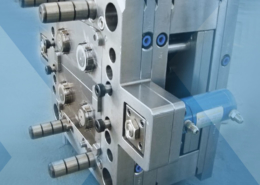
Exploring Plastic Overmolding: Innovation in Manufacturing
Author:gly Date: 2024-06-08
Introduction
Plastic overmolding, a technique revolutionizing manufacturing processes, involves molding one material over another to create a single integrated piece. This method not only enhances the aesthetic appeal of products but also improves functionality and durability. In recent years, its application has expanded across various industries, from automotive to consumer electronics, showcasing its versatility and efficacy. This article delves into the intricacies of plastic overmolding, exploring its diverse applications, advantages, challenges, and future prospects.
Applications
Consumer Electronics:
In the realm of consumer electronics, plastic overmolding has gained significant traction. Devices such as smartphones and wearables utilize this technique to achieve sleek designs, ergonomic grips, and enhanced durability. The seamless integration of different materials allows for the incorporation of features like buttons, grips, and seals, contributing to the overall user experience.
Automotive Industry:
Plastic overmolding has become indispensable in automotive manufacturing. Components such as handles, panels, and interior trim benefit from this process, offering improved aesthetics, noise reduction, and weather resistance. Moreover, the ability to combine dissimilar materials enables the production of lightweight yet robust parts, promoting fuel efficiency and sustainability.
Medical Devices:
In the medical field, precision and reliability are paramount, making plastic overmolding an ideal choice for producing intricate and sterile devices. From surgical instruments to drug delivery systems, this technique ensures biocompatibility, ergonomic designs, and seamless assembly, meeting the stringent regulatory standards of the healthcare industry.
Advantages
Enhanced Design Flexibility:
Plastic overmolding allows designers to explore new possibilities by combining materials with different properties. This flexibility enables the creation of complex geometries, ergonomic shapes, and multi-functional components, expanding the realm of product innovation.
Improved Product Performance:
By encapsulating functional elements within a protective layer, plastic overmolding enhances product performance and longevity. Components are shielded from environmental factors such as moisture, chemicals, and impact, leading to greater reliability and customer satisfaction.
Cost Efficiency:
Despite its advanced capabilities, plastic overmolding offers cost savings compared to traditional manufacturing methods. By consolidating multiple parts into a single assembly, it reduces material waste, labor costs, and assembly time, making it an economically viable solution for mass production.
Challenges
Material Compatibility:
Achieving optimal adhesion between different materials can be challenging, especially when they have disparate properties such as hardness and thermal expansion coefficients. Selecting compatible materials and fine-tuning process parameters are crucial to ensuring bond strength and durability.
Tooling Complexity:
The design and fabrication of molds for overmolding processes require meticulous attention to detail. Complex part geometries, precise material distribution, and multi-cavity configurations add to the intricacy and cost of tooling, necessitating thorough planning and expertise.
Quality Control:
Maintaining consistent quality throughout the overmolding process is imperative for product performance and reliability. Factors such as material purity, injection molding parameters, and post-processing techniques influence the final outcome, highlighting the importance of stringent quality control measures.
Future Outlook
As technology continues to advance, plastic overmolding is poised to play an even greater role in shaping the future of manufacturing. Innovations in materials science, additive manufacturing, and automation are driving improvements in process efficiency, product customization, and sustainability. Furthermore, the integration of digital design tools and simulation software enables predictive modeling and optimization, empowering manufacturers to stay ahead of the curve.
Conclusion
Plastic overmolding represents a paradigm shift in manufacturing, offering unparalleled design flexibility, performance enhancement, and cost efficiency. Its widespread adoption across diverse industries underscores its transformative potential and enduring relevance in an ever-evolving landscape. By addressing challenges and embracing technological advancements, stakeholders can harness the full benefits of plastic overmolding and drive innovation to new heights.
GETTING A QUOTE WITH LK-MOULD IS FREE AND SIMPLE.
FIND MORE OF OUR SERVICES:
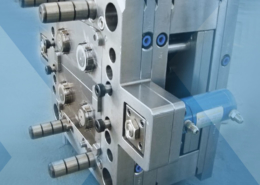
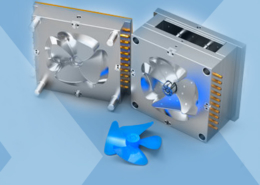
Plastic Molding

Rapid Prototyping
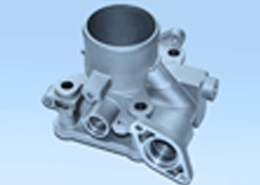
Pressure Die Casting
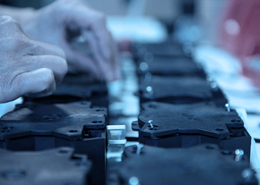
Parts Assembly
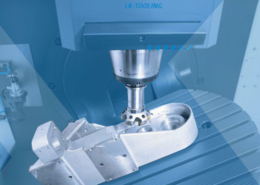