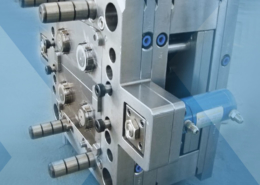
HDPE Prices Rise in Europe and Decline in Asia Due to Shifts in Supply and
Author:gly Date: 2024-09-30
“We’re building up our design capability,” adds Ritzema. “We already understand design for manufacturability, and we can evaluate customers’ designs for potential tooling, molding, and assembly problems. We help to design for automation where possible.” This knowledge is especially vital in LSR jobs. “Few customers understand LSR design. They don’t realize how it can flash through half a mil gap.”
While prices moved up for three of the five commodity resins, there was potential for a flat trajectory for the rest of the third quarter.
Second quarter started with price hikes in PE and the four volume engineering resins, but relatively stable pricing was largely expected by the quarter’s end.
“We’ve tried to create a platform that combines the benefits from 3D printing with injection moulding, so you get the same low start-up costs, short lead times and design freedom, but the baseline is injection moulding. That means we can process all the materials that an injection moulding user would normally want to process: all those pre-qualified grades for the automotive industries, all the pre-qualified grades for the aerospace industries, the stuff you use for medical devices, which also have to be biocompatible. Most of those materials are not available as 3D printable materials, but FIM allows us to process them off the shelf.”
These smartphone cases consist of two-shot molded TPU on TPU in different colors and durometers, with an inserted PC ring that forms the camera window. This job was “reshored” from China.
Then and now: In 1946, Rogan Corp. began compression molding phenolic knobs and dials for appliances. Today, Rogan is clean-room molding LSR, including overmolding of metal and thermoplastics on this vertical Sodick press.
Today, Rogan Corp. is a $10-million business with some 65 employees in a 45,000-ft2 plant in Northbrook, Ill. Rogan specializes in liquid silicone (LSR), two-shot, and insert molding for medical, electronic, aerospace, telecommunications, appliance, lawn/garden, and sports/recreation industries. But while it is pursuing some of the hottest areas of injection molding innovation, Rogan also remains tied to its roots.
Mike Sepe has authored more than 25 ANTEC papers and more than 250 articles illustrating the importance of this interdisciplanary approach. In this collection, we present some of his best work during the years he has been contributing for Plastics Technology Magazine.
In this collection of content, we provide expert advice on welding from some of the leading authorities in the field, with tips on such matters as controls, as well as insights on how to solve common problems in welding.
Medical is Rogan’s main growth target. It accounts for the installation of the company’s first “hard” clean room, with 1500 ft2 devoted entirely to LSR molding and assembly. Previously, Rogan used some portable, soft-sided clean-room machine enclosures and may use them again, though it is already planning a Phase II expansion of the permanent clean room.
Across the show, sustainability ruled in new materials technology, from polyolefins and engineering resins to biobased materials.
Exhibitors and presenters at the plastics show emphasized 3D printing as a complement and aid to more traditional production processes.
These moulds are then placed in an injection moulding machine – AddiFab exhibited alongside a Babyplast system at TCT Show – where a material will be pressed into the mould’s cavity. The mould is then dissolved, inlets and outlets trimmed away, and the final part revealed. Because AddiFab only expects the printed moulds to last one shot, the company says it can process thousands of high-performance injection moulding materials – from flame retardant ABS grades to ultra-soft TPEs to carbon- reinforced PPA injection moulded at 350°C – and enable users to validate their components before scaling to thousands of parts with the same material and the same technology.
Ultradent's entry of its Umbrella cheek retractor took home the awards for Technical Sophistication and Achievement in Economics and Efficiency at PTXPO.
In Birmingham, UK in September, AddiFab pitched this to hordes of visitors who, at times, waited up to 20 minutes to learn about FIM. Talking to TCT - just the ten-minute wait for us - Staal revealed the motivation behind the company’s cross over between additive manufacturing and injection moulding.
The Plastics Industry Association (PLASTICS) has released final figures for NPE2024: The Plastics Show (May 6-10; Orlando) that officially make it the largest ever NPE in several key metrics.
LSR is the fastest-growing business sector at Rogan, fueled by expertise in bonding silicone to thermoplastics (PC/ABS in left photo).
In a time where sustainability is no longer just a buzzword, the food and beverage packaging industry is required to be at the forefront of this innovation. By adopting circular packaging processes and solutions, producers can meet regulatory requirements while also satisfying consumer demand and enhancing brand reputation. Join Husky to learn more about the broader implications of the circular economy — as well as how leading brands are leveraging this opportunity to reduce costs, increase design flexibility and boost product differentiation. Agenda: The cost and operational benefits of embracing circularity Key materials in circular packaging — including rPET and emerging bioplastics How to design a circular food and beverage package Strategies for selecting sustainable closures to future-proof packaging solutions Optimization and streamlining of production processes for enhanced efficiency How Husky Technologies can enable your sustainable success
Rogan quickly became expert at molding LSR with very tight tolerances and difficult shapes. “Customers are always pushing the limits,” says Ritzema. “They ask us, ‘How thin can you go?’ We have molded a 4-mil LSR bottom onto the PC rim of a petri dish 3 inches in diameter,” says Ritzema. “We can hold half a mil tolerance on an 8-mil-thick diaphragm that’s overmolded onto a PC rim. We’re also one of the few firms with experience in molding optical-grade LSR.”
These materials are the kind to feature on approved lists inside factories in the aerospace, automotive, and medical industries. There are similar documents at Danfoss, a company currently testing FIM, which include grades such as PEEK and 40% glass-filled PPS, the former of which is notoriously not the easiest to 3D print, and the latter of which is barely 3D printable at all. It means that Danfoss is rarely able to 3D print prototypes of parts in the same materials it intends to use when it steps into production.
“Because of minimum order quantity, a lot of products get scrapped,” Staal said. “With Freeform Injection Molding, we don’t have a minimum order quantity. That means [users] can move into the market incrementally. When you hit the tipping point where you can see that it now makes sense to invest in a tool, you can make that investment because your demand is there. You can step away from Freeform Injection Molding into conventional injection moulding, but you haven’t over-invested in capacity from the beginning and you can do the capacity investment when demand has been verified. That means you save a lot of material and you save a lot of energy in the start-up of a new product.”
Join Wittmann for an engaging webinar on the transformative impact of manufacturing execution systems (MES) in the plastic injection molding industry. Discover how MES enhances production efficiency, quality control and real-time monitoring while also reducing downtime. It will explore the integration of MES with existing systems, emphasizing compliance and traceability for automotive and medical sectors. Learn about the latest advancements in IoT and AI technologies and how they drive innovation and continuous improvement in MES. Agenda: Overview of MES benefits What is MES? Definition, role and brief history Historical perspective and evolution Longevity and analytics Connectivity: importance, standards and integration Advantages of MES: efficiency, real-time data, traceability and cost savings Emerging technologies: IoT and AI in MES
AddiFab is a company positioning itself in the in-between, hoping to relieve manufactures of the above considerations: “I see a gap between the prototyping and production that is not really being remedied by many 3D printing solutions,” Stall emphasised. The company has brought to market Freeform Injection Molding (FIM) and a portfolio of open digital light processing (DLP) 3D printers promising high precision and high repeatability for the additive manufacture of advanced single-use moulds with proprietary tooling resins.
Join KraussMaffei for an insightful webinar designed for industry professionals, engineers and anyone interested in the manufacturing processes of PVC pipes. This session will provide a comprehensive understanding of the technology behind the production of high-quality PVC pipes: from raw material preparation to final product testing. Agenda: Introduction to PVC extrusion: overview of the basic principles of PVC pipe extrusion — including the process of melting and shaping PVC resin into pipe forms Equipment and machinery: detailed explanation of the key equipment involved — such as extruders, dies and cooling systems — and their roles in the extrusion process Process parameters: insight into the critical process parameters like temperature, pressure and cooling rates that influence the quality and consistency of the final PVC pipes Energy efficiency: examination of ways to save material and energy use when extruding PVC pipe products
What happens in between often requires a lot of thought, even more action, and more time than anybody would like to spend. It’s likely that prototypes are 3D printed in one material and the subsequent end-use components injection moulded or machined in another.
Despite price increase nominations going into second quarter, it appeared there was potential for generally flat pricing with the exception of a major downward correction for PP.
After successfully introducing a combined conference for moldmakers and injection molders in 2022, Plastics Technology and MoldMaking Technology are once again joining forces for a tooling/molding two-for-one.
LSR accounts for only about 10% of Rogan’s current sales, but that share could soon double, because 40-50% of its new business is in LSR, says Robert Flammini, v.p. of sales and marketing. “LSR and two-shot molding are the areas we want to grow in,” says Ritzema. “We don’t want to compete in commodity molding.”
A collaboration between show organizer PLASTICS, recycler CPR and size reduction experts WEIMA and Conair recovered and recycled all production scrap at NPE2024.
Mitsubishi Chemical sees FIM as a possible gateway into the additive space, having users of FIM process o the shelf injection mouldable materials to produce prototypes, and perhaps draw conclusions as to the demand that way. That, AddiFab told TCT, is a main goal of the collaboration – and its general industrialisation efforts – but beyond, conversations are still to be had about how the partnership moves forward.
After completely filling the classroom last year, the Silicone Elastomers Technology and Fabrication course returns to Pomona, Calif. Jan. 31-Feb. 3.
August 29-30 in Minneapolis all things injection molding and moldmaking will be happening at the Hyatt Regency — check out who’s speaking on what topics today.
“We want to get bigger in contract manufacturing,” says Bob Flammini. “OEMs want a single supplier for a full turnkey package. We can supply molding and pad printing, hot stamping, heat staking, ultrasonic welding, kitting, and packaging. We want to be a total solution provider.”
Rogan buys Sumitomo Demag presses for one- and two-shot thermoplastic molding. “Without experience in this field, it’s hard to buy a two-shot machine,” says Ritzema. There really is no ‘general-purpose’ model. A lot of two-shot jobs are very specific, and there are so many different types of machine and tooling design. You could spend $500,000 on a machine that might not work for half the jobs out there.” Rogan gains an edge in two-shot molding from its proprietary mold designs. Explains Ritzema, “We have hundreds of modular mold bases that allow us to load cavity and core inserts for different jobs from the mold face. It adds flexibility and reduces tooling cost. We also have a proprietary rotating mold base.”
Additive technology creates air pockets in film during orientation, cutting down on the amount of resin needed while boosting opacity, mechanical properties and recyclability.
Resin drying is a crucial, but often-misunderstood area. This collection includes details on why and what you need to dry, how to specify a dryer, and best practices.
technotrans says climate protection, energy efficiency and customization will be key discussion topics at PTXPO as it displays its protemp flow 6 ultrasonic eco and the teco cs 90t 9.1 TCUs.
In 1967, the firm bought its first injection machines and began insert molding plastic over metal. In 1969, Rogan Corp. received a commendation from the U.S. government for its contribution to the first moon landing. “We believe we had a knob on the instruments that collected or analyzed moon rocks,” Ed Rogan explains.
Learn about sustainable scrap reprocessing—this resource offers a deep dive into everything from granulator types and options, to service tips, videos and technical articles.
One of Rogan’s customers is developing a home dialysis device that is PC with eight small TPE bladder inserts. These are overmolded at present but eventually will be in two-shot production.
Mold maintenance is critical, and with this collection of content we’ve bundled some of the very best advice we’ve published on repairing, maintaining, evaluating and even hanging molds on injection molding machines.
"That is a risky process because it entails new validations, it entails new materials, it entails extra time, extra costs,” Lasse G Staal, Co-founder and CEO of AddiFab, said for possibly the umpteenth time on the third afternoon of TCT Show.
“If you’re basing your prototyping on 3D printing, you may get to a point where you get it qualified, then you need to decide how to produce. If you want to scale up to massive levels, you need to go into injection moulding because 3D printing is neither cost competitive nor quality competitive for higher volumes,” Staal argued. “If you decide ‘I’m only going to sell this [product] in low volumes’, then stay with 3D printing, but you need to make that decision before you go into market. That’s a pretty important decision to make.
Gifted with extraordinary technical know how and an authoritative yet plain English writing style, in this collection of articles Fattori offers his insights on a variety of molding-related topics that are bound to make your days on the production floor go a little bit better.
Join this webinar to explore the transformative benefits of retrofitting your existing injection molding machines (IMMs). Engel will guide you through upgrading your equipment to enhance monitoring, control and adaptability — all while integrating digital technologies. You'll learn about the latest trends in IMM retrofitting (including Euromap interfaces and plasticizing retrofits) and discover how to future-proof your machines for a competitive edge. With insights from industry experts, it'll walk you through the decision-making process, ensuring you make informed choices that drive your business forward. Agenda: Maximize the value of your current IMMs through strategic retrofitting Learn how to integrate digital technologies to enhance monitoring and control Explore the benefits of Euromap interfaces and plasticizing retrofits Understand how retrofitting can help meet new product demands and improve adaptability Discover how Engel can support your retrofitting needs, from free consultations to execution
Meanwhile, LSR adhesion to metal “still has a ways to go,” in Ritzema’s opinion, “especially for small parts with little surface area to bond to. We’ve tried primers. We’ve tried plasma treating metal, but it didn’t help.”
Join Engel in exploring the future of battery molding technology. Discover advancements in thermoplastic composites for battery housings, innovative automation solutions and the latest in large-tonnage equipment designed for e-mobility — all with a focus on cost-efficient solutions. Agenda: Learn about cutting-edge thermoplastic composites for durable, sustainable and cost-efficient battery housings Explore advanced automation concepts for efficient and scalable production See the latest large-tonnage equipment and technology innovations for e-mobility solutions
The key to Rogan’s success in LSR overmolding has been the arrival of “bondable” silicones that adhere well to thermoplastics. Rogan has formed a close relationship with its main LSR material supplier, Shin-Etsu Silicones, which has helped it deal with adhesion issues. Though bondable LSR works well with thermoplastics, there still can be occasional problems. In one case, Rogan was buying a polycarbonate part from another molder and found that overmolded LSR was not adhering as expected. The culprit turned out to be mold release on the PC part.
“Mitsubishi Chemical has aligned now with Freeform Injection Molding as a platform, it has a clear need we have demonstrated we can meet, but I’m not sure either Mitsubishi or AddiFab know where the collaboration is going to end up in a couple of years,” Staal finished. “We can see some evident opportunities with the KyronMAX, Tefabloc, Trexprene and DIAKON series of materials – materials which are difficult to 3D print. But I think Mitsubishi Chemical has about 450 subsidiaries. I haven’t even started talking to ten of them yet. It’s going to be a very interesting journey.”
“We’re bidding on bigger jobs now,” says Flammini, “so we’re looking at bigger machines for more cavities.” Rogan wants to go smaller, too. It has ordered a 20-ton Sodick press with a 14-gram shot capacity to mold smaller thermoplastic parts.
The other arm of Rogan’s growth strategy is two-shot molding. “We were pushed into it by one of our biggest customers,” says executive v.p. David Schoessow, who has been with the company for 34 years. “They wanted soft-touch knobs. We did two-shot even before we had tried insert overmolding.”
Plastics Technology’s Tech Days is back! Every Tuesday in October, a series of five online presentations will be given by industry supplier around the following topics: Injection Molding — New Technologies, Efficiencies Film Extrusion — New Technologies, Efficiencies Upstream/Downstream Operations Injection Molding — Sustainability Extrusion — Compounding Coming out of NPE2024, PT identified a variety of topics, technologies and trends that are driving and shaping the evolution of plastic products manufacturing — from recycling/recyclability and energy optimization to AI-based process control and automation implementation. PT Tech Days is designed to provide a robust, curated, accessible platform through which plastics professionals can explore these trends, have direct access to subject-matter experts and develop strategies for applying solutions in their operations.
While pinning much of its growth strategy on LSR, Rogan acknowledges that competition is growing in this area. Ritzema thinks the LSR market is expanding enough to accommodate new players. “The greatest difficulty in getting started in LSR,” he says, is finding experienced people. Until recently there were no school programs for LSR engineering.”
AddiFab believes FIM has the capacity to resolve this issue and encourages manufacturers to work backwards from how they intend to manufacture their part in order to decide how to prototype it.
In this three-part collection, veteran molder and moldmaker Jim Fattori brings to bear his 40+ years of on-the-job experience and provides molders his “from the trenches” perspective on on the why, where and how of venting injection molds. Take the trial-and-error out of the molding venting process.
An example of two-shot, hard/soft molding is a child’s dinnerware set of PP and TPE. Another is a smartphone cover of TPU molded on TPU—two colors and durometers—with an insert of a thin PC ring for the phone’s camera window. What’s notable about these parts is that they are both examples of “reshoring” jobs that had been outsourced to China. They came back here because of issues with quality and logistics—transportation time and cost, according to Ritzema. “We’re even shipping some parts to China,” he adds. That’s because medical OEMs are more comfortable with domestic manufacture.
Successfully starting or restarting an injection molding machine is less about ticking boxes on a rote checklist and more about individually assessing each processing scenario and its unique variables.
Right from the start, Rogan jumped into LSR overmolding onto stainless steel and thermoplastics like PC, PC/ABS, nylon, PBT, and Ultem polyetherimide (PEI). At present, all such jobs involve insert overmolding the thermoplastic or metal component, though true two-shot thermoplastic/LSR molding is the logical next step for high-volume jobs. The company is even looking into two-shot LSR-on-LSR molding. “It’s not easy to do soft on soft,” cautions Ritzema. “Shutting off steel on a soft material is tricky.”
Today’s Rogan Corp. is a mix of old and new. Dials and knobs remain 65% of its business. Three thermoset compression molding presses still get some use. “We’ve been making some of these products for as long as 40 years,” says Operations director Jim Ritzema. “They still pay the bills.”
Plastics processors are finding applications for 3D printing around the plant and across the supply chain. Here are 8 examples to look for at NPE2024.
“We began strategic planning for an entry into LSR in 2003,” recalls Ed Rogan. “That was just after the SARS epidemic hit. We saw the trend in hospitals to replace devices in contact with patients more frequently, such as every eight hours instead of once a day. That made it more economical to purchase more costly but re-sterilizeable components instead of disposables.”
In 1946, the company acquired three war-surplus compression molding presses and began making its own phenolic knobs and dials. Ed Rogan II, son of one of the founders (and now the sole owner), joined the family enterprise in 1949 at six years old, earning a Chicago Cubs game ticket for inserting 5000 screws in a 6-hr shift, doubtless violating all sorts of child-labor laws by today’s standards.
Plastics Technology covers technical and business Information for Plastics Processors in Injection Molding, Extrusion, Blow Molding, Plastic Additives, Compounding, Plastic Materials, and Resin Pricing. About Us
Thousands of people visit our Supplier Guide every day to source equipment and materials. Get in front of them with a free company profile.
In this collection, which is part one of a series representing some of John’s finest work, we present you with five articles that we think you will refer to time and again as you look to solve problems, cut cycle times and improve the quality of the parts you mold.
While prices moved up for three of the five commodity resins, there was potential for a flat trajectory for the rest of the third quarter.
The three Rogan brothers left Winnipeg, Manitoba, in 1927 to seek their fortune in Chicago. They founded Rogan Brothers Co. in 1934, providing calligraphy services to retailers, schools, and churches. They broke into plastics in 1937—on a wager. A business acquaintance bet Nick Rogan a fifth of whiskey that he couldn’t invent a process for decorative marking on plastics. By 4:00 AM the next morning, Nick had come up with a “branding” technique that family legend holds to be the origin of what is now called hot stamping.
Today, two-shot molding is around 40% of Rogan’s business (including some dial and knob applications), and nine of its 34 thermoplastic presses have two-shot capability.
This month’s resin pricing report includes PT’s quarterly check-in on select engineering resins, including nylon 6 and 66.
Rogan’s growth in medical molding is spearheaded by a new 1500-ft2, Class 100,000 clean room that houses four LSR molding machines, both horizontal and vertical.
Sustainability continues to dominate new additives technology, but upping performance is also evident. Most of the new additives have been targeted to commodity resins and particularly polyolefins.
The appliance industry eagerly embraced this new method for decorating plastic knobs and dials as a replacement for time-consuming engraving and “paint-and-wipe” methods. Throughout the 1930s and ’40s, Rogan Brothers thrived in marking plastic knobs and military equipment, such as dials for gun turrets.
Mixed in among thought leaders from leading suppliers to injection molders and mold makers at the 2023 Molding and MoldMaking conferences will be molders and toolmakers themselves.
How does Rogan keep abreast of this fast-moving area of technology? Ritzema responds, “We read, go to seminars, do as much investigating as possible. We discovered Sodick at a trade show. And we have learned a lot from the LSR materials people, who helped us through a lot of adhesion problems.”
From compression molding phenolic knobs and dials to overmolding liquid silicone rubber onto metal and thermoplastics, the 78-year history of the Rogan Corp. is full of twists and turns—what chairman Edward Rogan calls “transformations” in his decade-by-decade narration on the company’s website (rogancorp.com). But one consistent theme stands out—an adventurous and inventive spirit that has put Rogan on the leading edge of a number of important trends in plastics—and even on the frontiers of space exploration.
After field testing, validation and refinement with customer feedback, Husky announced the introduction of a cold-deck system for direct gate molding of LSR.
Walk the floor at an additive manufacturing trade show and one will find companies pitching their solutions for the design and prototyping of a product, the manufacture and measurement of the parts, and everything in between.
Rogan is getting into smaller parts, like mini-microphones of Ultem and stainless steel overmolded with LSR. Versions above do not contain Ultem.
Take a deep dive into all of the various aspects of part quoting to ensure you’ve got all the bases—as in costs—covered before preparing your customer’s quote for services.
Another LSR overmolded part is a medical device (cervical seal) consisting of a section of thin PC tubing with 5-6 mil LSR fins molded onto it. Another part (lung catheter) is a 30-in.-long tube of Pebax TP elastomer from Arkema with an LSR finned “bumper” molded onto the end. A tiny button-sized device that is actually a miniature microphone consists of stainless steel and Ultem encapsulated in LSR. Another developmental medical part (arterial shunt) consists of a stainless-steel spring overmolded with two separate shots of LSR.
While the major correction in PP prices was finally underway, generally stable pricing was anticipated for the other four commodity resins.
Formnext Chicago is an industrial additive manufacturing expo taking place April 8-10, 2025 at McCormick Place in Chicago, Illinois. Formnext Chicago is the second in a series of Formnext events in the U.S. being produced by Mesago Messe Frankfurt, AMT – The Association For Manufacturing Technology, and Gardner Business Media (our publisher).
Similar tentativeness in launching products into market can be found at Mitsubishi Chemical, who recently invested in AddiFab as their partnership intensified. The company would quite like to make around 7,500 of its materials available in the additive manufacturing space, but with further hardware and process developments still needed, Mitsubishi can’t place an accurate measure on demand for many of its products. Without a guarantee of demand, the company is reluctant to invest in the required conversion processes.
Discover how artifical intelligence is revolutionizing plastics processing. Hear from industry experts on the future impact of AI on your operations and envision a fully interconnected plant.
Multiple speakers at Molding 2023 will address the ways simulation can impact material substitution decisions, process profitability and simplification of mold design.
Introduced by Zeiger and Spark Industries at the PTXPO, the nozzle is designed for maximum heat transfer and uniformity with a continuous taper for self cleaning.
LSR is the key to its medical market focus. “LSR can be autoclaved,” notes Ritzema. “It has low compression set, and its flexibility allows it to be demolded from large undercuts on both cavity and core sides.”
While AddiFab is looking to meet the accuracy, repeatability and materials standards of the injection moulding space, it also hopes FIM can bring change to the sector. A big driver for the commercialisation of FIM was to help companies produce small volumes in the early days of product development to test the water. Typically, companies have to meet a minimum order quantity to injection mould parts but, prior to launch, will often be uncertain of the level of demand in the marketplace.
One of Rogan’s specialties is overmolding LSR onto metals and thermoplastics. Inset: This medical part consists of a thin PC tube overmolded with LSR fins 5-6 mils thick.
“If I want to be able to scale into the millions, then I want to start with injection moulding from day one. The decision point is not, 'do I want to prototype on a 3D printer?' It's, 'what is my end production going to be? Is it going to be a highly specialised geometry or is it going to be a high run of product?’ If it’s high run, let’s start with injection moulding from day one. That’s why we’ve built this platform and that’s why we want to be able to comply with the requirements of the injection moulding industry.”
In 1982, Rogan pioneered the new field of multi-material or two-shot injection. This led to hard/soft overmolding of TPE onto rigid thermoplastics—another headstart in what is now a booming specialty. In 1991, Rogan was one of the early practitioners of gas-assist molding. The latest “transformation” was Rogan’s 2006 entry into liquid silicone—jumping right into overmolding LSR onto stainless steel and polycarbonate (PC). And just this year, the company built a Class 100,000 clean room to house its four horizontal and vertical LSR presses.
When, how, what and why to automate — leading robotics suppliers and forward-thinking moldmakers will share their insights on automating manufacturing at collocated event.
Rogan started out in LSR with a Nissei press but now prefers Sodick Plustech machines because it finds their V-Line two-stage screw/plunger injection system to be more precise, since there’s no check valve to leak. One of its presses is a 150-tonner, which is on the large side for LSR. The Sodick machines are electric/hydraulic hybrids, but Rogan may look into all-electrics in the future. Rogan uses LSR mixing/metering systems from Fluid Automation, Inc. While Rogan works with several moldmakers that specialize in LSR (M.R. Mold, Kingson Mold, and Roembke), Rogan uses its own cold-deck design. All its LSR molds use cold runners to avoid discarding cured waste that costs $8 to $13/lb.
Rogan’s first exposure to plastics in the 1930s was hot stamping (a process it claims to have invented) of knobs and dials for appliances.
Processors with sustainability goals or mandates have a number of ways to reach their goals. Biopolymers are among them.
This Knowledge Center provides an overview of the considerations needed to understand the purchase, operation, and maintenance of a process cooling system.
In this collection of articles, two of the industry’s foremost authorities on screw design — Jim Frankand and Mark Spalding — offer their sage advice on screw design...what works, what doesn’t, and what to look for when things start going wrong.
Core Technology Molding turned to Mold-Masters E-Multi auxiliary injection unit to help it win a job and dramatically change its process.
Left to right, back row: Jim Ritzema, operations director; Tushar Patel, director of continuous improvement; Bob Flammini, v.p. of sales and marketing. Front row: David Schoessow, exec. v.p.; Ed Rogan, chairman and owner.
the 78-year history of the Rogan Corp. is full of twists and turns. But one consistent theme stands out—an adventurous and inventive spirit that has put Rogan on the leading edge of a number of important trends in plastics—and even on the frontiers of space exploration.
Across all process types, sustainability was a big theme at NPE2024. But there was plenty to see in automation and artificial intelligence as well.
While the melting process does not provide perfect mixing, this study shows that mixing is indeed initiated during melting.
The aim of this presentation is to guide you through the factors and the numbers that will help you determine if a robot is a smart investment for your application. Agenda: Why are you considering automation? What problems are you trying to solve? How and why automation can help Crunch the numbers and determine the ROI
Say “manufacturing automation” and thoughts immediately go to the shop floor and specialized production equipment, robotics and material handling systems. But there is another realm of possible automation — the front office.
GETTING A QUOTE WITH LK-MOULD IS FREE AND SIMPLE.
FIND MORE OF OUR SERVICES:
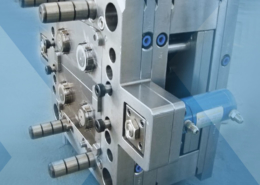
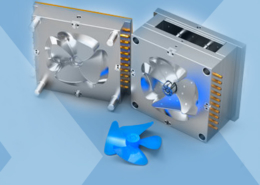
Plastic Molding

Rapid Prototyping
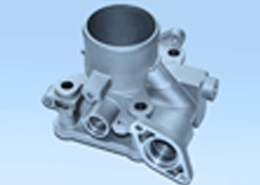
Pressure Die Casting
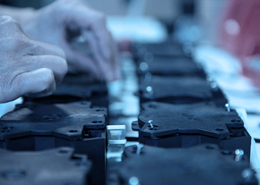
Parts Assembly
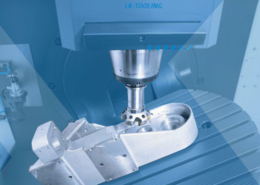