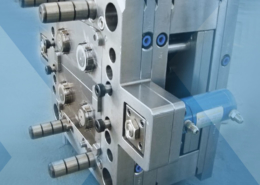
HDPE Prices Rise in Europe and Decline in Asia Due to Shifts in Supply and
Author:gly Date: 2024-09-30
KraussMaffei claims that its Adaptive Process Control (APCplus) system is the only controller on the market that uses material-specific compression curves for process control. The APCplus database contains all common material types that can be selected by the converter for process control.
The Fortify Digital Tooling material is the first launched by Fortify and believed to be the industry’s first microparticle filled DLP/SLA resin. By reinforcing this material with microparticle-sized engineering-grade ceramics, the company is able to produce additively manufactured tools that are stronger, stiffer, exhibit a higher heat deflection temperature, and an increased wear resistance compared to other 3D printed tooling. These are crucial metrics to maximise when designing a 3D printed tool due to the repeated exposure to high temperature polymers at high pressures.
The blue turtle that will be molded at the international plastics processing trade show has a black core made of mechanically recycled PC/ABS and an outer layer made of chemically recycled ABS.
Another sustainable aspect is removal of the cold runner sprue, which is then shredded and fed directly back into the production process for the core material. This is accomplished with the new mini sprue mill from partner Getecha, which is being used for the first time. This also creates a closed material cycle.
In terms of machine control, the simple switchover from skin to core melt flow ensures flexibility and quality at the same time. On the one hand, the skin material can be added to seal the sprue point. On the other hand, it is possible to switch between component A and B several times. This also allows marbling effects to be achieved for an individual design, for example.
Stephen has been with PlasticsToday and its preceding publications Modern Plastics and Injection Molding since 1992, throughout this time based in the Asia Pacific region, including stints in Japan, Australia, and his current location Singapore. His current beat focuses on automotive. Stephen is an avid folding bicycle rider, often taking his bike on overseas business trips, and a proud dachshund owner.
The all-electric PXZ 121 Multinject demos a high-quality sandwich application with a high proportion of recycled material at Fakuma. Image courtesy of KraussMaffei.
Traditionally, injection mould tools made for prototyping are produced by machining a large block of aluminium, which can cost thousands of dollars and is subject to long lead times, often upwards of six weeks. Boston-based composite 3D printing company Fortify has created a digital tooling process that gave Catalysis Additive Tooling the ability to create quick-turn injection mould tools at a fraction of the cost and time.
The patented APCplus machine function now incorporates individual grade-specific property data. Image courtesy of KraussMaffei.
By reinforcing the resin with engineering-grade ceramic microparticles, Fortify achieved optimum mechanics compared to other additive techniques, which suggests that Digital Tooling can offer comparable performance to aluminium soft tooling with shorter lead times and lower costs.
Accelerating time-to-market when launching a new product is invaluable in enabling R&D teams to stay competitive. The need to produce agile prototypes faster and accurately evaluate the geometry, design, performance and feel of plastic injection moulded parts is necessary before creation of the final mould. However, the cost and lead time associated with machining aluminium soft tooling can make many iterations impractical for most organisations.
Tooling and dynamic mold temperature control are supplied by partner Contura MTC. Near-contour temperature control optimizes the entire production process and is particularly important in order to achieve the required high-quality surface of the turtle at economical cycle times.
KraussMaffei will exhibit at stand 7303 in hall A7 at Fakuma, the international plastics processing trade show in Friedrichshafen, Germany, on Oct. 15 to 19.
The all-electric 1200-kN clamping force PXZ 121 Multinject features a compact, space-saving Z-position configuration for the electric injection units. In addition, the attached, removable sandwich platen offers a high degree of flexibility in production. This means that the PXZ 121 can be used as a single-component, two-component, or sandwich machine without any additional effort.
Lightweight, with a glossy surface and a sustainable message, describes the small blue turtle that will be produced on an all-electric PXZ 121-380-180 Multinject press using the sandwich process at the KraussMaffei stand at Fakuma. It has a black core made of mechanically recycled polycarbonate/acrylonitrile-butadiene-styrene (PC/ABS) and a high-quality outer layer made of chemically recycled ABS.
Using fibre-reinforced systems and materials, the tools are said to function better than traditional 3D printed injection mould tools and eliminate the need to wait weeks for an aluminium tool.
Groups like Catalysis Additive Tooling specialise in creating injection moulded prototype parts that allow designers and engineers to run tests on a product and gather customer feedback before going into full scale production, de-risking investment in production tooling costs. Because of this need, it is invaluable for their customers to prototype their parts in their end-use plastic as soon as possible.
The core material of the durable turtle at Fakuma consists of mechanically recycled PC/ABS E-Loop 5120MR from Elix Polymers. However, a foamed or reinforced core made from recycled material is also feasible and offers further potential for sustainable production. The visible, high-quality outer skin is made of chemically recycled and processed ABS E-Loop P2H-AT CR, which can be supplied in various colors.
"The increased use of recyclates has brought sandwich technology back into focus in multi-component technology and offers great potential,” said Manuel von Varchmin, responsible for sales of injection molding technology and automation at KraussMaffei. “Thanks to its precision, efficiency, and flexibility, our all-electric PXZ Multinject version is ideally suited for this. We will be demonstrating this at Fakuma using the example of the Turtle project, which we have implemented with Contura MTC and other partners."
“I believe the growing use [in] tooling and moulding is due to the buying market maturing and the awareness of additive manufacturing increasing. Many companies are in the early phases of adopting additive manufacturing. Additive tooling wins are much lower risk than full adoption of additive manufacturing. Tooling in many ways is a perfect “gateway” application to customers’ transition to the new technology platforms of AM.”
In one case, this led to a 35% reduction in cost compared to CNC machining and a 3 to 5 day lead time for over 200 parts produced using a tool measuring 100 x 95 x 150 mm. According to Fortify data, the same tool produced on a laser sintering system would have cost more than three times the amount for the same number of parts, while polymer material jetting would have been slightly cheaper but would only have provided 25 parts.
“We are currently focused on short run injection mould tooling - an application that has been attempted for years with limited success and adoption with other 3D print technologies,” Josh Martin, CEO and Co- Founder at Fortify, explained. “The primary reasons for this come down to a lack of performance of available polymer materials or challenging workflows with metals. Fortify Digital Tooling is different because we are reinforcing high-temperature thermoset systems with specialised ceramics to improve strength, stiffness, wear resistance and performance at temperature. When we couple this material system with DLP technology, we are able to achieve a surface finish that does not need secondary machining. So the complete package [offers] both higher performance and less processing. We are excited to explore other tooling applications where we can add value.”
The Turtle project combines a high-quality mold with a high-performance, all-electric injection molding machine from the PX series and the new LRXplus linear robot. This combination brings clear economic benefits with an early ROI, while at the same time using valuable resources responsibly.
KraussMaffei is going one step further at Fakuma. All materials for use on the PXZ 121 Multinject come from Elix Polymers, which, like KraussMaffei, is also a Sinochem Group company. With specific material parameters from Elix Polymers integrated into the APCplus database, the machine function is precisely adjusted to the material being processed, making the injection molding process even more precise and efficient overall.
Part removal, separation from the sprue, separation into the grinder, and depositing on the belt are automated by the new LRXplus linear robot, which is premiering at Fakuma together with the MC7 control system. The LRXplus from KraussMaffei offers numerous new functions that make production even more flexible and economical. Thanks to its compatible interfaces, the LRXplus can be combined with almost any system, whether with KraussMaffei injection molding machines, injection molding machines from other manufacturers, or as a standalone solution for all other automation tasks.
Numerous features of the PXZ 121 injection press — such as the new sandwich platen, near-contour mold temperature control from partner Contura MTC, and the APCplus machine function, which uses specific property values of different resin grades — make the multi-component process even more efficient and economical, according to KraussMaffei.
GETTING A QUOTE WITH LK-MOULD IS FREE AND SIMPLE.
FIND MORE OF OUR SERVICES:
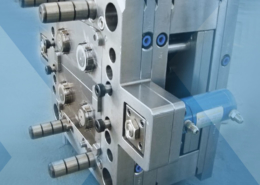
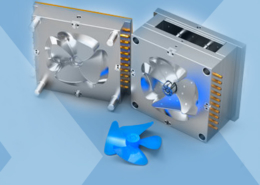
Plastic Molding

Rapid Prototyping
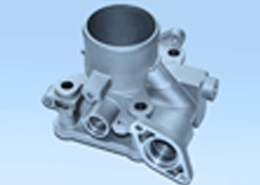
Pressure Die Casting
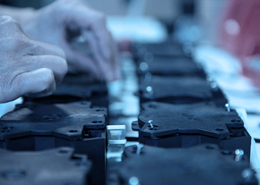
Parts Assembly
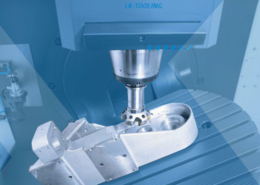