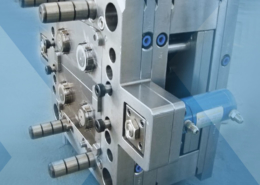
Polycarbonate Injection Molding: Revolutionizing Manufacturing
Author:gly Date: 2024-06-08
Introduction
Polycarbonate injection molding stands as a pinnacle of modern manufacturing techniques, combining versatility, durability, and precision. As industries evolve towards more complex design requirements, the demand for materials that can meet these challenges has intensified. Polycarbonate, with its exceptional properties, has emerged as a frontrunner in various sectors ranging from automotive to electronics. This article delves into the intricacies of polycarbonate injection molding, exploring its applications, advantages, and future prospects.
Material Properties
Polycarbonate, a thermoplastic polymer, boasts remarkable properties such as high impact resistance, optical clarity, and heat resistance. These attributes make it an ideal choice for applications where strength and transparency are paramount. In injection molding, polycarbonate's ability to flow easily into intricate molds while retaining its structural integrity sets it apart from other materials.
Mechanical Strength
One of the most notable features of polycarbonate is its exceptional mechanical strength. With a tensile strength comparable to that of metals, polycarbonate components can withstand high impact loads without deforming or breaking. This property makes it indispensable in industries where durability is non-negotiable, such as automotive and aerospace.
Optical Clarity
The optical clarity of polycarbonate makes it invaluable in applications requiring transparent or translucent components. Unlike other transparent plastics, polycarbonate exhibits minimal yellowing or hazing over time, ensuring long-term visual appeal. This characteristic makes it a preferred choice for items like lenses, visors, and display panels.
Heat Resistance
Another key advantage of polycarbonate is its exceptional heat resistance. It can withstand high temperatures without deforming, making it suitable for applications exposed to extreme thermal conditions. This property expands its utility in industries such as electronics, where components may encounter elevated operating temperatures.
Manufacturing Process
The injection molding process for polycarbonate involves several precise steps, each crucial for achieving the desired outcome. From material selection to mold design and post-processing, every aspect requires meticulous attention to detail to ensure quality and consistency.
Material Preparation
Before the injection molding process begins, polycarbonate resin is carefully selected based on the desired properties of the final product. The resin is then heated to a precise temperature to achieve optimal flow characteristics, ensuring uniformity and strength in the molded parts.
Mold Design
The design of the mold plays a critical role in the success of polycarbonate injection molding. Complex geometries and intricate details must be carefully incorporated into the mold design to ensure the accurate replication of the desired shape. Advanced CAD software and computer simulations aid in optimizing mold design for efficiency and cost-effectiveness.
Injection Molding Process
During the injection molding process, molten polycarbonate resin is injected into the mold cavity under high pressure. The resin fills the mold, taking on its shape and intricacies. Controlled cooling cycles help solidify the resin, after which the molded part is ejected from the mold for further processing or assembly.
Applications
The versatility of polycarbonate injection molding opens doors to a myriad of applications across various industries. From consumer electronics to medical devices, polycarbonate components find use in diverse sectors where performance and reliability are paramount.
Automotive
In the automotive industry, polycarbonate injection molding is utilized for manufacturing exterior components such as bumpers, side mirrors, and headlamp lenses. Its lightweight nature, coupled with high impact resistance, contributes to improved fuel efficiency and safety standards.
Electronics
Polycarbonate's excellent electrical insulation properties make it indispensable in the electronics industry for producing housings, connectors, and components for devices ranging from smartphones to industrial machinery. Its ability to withstand high temperatures and harsh environments ensures the longevity and reliability of electronic products.
Medical
In the medical field, polycarbonate injection molding is employed to fabricate equipment and devices requiring sterilization and biocompatibility. Its transparency, coupled with resistance to chemicals and impact, makes it ideal for manufacturing surgical instruments, housings for diagnostic equipment, and medical device components.
Future Prospects
As technology advances and industries continue to push the boundaries of innovation, the future of polycarbonate injection molding looks promising. Ongoing research focuses on enhancing material properties, optimizing manufacturing processes, and exploring new applications to meet evolving market demands.
Advanced Materials
Researchers are actively developing advanced formulations of polycarbonate with tailored properties to address specific industry needs. These include enhanced thermal stability, improved impact resistance, and novel additives for specialized applications such as 3D printing and aerospace.
Industry 4.0 Integration
The integration of polycarbonate injection molding with Industry 4.0 technologies promises increased automation, efficiency, and customization. Smart manufacturing systems equipped with real-time monitoring and predictive maintenance capabilities optimize production processes, minimize downtime, and ensure consistent quality.
Conclusion
Polycarbonate injection molding stands as a cornerstone of modern manufacturing, offering unparalleled versatility, durability, and precision. Its widespread applications across industries underscore its significance in driving technological advancements and innovation. As we look to the future, continued research and development efforts will further enhance the capabilities of polycarbonate, unlocking new possibilities and reshaping the landscape of manufacturing.
This comprehensive exploration of polycarbonate injection molding highlights its transformative impact on diverse industries and underscores the importance of ongoing innovation to meet evolving market demands. With its exceptional properties and endless possibilities, polycarbonate remains at the forefront of material science, shaping the future of manufacturing.
GETTING A QUOTE WITH LK-MOULD IS FREE AND SIMPLE.
FIND MORE OF OUR SERVICES:
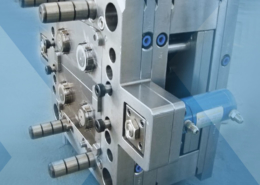
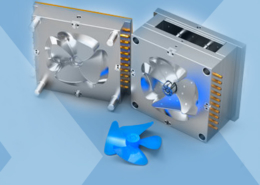
Plastic Molding

Rapid Prototyping
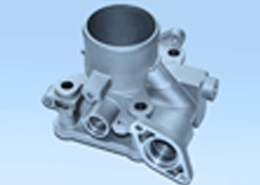
Pressure Die Casting
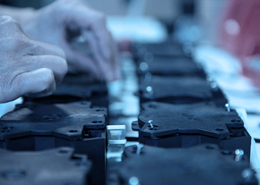
Parts Assembly
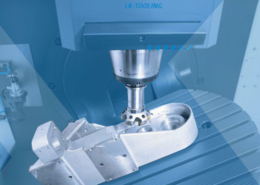