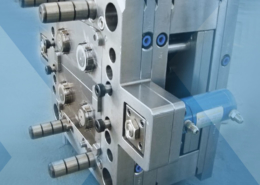
GW Plastics expands global medical molding footprint with acquisition of
Author:gly Date: 2024-09-30
Every fisherman has a secret. A secret spot, a secret technique, or a secret bait. Maybe that’s why tying flies is so popular. [Steve] certainly has is own special lures, although he’s not keeping it a secret. (Video, embedded below.) He designs lures in Simplify3D, 3D prints molds, and then casts them.
Engel is presenting a mold at the K show which can process different labels at the same time. This sees the partners respond to the globally different trends in in-mold labeling which are in line with the EPBP and/or Recyclass recommendations in the EU, and with the specifications from the Association of Plastic Recyclers (APR) for the USA.
The modified rPET being processed at the K show is sourced from PET beverage bottles recycled in the plants of packaging and recycling specialists ALPLA Group, which is headquartered in Hard, Austria. Other partner companies involved in the show exhibit are Brink (Harskamp, Netherlands) for the mold and IML automation and IPB Printing (Reusel, Netherlands) for the labels.
By using our website and services, you expressly agree to the placement of our performance, functionality and advertising cookies. Learn more
An Engel e-speed 280/50 injection molding machine is the heart of the production cell. Engel specifically developed this hybrid machine with its electrical clamping unit and hydraulic injection unit for the high-performance requirements of thin-wall injection molding.
To process rPET, Engel combines the new injection unit with a plasticizing unit from in-house development and production specifically designed for processing recycled material. During plasticizing and injection, the viscosity of the PET is configured for thin-wall injection molding. The new Engel e-speed supports the processing of arbitrary recycled materials up to 100% rPET.
Featuring a wall thickness of 0.32mm/0.013 inch, the transparent, round 125-mL containers are representative of a whole category of plastic packaging, especially in the food industry.
For the first time, thin-walled containers made of PET, specifically recycled PET (rPET), can be produced in a single injection-molding process step.
A different technology is used in Europe: an in-mold label that floats during the recycling process makes it easy to separate the dyes and the label from the PET.
To date, PET is the only packaging material which can be processed as a recycled material on an industrial scale to create food packaging. This innovation sees partner companies pave the way for removing the need to downcycle packaging products other than bottles, and opens an opportunity for recycling or upcycling. This would substantially extend the range of uses for PET and rPET. In addition to the bottle-to-bottle cycle, this also means that the establishment of bottle-to-cup or even a cup-to-bottle recycling is conceivable.
An Engel spokesperson tells PlasticsToday that, among others, “the [rPET] cups can be used for food products such as dairy products, gourmet salads, or sandwich spreads.”
We suppose these could be used with a drone fishing rig. In theory, you could use it for remote ice fishing, but we aren’t sure how you would jig it by remote control.
Engel and partners’ development yields thin-walled food containers made in a single injection-molding step using up to 100% recycled PET.
Under the European Plastics Pact, the intent is for all plastic packaging to contain 30% recycled material and to be 100% recycling capable by 2025. Typical materials used for packaging foods in thin-walled containers are polyolefins (polyethylene, polypropylene) or polystyrene.
I bought a PIM Shooter 150A off of Craigslist for quite a bit less than list price, and I have printed molds for polypropylene in ABS. It holds up ok. Not great – just ok. The PP melting point is close to ABS and every shot tends to degrade the mold more and more. I had tried to coat the mold in a thin layer of epoxy, and that certainly helped keep it together a bit longer. Ultimately, I think the best way to make molds with FDM is to print a positive and then cast a mold in resin in two halves.
In cooperation with partners Alpla Group, Brink Recycling, IPB Printing, injection molding machine manufacturer Engel is presenting a step forward for the packaging industry at K 2022 by processing recycled material, rPET, at its stand. Featured will be an Engel e-speed injection molding machine with a newly developed and extremely powerful injection unit.
Rick Lingle is Senior Technical Editor, Packaging Digest and PlasticsToday. He’s been a packaging media journalist since 1985 specializing in food, beverage and plastic markets. He has a chemistry degree from Clarke College and has worked in food industry R&D for Standard Brands/Nabisco and the R.T. French Co. Reach him at [email protected] or 630-481-1426.
The 3D printing part is interesting, but it is also kind of neat to see the lures and the natural prey he uses for inspiration. If you want to catch fish, you have to use bait that looks like real food.
Until now, it has only been possible to process PET in thick-walled parts such as bottle preforms in injection molding. In that standard process, the final packaging format was created in a second step of the process — by blow molding, for example.
Engel will present this technology and other developments at K 2022 in Düsseldorf, Germany, from Oct. 19 to 26, in booth C58 in Hall 15.
Also, recycling schemes for these materials lack the approval of the European food authority, European Food Safety Authority (EFSA). rPET offers a solution for avoiding penalties and special taxes. Although the price for PET is currently high, this concept makes the material a cost-effective alternative. EFSA has approved numerous recycling processes for PET, thus ensuring that rPET is available in Europe.
With the use of integrated in-mold labeling (IML), the containers are ready-for-filling as soon as they leave the production cell. The special feature in this application is the material. The thin-walled containers are produced directly from rPET in a single step.
[Steve] has other videos that cover more basic lures, but one covers a wavy split line cuttlefish analog and a four-tailed grub. The grub’s mold is in four parts and each part took six hours to print, so this isn’t a project for those of us with short attention spans.
The plastic in use is Dead On Plastix brand “plastisol”. The color is an add-in, so you can create different color bait. In the video, you can see purple and green in the video. The results looked like something you might buy but — of course — better. There was some tweaking needed for one of the molds, but even with the mold that needed tweaking, the results looked fine.
I think what you meant to say in the first paragraph is “designed in fusion 360, and sliced in simplify3d” As simplify 3d is a commercial/high end hobbyists slicing tool for fdm. Its not possible to do any 3d modeling/designwork in simplify3d.
The new model 280 e-speed high-performance injection unit for K 2022 (shown above) achieves injection speeds up 1,400 mm/55 inches per second at a maximum injection pressure of up to 2,600 bar when processing small shot weights with an extreme wall-thickness-to-flow-path ratio.
The dyes used on in-mold labels for the American market and its requirements can be washed off as the intent is to recycle the labels and the packaging.
GETTING A QUOTE WITH LK-MOULD IS FREE AND SIMPLE.
FIND MORE OF OUR SERVICES:
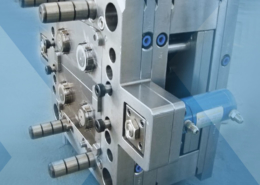
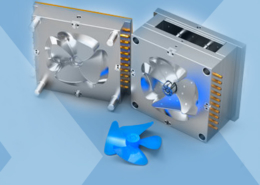
Plastic Molding

Rapid Prototyping
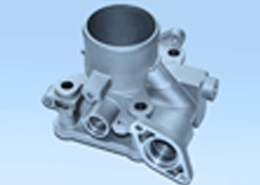
Pressure Die Casting
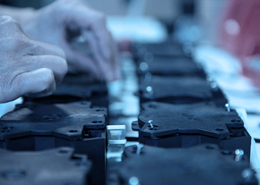
Parts Assembly
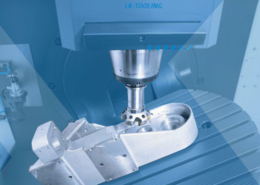