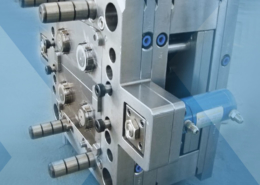
Haitian Gears Up for New Energy Vehicle Generation - haitian injection molding
Author:gly Date: 2024-09-30
DuPont Mobility & Materials will showcase these and other innovations at K 2022 in Düsseldorf, Germany, from Oct. 19 to 26. The company is exhibiting in booth C43 in Hall 6.
The two new Arburg machines include a 110 US ton ALLROUNDER 470 A 1000 - 290 Comfort, and a 220 US ton ALLROUNDER 570 A 2000 - 400 Comfort. Both are all-electric machines specified with LIM/LSR moulding options as well as thermoplastic moulding capabilities. They will both be equipped with MULTILIFT SELECT 8 servo electric robotics for parts removal and manipulation. Delivery is scheduled for summer 2024.
Zytel HTN has been identified as an elegant material solution in this area. For example, safety standards dictate that bus bars maintain a stable orange color indicating high voltage, even after repeated exposure to high heat. Zytel HTN accelerated aging tests show no noticeable color shifts, even at 130°C. It also contributes insulative properties for safer thermal runaway, and easily overmolds onto aluminum or copper, the most common bus bar metals.
Overmolded bus bars are found in virtually every xEV system. They transfer electrical energy from high-power battery packs to inverters, and inverters to e-motors, while insulating the conductor from ground or other phases. With the right materials, a bus bar can enhance a battery or e-motor energy density, durability, and electrical safety. However, it must be adequately insulated if the battery overheats, a condition known as thermal runaway, to help avoid module-to-module heat propagation.
He continued, “Our decision to move forward with Arburg was clearly based on our history of success using their machines. Their machines feature a sound mechanical design coupled with a very progressive control system.”
Additionally, Zytel HTN insulation materials for bus bars resist multiple thermal shock cycles (typically 1000 cycles) at temperatures (-40° to 150°C) normally needed for motors and power electronics applications. This means the material resists cracks after being overmolded onto metal conductors. Further, the material is chemically resistant to the fluids used for thermal management and has a high comparative tracking index (CTI) at elevated temperatures.
Leveraging a host of production equipment, lab testing, and engineering capabilities, DuPont has fine-tuned an overmolding process for bus bars that incorporates Zytel HTN material along with robust technical and processing support. Using sophisticated computer-aided analysis tools, DuPont collaborates with customers to reduce manufacturing time and cost yet maintain performance and safety standards.
“At that time there were only two significant players offering LIM options for their moulding machines – Arburg was one of them.”
“Although small, bus bar components are numerous, and also critical to the efficiency and durability of xEV batteries, motors, and power electronics,” said Giacomo Parisi, Marketing Director for Automotive Electrification at DuPont. “Our goal is to provide an excellent material for the application, along with assisting customers in their bus bar design and overmolding, to help them achieve their performance and production goals.”
Isolde Boettger, vice president and co-founder of Silcotech North America, said, “Michael’s technical experience, coupled with Arburg’s very solid and proven technology developments in LSR moulding technology, were superior when we made the decision to purchase our first two Arburg machines in 1998 when we started Silcotech North America. Looking back on our decision and evaluating the technology on a regular basis, it is clear Arburg was, and continues to be, the right decision for the competitive LSR space.”
Michael Maloney, Silcotech president, said that Arburg was chosen as the supplier of the new machines because of their long history of success providing machines for LSR applications.
The new machines will be used to expand capacity at Silcotech's headquarters in Bolton, Ontario. They will be added to the existing fleet to handle growing business volume, and the new machines are sizes where increased capacity is needed, said Dan Morris, Business Development Manager at Silcotech.
Silcotech North America, a specialist in Liquid Silicone Rubber (LSR) injection moulding, has announced its expanding capacity with the purchase of two new injection moulding machine workcells.
“Twenty-five years ago, we set out to become a global leader of liquid silicone moulded parts. Having spent 17 years in a technical capacity with a world-renowned moulding machine manufacturer, injection moulding machines were part of my DNA,” he said.
“Silcotech’s business has seen growth in the 15% to 20% per year range over the past two years and the outlook is to keep that pace that in FY2024 and beyond,” said Morris.
DuPont Mobility & Materials is breaking new ground for manufacturers of xEV components with a combined material-process-service solution for overmolding bus bars with Zytel HTN polyamide (PA) material. Bus bars are a workhorse component essential for distributing power in xEV batteries, motors, and power electronics.
GETTING A QUOTE WITH LK-MOULD IS FREE AND SIMPLE.
FIND MORE OF OUR SERVICES:
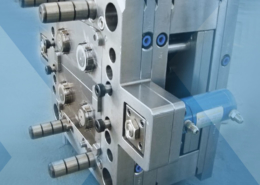
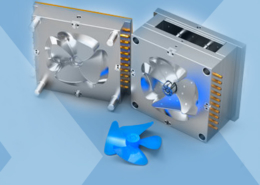
Plastic Molding

Rapid Prototyping
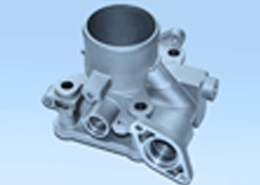
Pressure Die Casting
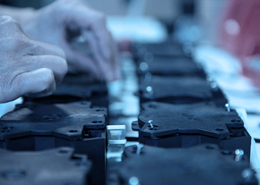
Parts Assembly
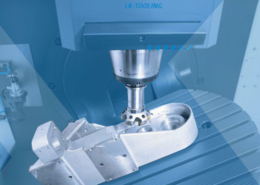