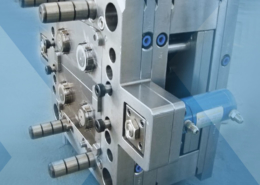
Handicapping Plastics M&A Winners and Losers in 2023 - plastics rotational moldi
Author:gly Date: 2024-09-30
Our existing business is focused on the automotive and amusement sectors and other miscellaneous fields. Moving forward, we would like to address new markets and have a third or fourth pillar for our business. To achieve that, we would like to approach and collaborate with various customers, regardless of the size of the company or the length of its history.
The reason is that we do not know which field will grow in the future. We used to have key products for the TV cabinet and we started molding for that component in 1955 which was the first time in the world, but at the time, there was not one TV per household. Today, the market has grown and now we have more than one TV per household. Perhaps one room has one TV. Even if the market is still small, if we see a potential for future growth, we will not hesitate to enter that field.
The Worldfolio provides business, industrial and financial news about global economies, with a focus on understanding them from within.
Raspberry Pi’s Eben Upton, Hailo’s DC Smalley, and Hellbender co-founders Brian Beyer and Adela Wee discuss the technology in a series of interviews on Covestro's YouTube channel recorded at CES.
Through your R&D, you made advancements and found a new application for Gas Assisted Injection molding technology. Can you give us a simple explanation of how Gas Assisted Injection molding is different or more effective in creating parts than conventional plastic injection molding?
The material in question is Covestro’s Makrolon TC thermally conductive polycarbonate, which its maker says “combines heat management with the properties next-generation materials demand: Functional integration, reduced weight, and reduced RF interference for wireless connectivity.”
A few years ago, we received a request for the same material for industrial cameras. Again, we worked with a partner to develop that material. It does not have a surface coating but the client wanted a good appearance and the same electromagnetic shield property and level of hardness. We achieved this with the new material and our client adopted it. Every year, Panasonic requests suppliers to come up with eco-friendly proposals and they evaluate them under the ECO-VC Initiative. We got the Gold Award in 2021 for this material.
As the devices — now in their fifth generation — became more powerful, Upton and his team packed their printed circuit boards with copper, all with the aim of siphoning away as much heat as possible from the central processing unit.
Just ask Eben Upton, CEO of Raspberry Pi Ltd. The UK-based firm makes small, single-board computers (SBCs) initially designed to help advance computer science in schools. Its products contain most of the components found in a traditional desktop computer, but the firm squeezes them all onto a small board about the size of a deck of playing cards.
We are seeing new components used for EVs that did not exist before. We make proposals for the designs of new components that need to be developed from scratch and work together with our customers to develop these.
Covestro says the PC heat sink can be part of an in-mold assembly process that can integrate LED modules directly into a vehicle’s headlamp housing, reducing both weight and labor.
Back in 1976, we launched about several B2C products. One was puzzles and another was big block toys for children to build houses. They did not sell very well so we stopped manufacturing B2C products. It was too early to launch to the market. I think that if we launch them now, they might sell better.
Low-cost Raspberry Pi CM4 board packs most of the functionality of a desktop computer onto this tiny device. Image courtesy of Raspberry Pi.
The other thing is we are trying to utilize the data generated from monozukuri to contribute to better efficiency in production. We believe the various data which can be received from making plastic products predict potential defects.
We do not have a presence in the overseas market at this time. We have plenty of collaboration, especially with material production companies. Our long-standing relationship and collaboration with Panasonic started because they used to use magnesium, which was expensive and hard to handle and they consulted with us to make an alternative material with the same properties. This was the component used for personal handheld digital cameras. They wanted to replace their existing material with plastic. I talked with several material production companies to address this request but it was difficult because magnesium has an electromagnetic shield property that plastic does not have. The client wanted to keep the same property and level of hardness. We mixed the plastic with carbon fiber to give the electromagnetic shield property and added hardness. This is how our new material was applied by Panasonic. This added to the complexity of the production process, however we overcame it and increased its productivity.
Since launching its first product in 2012, the company now has sold more than 56 million units, and its devices are finding use in mainstream computing applications.
Brian Beyer, co-founder and CEO of Pittsburgh-based computer vision company Hellbender Inc., also in an interview at CES, expanded on the potential benefits of using TC PC in the type of electronic component design and manufacturing that his firm does.
Pi, as the company is often called, donates its profits to the Raspberry Pi Foundation. The foundation is an educational charity that works to empower young people to use computing technologies.
About 20 years ago, we started again and launched Healthy Foot Washer because we wanted to have our original brand. Having our own brand made our employees happy. We got plenty of media exposure, which motivated our employees. In addition, we developed new products for traveling goods and Kasa Hotaru, an umbrella that shines by itself. It was shown on a TV program recently. The Healthy Foot Washer was also picked up by some TV programs. Recently, we have released new brands and one of them is SOEM. For branding and designing of SOEM, we are collaborating with a company specializing in designing and branding to develop it.
A Colorado molding company also is finding TC polymers to be very useful. X2F, a 6-year-old firm based in Loveland, has developed and patented a low-pressure process it calls Controlled Viscosity Molding. This low-pressure CVM process can overmold highly filled, thermally conductive polymer composites, which usually is difficult to do.
I am oriented toward the foreign market. I used to work in a foreign capital company and I used to live in a foreign country as well. When my predecessor entered the Singaporean market, I lived there for six years. However, the market of injection molding has become a commodity now. If we bring it as it currently is to foreign markets, we may not be able to be competitive when it comes to pricing. We are trying to change our business model to be competitive in the foreign market. Once we find a way to compete in the other markets, we would like to enter the overseas market with that new business model. I don't have any region in mind but it is going to be either Asia or North America.
Raspberry Pi CEO Eben Upton began developing his mini-computer in 2006 at the University of Cambridge in England. Image courtesy of Raspberry Pi.
TV cabinet produced in 1955 SOEM Healthy Foot Washer Gas Assist Injection Molding (interior) Previous Next
This also eliminates the need to use a separate antenna, which typically would be taped to a secondary plastic part of the product’s shell. “Now,” Beyer said, “the entire device can be made out of polycarbonate, and then it's a better look, fit, and finish, and more texture can be applied.”
A molded plastic parts manufacturer first established over 100 years ago, Daimei Plastic is a leading light when it comes to sustainable innovation.
Colorado-based X2F developed its own molding machine to use its patented Controlled Viscosity Molding process. The system’s very low pressures make it safer to overmold materials onto highly sensitive electronics. Image courtesy of X2F.
Pi now may have another option. It is intrigued by the possibility of overmolding its boards with thermally conductive (TC) polycarbonate (PC) to replace the previously required metal heat sinks. Upton, a Welshman who first began developing his mini-computer in 2006 at the University of Cambridge, calls the concept of TC PC “fascinating.”
Velo AI Inc., meanwhile, is leveraging these technologies to help make cyclists safer. The Pittsburgh firm is using Hellbender’s manufacturing services and a chip from Hailo Technologies Ltd. in a Raspberry Pi computer module 4 (CM4) to create what it calls “smart tech for your bike.”
Using a thermally conductive polycarbonate, he suggests, can dramatically lower the assembly cost and the end item cost of a product.
You are celebrating your 109th year anniversary this year. If we come back six years from now and have this interview again, what goals and dreams would you like to have accomplished by then?
CEO Mike Slowik said in an interview at CES that X2F (short for Extrude to Fill) developed its own, proprietary molding machine. It uses a pulse-packing process that precisely modulates polymer viscosity and material flow into the mold cavity at pressures some 70 to 90 percent lower than with standard injection molding. This helps to reduce molded-in stresses and damage to sensitive components during overmolding.
The technology, says Velo, also has the ability to capture and store images, including, for example, license plate numbers. This could come in handy if one needs to identify the parties involved in an incident on the road.
Electronics makers continue to pack more power into ever-smaller form factors. And, increasingly, they are also adding artificial intelligence (AI) capabilities to their products. This may offer benefits to the consumer, but it also raises the stakes when it comes to keeping device temperatures down as computing power rises.
Hailo, an Israeli maker of AI edge processors, plans to incorporate Covestro’s thermally conductive polycarbonate into some of its future products, according to DC Smalley, Hailo’s North America general manager. Its Hailo 8 chip, for instance, powers Velo’s CoPilot product.
“There are situations,” he said, “where you don't want to use metal because you want to be RF transparent. You want to be able to use Wi-Fi, you want Bluetooth connectivity. Then the PC heat sink is going to be a great option because now we can use this as a part of our overall enclosure design.”
It can understand when one is about to overtake and identify an aggressive or distracted driver approaching dangerously. In such cases, it issues audible and visual alerts for the cyclist to help prevent dangerous situations and crashes, as shown in the video below.
Lee Kuan Yew is the founding father of Singapore. He loved Japan and often talked about the story of chopsticks. He knew of the Japanese kaizen philosophy of constantly improving products. He wanted to incorporate the kaizen culture into Singapore. The Japanese are not good at disruptive innovation but we are good at sustainable innovation. Automotive makers in Europe are familiar with the term kaizen. In our company, each engineer on the gemba can come up with an idea for kaizen. The Japanese have high-quality products because they pursue perfection in their products. This is what keeps us competitive.
When it comes to EVs, lightweight parts are required. The Gas Assist Injection molding technology was a proposal we made to improve the surface appearance of thick plastic surfaces with sink marks. We improved the technology to be used for lightweight automotive parts. We improve and look for new applications for existing technologies to meet customer demands.
The Japanese advantage is the ability to see something through to the end. We are good at sustainable innovation. The Japanese are very detail oriented and skillful in their work. We spare no effort in improving the tools we are using when the current tools present inconveniences. Let’s take chopsticks as an example. In Japan, one edge is thinner than the other, but Chinese chopsticks are not this way. Chopsticks originally came from China, but the Japanese made improvements to them because they found them inconvenient. This is a strength of the Japanese monozukuri. When we realize that something needs improvement, we are willing to put forth the effort to improve the process or the product. This is our competitive edge.
Technologies are important, but something more important than that is the ability to meet customer requests. We have three Top Management Policies: making the most of people’s ability, sustainable creation of technical products and a flexible management system. Our employees act according to these policies. We believe that our ability to meet the demands of our customers, which we consider our core competence, is also the result of embodying one of our policies, the sustainable creation of technological products. In 2004-2005, about 80% of Daimei's sales was from Panasonic. Today, 30-40% of our sales comes from the automotive sector, 30-40% from the amusement sector, and the rest comes from Panasonic and the others. We were the first vendors which means the most reliable supplier for Panasonic's flagship product, the TV. There were only three companies manufacturing TVs, so we had a large share in the field.
Upton, interviewed at January’s CES 2024 consumer technology show in Las Vegas, said: “We’re used to the idea of plastic being used as an insulator. As Raspberry Pi boards got more powerful over the years, they’ve become more thermally generating. To keep the heat under control, they’ve had to become more thermally conductive.”
“Rather than making the heat under the plastic go up,” he said, “it makes the temperatures go down” — all without interfering with the device’s Wi-Fi performance. “That’s an incredible thing to do with plastic.”
We are also trying to find new business from our existing production process. We would like to find something that can be spun out of the process. An example is the repair of our molds. Although we used to just produce new molds, we have started a repair business with our skills.
From computer circuit boards to vehicle headlamps and bicycle-seat vision systems, thermally conductive polycarbonate is a game changer.
A big part of our sales comes from the automotive and amusement sectors, and we became the first vendor in both fields. We have about a 70-year relationship with Panasonic, but less than 20 years in the automotive and amusement field. In these latter two fields, we are new players. Most companies have existing suppliers already. Despite that, we became the first vendor. This was a result of responding to customer requests. The automotive sector has very high standards for quality and we tried to meet their requests. In addition, we responded to new methods of production and technologies demanded by the customers. Furthermore, we are pursuing material development. All these contributed to making us the first vendor. Our employees like new challenges. When they receive requests, they are very willing to address and work on them which gains the trust of customers.
Robert Grace is a writer, editor, and marketing communications professional who has been active in B2B journalism since 1980. After editing trade publications in London for seven years, he returned to the US in 1989 to help start the weekly Plastics News. Bob was PN’s editor-in-chief for 25 years and also served as its associate publisher and conference director. In May 2014 he founded RC Grace LLC and has developed an active freelance business.
This technology was used to improve the appearance of thick plates that have surface sink marks or dents. Resins can have different thicknesses. One part can be thinner while the other part is thicker. They get compressed when the temperature drops. The thicker parts are more compressed than the thinner part. Sink marks and dents appear during compression. This technology uses air to correct the sink mark on the surface. It is a technology that has been around for a long time but we have pioneered this kind of application.
It is common to have a proposal-oriented approach with the clients and use technologies for advancement in the B2B market in components, household products, or cars. However, we are also curious about your B2C client, For example, your Healthy Foot Washer. What motivated you to apply your technologies and expertise in the B2C fields? Can you give us an introduction to some of your key B2C products?
CVM enables easy molding of various challenging materials, from carbon-fiber-filled and glass-filled polymers to PEEK and ultrahigh-molecular-weight polyethylene (UHMWPE). Slowik also is using the Makrolon TC grades to replace cast-aluminum heat sinks with thermally conductive PC.
Dubbed CoPilot, it is an AI-powered bicycle light and camera that attaches under a bike seat to detect and distinguish nearby vehicles. CoPilot’s vision technology integrates with a smartphone app that can be mounted on the bike’s handlebars.
As a molded plastic part manufacturer, what do you think are your company's core competencies that make you the optimal choice compared to your competitors in Japan and overseas?
Velo’s AI-powered CoPilot light and camera attaches under the seat of a bicycle to enhance cyclists’ safety. It also can capture and store images such as the license plate numbers of vehicles in its view. Image courtesy of Velo AI Inc.
GETTING A QUOTE WITH LK-MOULD IS FREE AND SIMPLE.
FIND MORE OF OUR SERVICES:
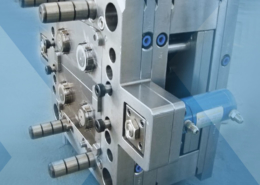
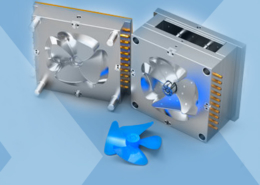
Plastic Molding

Rapid Prototyping
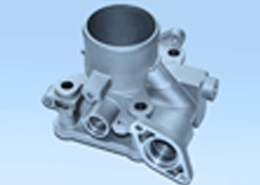
Pressure Die Casting
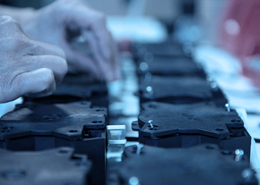
Parts Assembly
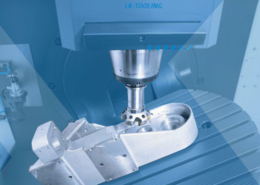