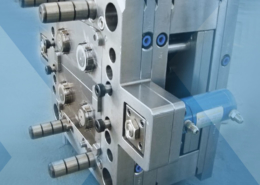
How Lego makes its bricks (photos) - abs plastic molding at home
Author:gly Date: 2024-09-30
Mainland China was the largest consumer of MMA at 30% of global consumption in 2022. In the last five years, the MMA market has been heavily defined and influenced by: the global automobile and construction industries, older versus newer MMA technologies, raw material shortages, new MMA trade flows (especially from Saudi Arabia exports), new MMA capacity in mainland China, the COVID-19 pandemic, increases in global PMMA sheet production and consumption (for example sneeze guards), the conflict in Ukraine (including geopolitical instability) and high inflation.
What they developed was Mantle’s Trueshape technology. It starts with the company’s proprietary Flowable Metal Paste printing materials (inspired by Connor’s silver pastes), which mimic existing standard tool steels once the printing process is completed. The pastes are used to print a rough version of the tool being made using an extrusion-based print head. While the part is still in the printer, it’s shaped via a more standard machining process using a high-speed cutting tool to deliver the tight tolerances and fine surface finishes required. “We’ve broken the problem down into a very specific set of steps,” said Sorom. “We know what material has to be removed, because we put it there.”
Paul DiLaura, Chief Commercial Officer, was at 3D printing company Carbon when it released its first products, and he built the sales and applications engineering teams from the ground up.
From a production standpoint, the process offers distinct advantages over the current standard of CNC (computer numeric control) machining for tool production. That fully subtractive method results in substantial material waste and added cost, and it’s extremely time-consuming. “We’ve taken a process that’s extremely costly and requires multiple steps, and collapsed it into a single machine,” Sorom said.
S&P Global’s Chemical Economics Handbook – Methyl Methacrylate is the comprehensive and trusted guide for anyone seeking information on this industry. This latest report details global and regional information, including
PMMA accounted for close to two-thirds of global consumption of MMA. Acrylic surface coatings and other uses accounted for the remainder.
S&P Global’s Chemical Economics Handbook – Methyl Methacrylate has been compiled using primary interviews with key suppliers and organizations, and leading representatives from the industry in combination with S&P Global’s unparalleled access to upstream and downstream market intelligence and expert insights into industry dynamics, trade, and economics.
“The first several years, we focused on understanding the requirements–the materials and surface finishes–and developing the technology,” said DiLaura. “We wanted ours to be proven to be differentiated, and we didn’t want to come out with something that wasn’t fully formed.” Now as the company begins ramping up for full commercialization, with its first full-scale systems expected to ship in early 2022, its co-founders see ample opportunities. “One nice thing about tooling is that the requirements are similar whether you’re making a bottle cap or a surgical device,” DiLaura added. “We’re able to address a wide range of products across industries because we focus on the tooling.”
Meanwhile, they also see themselves helping solve some other big problems. “We want to help bring back industry from overseas,” Sorom said. “Billions of dollars in tooling is needed each year in the U.S., and more than 25% is currently imported from overseas. Pretty much every customer we talk to is talking about reshoring. And we know our technology can help address the skilled labor shortage as well.”
Mantle has worked with a number of parts producers to evaluate and validate its materials and technology, including Tessy Plastics and a global medical device manufacturer. Tessy has run over 400,000 cycles using Mantle-produced tooling, with the parts produced meeting all quality standards. The medical device company was able to reduce the cost of a prototype tool development by 65% while cutting its development time from twelve to four weeks.
Obtain the data you need to make the most informed decisions by accessing our extensive portfolio of information, analytics, and expertise. Sign in to the product or service center of your choice.
Methyl methacrylate (MMA) is widely used in large amounts for the production of polymethyl methacrylate (PMMA), which is used in applications such as cast and extruded sheet and resins (PMMA pellets) for injection molding and extrusion products. MMA is also used extensively in acrylic surface coatings (acrylic latexes and enamels) and adhesives. Other important applications for MMA include impact modification and acrylic processing aids; emulsion polymers principally for paper, textiles, leather and floor polishes; mineral-filled sheet; polyesters; and polymer concrete.
The company’s executive team members bring a set of experiences that were critical to what Mantle has developed. “The impetus is from where I started,” said Ted Sorom, the company’s CEO. “I worked in a design and manufacturing facility that made underwater equipment and consumer products. I ended up as CTO, and was responsible for the tools we used to make hundreds of metal and plastic parts.” He brought the knowledge of the difficulties of design and production of those tools.
Steve Connor, Mantle’s Chief Science Officer, brought materials and tech know-how from his background as a chemist from the solar industry, where he developed silver pastes used to coat the back of photovoltaic panels. “He wasn’t excited about that as an industry, but that focus was a match for what we do–high-precision parts, with tens of microns accuracy,” said Sorom.
In the future, though, they see the focus shifting. “Long-term, we don’t want to be a tooling company,” said Sorom. “We want to be a 3D printing company. We chose the tooling application specifically to build our business case. A potential future customer could be a manufacturer with older production machines that need replacement parts. Other metal 3D printers can’t make parts that will plug right into the machine to get it back up and running. Our parts can. We see a future where 60% of our business is in tooling, and 40% is in other applications like that.”
Mantle, a metal 3D printing startup based in San Francisco, offers a solution. By focusing on the tools, molds and dies needed for high-volume parts production, the company has developed proprietary materials and a combined 3D printing and machining platform to deliver production tooling that has the required tolerances and surface finish without the need for post-processing. In doing so, they’ve dramatically cut both the time and cost of tool development and fabrication. Today the company announced the closing of its Series B funding round, which raised $25 million and brought Mantle’s total funding to $41.5 million.
I’ve written extensively about the rise of 3D printing and its use in countless applications for both production tools and equipment, and finished parts and products. The technology has many benefits, but also has shortcomings in both areas. For finished parts, it’s too slow for many mass-production applications, so most experts admit it’s never going to replace legacy technologies like injection molding. For tooling, its tolerances and surface finishes often lead to the need for post-production processes that add time, cost and complexity.
The other advantage comes from Mantle’s production software. It takes the CAD file for a tool, including CAD files developed for the legacy processing methods, and automatically creates the toolpaths for printing and shaping. That eliminates the specialized and time-consuming CNC programming that’s required for the subtractive process.
GETTING A QUOTE WITH LK-MOULD IS FREE AND SIMPLE.
FIND MORE OF OUR SERVICES:
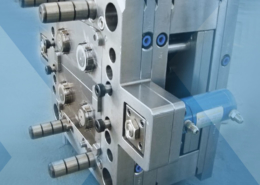
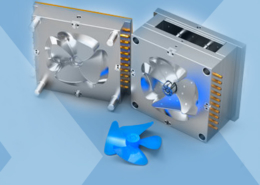
Plastic Molding

Rapid Prototyping
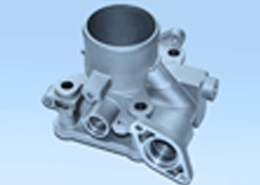
Pressure Die Casting
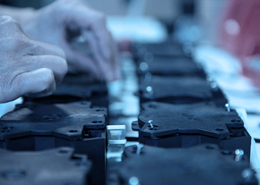
Parts Assembly
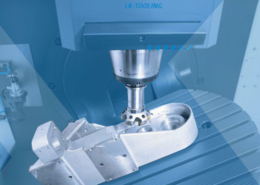