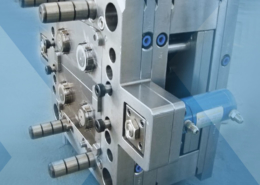
How A Michigan Injection Molder Overhauled Its Floor for the Future - bumper inj
Author:gly Date: 2024-09-30
It was stated at a Special Interest Seminar on Powder Injection Molding at the PM2012 World Congress, Yokohama, Japan, 14-18 October, that production of the Lightning connector parts was running at 5 million parts per month, whilst other MIM components for the iPhone amount to more than 10 million parts per month, with large number of workers required to achieve the required level of surface finish and necessary tolerances.
Extensive MIM, CIM industry and sinter-based AM industry news, plus the following exclusive deep-dive articles and reports:
The Informa Markets Engineering network of B2B media sites includes Design News, Battery Technology, Medical Device & Diagnostic Industry (MD+DI), Packaging Digest, PlasticsToday, and Powder & Bulk Solids.
Industry sources state that Apple has specified a single MIM feedstock supplier for the production of the Lightning dock components, a move that can be seen as a way of ensuring feedstock quality and consistency when using a number of different component manufacturers. It is also understood that a preferred supplier has been specified for the furnaces used to debind and sinter the parts.
What’s the appeal of MIM technology? The Powder Injection Molding (PIM) industry, which includes both metal (MIM) and ceramic (CIM) components, is currently estimated to generate sales of US$1.5 billion, with an annual growth rate of 15-20%.
With Apple announcing that five million units of the iPhone 5 were sold on the product’s launch weekend, and some analysts projecting that up to 200 million units could be sold over the next year, it is clear that demand for MIM components for Apple’s new generation range of connectors, to be used with all new Apple mobile devices, is set to rocket.
A multi-vertical, family-owned private equity firm, HF Companies comprises more than 110 global brands and employs approximately 11,000 people in 400 locations across the United States, Canada, and China.
Don't miss any new issue of PIM International, and stay up to date with the latest industry news. Sign up to our fortnightly newsletter.
Reach a truly international audience that includes component manufacturers, end-users, industry suppliers, analysts, researchers and more.
In 2006 Advanced Materials Technologies Pte Ltd, Singapore, won a Metal Powder Industries Federation (MPIF) award for a series of MIM parts for Motorola’s clamshell designed PEBL mobile phone. Ceramic Injection Molding (CIM) is also finding applications in this sector, particularly in the luxury market, with Dutch CIM producer Formatec Technical Ceramics B.V manufacturing black zirconia cover pieces for high-end Vertu mobile phones.
Apple’s new Lightning connector system, featured on the recently launched iPhone 5 and iPad mini, has given the international Metal Injection Moulding (MIM) industry a substantial boost thanks to its use of this advanced manufacturing process. The use of MIM in the Lightning connector has resulted in a surge in demand for MIM grade powders and a drive to install additio nal component manufacturing capacity.
"Viking Plastics has laid the groundwork essential for expansion, supported by its robust team, advanced manufacturing capabilities, and distinctive commitment to culture,” said HF Companies co-CEO Geoff Hoffmann. “We are excited to enhance our investment in the US manufacturing sector with such a transformative organization."
Founded in 1972, Viking Plastics operates more than 50 injection molding machines and multiple automated assembly cells at plants in Kentucky, Indiana, and Pennsylvania. Headquartered in Corry, PA, Viking Plastics serves a broad customer base across North America as well as in international markets.
The Hoffmann Family of Companies announced today the acquisition of Viking Plastics, a custom injection molder serving the automotive, HVAC, and general industrial markets. Its clientele includes Ford, General Motors, Rheem, and Saft.
Discover suppliers of these and more in our advertisers’ index and buyer’s guide, available in the back of PIM International.
The free-to-access PIM International magazine archive offers unparalleled insight into the world of MIM, CIM and sinter-based AM from a commercial and technological perspective through:
The use of MIM in mobile phones is not new, with numerous keys, buttons and vibrators manufactured in large quantities by the Asian MIM industry for a diverse range of end-users. This new application in the Lightning connector is, however, one of the most important developments in terms of production volumes.
All key MIM grade powder suppliers have announced capacity increases over the last 12 months in anticipation of continuing industry growth.
It is understood that production is being met by primary Apple suppliers in Taiwan, some of whom have large MIM operations in China. Additional manufacturers in China are also reported to be engaged to help meet capacity.
With the use of multi-cavity tooling, which can often have 16 or even 32 cavities for some micro-sized components, and continuous debinding and sintering systems, a MIM facility is ideally suited to the high volume production of small precision components.
Powder Injection Moulding, which was first developed in the 1970s and commercialised in the 1980s, is regarded as an ideal process for the manufacture of small, high volume precision components and the technology has for many years been an essential manufacturing process for the telecommunications sector.
In addition to strengthening HF Companies' global portfolio, the acquisition also brings Viking Plastics’ advanced automation capabilities and ability to rapidly produce high-quality products into the fold, driving efficiency and margin expansion, said the private equity firm.
GETTING A QUOTE WITH LK-MOULD IS FREE AND SIMPLE.
FIND MORE OF OUR SERVICES:
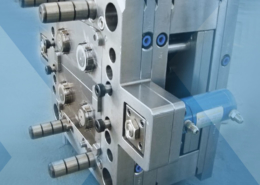
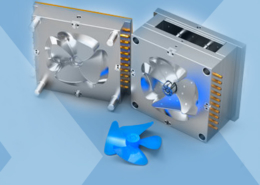
Plastic Molding

Rapid Prototyping
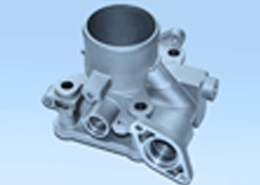
Pressure Die Casting
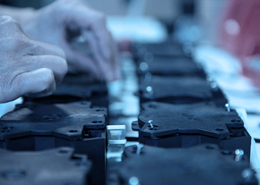
Parts Assembly
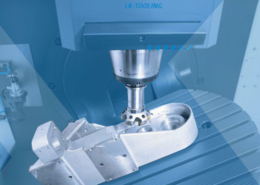