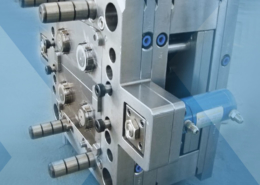
Unveiling the Dynamics of the Plastic Molding Business
Author:gly Date: 2024-06-08
The plastic molding business stands as a cornerstone of modern manufacturing, driving innovation, and efficiency across diverse industries. In this comprehensive exploration, we delve into the intricacies of the plastic molding business, shedding light on its evolution, applications, technological advancements, and future prospects.
Unraveling Plastic Molding
Introduction to Plastic Molding
Plastic molding, also known as injection molding, is a versatile manufacturing process that involves injecting molten plastic material into a mold cavity, where it solidifies to form a desired shape. This method has gained immense popularity due to its ability to produce complex parts with high precision and efficiency.
Historical Evolution
The roots of plastic molding can be traced back to the early 20th century when John Wesley Hyatt developed the first injection molding machine to produce celluloid billiard balls. Since then, advancements in materials science, machinery, and process optimization have propelled plastic molding into the forefront of industrial manufacturing, revolutionizing product design and production methodologies.
Market Landscape
The plastic molding business encompasses a wide array of industries, including automotive, aerospace, electronics, healthcare, and consumer goods. The demand for plastic components continues to soar, driven by factors such as population growth, urbanization, technological innovation, and evolving consumer preferences.
Applications Across Industries
Automotive Sector
In the automotive industry, plastic molding plays a critical role in the production of interior and exterior components, such as dashboards, bumpers, and trim panels. The lightweight nature of plastic parts, coupled with their design flexibility and cost-effectiveness, makes them indispensable for enhancing vehicle performance, fuel efficiency, and aesthetic appeal.
Electronics and Consumer Goods
Plastic molding finds extensive application in the electronics and consumer goods sectors, where it is used to manufacture casings, enclosures, and components for smartphones, appliances, and electronic devices. The ability to integrate intricate features, such as mounting bosses, snap fits, and internal ribs, facilitates product miniaturization, functionality, and durability.
Medical Devices and Healthcare
The medical industry relies on plastic molding for the production of sterile, high-precision components used in medical devices, diagnostic equipment, and surgical instruments. Biocompatible materials, stringent quality control measures, and regulatory compliance ensure the safety, efficacy, and reliability of plastic-molded medical products, contributing to advancements in healthcare delivery and patient outcomes.
Technological Innovations
Advanced Materials
Advancements in polymer chemistry have led to the development of a wide range of engineering thermoplastics tailored for specific applications in plastic molding. From high-temperature resistant resins to bio-based polymers, these materials offer enhanced mechanical properties, chemical resistance, and environmental sustainability, expanding the design possibilities and performance capabilities of plastic-molded products.
Industry 4.0 Integration
The integration of Industry 4.0 technologies, such as IoT sensors, AI algorithms, and data analytics, into plastic molding processes has ushered in a new era of smart manufacturing. Real-time monitoring of production parameters, predictive maintenance, and quality control measures optimize efficiency, minimize downtime, and ensure consistent product quality, thereby enhancing competitiveness and customer satisfaction.
Additive Manufacturing Synergy
The synergy between plastic molding and additive manufacturing technologies, such as 3D printing, enables rapid prototyping, tooling fabrication, and customization of plastic molds. Hybrid processes, such as mold inserts with conformal cooling channels, reduce cycle times, improve part quality, and enable complex geometries that were previously unattainable with traditional manufacturing methods.
Challenges and Future Outlook
Sustainability Imperative
The plastic molding industry faces increasing pressure to adopt sustainable practices and materials to mitigate environmental impact. Initiatives such as recyclable resins, biodegradable polymers, and closed-loop recycling systems are pivotal in addressing plastic waste and pollution while ensuring the long-term viability of the plastic molding business.
Skills Development
As plastic molding technologies continue to evolve, the demand for skilled professionals proficient in design, simulation, and process optimization grows. Training programs, apprenticeships, and academic partnerships are essential for nurturing talent and fostering innovation within the plastic molding workforce, driving continuous improvement and competitiveness in the industry.
Regulatory Compliance
Stringent regulatory requirements governing materials, processes, and product safety pose challenges for plastic molding businesses, particularly in highly regulated industries such as healthcare and automotive. Collaboration with regulatory agencies, adherence to industry standards, and investment in quality management systems are crucial for achieving compliance and maintaining market access.
Conclusion
The plastic molding business stands at the intersection of innovation, technology, and market demand, shaping the landscape of modern manufacturing. As we navigate the complexities of a rapidly evolving global economy, embracing sustainability, technological advancements, and talent development will be paramount in ensuring the resilience and prosperity of the plastic molding industry for generations to come.
GETTING A QUOTE WITH LK-MOULD IS FREE AND SIMPLE.
FIND MORE OF OUR SERVICES:
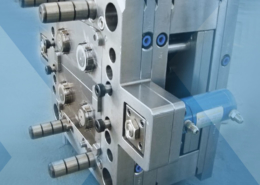
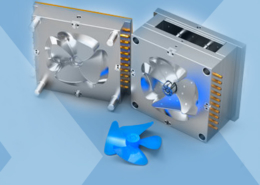
Plastic Molding

Rapid Prototyping
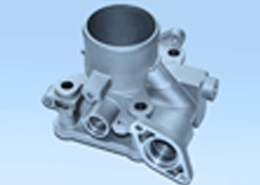
Pressure Die Casting
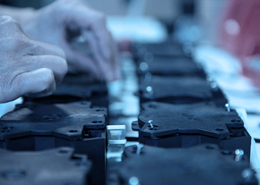
Parts Assembly
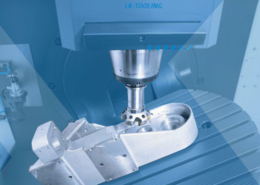