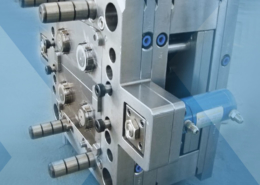
Grimsby: HSH Cold Stores seafood storage firm wins £5m boost - pallet injection
Author:gly Date: 2024-09-30
The RFID Mould Tag is installed as standard in all two-stage ejectors and enables access to relevant data such as 3D models, installation and maintenance instructions or technical limit values. The new Hasco app shows the counterfeit-proof originality of the products when the tag is scanned. The tag can be read directly with an NFC-enabled mobile phone.
The third ship of the new Stargate line follows the Earth battlecruiser Daedalus, which was released at the end of 2021. The Ha’tak-class Goa’uld mothership is still on pre-order in the United States, with shipping expected to start shortly.
The simple, strong crescent structure of the Death Glider contains a cockpit fit for two — a pilot and a gunner — although the ships are often flown by a single warrior. Each glider is equipped with an external loudspeaker to intimidate and control enemies of the empire, as well as more traditional weaponry in the shape of wing-mounted staff cannons.
In many cases, a 10 mm hole is already provided at the factory on tools or standard components. The NeoTAG Plug can be pressed in safely and reliably with the easy-to-use press-fit housing. In the end, it was the tag’s size of 8 millimeters that tipped the scales.
In addition to Industry 4.0, they also include the construction industry, medical laboratories, the dental technology sector, mechanical engineering and mould making. These sectors include applications such as maintenance, product identification and tracking, inventory, and tool protection.
The decision-makers were convinced by the fact that we also coated the tag in orange and added the Hasco logo. The tag can also be read with any NFC-enabled smartphone. This means that there is no need to purchase additional readers.
The logistical preparations for increasing market requirements have thus been implemented. With the integration of UWB and RFID technology, the company is taking a consistent step towards digitalization.
These tools are not part of the production system itself. They have to be specially developed, designed or individually adapted for each article to be produced. If a tool has faults or is not optimally adapted to the plastic component in the design, this will result in deficits in the quality of the moulded part.
The full-range supplier for mould making is the first player on the market to introduce the RFID Mould Tag for sophisticated products such as the two-stage ejector.
The fully integrated automated plate warehouse is one of the most modern in Europe. It has 5,000 pallet spaces. Hasco has also invested in a state-ofthe- art, fully automated small parts warehouse at the Lüdenscheid site. The new Autostore System has a storage capacity of 24,000 boxes. Twenty robots equip the picking workstations and enable around 720 retrievals per hour.
The company gained international significance with the patented invention of the modular standard mould system in the 1960s. Hasco has been expanding globally since the 1970s and is now represented at 35 locations worldwide. The main markets include Europe, Asia and North America. Growth regions include Mexico and India.
Alexander Ulman and Andre Brandt explain how RFID optimizes processes and why the solution represents a leap into the digital age for mould making.
“With its specialized injection moulding process, Neosid is the world market leader in the production of complex ferrites, the basis for high-performance RFID transponders.”
Simply explained, the two-stage ejector ensures that the plastic article is ejected in two stages. These components are used to demould plastic parts from the machine movement and enable complex movement sequences. Several separation stages can be realized with two-stage ejectors. To protect the product, the movements can be carried out slowly.
It is suitable for all branches of industry in which miniaturized transponders are required in a metallic environment. This covers numerous sectors.
The full-range supplier for mould making is the first player on the market to introduce the RFID Mould Tag for sophisticated products such as the two-stage ejector.
The decision-makers were convinced by the fact that we also coated the tag in orange and added the Hasco logo. The tag can also be read with any NFC-enabled smartphone. This means that there is no need to purchase additional readers.
Last fall GateWorld gave you the first look at the brand new Death Glider model from Eaglemoss’ Hero Collector line, and today the ship is available for pre-orders.
In principle, every mould design for injection moulding machines is identical. However, each injection mould is individually manufactured in two halves – a nozzle side and an ejector side. These mould halves contain complex components that include the cavity inserts, the sprue systems, the cores, the ejector elements and the cooling system.
As the primary attack fighters of the powerful Goa’uld empire, Death Gliders have patrolled the Milky Way galaxy for thousands of years. Capable of both atmospheric and deep space flight, the sight and unique, terrifying sound of swarms of these ships has signalled planetary invasion and spread fear across the stars.
Starting with the design of the plastic article, through the construction of the tool and the actual production, to sampling and modification grinding. Each of these process steps requires coordination. Communication with the customer and the constant updating of drawing data is crucial to the success of production. In the future, Hasco also plans to launch the use of a USB stick and its direct connection to the customer portal.
Numerous plastics processing industries such as the chemical, automotive and packaging industries as well as the consumer goods industry rely on large quantities of high-quality plastic components. These components are almost always manufactured using an injection moulding process. A complex forming process is used for this. Hasco has been manufacturing standard components, which can be described as the central assembly in injection moulding, for almost 100 years.
The fully integrated automated plate warehouse is one of the most modern in Europe. It has 5,000 pallet spaces. Hasco has also invested in a state-ofthe- art, fully automated small parts warehouse at the Lüdenscheid site. The new Autostore System has a storage capacity of 24,000 boxes. Twenty robots equip the picking workstations and enable around 720 retrievals per hour.
Hasco, the standard components specialist, has been headquartered in Lüdenscheid, North Rhine-Westphalia, Germany, since 1924.
Unlock the universe! This screen-accurate collection of highly-detailed, hand-painted models will capture the most famous starships and vehicles from the beloved science fiction franchise, Stargate. Spanning three TV series, Stargate tells the story of human explorers embarking on near-instantaneous travel across the cosmos to study new worlds, alien cultures, and advanced civilisations.
It is suitable for all branches of industry in which miniaturized transponders are required in a metallic environment. This covers numerous sectors.
Hasco, the standard components specialist, has been headquartered in Lüdenscheid, North Rhine-Westphalia, Germany, since 1924.
Hasco has been tagging two-stage ejectors with RFID since 2023. The tag, which is just a few millimetres in size and has an orange design, optimizes processes and services for mould manufacturers worldwide. From the perspective of the medium-sized company with around 700 employees, the RFID tag represents an innovative novelty in the mould making market.
Tools used in industrial applications in the smart factory can be turned into smart tools in just a few simple steps. They can then be located and seamlessly identified. Conclusion: These tools become transparent and digital, and can be integrated into other digital processes.
Around 180 technical sales representatives are direct contacts for customers worldwide. Production and logistics take place at the two production sites in Lüdenscheid, Germany and Guntramsdorf, Austria. Over 30,000 customers value the expertise of the standard components manufacturer.
The new model comes with a 7.8-inch (20-centimetre) wingspan, 4.2 inches long and 2.5 inches tall. Like the two previous models in the Stargate line it is made of die-cast metal and ABS plastic.
Around 180 technical sales representatives are direct contacts for customers worldwide. Production and logistics take place at the two production sites in Lüdenscheid, Germany and Guntramsdorf, Austria. Over 30,000 customers value the expertise of the standard components manufacturer.
Since 2020, the company has been focusing intensively on the digital connection of all tools and is launching an innovation on the market with the two-stage ejector: a small orange RFID tag measuring just 8 millimetres turns the tool into a digital and smart component.
We’ll do unboxing and reviews over on GateWorld’s YouTube channel when our models arrive, so subscribe now and join the community!
The company gained international significance with the patented invention of the modular standard mould system in the 1960s. Hasco has been expanding globally since the 1970s and is now represented at 35 locations worldwide. The main markets include Europe, Asia and North America. Growth regions include Mexico and India.
These tools are not part of the production system itself. They have to be specially developed, designed or individually adapted for each article to be produced. If a tool has faults or is not optimally adapted to the plastic component in the design, this will result in deficits in the quality of the moulded part.
Simply explained, the two-stage ejector ensures that the plastic article is ejected in two stages. These components are used to demould plastic parts from the machine movement and enable complex movement sequences. Several separation stages can be realized with two-stage ejectors. To protect the product, the movements can be carried out slowly.
“The project arose from discussions with customers. We were repeatedly asked whether it would be possible to link 3D data, installation instructions or maintenance instructions directly to the product in order to reduce the need to search for documentation. We are now receiving recognition and positive feedback from customers. The “aha effect” has been achieved.”
“Alexander and I have been developing components for mould and tool making for many years. Our goal is to always be one step ahead and offer innovative solutions for injection moulds. Hasco’s portfolio now includes more than 100,000 different components. All of them are designed for plastics processing industries, tool-making and injection moulding shops.”
Tools used in industrial applications in the smart factory can be turned into smart tools in just a few simple steps. They can then be located and seamlessly identified. Conclusion: These tools become transparent and digital, and can be integrated into other digital processes.
GateWorld receives a commission on purchases made through our affiliate links. Thank you for supporting independent fan journalism!
Hasco is a supplier for tool and mould making, the plastics processing industry and injection moulders. The portfolio includes all the components that a manufacturer of plastic components needs to produce an injection mould. This includes a total of over 100,000 products.
In many cases, a 10 mm hole is already provided at the factory on tools or standard components. The NeoTAG Plug can be pressed in safely and reliably with the easy-to-use press-fit housing. In the end, it was the tag’s size of 8 millimeters that tipped the scales.
Making its debut in the 1994 Stargate feature film, the alien fighter craft was retooled a bit for the Stargate SG-1 television series. It was featured throughout the show’s run, as a cornerstone of the Goa’uld empire’s arsenal of intimidation and domination.
Hasco offers a total of seven different two-stage ejectors in various dimensions. Since 2023, every two-stage ejector has been fitted with an RFID tag at the factory.
Hasco is laying the foundations for its planned digitalization strategy with the RFID tag on the two-stage ejector. Further products are to follow. The functionality and range of communication options are to be expanded. The aim is to optimize direct communication with the customer and thus also improve the value chain. Numerous process steps are part of the manufacturing process.
The logistical preparations for increasing market requirements have thus been implemented. With the integration of UWB and RFID technology, the company is taking a consistent step towards digitalization.
In addition to Industry 4.0, they also include the construction industry, medical laboratories, the dental technology sector, mechanical engineering and mould making. These sectors include applications such as maintenance, product identification and tracking, inventory, and tool protection.
Numerous plastics processing industries such as the chemical, automotive and packaging industries as well as the consumer goods industry rely on large quantities of high-quality plastic components. These components are almost always manufactured using an injection moulding process. A complex forming process is used for this. Hasco has been manufacturing standard components, which can be described as the central assembly in injection moulding, for almost 100 years.
The tag is pressed into an indentation and is clearly visible on the steel surface. Even when installed, the customer can read the tag with a mobile phone or RFID reader. This makes handling easy.
Since 2020, the company has been focusing intensively on the digital connection of all tools and is launching an innovation on the market with the two-stage ejector: a small orange RFID tag measuring just 8 millimetres turns the tool into a digital and smart component.
Hasco offers a total of seven different two-stage ejectors in various dimensions. Since 2023, every two-stage ejector has been fitted with an RFID tag at the factory.
Two-stage ejectors are products with high mechanical requirements. This also applies to maintenance. Due to the way they work, they are more cost-intensive than other standard components and, above all, require more consultation. Hasco has been equipping these components with an orange-colored RFID tag as standard and at the factory since 2023.
Hasco is a supplier for tool and mould making, the plastics processing industry and injection moulders. The portfolio includes all the components that a manufacturer of plastic components needs to produce an injection mould. This includes a total of over 100,000 products.
GETTING A QUOTE WITH LK-MOULD IS FREE AND SIMPLE.
FIND MORE OF OUR SERVICES:
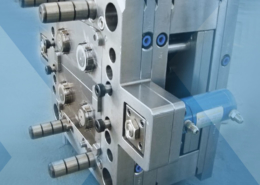
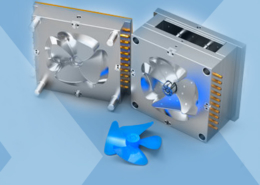
Plastic Molding

Rapid Prototyping
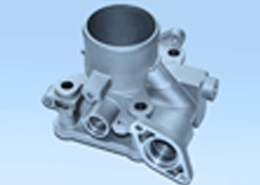
Pressure Die Casting
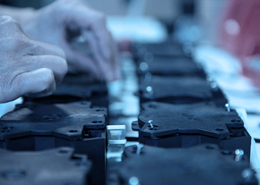
Parts Assembly
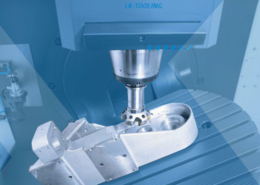