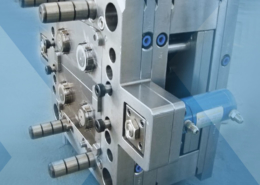
GOJIRA's JOE DUPLANTIER To Take Part In A Peaceful Protest Against PAUL
Author:gly Date: 2024-09-30
Wittmann’s new beside-the-press blade granulator is suited for grinding large injection molded parts up to 500 x 200 mm (19.7 x 7.9 in.) in size.
New T-Flow HRS control units from Oerlikon HRSflow increase the precision and reliability of temperature control in hot-runner injection molding. Modular in design, three models are configurable to multiples of six zones.
The duo 5500 combi M represents the latest technology in injection molding, said Engel in the announcement. It features two movable (combined and individually operable) horizontal injection units and a combi M injection unit. It is also equipped with two six-axis Engel easix articulated robots for flexible and efficient automation.
Initially developed to mold large parts for the automotive sector, the press is now available for customer trials at the St. Valentin, Austria, technical center.
Designed to fit into small, crowded cavity and core inserts, the pins are manufactured with hardened M-2 steel and are available in diameters from 0.060 to 0.320 in. and in 2.5- and 5.5- in. lengths. Cut-to-length and custom options are also available.
The starter kit comes with a small controller, an air regulator, silicone tubing, stainless-steel tubing, and polyurethane tubing. Users can build onto the starter kit with additional accessories that make it possible to perform full hot-runner manifold leak detection.
Until now, large plastic parts have often been manufactured using various processes other than injection molding, which have significant limitations. With the availability of an injection molding machine as large as the duo 5500 combi M in a technical center, extensive possibilities for part and technology development and sampling are now available. This offering reinforces Engel's role as an enabler of new technologies, allowing customers and partners to actively pursue developments in new dimensions and expand injection molding capabilities.
Because of its compact footprint, performance, and maximum material throughput of 100 kg per hour, the G-Max XL can be used as a beside-the-press granulator for inline recycling of sprues and reject parts during machine startup. It can also be used as a central granulator.
The integrated pull-push mechanism moves dies on and off the press bed via the roller rails. A safety device ensures that loads can only be moved when the RWS die changing table is firmly attached to the press or storage space.
The system sends tiny volumes of low-pressure air through robust stainless-steel sensor tubes to quickly detect most leaks thanks to a self-teaching algorithm, said PCS.
The combination of integrated touchscreen, clear text display, smart navigation, and guided operation results in a particularly user-friendly concept without the need for instruction or prior knowledge, according to Oerlikon HRSflow. Recipes and test reports can be installed and transferred quickly and efficiently via the integrated USB port. Data is exchanged with the injection molding machine via the OPC UA interface in accordance with the new Euromap 82.2 standard protocol for hot-runner controllers. The integrated VNC server also enables convenient operation via notebook, tablet, or smartphone.
With the introduction of the duo 5500 combi M, Engel said it has reinforced its role as a leading hub for testing new technologies and collaborating closely with the industry to promote new injection molding possibilities. The machine allows for the testing and development of existing and new customer projects under real conditions and on neutral ground. This includes tool and material tests as well as the development of new manufacturing technologies.
A standardized base plate accepts dies of various sizes, and the integrated control system enables semi- and fully automatic die changes and precise positioning to within ±0.3 mm.
Manufacturers of large, complex plastic parts and toolmakers can now test feasibility and implementation at an early project stage. This significantly shortens time to market and avoids costly subsequent errors by identifying and eliminating sources of error early on. Initial customer trials are scheduled to begin shortly.
The open design of the three-blade cutting rotor makes the G-Max XL ideal for grinding heat-sensitive materials that still retain heat from processing, according to Wittmann. Open spaces between the blades and rotor shaft ensure ventilation, and the knives can be easily changed. The rotating and fixed blades, which are angled in opposite directions, ensure a clean scissor cut.
All digital assistance systems from Engel are integrated into the machine control, enabling energy-efficient, sustainable production while optimizing processes.
Engel reports that it has expanded its technical center in St. Valentin, Austria, with one of the largest injection molding machines from its standard portfolio — the duo 5500 combi M. With a clamping force of 55,000 kN and measuring 32 meters long, 13 meters wide, 6.8 meters high, and weighing 545 tonnes, it is by far the largest technical center machine in the world, according to Engel.
Unlike stamping punches, which are sometimes used as core pins in molds, the heads of TI pins are precision ground to mold tolerances. Also, rather than beginning with a fractional-diameter core pin, step grinding can be eliminated with mold inserts fabricated to the molded part diameter via wire electrical discharge machining. The TI pins only need to be cut to the finished length.
Stephen has been with PlasticsToday and its preceding publications Modern Plastics and Injection Molding since 1992, throughout this time based in the Asia Pacific region, including stints in Japan, Australia, and his current location Singapore. His current beat focuses on automotive. Stephen is an avid folding bicycle rider, often taking his bike on overseas business trips, and a proud dachshund owner.
T-Flow HRS precisely controls the nozzle temperatures, allowing universal use, even in demanding high-performance applications with compact nozzles. Several heating options are available, and different recipes can be saved, stored, compared, and quickly called up.
For PU applications, two Cannon systems are available — one for small-volume applications and another for high-volume output. A corresponding dosing unit allows for coloring the polyurethane.
The RWS system, for example, can help car manufacturers integrate numerous individual parts into increasingly large castings, which are processed with heavier dies in larger presses and punches.
The die changing table travels on floor-level round rails, with a rolling resistance so low that up to five-ton loads can be moved manually by one person. In addition, the rails are designed to facilitate precise carriage guidance and to prevent dirt deposits and tripping hazards in the floor.
The new Engel technical center facility covers all application areas for the automotive sector and technical injection molding.
From nozzle leak-detection systems to precision-ground ejector pins, these recently introduced products promise to save injection molders time and money.
Editor in chief of PlasticsToday since 2015, Norbert Sparrow has more than 30 years of editorial experience in business-to-business media. He studied journalism at the Centre Universitaire d'Etudes du Journalisme in Strasbourg, France, where he earned a master's degree.
The new Airtect Plastic Leak Detection System from PCS Co. is designed to provide 24/7 protection of injection molding machine nozzles and manifold systems, reducing downtime and costly repairs.
The automotive industry increasingly uses larger plastic parts to reduce vehicle weight, improve fuel efficiency, and lower production costs. Plastics offer design flexibility, enhance corrosion resistance, and contribute to the longevity and safety of vehicles. They also allow for the integration of functional elements and reduce the number of individual parts needed. Engel’s new facility supports this trend by enabling the production of larger plastic components.
The company aims to use this machine to explore technologies and mold components in completely new dimensions in collaboration with its customers and partners. The extra-large mold space accommodates molds weighing up to 150 tonnes, with possible shot weights up to a massive 42 kg. The state-of-the-art machine was developed to meet the demands of the automotive industry and technical injection molding and is now available for customer trials.
“The Airtect Plastic Leak Detection System is an essential tool that can be installed directly onto the injection molding machine nozzle or hot runner manifold system," said PCS VP of sales Derrick Jones. “It quickly alerts users of leaks in the form of an alarm and/or the suspension of production, enabling faster operator response and repair. The system can be adapted to any hot runner system, either new or retrofit.”
A new rail-guided die changing table for transporting heavy dies and molds is available in three versions for loads up to 15, 25, or 40 tonnes per die. The electric RWS system from Roemheld is equipped with two different pull-push mechanisms for the safe, automatic transport of dies to set-up presses. It is compatible with most machines.
No tools are required to access the cutting chamber or the screen fixture, which also facilitates cleaning and maintenance operations. Even material and color changes can be carried out very quickly, further increasing productivity.
GETTING A QUOTE WITH LK-MOULD IS FREE AND SIMPLE.
FIND MORE OF OUR SERVICES:
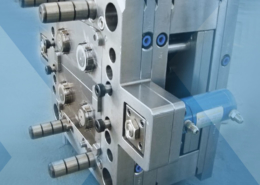
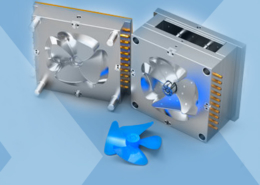
Plastic Molding

Rapid Prototyping
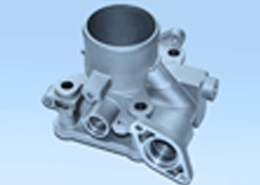
Pressure Die Casting
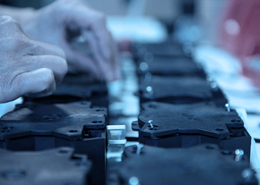
Parts Assembly
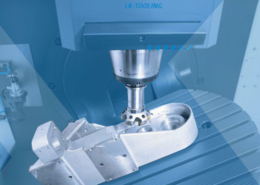