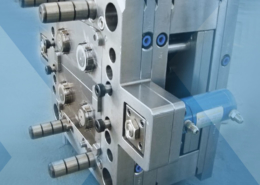
Getting started: Setting up an injection molding plant - plastics that can be in
Author:gly Date: 2024-09-30
“We have made significant investments in new equipment, and this will allow us to produce our products more effectively and efficiently,” said Bryan Coppes, vice president of engineering and R&D at Infiltrator. “It is the new capabilities and opportunities for continued product development that are truly exciting. This new equipment will allow us to continue to bring new and innovative products to market and meet and exceed our customers' needs.”
“Silcotech’s business has seen growth in the 15% to 20% per year range over the past two years and the outlook is to keep that pace that in FY2024 and beyond,” said Morris.
“Twenty-five years ago, we set out to become a global leader of liquid silicone moulded parts. Having spent 17 years in a technical capacity with a world-renowned moulding machine manufacturer, injection moulding machines were part of my DNA,” he said.
Getting the 8,000-ton machines from Austria to the Infiltrator Water Technologies plant in Kentucky was a logistical challenge.
Engel said it received the purchase order in November 2020 and completed handover of the first machine in February 2022. The second machine, a replica of the first, was delivered this month.
Engel added in the news release that it shares a commitment to sustainability with ADS, which claims to recycle more plastic than any other company in North America.
The duo injection molding machines each have two 85,000 cm³ injection units, which allow for injecting a total shot weight of 270 lb (122 kg). Despite the clamping force and shot size, the machines have a relatively small footprint — 96 ft. (29.3 meters) long and 37 ft. (6.4 meters) wide — enabled by Engel’s two-platen design.
Silcotech North America, a specialist in Liquid Silicone Rubber (LSR) injection moulding, has announced its expanding capacity with the purchase of two new injection moulding machine workcells.
At the IWT site in Winchester, new manufacturing facilities had to be built to house the large machines. As 29 truckloads of machine parts were arriving from Austria, the 59,000-square-foot building expansion went forward. A 150-ton overhead crane was installed to move molds in and out of the machine and was also used to help assemble the new press.
“At that time there were only two significant players offering LIM options for their moulding machines – Arburg was one of them.”
Engel was recently awarded a gold sustainability rating by EcoVadis, which relies on data from more than 90,000 evaluated companies and global supply chains to rank companies.
The two new Arburg machines include a 110 US ton ALLROUNDER 470 A 1000 - 290 Comfort, and a 220 US ton ALLROUNDER 570 A 2000 - 400 Comfort. Both are all-electric machines specified with LIM/LSR moulding options as well as thermoplastic moulding capabilities. They will both be equipped with MULTILIFT SELECT 8 servo electric robotics for parts removal and manipulation. Delivery is scheduled for summer 2024.
Michael Maloney, Silcotech president, said that Arburg was chosen as the supplier of the new machines because of their long history of success providing machines for LSR applications.
The new machines will be used to expand capacity at Silcotech's headquarters in Bolton, Ontario. They will be added to the existing fleet to handle growing business volume, and the new machines are sizes where increased capacity is needed, said Dan Morris, Business Development Manager at Silcotech.
He continued, “Our decision to move forward with Arburg was clearly based on our history of success using their machines. Their machines feature a sound mechanical design coupled with a very progressive control system.”
Isolde Boettger, vice president and co-founder of Silcotech North America, said, “Michael’s technical experience, coupled with Arburg’s very solid and proven technology developments in LSR moulding technology, were superior when we made the decision to purchase our first two Arburg machines in 1998 when we started Silcotech North America. Looking back on our decision and evaluating the technology on a regular basis, it is clear Arburg was, and continues to be, the right decision for the competitive LSR space.”
Special shipping and ground transportation arrangements were needed to move the machine from Austria to the United States and even within Austria. The platens were transported to and from the St. Valentin manufacturing facility along the Danube River on barges. “Each machine was fully assembled and tested prior to shipping and then disassembled to be shipped to the United States,” said Jim Moran, business development manager at Engel North America.
Engel said it is increasingly receiving requests for custom solutions in the extremely high clamping force range. Clamping forces of 10,000 tons and more are possible. Machines of this size can process individual shot weights of several hundred kilograms or pounds and achieve two-ton-per-hour material throughput.
Two injection molding machines with a clamping force of 8,000 tons each have now been delivered by Austrian injection molding machine maker Engel to the Infiltrator Water Technologies (IWT) plant in Winchester, KY. IWT took delivery of the first Engel duo 130000/130000H/8200 combi US machine, the largest machine ever built at Engel’s St. Valentin facility in Austria, in February of last year. A second machine, a replica of the first, arrived at the facility this month. IWT, a subsidiary of Advanced Drainage Systems (ADS), produces water management products.
GETTING A QUOTE WITH LK-MOULD IS FREE AND SIMPLE.
FIND MORE OF OUR SERVICES:
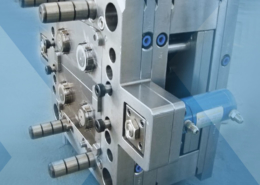
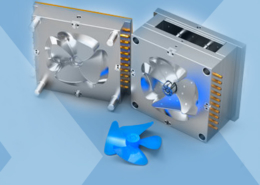
Plastic Molding

Rapid Prototyping
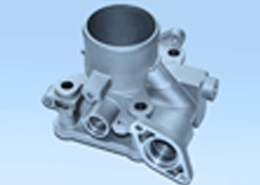
Pressure Die Casting
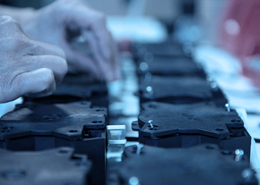
Parts Assembly
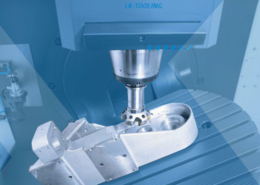