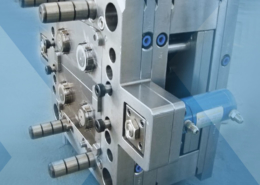
Global PE and PP indexes Week Two: Asian prices recover as Europe declines
Author:gly Date: 2024-09-30
“This process chain is suitable for products in intermediate scale (from 1000 – 10,000 cycles by injection molding or similar) production, but high variation in design,” the researchers state. “Moreover, for 3D printed inserts, no special mold plates are required. Standard commercial injection molding plates were purchased and machined to fit the inserts.”
Stay up-to-date on all the latest news from the 3D printing industry and receive information and offers from third party vendors.
(a) Inserts produced by additive manufacturing process form the mold cavity; one polyethylene (PE) replica produced by injection molding is displayed. Markings on the reference ruler are millimeters; numbers mark centimeters. (b) Scanning electron microscope (SEM) image shows the surface of the insert; (c) SEM image shows the surface of the PE parts made by injection molding.
“Materials for premium cars in the future need to combine both light weight and multi-functionality with world class aesthetics. New developments in advanced plastics have great potential to satisfy all of these requirements but the challenge is not to make a few prototypes but to make parts in hundreds of thousands at high quality and sustainable cost. This unique new centre will provide the UK with the capability it needs to exploit this potential. “
Stay up-to-date on all the latest news from the 3D printing industry and receive information and offers from third party vendors.
There’s lots to choose from in this week’s 3D Printing Webinar and Event Roundup! Stratasys continues its North American tour, as well as its in-person training classes, and HP will...
“The manufacture and processing of plastic and rubber materials is a multi-billion pound industry central to the future prosperity of the UK. There isn’t an industry which is not underpinned in some manner by plastics materials, from telecommunications, energy, transport and defence to healthcare. The centre will have capability in every polymer process with pilot scale equipment and larger, extensive testing and characterisation facilities.”
The new NPPC brings a fully integrated approach to plastics design, manufacturing and disposal, encompassing multifunctional design and low environmental impact.
We use cookies to give you the best online experience. Please let us know if you agree to functional, advertising and performance cookies. You can update your cookie preferences at any time.
“Our new Centre’s research will be built upon four principles for materials processing: innovating the manufacturing process, added functionality to material and component, full integration into structure, and sustainability and holistic environmental design, including end of life.”
“This method will create the possibility for creating micro features on real free-form surface on a new production platform meeting industrial demands,” the researchers state. “Therefore, this method has the potential to be applied and investigated for applications in connection with next generation medical devices that require micro features on complex shapes, for example in connection with medical devices or implanting devices. This method will facilitate value creation through significantly reduced expenses for small-to-medium volume series productions, and positively affect the timescale for production in the gap between 1 – 10 individual devices and real mass production. It will open up new high-value products and design solutions.”
Lisa Barwick, Head of Marketing and Communications, WMG, University of Warwick Tel: 024 76 524721 or 07824 540845 L.Barwick@warwick.ac.uk
SPEE3D participated in a U.S. Army Combat Capabilities Development Command (DEVCOM) Army Research Laboratory (ARL) demonstration. The demo took place at the University of Tennessee Knoxville and ran from the...
There are many ways of manufacturing micro pillars or features, the researchers explain, but most of them can only be applied on flat surfaces or on surfaces with constant curvature. In the paper, they describe how they created micro features on complex surfaces using what they call “a soft tooling process chain.” Steel mold cavities in the injection molding machine were replaced by a set of inserts produced using DLP 3D printing. This technology was able to achieve higher precision than metal additive manufacturing, and the machining time and cost was significantly reduced compared to conventional tooling processes based on CNC machining.
Peter Dunn, Director of Press and Policy, University of Warwick Tel UK: 024 76523708 office 07767 655860 mobile Tel Overseas: +44 (0)24 76523708 office +44 (0)7767 655860 mobile/cell Email: p.j.dunn@warwick.ac.uk
From the early days of their research, WMG recognised that plastics offer significant design flexibility advantages for industrial application – examples include:
3D printing is a great technology on its own, but it also lends itself well to complementing other manufacturing technologies, such as injection molding. In a paper entitled “A Soft Tooling Process Chain for Injection Molding of a 3D Component with Micro Pillars,” a group of researchers discusses using 3D printing to create injection molding inserts with micro surface features.
Experts DirectoryTelephone ListingsCommunications OfficePress and Media RelationsImage LibraryUniversity ProfileSocial Media
Authors of the paper include Yang Zhang, David Bue Pedersen, Michael Mischkot, Matteo Calaon, Federico Baruffi, and Guido Tosello.
“The research focus of the Centre will be in innovation in the manufacturing processes and processing of advanced functional plastic and elastomer materials. We will work collaboratively with industry to deliver significant added value, engage in technology transfer and provide training and further education to the sector.”
WMG at the University of Warwick has established a new National Plastics Processing Centre (NPPC) which will provide a national hub for innovation and research in plastics processing.
The surface quality of the injection molded parts produced with the 3D printed plates was limited, the researchers conclude, but post-processing methods such as chemical etching could be used to improve the surface quality. The precision of the surface features was also limited, they add; however, they did find additive manufacturing to be a time- and cost-effective way of producing injection molding inserts for parts with complex surfaces and micro features.
WMG has an established track record of innovation and technology transfer in plastics processing. It has developed extensive capabilities and facilities across a wide range of processes and working with both large global companies and SMEs across a variety of sectors to develop and embed plastics processing. The capability offered from WMG is that most widely used within the plastics industry's processes including extrusion/compounding, injection moulding, thermoforming, blow moulding and rotational moulding.
Additive manufacturing and injection molding have been combined before; more frequently, additive manufacturing is being used to manufacture the molds for injection molding. The advantages are many: it is cheaper, faster, and allows for easy production of molds for single or limited use. This paper shows another way that 3D printing can be used to enhance injection molding processes, offering a look at how manufacturing technologies are often better together than by themselves.
The inserts were 3D printed and installed on an injection molding machine. With the inserts installed, the researchers then injection molded parts from PE material.
In a major leadership shift, VulcanForms has appointed Kevin Kassekert as its new CEO and Jay Martin as President. This change comes at a crucial time as the company moves...
Amidst the backdrop of last week’s FAA/EASA workshop in Wichita, Bill Bihlman, Consultant and Volunteer to SAE, analyzes the state of AM aerospace standards. Commercial aviation is notoriously risk averse....
WMG has an extensive range of plastic design, manufacture and research technologies across its facilities which will now work together in the new Centre.. It will have its own bespoke building by 2017 with facilities for training, research and development, and will also house a fully equipped elastomer technology laboratory
Register to view and download proprietary industry data from AM Research and 3DPrint.com Questions? Contact info@3dprint.com
GETTING A QUOTE WITH LK-MOULD IS FREE AND SIMPLE.
FIND MORE OF OUR SERVICES:
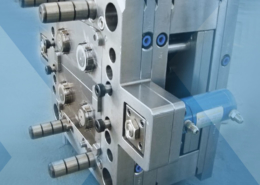
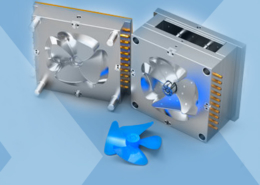
Plastic Molding

Rapid Prototyping
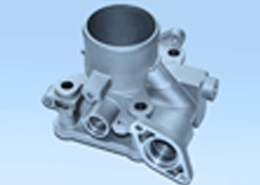
Pressure Die Casting
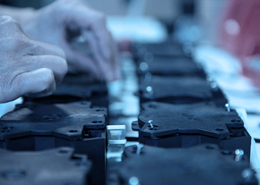
Parts Assembly
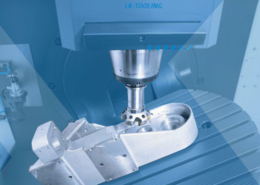