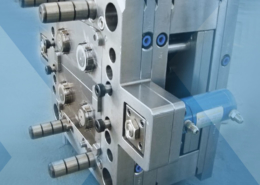
How Artificial Intelligence Is Transforming Injection Molding - short mould in i
Author:gly Date: 2024-09-30
Wittmann Battenfeld, which has fully embraced Industry 4.0 connectivity across its portfolio of injection molding and auxiliary machines over the past several years, employs AI with its robots to monitor cycle times and control robots’ speeds outside the molding machine.
With regard to machinery, there is a strong move towards “copy & paste” systems and processes in both Europe and North America. The global medical team at Sumitomo (SHI) Demag, led by business development director Anatol Sattel, are also noting more requests for remote system access to historical machine data. This is predominantly to assist with troubleshooting and monitoring validated process settings.
Geoff Giordano is a tech journalist with more than 30 years’ experience in all facets of publishing. He has reported extensively on the gamut of plastics manufacturing technologies and issues, including 3D printing materials and methods; injection, blow, micro and rotomolding; additives, colorants and nanomodifiers; blown and cast films; packaging; thermoforming; tooling; ancillary equipment; and the circular economy. Contact him at [email protected].
The company’s machine-learning capabilities — HiQ Flow and CMS technology — will be on display at this year’s K show on Oct. 19 to 26 in Düsseldorf, Germany. The speed of ROI can be as short as a few cycles with HiQ Flow, and the software can often be retrofitted to older injection molding machines equipped with a B8 machine control. A CMS Pro version will be available at a later date.
The company’s Eco-Mode saves wear and tear on the robot by ensuring it does not run faster than necessary — ultimately saving maintenance and energy costs. Offered standard on many Wittmann robots, Eco-Mode “requires no special programming or interface with the IMM or operator/programmer,” said Jason Long, National Sales Manager for robots and automation for Wittmann USA. “All the end user has to do is tell the robot how many seconds it should get back over the IMM before the mold opens.”
Comparing AI and machine learning, Glueck said, “AI actually requires a much higher time investment and, correspondingly, a higher financial investment. A large number of parameters must be recorded from a running process and the relevant parameters are determined on the basis of the deviations. These are compared with measurement data of the product.”
More recently, there is a stronger leaning in the medical market towards larger strategic and more complex projects, such as drug delivery devices and pen style injectors. This is predominantly due to the global growth in diabetes care, where demand for advanced glucose monitoring and insulin delivery devices is propelling innovation. Testament to demand, credible industry reports forecast that the diabetes device market will surpass $68.2 billion by 2032, almost triple its 2022 value.
The development of process optimisation systems, integrating material and knowledge with simulation tools is probably the most exciting development on the horizon, claims Sargisson. Such systems will enable processors to observe advanced settings and capture deeper processing insights.
High profile acquisitions of diagnostics companies, IPO listings, strategic partnerships, and the rise of virtual care platforms provide further assurance that the diagnostics market is on the cusp of another huge growth curve. This all indicates that there are clearly exciting opportunities ahead for moulders operating in the high tech medical device and diagnostics product development and production space.
Wittmann Battenfeld’s HiQ software can generally be retrofitted even to older injection molding machines equipped with a B8 machine control.
The Industry 4.0 era of manufacturing depends so heavily on data-driven precision that artificial intelligence (AI) is playing an increasing role in harnessing that data to enhance the performance of machines — including injection molders.
In 2023, the global medical injection moulding market size was estimated at $22.54 billion. It is expected to grow at a compound annual growth rate (CAGR) of 5.8% from 2024 to 2030. Much of this growth is being driven by advances in self diagnostics, the home healthcare sector, improved healthcare infrastructures in emerging economies, and an ageing population, which WHO predicts will double by 2050.
For medical moulders already producing vital monitoring devices, including oxygen, weight, glucose and ECG devices, as well as infusion pumps and cannulas etc. and already meeting the exacting healthcare standards, the transition to homecare device production should be relatively seamless.
Also observed during the pandemic, larger scale adoption of home healthcare and smart diagnostic devices, continues to accelerate at pace.
AI in manufacturing encompasses an array of technologies that allow machines to perform with intelligence that emulates that of humans. Machine learning and natural language processing help machines approximate the human capacity to learn, make judgments, and solve problems. Data-enhanced efficiency keeps processes moving faster and more cost-effectively.
Based on factors like changes in material, ambient temperature, machine wear, tool wear, and other influences, “AI can determine which machine parameters need to be changed so that the product can be produced within its quality tolerances. This can take months, as errors first must occur in order to learn from them.”
“One of Arburg's medium-term goals is to develop a system for digital twins of customized injection molding machines. This will open up completely new possibilities for simulating the cycle and making energy predictions. In addition, 3D views and installation plans of the machine — stored in the arburgXworld customer portal and in the control system — support the operator,” said Faulhaber.
MedTech is a multi-billion-dollar manufacturing sector. Unsurprisingly, industry analysts are always keen to pinpoint the newest transformational medical and life science technologies that are expected to shape future treatment pathways.
Thermoplastic and LSR moulding continues to be used extensively to manufacture a huge variety of everyday medical applications. The range is broad and can include implantable components, test tubes, petri dishes, PCR tubes, pipette tips and other labware, as well as medical monitoring devices, drug delivery components and surgical equipment.
To support these advances and in order to meet the explicit quality management and validation ISO 13485 standards for medical devices, Sumitomo (SHI) Demag introduced new machine user parameters, digital quality control and KPI analytics into its IntElect S medical production package. One of these advanced Med-Spec demo cells is now located in Limerick, Ireland. This will enable customers to perform validations, run tool trials and use the facility to provide valuable process optimisation training to technicians.
To support these efforts, the company’s R&D team continues to develop an IoT dashboard to facilitate data analysis and visualisation, transfer and storage of know-how, as well as maintenance planning and prediction. Within this assistance system, additional autonomous and interconnected functions are being conceived to provide valuable insight into the machine performance and different production variables.
Thanks to the integrated arburgXworld Control FillAssist, Arburg’s Allrounder "knows" the molded part it is supposed to produce. One issue for the future is to ensure that the machine not only keeps itself stable, but also self-optimizes.
The company’s ultimate vision is an intelligent machine that can independently make predictions about part quality, machine wear and failures and deliver optimisations online. Enabling greater process consistency and allowing for real-time machine maintenance to be adjusted accordingly.
With significant access to start-up finding, telehealth is the boom-market to watch. It is current exhibiting a CAGR of 19.7% between now and 2030. Online video and audio consultations with physicians and medical consultants are increasingly being used to deliver quality healthcare while simultaneously reducing heavy work and cost burdens. The telehealth segment is split between services and products. Items such as wearable patient monitoring and telecommunication devices accounts for around one third of the market.
By harnessing the reams of data produced in modern plastics processing facilities, artificial intelligence can improve machine performance.
In 2024, Sumitomo (SHI) Demag will host its inaugural productivity roadshow. With four stopovers planned for July in the UK and Ireland, including Limerick, customers will be invited to explore all the latest trends, productivity and profit-enhancing technologies.
As AI and machine learning are further leveraged to improve injection molding operations, simply gathering data is not enough to optimize processes, Faulhaber cautioned. “You also need the process expertise and domain knowledge. In the future, the evaluation of many data directly in the control unit will offer further added value.”
“AI is becoming increasingly important in mechanical engineering, not least because of the need to automate injection molding processes efficiently and flexibly despite ever smaller batch sizes and shorter product life cycles,” said Werner Faulhaber, Director of Research and Development at Arburg. “Application examples of AI include automatic programming of robotic systems, targeted malfunction remedying, and a spare parts system with ‘intelligent’ image processing. Arburg is working on making injection molding more intelligent, step by step — ensuring that the machine continuously learns, keeps itself stable, and can even optimize itself in the future.”
Arburg forms flexible — and controllable — production systems by combining machines, automation, and proprietary IT solutions. The company’s Gestica control system, with its intelligent assistant functions, is integral to those systems. “All Kuka six-axis robots, for example, have been equipped with the new Gestica user interface as standard,” Faulhaber noted. “This simplifies programming, as well as the monitoring, storage, and evaluation of process data.”
Regional medical director of the Sumitomo (SHI) Demag team Andrew Sargisson shares his industry insight and global predictions for the medical market, touching upon how these latest trends are influencing investments in medical injection moulding facilities worldwide.
“The technology draws new conclusions from current parameters and, thus, becomes increasingly intelligent as it monitors performance,” said Product Manager Christian Glueck. “We limit it to a methodical determination of parameters. Therefore, the time required to use the technology is minimal, as is the price.”
One application Arburg is working on is the automatic programming of its Multilift linear robotic systems. “The idea is that the operator simply enters the destination, as with a car navigation device, and the system automatically calculates the optimal route. For robotic systems, this means that the operator simply enters the desired start and end positions, and the control system takes care of the rest.”
The medical market, particularly diagnostics, was strongly influenced by the Coronavirus pandemic. As anticipated, there has been a natural levelling-off for pandemic-related consumables.
Another Wittmann feature, Eco-Vac conserves energy by setting a few parameters on the robot and allowing the robot to turn its vacuum circuits off and on. “The robot monitors the vacuum level of the circuit used for picking the part out of the mold. If the robot senses the vacuum has reduced to a level that it could drop the part before it is told to, the robot will turn the vacuum on until it reaches the safe level again, then shuts back off.” This feature cuts the amount of compressed air each robot uses “and could save customers hundreds of dollars a year per robot.”
Arburg uses AI “to develop master models using experience and data collected over the years on process, material, and machinery,” Faulhaber continued. “The customer could then sharpen the provided master model ‘on edge’ and optimize their processes. The in-house development Gestica control system, the Arburg host computer system, and the arburgXworld customer portal give an advantage here.
Wittmann co-funded such an assessment program with Austria’s Montanuniversität Leoben university, “but we found that the time needed to make it workable for production had to be questioned because in addition to the long-term investigation of the process, you also need the manpower necessary to handle it.”
GETTING A QUOTE WITH LK-MOULD IS FREE AND SIMPLE.
FIND MORE OF OUR SERVICES:
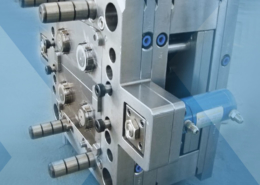
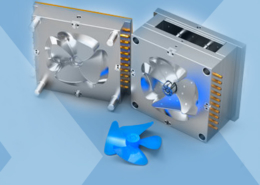
Plastic Molding

Rapid Prototyping
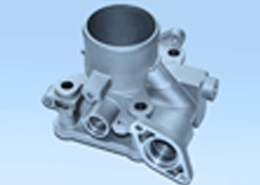
Pressure Die Casting
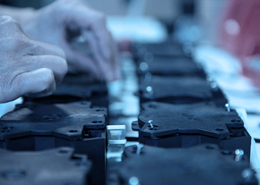
Parts Assembly
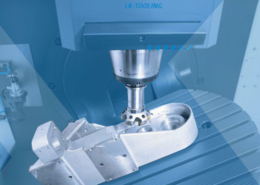