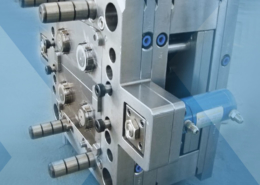
Global Markets for Metal Injection Molding: Data and insight from World
Author:gly Date: 2024-09-30
The undertray consists of Tepex dynalite continuous-fiber-reinforced thermoplastic composite from Lanxess combined with a DLFT (direct long fiber thermoplastic) composite. “Thanks to the toughness and tensile strength that Tepex delivers, this composite design is significantly more resistant to impacts and damage than previous material solutions,” explains Tepex application developer Harri Dittmar. The new component also results in significant weight savings. The engine tray in the Tepex-DLFT composite design is over 60 percent lighter than an equivalent component made of steel, and up to 20 percent lighter when the new material is substituted for aluminum.
Tepex dynalite is developed and produced by the Lanxess subsidiary Bond-Laminates GmbH based in Brilon, Germany. In addition to underbody protection, it is also shaped and back-injected to make seat backs, module supports, battery consoles, front-end components, brake pedals and bumper crossbars. Due to the growing potential uses for Tepex in lightweight automotive engineering, Lanxess has set up a dedicated project group that supports partners worldwide through all stages of Tepex component development, right up to production launch.
Engel supplied the 1,700-tonne press with a mold and integrated HP-RTM equipment. With a mold mounting surface of 2.2 by 1.8 meters, the machine offers WMG the opportunity to produce a multitude of components and use different materials and manufacturing processes.
The Engel v-duo is characterised by a very high degree of rigidity and excellent platen parallelism. Platen-parallelism control for injection compression moulding is included in the standard version of the machine. In addition, handling devices that move straight into the mould area can be integrated to save space. Using the sliding tables, insertion tasks and set-ups can be carried out flexibly and easily. The hydraulic accumulator has been done away with completely, and with the ecodrive servo-hydraulic system fitted on the standard version of the machine, the Engel v-duo is setting new standards in energy efficiency too.
The Engel v-duo machine was designed specifically for fiber composite applications. Compared to conventional presses, the it is 50 per cent shorter in height and about 60 per cent lighter. The large vertical machine, which is available with clamping forces from 4,000 to 36,000 kN, therefore makes it possible to create compact production cells at low investment costs.
Great Britain's first Engel v-duo press has been delivered to WMG's Automotive Composite Research Centre at the University of Warwick. "As a development partner with the automotive industry, flexibility is very important to us. The Engel v-duo enables us to research thermoset composites prepreg compression molding (PCM), sheet molding compound (SMC) compression molding, HP-RTM and stamp forming of thermoplastic composites," says Professor Ken Kendall, Professorial Fellow at WMG's Automotive Composite Research Centre. "The precise control provided by this equipment is an essential feature for us when researching these processes".
Engel's decades of experience in the automotive industry was another crucial factor in WMG's decision to invest in an Engel v-duo machine. It was also important to Professor Kendall to purchase an integrated solution where everything came from a single source. When Engel is used as a system supplier, the customer only communicates with one Engel contact, which can speed up the project planning and start-up of the plant significantly. A further advantage is that the HP-RTM unit, which Engel implemented in cooperation with its system partner Hennecke (in St. Augustin, Germany), has been integrated into the machine's control unit, meaning the entire manufacturing process can be managed via the machine's display.
Stephen has been with PlasticsToday and its preceding publications Modern Plastics and Injection Molding since 1992, throughout this time based in the Asia Pacific region, including stints in Japan, Australia, and his current location Singapore. His current beat focuses on automotive. Stephen is an avid folding bicycle rider, often taking his bike on overseas business trips, and is a proud dachshund owner.
WMG is a research and education group based at the University of Warwick and works collaboratively with global companies to develop innovative products, services and processes. Along with its UK base, the group operates education centers and partnerships in seven countries. The Centre's aim is to help the automotive sector tap into innovative technologies, using the industrial-scale machine to develop mass-production processes for the manufacture of fiber reinforced composite components
In regions where road surfaces are poor, vehicle underbodies are subjected to tough conditions, having to withstand the impact of stones thrown up from the surface and, in extreme cases, even direct contact with the ground. A major German car manufacturer is therefore equipping the first vehicles of various model series that are delivered to countries with poor road infrastructure with an engine undertray made of a particularly robust thermoplastic composite construction.
At its Center for Lightweight Composite Technologies in St. Valentin, Austria, the injection moulding machine manufacturer focuses on promoting the interdisciplinary development of fiber composite technologies with partner companies and universities. The aim is to speed up the launch of composite technologies in the automotive industry. The technology center is currently focusing on the processing of semi-finished thermoplastic products (thermoplastic fabrics and tapes) and on reactive technologies that use thermoset and thermoplastic material systems, such as HP-RTM and in situ caprolactam polymerization.
Continuous-fiber-reinforced thermoplastic composite used in combination with direct long fiber thermoplastic compound can reduce the weight of a protective undertray by 60 percent versus steel.
Lanxess is confident that Tepex will become an increasingly popular solution for underbody protection of vehicles. Many car manufacturers currently use steel or aluminum for components of this kind, which presents certain disadvantages, including with regarding to weight. In electric vehicles, comparatively heavy aluminum panels have been a particularly popular solution for protecting the underside of battery systems. “Using Tepex in combination with DLFT produces considerably lighter, more robust components that also provide more effective sound insulation,” Dittmar sums up.
The engine undertray is manufactured by GSI Deutschland GmbH, based in Hörgertshausen, Germany. The component solution with Tepex and DLFT was developed by the Polytec Group (Hörsching, Austria) in collaboration with Lanxess. The underbody protection was previously made of a polypropylene (PP) -based composite design consisting of a glass-mat-reinforced thermoplastic system (GMT) and an additional fabric-reinforced GMT; before that, sheet steel was used.
At Composites Europe 2015, which takes place from September 22nd to 24th in Stuttgart, Engel will be presenting the full potential of the Engel v-duo series and also guarantees visitors a look at many other current lightweight-design projects at its booth (stand D20, hall 7).
Great Britain's first Engel v-duo press has been delivered to WMG's Automotive Composite Research Centre at the University of Warwick. "As a development partner with the automotive industry, flexibility is very important to us. The Engel v-duo enables us to research thermoset composites prepreg compression molding (PCM), sheet molding compound (SMC) compression molding, HP‑RTM and stamp forming of thermoplastic composites," says Professor Ken Kendall, Professorial Fellow at WMG's Automotive Composite Research Centre.
The Engel v-duo machine was designed specifically for fibre composite applications. Compared to conventional presses, the Engel v-duo is 50 per cent shorter in terms of height.
The new underbody protection is manufactured in molds as used, for example, for GMT and its related materials. The difference is that a Tepex dynalite 104-RG601 insert with a wall thickness of one millimeter is used. This consists of a glass fiber fabric, containing 47 percent continuous glass fiber rovings by volume, and a PP matrix. It is heated up while the required volume of DLFT compound (containing glass fibers 5 to 50 mm long) is extruded. Both materials are then shaped in a compression mold. Components are thus produced that have a Tepex surface on the engine side – the side subjected to tensile load. “Our material solution is more cost-effective than the previous composite variant because DLFT is a direct extrudate that can be produced at particularly low cost and makes up the larger part of the component’s volume,” says Henrik Plaggenborg, head of Technical Marketing Business Development Tepex Automotive.
Great Britain's first Engel v-duo press has been housed at WMG's Automotive Composite Research Centre at the University of Warwick. Engel supplied the 1,700-tonne press with a mould and integrated HP-RTM equipment.
GETTING A QUOTE WITH LK-MOULD IS FREE AND SIMPLE.
FIND MORE OF OUR SERVICES:
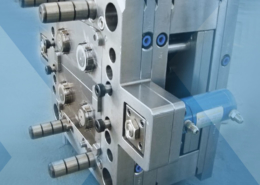
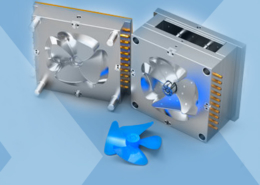
Plastic Molding

Rapid Prototyping
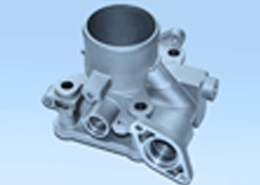
Pressure Die Casting
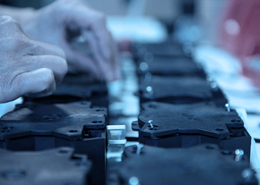
Parts Assembly
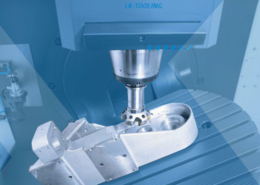