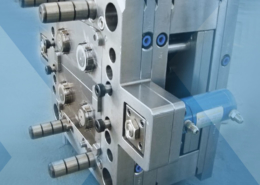
Genome of Alexander Fleming’s original penicillin-producing mould sequenced - in
Author:gly Date: 2024-09-30
NPE 2021 may have been cancelled, but that hasn’t stopped Wittmann Battenfeld from refreshing its product line. It recently shared information on new products and upgrades it has made across its portfolio of injection molding machines, automation systems, and auxiliary equipment. Here are some of the product announcements that stood out.
Such recycled plastics may have lower mechanical properties compared to virgin plastics, because each time you melt and process a plastic, the polymeric chains degrade. But these properties can be recovered by mixing it to additives or virgin plastic. Examples of successful industrial recycling include PET, or poly(ethylene therephtalate), which is used to make soft drinks bottles, and polystyrene.
The disposal of plastics is a highly visible global problem – from the highest mountains to the deepest ocean trenches, waste plastic seems inescapable. In natural conditions, plastics are nearly indestructible, and yet they are discarded worldwide on a large scale: the world produces around 359 million tonnes of plastics each year. The environment cannot address their disposal at a speed fast enough to prevent harm to living beings.
The company shares information on new products and upgrades across its portfolio of injection molding machines, automation systems, and auxiliary equipment.
There is a common conception that some plastic is "unrecyclable", but given the right treatment it need not go to landfill (Credit: Sibele Cestari)
So perhaps plastics are not necessarily the problem. They can be part of a pathway towards a more sustainable way of living. Using a natural or renewable resource is not necessarily environmentally friendly. The ecological footprint of a polymeric material is smaller than that of natural materials, which have a sizeable demand on arable land, clean water, fertilisers and regeneration time.
But there are many ways we could set plastics on a different lifecycle – and one that I have been working on is turning disused plastics into a hardy, reliable and sustainable building material.
Building materials made from recycled plastics are not yet widely used in the construction industry – prototypes have mainly been used for demonstrative installations. It will take political will and widespread environmental awareness to encourage more investment into the potential in plastics recycling.
Our team is currently trying to develop a viable building block made of recycled plastics. We have prepared a range of prospective materials using a mix of virgin and recycled plastics – coloured PET bottles, polypropylene, polyethylene – and other local waste-stream materials, such as hemp, sawdust, concrete waste and red mud.
Most people believe that plastics recycling is severely restricted: that only a few types can be recycled at all. This is unsurprising. The proportion of plastics that are recycled is minimal. The UK, for example, uses five million tonnes of plastic each year, and only 370,000 tonnes are recycled each year: that’s just 7%.
Wittmann Battenfeld’s ultra-high-speed Sonic robot series is already a customer favorite because of its performance, according to the company. It achieves maximum acceleration of 65 m/s2, allowing for mold-open times of less than 1 second and sub-10-second cycle times at payloads up to 15 lb. The ultra-high speeds require a robust design, said Wittmann Battenfeld, and it has created a streamlined, efficient, and durable new look for the Sonic Ultra series.
The company’s Primus robots are designed for pick-and-place applications, and Wittmann Battenfeld recently expanded the series with the largest Primus model yet — the Primus 48T. The 48T carries a 20-kg payload and has clamping forces between 20 and 900 T while maintaining the smooth and quiet operation for which the Primus series is known.
I study plastic waste with the specific aim of finding interesting ways to remove it from the environment. Since 2009, I have developed a number of building materials made of post-consumer plastics mixed with different waste-stream materials. From agricultural wastes such as sugarcane bagasse – a by-product of the sugar industry in Brazil – and coffee dregs, to concrete waste and construction debris, compounded with recycled plastics, there are many ways to obtain materials to produce bricks, roof tiles, plastic lumber and other useful elements for building.
We are also thinking about the aesthetics of the blocks. Blends of recycled mixed-colour plastics usually end up with a grey or black colour. To enable colour, we are preparing blends of virgin or recycled plastics to overlay the main bulk of the block.
Wittmann Battenfeld has made advances in its robot and automation line since the last NPE, notably adding new features to its R9 robot control system. Most of these new features involve making the control easier to use with the addition of a quick “wizard” programming function and ergonomic vertical touch screen pendants. Other new features have made the R9 smarter and more error-proof through the addition of Replay troubleshooting and the incorporation of anti-collision features. A digital twin simulator helps users better simulate complex processes ahead of time to more accurately predict outcomes.
Building with plastic waste requires fewer resources than natural products, and would otherwise go to landfill or into the oceans (Credit: Sibele Cestari)
Two of the newest product lines from Wittmann Battenfeld are Mold Area Protection (MAP) and the Internal Air Cooling System (IACS). MAP is used to prevent condensation on the mold surface. This allows for cold-water temperatures — below the dew point of the ambient air — to be run year-round without concerns about the impact of climate conditions on production or the life of the mold. Operated through a FIT controller, all processes are monitored and any potential errors can be quickly corrected and addressed. The low-maintenance MAP is available for use in injection molding and blow molding applications. The IACS improves the quality of blow-molded products by exchanging the internal cavity with cold air during the cooling phase, which reduces thermal stress on the material and shortens the cooling time.
Bricks like these could be the prototype for plastic bricks that are strong and durable enough to be used in construction (Credit: Sibele Cestari)
Plastics are strong, durable, waterproof, lightweight, easy to mould, and recyclable – all key properties for construction materials. So what if all of this plastic waste could be converted into building materials for low-income populations? Existing initiatives are promising, but not yet reproducible on an industrial scale.
But hopefully the tide is beginning to turn, as a consequence of the increasing pressure from public opinion about the plastic pollution matter. Thanks to the engagement of government and industry with the idea of a circular economy, it seems that there will be an opening in the market – and in people’s minds – to welcome plastic initiatives to replace conventional building materials.
If you liked this story, sign up for the weekly bbc.com features newsletter, called “The Essential List”. A handpicked selection of stories from BBC Future, Culture, Worklife, and Travel, delivered to your inbox every Friday.
Until she retired in September 2021, Clare Goldsberry reported on the plastics industry for more than 30 years. In addition to the 10,000+ articles she has written, by her own estimation, she is the author of several books, including The Business of Injection Molding: How to succeed as a custom molder and Purchasing Injection Molds: A buyers guide. Goldsberry is a member of the Plastics Pioneers Association. She reflected on her long career in "Time to Say Good-Bye."
This has led to a consensus that plastics are an unsustainable material. And yes, plastics are certainly an enormous problem, but they don’t necessarily have to be.
The problem is that recycling much of this plastic waste is currently unfeasible and unprofitable. Polymers such as rubbers, elastomers, thermosets and mixed plastic waste are comfortably labelled as “unrecyclable” by the recycling sector. But the amount of these materials all over the world is frighteningly large and keeps on growing. What if this plastic waste could be used to produce something useful to society?
Available as a package with the EcoPower and SmartPower injection molding machines, the Ingrinder system integrates an advanced granulator and sprue picker with the press itself. The Ingrinder works best as a solution for smaller injection molding machines that run with molds incorporating cold runner technology with a corresponding need for scrapping or recycling sprues, according to Wittmann Battenfeld. Ingrinder integration provides cost savings through a more efficient grind and smaller footprint.
We are currently adjusting the properties of the materials for the rotomoulding process, a plastics moulding technology that is ideal for making large hollow articles. We want to use the maximum amount of recycled plastics in this block. Blocks made of 25% recycled plastics have performed extremely well in mechanical tests. Next we’ll try 50%, 75% and 100%.
According to the Global Footprint Network, before the pandemic we were demanding 1.75 times the available resources of the planet. Working with the “unrecyclable” waste and developing plastics alternatives to natural materials may reduce this demand and leave a cleaner and more sustainable planet for the next generations.
Sibele Cestari is a polymeric materials scientist from Brazil, who is currently a research fellow at Queen's University Belfast. This article originally appeared on The Conversation, and is republished under a Creative Commons licence. This is also why this story does not have an estimate for its carbon emissions, as Future Planet stories usually do.
All of the rest can technically be reprocessed into new materials for different applications. In the final instance, any plastic waste can be shredded and used as filler for asphalt, or be pyrolysed – decomposed through heating – to produce fuel. The Japanese company Blest Corporation already sells a portable machine to convert domestic plastic waste into fuel in a simple, affordable way.
This website is produced by BBC Global News Ltd, a commercial company that is part of BBC Studios, owned by the BBC (and just the BBC). No money from the licence fee was used to create this website. The money we make from it is re-invested to help fund the BBC’s international journalism.
Plastic items we think of as rubbish can have a second life in construction due to the same properties that make them so hard to dispose of (Credit: Getty Images)
But all polymers are, technologically, 100% recyclable. Some of them have the perfect cradle-to-cradle lifecycle: they can be used again and again to produce the same goods. Some plastics can be reused just as they are by shredding an object into flakes, melting it, and reusing.
Many universities and entrepreneurs are attempting to do this. Most solutions target mixed plastic waste and suggest applications different from the original ones. For example, several groups have developed building materials made of plastic waste.
The main issue is not with plastic as a material, but with our linear economic model: goods are produced, consumed, then disposed of. This model assumes endless economic growth and doesn’t consider the planet’s exhaustible resources.
GETTING A QUOTE WITH LK-MOULD IS FREE AND SIMPLE.
FIND MORE OF OUR SERVICES:
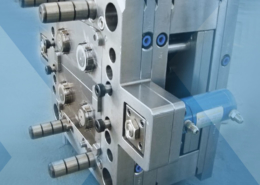
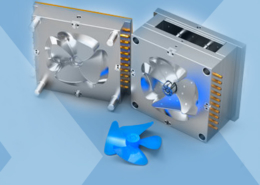
Plastic Molding

Rapid Prototyping
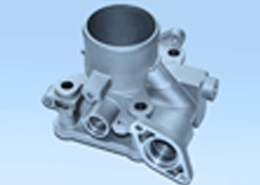
Pressure Die Casting
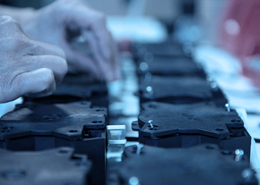
Parts Assembly
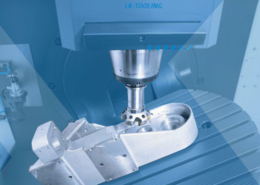