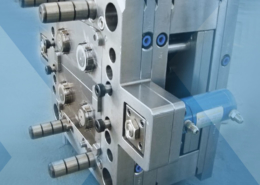
How gaming miniatures are made, from sculpt to table - hard plastic molds
Author:gly Date: 2024-09-30
In this collection of content, we provide expert advice on welding from some of the leading authorities in the field, with tips on such matters as controls, as well as insights on how to solve common problems in welding.
Discover how artifical intelligence is revolutionizing plastics processing. Hear from industry experts on the future impact of AI on your operations and envision a fully interconnected plant.
Second quarter started with price hikes in PE and the four volume engineering resins, but relatively stable pricing was largely expected by the quarter’s end.
Processors with sustainability goals or mandates have a number of ways to reach their goals. Biopolymers are among them.
Gifted with extraordinary technical know how and an authoritative yet plain English writing style, in this collection of articles Fattori offers his insights on a variety of molding-related topics that are bound to make your days on the production floor go a little bit better.
technotrans says climate protection, energy efficiency and customization will be key discussion topics at PTXPO as it displays its protemp flow 6 ultrasonic eco and the teco cs 90t 9.1 TCUs.
In this collection of articles, two of the industry’s foremost authorities on screw design — Jim Frankand and Mark Spalding — offer their sage advice on screw design...what works, what doesn’t, and what to look for when things start going wrong.
Ultradent's entry of its Umbrella cheek retractor took home the awards for Technical Sophistication and Achievement in Economics and Efficiency at PTXPO.
Introduced by Zeiger and Spark Industries at the PTXPO, the nozzle is designed for maximum heat transfer and uniformity with a continuous taper for self cleaning.
Despite price increase nominations going into second quarter, it appeared there was potential for generally flat pricing with the exception of a major downward correction for PP.
Successfully starting or restarting an injection molding machine is less about ticking boxes on a rote checklist and more about individually assessing each processing scenario and its unique variables.
Resin drying is a crucial, but often-misunderstood area. This collection includes details on why and what you need to dry, how to specify a dryer, and best practices.
Multiple speakers at Molding 2023 will address the ways simulation can impact material substitution decisions, process profitability and simplification of mold design.
Today, the company can injection mold 38-mm closures from PHA in a 5.5-second cycle from a 16-cavity tool. Key advances that made this possible include specialized tooling, with added attention to venting, from moldmaker Dauntless Industries Inc., Covina, California; a custom screw from Robert Barr Inc., Onsted, Michigan; and a unique hot runner design from an as-yet unnamed supplier.
In a time where sustainability is no longer just a buzzword, the food and beverage packaging industry is required to be at the forefront of this innovation. By adopting circular packaging processes and solutions, producers can meet regulatory requirements while also satisfying consumer demand and enhancing brand reputation. Join Husky to learn more about the broader implications of the circular economy — as well as how leading brands are leveraging this opportunity to reduce costs, increase design flexibility and boost product differentiation. Agenda: The cost and operational benefits of embracing circularity Key materials in circular packaging — including rPET and emerging bioplastics How to design a circular food and beverage package Strategies for selecting sustainable closures to future-proof packaging solutions Optimization and streamlining of production processes for enhanced efficiency How Husky Technologies can enable your sustainable success
To obtain an optimal bonding of the nylon to the fiber, the new matrix systems require a suitable carbon-fiber surface treatment. According to Dr. Hubert Jager, head of technology and innovation at SGL, “It is only with a custom-formulated finish that optimal bonding can form and the carbon fibers transmit their unique stiffness and strength properties fully to the part.”
The Plastics Industry Association (PLASTICS) has released final figures for NPE2024: The Plastics Show (May 6-10; Orlando) that officially make it the largest ever NPE in several key metrics.
Implementing a production monitoring system as the foundation of a ‘smart factory’ is about integrating people with new technology as much as it is about integrating machines and computers. Here are tips from a company that has gone through the process.
The Tier One automotive supplier with compounding and blowmolding machine capabilities adds the 50-yr-old molder and moldmaker.
In this collection, which is part one of a series representing some of John’s finest work, we present you with five articles that we think you will refer to time and again as you look to solve problems, cut cycle times and improve the quality of the parts you mold.
August 29-30 in Minneapolis all things injection molding and moldmaking will be happening at the Hyatt Regency — check out who’s speaking on what topics today.
Sustainability continues to dominate new additives technology, but upping performance is also evident. Most of the new additives have been targeted to commodity resins and particularly polyolefins.
Take a deep dive into all of the various aspects of part quoting to ensure you’ve got all the bases—as in costs—covered before preparing your customer’s quote for services.
Many of PHA’s strengths are also potential challenges to its processing and end-use application. Pinczuk notes that the material can be as soft as an amorphous rubber or as hard as a crystalline acrylic, depending on formulation and its temperature profile in processing. In its development work, Beyond Plastic began with a single-cavity closure tool as it sought to identify PHA’s shrink ratio. It molded caps, compensated for shrink and then formulated a new compound based on its findings, which it then tested in production.
In this cell, the goal is to compression mold PHA caps, and then separate 5% of that production, which will be reground into flake and mixed with PET and other scrap. Next, the demonstration cell will use an infrared, 3D flake analyzer provided by Eagle Vizion, Sherbrooke, Quebec to identify and separate the PHA scrap, which will be reintroduced back to the compression molding machine. The aim here is to show that in a mixed-waste stream, PHA is readily identifiable and can be reclaimed for recycled content in new.
Second quarter started with price hikes in PE and the four volume engineering resins, but relatively stable pricing was largely expected by the quarter’s end.
After proving out the viability of injection molding PHA closures, Beyond Plastic has shifted gears to using compression molding to produce the bioplastic caps. Partnering with Chinese firm Tech-Long Packaging Machinery Co. Ltd., Beyond Plastic took rush delivery of a machine, receiving the unit in three weeks. Since then, it has disassembled and reassembled portions of the system as it modifies the unit to process PHA. It is currently “dialing in” materials, according to Pinczuk, working toward a goal of creating a 24-cavity compression molding demonstration cell that can run traditional HDPE and PP, as well as PHA, all under one platform.
Processors with sustainability goals or mandates have a number of ways to reach their goals. Biopolymers are among them.
Mixed in among thought leaders from leading suppliers to injection molders and mold makers at the 2023 Molding and MoldMaking conferences will be molders and toolmakers themselves.
Exhibitors and presenters at the plastics show emphasized 3D printing as a complement and aid to more traditional production processes.
“With PHA, you have to reteach people rheology and processing,” Pinczuk says. “They have to think differently. If you did petrochemical resins your whole life, you must rethink rheology and how you process. Let go of those habits and really understand the limitations — PHA is shear sensitive; it doesn’t like high temperatures; and it will degrade if you don’t process properly.”
Beyond Plastic says its injection-molded PHA bottle caps are the first 100% biodegradable closure. Source: Beyond Plastic
The aim of this presentation is to guide you through the factors and the numbers that will help you determine if a robot is a smart investment for your application. Agenda: Why are you considering automation? What problems are you trying to solve? How and why automation can help Crunch the numbers and determine the ROI
KraussMaffei has installations at university labs and tech centers worldwide and estimates that of the 50 FiberForm machines now in production, only a handful are currently overmolding glass mats; the majority are just molding long-glass compounds direct from rovings.
While prices moved up for three of the five commodity resins, there was potential for a flat trajectory for the rest of the third quarter.
Formnext Chicago is an industrial additive manufacturing expo taking place April 8-10, 2025 at McCormick Place in Chicago, Illinois. Formnext Chicago is the second in a series of Formnext events in the U.S. being produced by Mesago Messe Frankfurt, AMT – The Association For Manufacturing Technology, and Gardner Business Media (our publisher).
This Knowledge Center provides an overview of the considerations needed to understand the purchase, operation, and maintenance of a process cooling system.
•One of the most exciting parts was a passenger airbag module housing said to weigh at least 30% less than a current commercial version injection molded from glass-reinforced nylon 6. Now in advanced development in Germany, this project involves Lanxess, Bond-Laminates, KraussMaffei, Takata-Petri AG, and Christian Karl Siebenwurst GmbH. KM’s FiberForm process is used to make the airbag housing from Tepex dynalite 102 RG 600 sheet with 47% continuous glass, overmolded with Lanxess’ Durethan DP BKV 240 H2.0 with 40% short glass. In addition to weight savings, the high strength and stiffness of the sheet composite allowed thinning the sidewalls from 3-4 mm down to 0.5-1 mm.
Join KraussMaffei for an insightful webinar designed for industry professionals, engineers and anyone interested in the manufacturing processes of PVC pipes. This session will provide a comprehensive understanding of the technology behind the production of high-quality PVC pipes: from raw material preparation to final product testing. Agenda: Introduction to PVC extrusion: overview of the basic principles of PVC pipe extrusion — including the process of melting and shaping PVC resin into pipe forms Equipment and machinery: detailed explanation of the key equipment involved — such as extruders, dies and cooling systems — and their roles in the extrusion process Process parameters: insight into the critical process parameters like temperature, pressure and cooling rates that influence the quality and consistency of the final PVC pipes Energy efficiency: examination of ways to save material and energy use when extruding PVC pipe products
August 29-30 in Minneapolis all things injection molding and moldmaking will be happening at the Hyatt Regency — check out who’s speaking on what topics today.
technotrans says climate protection, energy efficiency and customization will be key discussion topics at PTXPO as it displays its protemp flow 6 ultrasonic eco and the teco cs 90t 9.1 TCUs.
This all-plastic “organic hybrid” composite technology involves heating a continuous-fiber reinforced sheet blank impregnated with nylon 6, and then placing it in an injection mold, where it is formed into a 3D shape and overmolded with more nylon 6 (unfilled or glass reinforced). In some cases, the sheet blank is thermoformed separately before being placed in the injection mold. This metal-replacement technology is a successor to plastic-metal “hybrid” composites, which involved preforming sheet metal and overmolding it to add ribs, attachment points, and other features.
Join this webinar to explore the transformative benefits of retrofitting your existing injection molding machines (IMMs). Engel will guide you through upgrading your equipment to enhance monitoring, control and adaptability — all while integrating digital technologies. You'll learn about the latest trends in IMM retrofitting (including Euromap interfaces and plasticizing retrofits) and discover how to future-proof your machines for a competitive edge. With insights from industry experts, it'll walk you through the decision-making process, ensuring you make informed choices that drive your business forward. Agenda: Maximize the value of your current IMMs through strategic retrofitting Learn how to integrate digital technologies to enhance monitoring and control Explore the benefits of Euromap interfaces and plasticizing retrofits Understand how retrofitting can help meet new product demands and improve adaptability Discover how Engel can support your retrofitting needs, from free consultations to execution
Joachim Kragl, director of advanced molding systems and processing at Engel, says there are today only a select number of Organomelt systems installed, most of them at university or independent laboratories, in addition to Engel’s own technology center.
While the major correction in PP prices was finally underway, generally stable pricing was anticipated for the other four commodity resins.
Whatever the label, this technology also has significant potential for use in other markets. There are variants of the technology in development that will further the use of thermoplastic composites in a range of industries that are seeking lightweight but high-strength material options, as well as the low cost, automation, and short cycle times possible with injection molding.
Join KraussMaffei for an insightful webinar designed for industry professionals, engineers and anyone interested in the manufacturing processes of PVC pipes. This session will provide a comprehensive understanding of the technology behind the production of high-quality PVC pipes: from raw material preparation to final product testing. Agenda: Introduction to PVC extrusion: overview of the basic principles of PVC pipe extrusion — including the process of melting and shaping PVC resin into pipe forms Equipment and machinery: detailed explanation of the key equipment involved — such as extruders, dies and cooling systems — and their roles in the extrusion process Process parameters: insight into the critical process parameters like temperature, pressure and cooling rates that influence the quality and consistency of the final PVC pipes Energy efficiency: examination of ways to save material and energy use when extruding PVC pipe products
Engel’s Organomelt (below) and KraussMaffei’s FiberForm above) processes are both used to produce all-plastic “organic hybrid” composite parts from continuous-fiber sheet blanks overmolded in an injection machine.
Plastics Technology covers technical and business Information for Plastics Processors in Injection Molding, Extrusion, Blow Molding, Plastic Additives, Compounding, Plastic Materials, and Resin Pricing. About Us
Take a deep dive into all of the various aspects of part quoting to ensure you’ve got all the bases—as in costs—covered before preparing your customer’s quote for services.
Mixed in among thought leaders from leading suppliers to injection molders and mold makers at the 2023 Molding and MoldMaking conferences will be molders and toolmakers themselves.
The initial development focus has been primarily on automotive interiors, including seating area components, door side-impact beams, cross-car beams, brake pedals, steering-column holders, airbag modules, and front ends. “At this time of increasing fuel requirements for automotive, OEMs are putting a lot of emphasis on lightweighting,” says Calvin Nichols, market development manager for automotive seating at BASF in Wyandotte, Mich. BASF refers to the technology as “continuous fiber-reinforced thermoplastic” or CFRT, while Pittsburgh-based Lanxess typically calls it “nylon composite sheet hybrid technology.” Similarly, Engel in York, Pa., refers to its process as Organomelt and KraussMaffei, Florence, Ky., calls its version FiberForm. The technology has also been described as “organic sheet overmolding.”
Join Engel in exploring the future of battery molding technology. Discover advancements in thermoplastic composites for battery housings, innovative automation solutions and the latest in large-tonnage equipment designed for e-mobility — all with a focus on cost-efficient solutions. Agenda: Learn about cutting-edge thermoplastic composites for durable, sustainable and cost-efficient battery housings Explore advanced automation concepts for efficient and scalable production See the latest large-tonnage equipment and technology innovations for e-mobility solutions
The aim of this presentation is to guide you through the factors and the numbers that will help you determine if a robot is a smart investment for your application. Agenda: Why are you considering automation? What problems are you trying to solve? How and why automation can help Crunch the numbers and determine the ROI
This month’s resin pricing report includes PT’s quarterly check-in on select engineering resins, including nylon 6 and 66.
This Knowledge Center provides an overview of the considerations needed to understand the purchase, operation, and maintenance of a process cooling system.
Here are processing guidelines aimed at both getting the PHA resin into the process without degrading it, and reducing residence time at melt temperatures.
Formnext Chicago is an industrial additive manufacturing expo taking place April 8-10, 2025 at McCormick Place in Chicago, Illinois. Formnext Chicago is the second in a series of Formnext events in the U.S. being produced by Mesago Messe Frankfurt, AMT – The Association For Manufacturing Technology, and Gardner Business Media (our publisher).
Machinery systems for in-situ polymerization of caprolactam into nylon 6 are under development at Engel. The company, which formed a Technology Centre for Lightweight Composites at its St. Valentin, Austria, plant last December, demonstrated a prototype in-situ composite molding system at an open house in June (see Sept. 2012 Close Up). It is based on an e-victory combi tiebarless press (120 m.t.) with two angled barrels and a high-pressure impingement mixing chamber adapted from PUR technology. It also features a new technology for feeding caprolactam flakes. One machine barrel feds caprolactam plus catalyst, and the other feeds caprolactam plus chemical activator.
In this three-part collection, veteran molder and moldmaker Jim Fattori brings to bear his 40+ years of on-the-job experience and provides molders his “from the trenches” perspective on on the why, where and how of venting injection molds. Take the trial-and-error out of the molding venting process.
Multiple speakers at Molding 2023 will address the ways simulation can impact material substitution decisions, process profitability and simplification of mold design.
This airbag module, which weighs at least 30% less than a current commercial version injection molded of glass-reinforced nylon 6, is made of a Tepex dynalite nylon 6 sheet with 47% continuous glass overmolded with a Lanxess Durethan nylon 6 containing 40% short glass. (Photo: KraussMaffei)
While prices moved up for three of the five commodity resins, there was potential for a flat trajectory for the rest of the third quarter.
Across the show, sustainability ruled in new materials technology, from polyolefins and engineering resins to biobased materials.
Join this webinar to explore the transformative benefits of retrofitting your existing injection molding machines (IMMs). Engel will guide you through upgrading your equipment to enhance monitoring, control and adaptability — all while integrating digital technologies. You'll learn about the latest trends in IMM retrofitting (including Euromap interfaces and plasticizing retrofits) and discover how to future-proof your machines for a competitive edge. With insights from industry experts, it'll walk you through the decision-making process, ensuring you make informed choices that drive your business forward. Agenda: Maximize the value of your current IMMs through strategic retrofitting Learn how to integrate digital technologies to enhance monitoring and control Explore the benefits of Euromap interfaces and plasticizing retrofits Understand how retrofitting can help meet new product demands and improve adaptability Discover how Engel can support your retrofitting needs, from free consultations to execution
While the major correction in PP prices was finally underway, generally stable pricing was anticipated for the other four commodity resins.
The Plastics Industry Association (PLASTICS) has released final figures for NPE2024: The Plastics Show (May 6-10; Orlando) that officially make it the largest ever NPE in several key metrics.
Successfully starting or restarting an injection molding machine is less about ticking boxes on a rote checklist and more about individually assessing each processing scenario and its unique variables.
Sustainability continues to dominate new additives technology, but upping performance is also evident. Most of the new additives have been targeted to commodity resins and particularly polyolefins.
Mike Sepe has authored more than 25 ANTEC papers and more than 250 articles illustrating the importance of this interdisciplanary approach. In this collection, we present some of his best work during the years he has been contributing for Plastics Technology Magazine.
KraussMaffei’s latest presses for the FiberForm process are the new GX Series of hydromechanical, two-platen presses, available from 400 to 650 m.t., which boast a number of new features (see July 2012 Keeping Up).
Exhibitors and presenters at the plastics show emphasized 3D printing as a complement and aid to more traditional production processes.
Resin drying is a crucial, but often-misunderstood area. This collection includes details on why and what you need to dry, how to specify a dryer, and best practices.
Last month, BASF and Germany’s SGL Group, a global leader in carbon-based products, announced they are jointly developing a composite material based on a reactive nylon system and carbon fibers that would allow cost-effective production of thermoplastic composites. The material system is intended for use in the T-RTM process (Thermoplastic Resin Transfer Molding) as well as reactive injection molding. It permits considerably shorter processing cycles than conventional thermoset RTM. Adjustment of the material system to these faster processing techniques is expected to play a key role in the entry of structural components made from carbon-fiber composites into automotive mass production.
Plastics Technology covers technical and business Information for Plastics Processors in Injection Molding, Extrusion, Blow Molding, Plastic Additives, Compounding, Plastic Materials, and Resin Pricing. About Us
When, how, what and why to automate — leading robotics suppliers and forward-thinking moldmakers will share their insights on automating manufacturing at collocated event.
While the melting process does not provide perfect mixing, this study shows that mixing is indeed initiated during melting.
This is BASF’s first cooperative development in carbon-fiber composites. BASF is contributing its competence in polymer development as a leader in nylon and precursor caprolactam, while SGL brings its expertise in carbon fiber and high-temperature processes. In-situ polymerization technology is just now being developed in BASF laboratories under Martin Jung, head of structural materials research. According to Jung, starting with the low-viscosity, highly reactive caprolactam allows optimal wetting of the carbon fiber and short cycle times in T-RTM or reactive injection molding.
Across all process types, sustainability was a big theme at NPE2024. But there was plenty to see in automation and artificial intelligence as well.
Join Engel in exploring the future of battery molding technology. Discover advancements in thermoplastic composites for battery housings, innovative automation solutions and the latest in large-tonnage equipment designed for e-mobility — all with a focus on cost-efficient solutions. Agenda: Learn about cutting-edge thermoplastic composites for durable, sustainable and cost-efficient battery housings Explore advanced automation concepts for efficient and scalable production See the latest large-tonnage equipment and technology innovations for e-mobility solutions
Plastics Technology’s Tech Days is back! Every Tuesday in October, a series of five online presentations will be given by industry supplier around the following topics: Injection Molding — New Technologies, Efficiencies Film Extrusion — New Technologies, Efficiencies Upstream/Downstream Operations Injection Molding — Sustainability Extrusion — Compounding Coming out of NPE2024, PT identified a variety of topics, technologies and trends that are driving and shaping the evolution of plastic products manufacturing — from recycling/recyclability and energy optimization to AI-based process control and automation implementation. PT Tech Days is designed to provide a robust, curated, accessible platform through which plastics professionals can explore these trends, have direct access to subject-matter experts and develop strategies for applying solutions in their operations.
Plastics Technology’s Tech Days is back! Every Tuesday in October, a series of five online presentations will be given by industry supplier around the following topics: Injection Molding — New Technologies, Efficiencies Film Extrusion — New Technologies, Efficiencies Upstream/Downstream Operations Injection Molding — Sustainability Extrusion — Compounding Coming out of NPE2024, PT identified a variety of topics, technologies and trends that are driving and shaping the evolution of plastic products manufacturing — from recycling/recyclability and energy optimization to AI-based process control and automation implementation. PT Tech Days is designed to provide a robust, curated, accessible platform through which plastics professionals can explore these trends, have direct access to subject-matter experts and develop strategies for applying solutions in their operations.
September marked the opening of Lanxess’ first production plant for high-tech plastics in the U.S. Located in Gastonia, N.C., this compounding plant is producing Durethan nylon and Pocan PBT compounds aimed primarily at premium, lightweight automotive plastic components, ranging from body parts, oil pans, coolant pipes and battery housings, to steering rods, pedals, and pedal brackets. Further development of organic hybrid composite technology is expected here.
Mike Sepe has authored more than 25 ANTEC papers and more than 250 articles illustrating the importance of this interdisciplanary approach. In this collection, we present some of his best work during the years he has been contributing for Plastics Technology Magazine.
In this three-part collection, veteran molder and moldmaker Jim Fattori brings to bear his 40+ years of on-the-job experience and provides molders his “from the trenches” perspective on on the why, where and how of venting injection molds. Take the trial-and-error out of the molding venting process.
Sources at these four suppliers foresee dramatic growth potential, starting with auto interior components but extending to exterior, chassis, and power-train applications. They also envision applications in aeronautics, trains, trucks, agricultural equipment, machinery manufacturing, and renewable-energy systems.
Engel’s in-situ nylon 6 polymerization prototype is based on an e-victory combi tiebarless press with two angled barrels and a high-pressure impingement mixing chamber adapted from PUR technology.
Thousands of people visit our Supplier Guide every day to source equipment and materials. Get in front of them with a free company profile.
There were new presses of all stripes aplenty at K 2010, but the “wow” factor was supplied by automated work cells and integrated manu-facturing systems performing multiple operations before, during, and after molding.
Join Wittmann for an engaging webinar on the transformative impact of manufacturing execution systems (MES) in the plastic injection molding industry. Discover how MES enhances production efficiency, quality control and real-time monitoring while also reducing downtime. It will explore the integration of MES with existing systems, emphasizing compliance and traceability for automotive and medical sectors. Learn about the latest advancements in IoT and AI technologies and how they drive innovation and continuous improvement in MES. Agenda: Overview of MES benefits What is MES? Definition, role and brief history Historical perspective and evolution Longevity and analytics Connectivity: importance, standards and integration Advantages of MES: efficiency, real-time data, traceability and cost savings Emerging technologies: IoT and AI in MES
In this collection of articles, two of the industry’s foremost authorities on screw design — Jim Frankand and Mark Spalding — offer their sage advice on screw design...what works, what doesn’t, and what to look for when things start going wrong.
This month’s resin pricing report includes PT’s quarterly check-in on select engineering resins, including nylon 6 and 66.
In a time where sustainability is no longer just a buzzword, the food and beverage packaging industry is required to be at the forefront of this innovation. By adopting circular packaging processes and solutions, producers can meet regulatory requirements while also satisfying consumer demand and enhancing brand reputation. Join Husky to learn more about the broader implications of the circular economy — as well as how leading brands are leveraging this opportunity to reduce costs, increase design flexibility and boost product differentiation. Agenda: The cost and operational benefits of embracing circularity Key materials in circular packaging — including rPET and emerging bioplastics How to design a circular food and beverage package Strategies for selecting sustainable closures to future-proof packaging solutions Optimization and streamlining of production processes for enhanced efficiency How Husky Technologies can enable your sustainable success
•Hybrid technology was also used to make the first auto seat pan on a production vehicle, offering 45% weight reduction vs. standard seat pans (see cover photo). Featured in the new Opel Astra OPC sport coupe, it consists of a preform of continuous-glass fabric impregnated with nylon, which is placed in an injection mold and overmolded with impact-modified, short-glass reinforced nylon to form ribs and edges. BASF developed two specialty Ultramid nylon grades for this unit—one for impregnating the glass-fabric and one for injection overmolding.
Ultrasonic gauge technology has evolved to simplify measurement of very thin layers in plastic containers. Today’s gauges with high-frequency capabilities and specialized software can make multilayer container measurement quick and easy for ordinary users.
Across all process types, sustainability was a big theme at NPE2024. But there was plenty to see in automation and artificial intelligence as well.
Demand for bioresins is growing in molded goods, particularly as a sustainability play to replace fossil-fuel based materials, but these materials are not a drop-in replacement for traditional materials. Molds and hot runners need to be optimized for these materials.
When, how, what and why to automate — leading robotics suppliers and forward-thinking moldmakers will share their insights on automating manufacturing at collocated event.
While prices moved up for three of the five commodity resins, there was potential for a flat trajectory for the rest of the third quarter.
Across the show, sustainability ruled in new materials technology, from polyolefins and engineering resins to biobased materials.
Engel’s Kragl forsees further potential for both Organomelt technology and the in-situ polymerization approach. “In-situ will be a future technology for very efficient lightweight design. However, there are still many questions to be answered before it will be a stable, commercially available process. It also should be understood that in-situ will be very unlikely to achieve the same cycle times achieved by Organomelt.” He sees the in-situ technology being used primarily for nylon 6 and possibly nylon 12. Because of flammability issues, it may be more applicable to nonautomotive applications such as sports equipment and medical devices, at least initially.
Beyond Plastic and partners have created a certified biodegradable PHA compound that can be injection molded into 38-mm closures in a sub 6-second cycle from a multicavity hot runner tool.
Introduced by Zeiger and Spark Industries at the PTXPO, the nozzle is designed for maximum heat transfer and uniformity with a continuous taper for self cleaning.
While prices moved up for three of the five commodity resins, there was potential for a flat trajectory for the rest of the third quarter.
In this collection of content, we provide expert advice on welding from some of the leading authorities in the field, with tips on such matters as controls, as well as insights on how to solve common problems in welding.
In less than a decade in injection molding, US Merchants has acquired hundreds of machines spread across facilities in California, Texas, Virginia and Arizona, with even more growth coming.
He is also aware of the challenges posed by processing bioplastics, noting that in the early days, the industry didn’t do itself any favors by often positioning bioplastics as drop-in replacements for traditional resins. “In the past, companies made PHA compounds and sold them as having similar properties to PP,” Pinczuk says. When processors attempted to run these bioresins using the same machine settings they’d apply for commodity polyolefins, the result was, as Pinczuk puts it, “a fiasco.”
Gifted with extraordinary technical know how and an authoritative yet plain English writing style, in this collection of articles Fattori offers his insights on a variety of molding-related topics that are bound to make your days on the production floor go a little bit better.
Learn about sustainable scrap reprocessing—this resource offers a deep dive into everything from granulator types and options, to service tips, videos and technical articles.
BASF’s Nichols says, “Glass in a unidirectional form is much stronger than other forms of glass or ferrous and nonferrous metals. Such a sheet composite overmolded with nylon 6 has tensile strength as much as five times that of metals. Strength-to-weight ratio is dramatically improved over metals—twice that of steel and three-to-four times higher than a standard injection molded glass-filled thermoplastic. Stiffness-to-weight ratio with the continuous-glass composite laminate overmolded with nylon is eight times as much as steel.”
Meanwhile, the machinery suppliers both have recently introduced new equipment to further progress in this nascent technology. Engel is recommending its new v-duo vertical large tonnage machines for Organomelt systems. Hydraulically powered with energy-saving servo-driven pumps, they are offered in five sizes from 400 to 2300 metric tons (see Sept. 2012 Close Up). The larger sizes are aimed at continuous-fiber composites, with their easy mold access to facilitate loading of reinforcing fabrics and organic sheets and tapes.
A thermoplastic composite technology that emerged just a couple of years ago promises to make dramatic strides within the next two years in automotive mass production of structural components.
Currently designated as a “7” or “other” material, Beyond Plastic is hoping to prove out PHA’s end-of-life recycling and composting options, as related to regulatory standards. Where another common bioplastic, PLA, is deemed compostable under the ASTM 6400 standard, breaking down in industrial digesters that feature the right temperatures, as well as pH, oxygen and moisture levels, PHA is certified as ASTM 6691 for marine degradation. It is also compostable under all conditions, including home composting, and Beyond Plastic has molded new closures from 100% recycled PHA. Future projects include determining PHA’s viability for extrusion blow molding and thermoforming.
Core Technology Molding turned to Mold-Masters E-Multi auxiliary injection unit to help it win a job and dramatically change its process.
Uniloy is revising its machinery lines across the board and strengthening after-sales services in tooling maintenance, spare parts and tech service.
Mold maintenance is critical, and with this collection of content we’ve bundled some of the very best advice we’ve published on repairing, maintaining, evaluating and even hanging molds on injection molding machines.
Mold maintenance is critical, and with this collection of content we’ve bundled some of the very best advice we’ve published on repairing, maintaining, evaluating and even hanging molds on injection molding machines.
Additive technology creates air pockets in film during orientation, cutting down on the amount of resin needed while boosting opacity, mechanical properties and recyclability.
While the melting process does not provide perfect mixing, this study shows that mixing is indeed initiated during melting.
•Also considered a first for this technology is a brake pedal from Germany’s ZF Friedrichshafen AG, which weighs 355 g, half as much as a steel brake pedal. It is made of a Tepex dynalite composite sheet of nylon 6 with 47% by volume continuous glass fibers, which is heated, thermoformed, and cut to size before overmolding with Lanxess’ Durethan BKV 30 H2.0 nylon 6 with 30% short glass.
Learn about sustainable scrap reprocessing—this resource offers a deep dive into everything from granulator types and options, to service tips, videos and technical articles.
In his three years at Beyond Plastic, Pinczuk has led that company’s research efforts to commercialize PHA for packaging — largely based on the material’s end-of-life biodegradability. “We don’t want to be in the closure business,” Pinczuk says. “We’re in the business to make formulations that can go mass market, be mass produced and replace petrochemical products currently used.”
At last month’s Dusseldorf European Composites show and at the Paris JEC Composite exhibition in March, the newest applications of composite-sheet hybrid technology were highlighted by the key players:
After successfully introducing a combined conference for moldmakers and injection molders in 2022, Plastics Technology and MoldMaking Technology are once again joining forces for a tooling/molding two-for-one.
Solvay’s KetaSpire KT-857 PEEK extrusion compound eliminates adhesion and sustainability constraints of conventional PEEK or enamel insulation processes.
A thermoplastic composite technology that emerged just a couple of years ago promises to make dramatic strides within the next two years in automotive mass production of structural components. At least two material suppliers—BASF and Lanxess—and two machine suppliers—Engel and KraussMaffei—are in the forefront of its development.
In-mold polymerization of caprolactam monomer into nylon 6 is being pursued on multiple fronts as the next step in thermoplastic composites technology. It allows low-viscosity caprolatam to impregnate dry fibers in a mold and react to form a nylon composite “in situ.”
Other thermoplastics considered as candidates for this technology include PP, PBT, PES, PEEK, nylon 612, and possibly nylon 66, depending in large part on how well they meet strict flammability requirements.
Say “manufacturing automation” and thoughts immediately go to the shop floor and specialized production equipment, robotics and material handling systems. But there is another realm of possible automation — the front office.
In this collection, which is part one of a series representing some of John’s finest work, we present you with five articles that we think you will refer to time and again as you look to solve problems, cut cycle times and improve the quality of the parts you mold.
After three years of research including the creation and testing of 174 different compounds, Beyond Plastic LLC, Commerce, California, says it has arrived at a completely biodegradable injection-molded closure based on polyhydroxyalkanoate (PHA), with phase two research looking at compression molding of the bioplastic caps. The PHA resin has been supplied by CJ Biomaterials Inc., a division of South Korea-based CJ CheilJedang. Heading up the project is Fred Pinczuk, Beyond Plastic’s chief technology officer, who has more than four decades of experience in packaging, including stints at major injection molding and blowmolding machinery OEMs.
Pinczuk acknowledges that bioplastics in general and PHA in particular are not new, but he feels PHA’s properties — and his company’s research — put the material in a new position to replace fossil fuel-based plastics currently used in single-use packaging applications, like closures.
Join Wittmann for an engaging webinar on the transformative impact of manufacturing execution systems (MES) in the plastic injection molding industry. Discover how MES enhances production efficiency, quality control and real-time monitoring while also reducing downtime. It will explore the integration of MES with existing systems, emphasizing compliance and traceability for automotive and medical sectors. Learn about the latest advancements in IoT and AI technologies and how they drive innovation and continuous improvement in MES. Agenda: Overview of MES benefits What is MES? Definition, role and brief history Historical perspective and evolution Longevity and analytics Connectivity: importance, standards and integration Advantages of MES: efficiency, real-time data, traceability and cost savings Emerging technologies: IoT and AI in MES
Core Technology Molding turned to Mold-Masters E-Multi auxiliary injection unit to help it win a job and dramatically change its process.
Say “manufacturing automation” and thoughts immediately go to the shop floor and specialized production equipment, robotics and material handling systems. But there is another realm of possible automation — the front office.
The two material suppliers displayed applications for the technology at K2010. Lanxess showed an Audi A8 front-end reinforcement molded by Germany’s Magna Decoma Exterior Systems, containing both aluminum and Tepex inserts overmolded with nylon 6. BASF displayed a seat back from Faurecia of France consisting of woven-glass/nylon sheet from California-based Performance Materials Corp., overmolded with a specially developed 35%-glass nylon 6 compound (BASF’s Ultramid CompoSIT XA3232) that combines stiffness, ductility, and Class-A-type finish. The part weighs about 20% less than standard seat backs and is expected to be commercial within the next two years.
Engel’s Organomelt (above) and KraussMaffei’s FiberForm (left) processes are both used to produce all-plastic “organic hybrid” composite parts from continuous-fiber sheet blanks overmolded in an injection machine.
Thousands of people visit our Supplier Guide every day to source equipment and materials. Get in front of them with a free company profile.
Additive technology creates air pockets in film during orientation, cutting down on the amount of resin needed while boosting opacity, mechanical properties and recyclability.
BASF’s Nichols expects an increase in shape complexity to facilitate market growth. This will require improvements in tooling that can preform composite sheet laminates and tapes with more 3D complexity and deep draws. KraussMaffei ventures that one way may be to use long-fiber compounds from an IMC machine in place of the organic sheet in some part areas that need more 3D form. According to a KM spokesman, “We will continue with our strong partnerships over the complete process chain to create knowhow for design and simulation of mechanical properties and the forming process. If all partners work together closely, there will be an economic solution.”
Both Engel and KraussMaffei first demonstrated the technology in two elaborate molding cells at the K2010 show in Dusseldorf, Germany (see our report in Jan. 2011). There, Engel molded a steering-column holder and KraussMaffei a door side-impact beam. Both used Tepex composite sheets from Germany’s Bond-Laminates GmbH and nylon overmolding compounds from Lanxess. (Lanxess recently acquired Bond-Laminates.) The two demonstrations used robots (linear or six-axis) to preheat the sheet in an oven at 300 C for 30-40 sec and then transfer the hot sheet to the injection mold. Closing the mold preformed the sheet, and then more nylon was injected over it in specific areas. Cycle times ranged from 33 to 55 sec. (the latter limited by oven-heating capacity).
Despite price increase nominations going into second quarter, it appeared there was potential for generally flat pricing with the exception of a major downward correction for PP.
Discover how artifical intelligence is revolutionizing plastics processing. Hear from industry experts on the future impact of AI on your operations and envision a fully interconnected plant.
After successfully introducing a combined conference for moldmakers and injection molders in 2022, Plastics Technology and MoldMaking Technology are once again joining forces for a tooling/molding two-for-one.
Engel’s part, with its more complex geometry, was laser-trimmed outside the mold. In the case of KraussMaffei, which compounded the long-glass overmolding compound direct from roving on its IMC injection molding compounder, the robot transferred the net-shaped part to a quality-check station after molding.
Ultradent's entry of its Umbrella cheek retractor took home the awards for Technical Sophistication and Achievement in Economics and Efficiency at PTXPO.
This ZF Friedrichshafen car brake pedal is said to be the first to be made of reinforced nylon 6, and weighs half as much as a steel brake pedal. (Photo: Lanxess)
GETTING A QUOTE WITH LK-MOULD IS FREE AND SIMPLE.
FIND MORE OF OUR SERVICES:
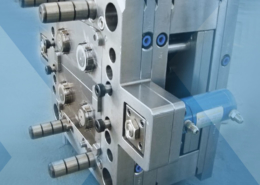
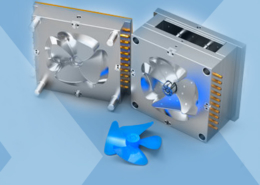
Plastic Molding

Rapid Prototyping
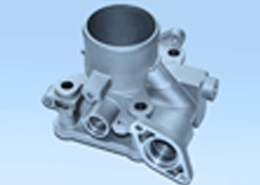
Pressure Die Casting
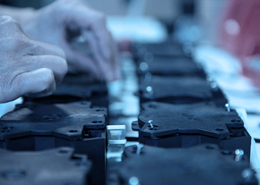
Parts Assembly
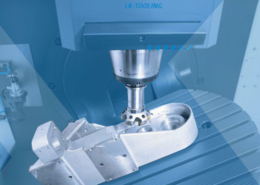