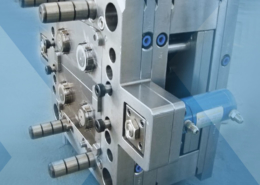
Full Specifications Released for the FOSSiBOT F101 rugged phone - injection mold
Author:gly Date: 2024-09-30
So what’s the solution? Well, partly, hold on to it if you can; sprues can be cut up to make bits of rubble for scenery and basing. Of course, this is hardly an end solution; miniatures come with an awful lot of sprue and there’s only so much you can hold on to indefinitely. It should be pointed out here that sprues can technically be recycled. Miniatures, like many other polystyrene objects, are made by a process called injection molding, where hot plastic is pumped into a mold at high pressure. There’s no reason, therefore, why sprues can’t be melted down again and used to create new figures. The problem is that there isn’t yet a process in place for doing so. It’s a tricky situation, and it’s one that Miniature Wargames will continue to investigate. There have been games companies in the past that have had a sprue recycling scheme, so if there’s any way you can hold on to them then it’s certainly worth doing so. Alternatively, you could see if there are any polystyrene recycling facilities in your local area. If neither option is viable, however, then landfill is definitely preferable to putting in the recycling bin. Landfill certainly isn’t an ideal solution – not just with sprues but generally – but, as Keith explains, if you put plastic in landfill it at least acts as a carbon sink and you lock the plastic in a place that won’t damage the environment as much.
The truth, however, is that putting plastics – including those sprues – that aren’t presently recycled in the recycling bin is in fact worse than sending it to landfill. I spoke to Keith Freegard, an expert in plastic recycling and all-round knowledgeable chap.
If you’re anything like me, you may have taken the ‘better safe than sorry’ approach in the past when it comes to putting stuff in the recycling bin, and included every bit of plastic used. At best, so my optimistic line of thinking went, it’d be stored somewhere until that happy day when recycling systems could deal with the waste, and at worst, it’d just go to landfill like the rest of the rubbish.
Monroe Capital LLC provided financing for the acquisition. Winston & Strawn LLP provided legal representation to Core and Fathom in the transaction.
In-house metalworking capabilities include engineering design, sheet metal shearing, punching and bending, roll forming, hardware integration, welding, grinding, polishing, painting, and assembly. Summit’s thermoplastics engineering expertise allows the company to process multi-shot and bi-injected tooling and perform insert overmolding. Pad printing, hot stamping, ultrasonic welding, and assembly are also offered by the company, which operates a 26,000-square-foot facility northwest of Chicago in McHenry, IL.
Founded in 1996, Summit provides plastic injection mold design, precision mold making, and close-tolerance injection molding with a specialty in small to medium prototype injection molds. Summit primarily serves long-tenured customers in the medical and packaging end markets with its fleet of more than 30 machines, said Core's announcement.
“Summit’s focus on customers during the design, prototyping, and low-volume production stages of a product’s life cycle perfectly aligns with Fathom’s unique customer-value proposition,” Fathom CEO Ryan Martin said in a prepared statement. “We’re excited to work with the Summit team to explore opportunities to even better serve its customers through Fathom’s comprehensive digital manufacturing platform while also providing Fathom’s existing customer base expanded domestic quick-turn precision tooling and molding capabilities,” added Martin.
There are seven different grades of plastic that can be recycled - if you’ve ever looked at a plastic item and seen that triangular symbol with the number inside it, that’s what it is. The plastic used for making miniatures is a derivative of polystyrene (yes, the same stuff that makes packing foam). For recycling, that’s grade number six. Sadly, along with grades four and seven (low-density polyethylene and all other types of plastic, respectively), polystyrene is at present almost never recycled in the UK.
Chicago-based private-equity firm Core Industrial Partners announced today the acquisition of Summit Tooling Inc. and Summit Plastics Inc. by its portfolio company Fathom. The precision tooling and injection molding supplier is the fourth add-on acquisition to the Fathom platform since Core made its initial investment in 2018.
“Summit’s leading customer base includes some of the largest and most recognizable players in the medical and packaging spaces,” said Matthew Puglisi, Partner of Core. “This acquisition significantly enhances Fathom’s domestic injection molding and tooling capabilities, and we’ll continue to actively pursue acquisitions, similar to Summit, that simultaneously broaden our customer base, enhance our service offering, and deepen our presence in attractive, recession-resistant end markets.”
The above may sound harsh, and it may seem as though I’m implying that gamers are bad people for their choice of pastime. This couldn’t be further from the truth! Many gamers care about the environment, and scratch-building terrain from things like leftover cans and packaging has long been a part of the hobby. A lot of the time, the problem comes down to a lack of information. Many gamers are confused about whether sprues can be recycled, and with good reason, as there’s not really a clear-cut answer. In fact, the problem goes far deeper than sprues; plastic recycling in general is something of a headache. According to a report from the BBC, there are no less than 39 different sets of rules across the UK for recycling plastic. Since the government doesn’t have a centralized system for dealing with the UK’s waste, the responsibility falls on local councils instead, and what can be recycled differs heavily according to which area you live in.
“The household recycling system is really just for PT bottles, HDPE milk bottles and some types of packaging”, Keith explains. “Recyclers wouldn’t want bits of sprue coming through as they wouldn’t get sorted at the sorting plant. Instead, it’s more likely that this unidentified plastic ends up with bits of cardboard and other things, which all gets sent to an Energy from Waste plant where it gets incinerated and releases long-life carbon up into the atmosphere. It’s not like burning paper, say, where you’re burning a bit of tree that’s maybe 50 years old; your burning a bit of oil that’s millions of years old. So when you send plastic to Energy from Waste plants you’re adding to the global warming effect at the same time.”
Core Industrial Partners’ portfolio company Fathom acquired the precision tooling and injection molding supplier serving customers in the packaging and medical markets.
Dan Martin, President of Summit, commented: “Since my wife, Michelle, and I founded Summit 25 years ago, we’ve been committed to providing outstanding quality and customer service to build the business into a leader in the design, engineering, and construction of molds and molded components. We’ve now reached an inflection point in our growth trajectory, and we believe Fathom is the perfect fit in terms of both culture and customer-value proposition to help take Summit to the next level.”
It’s a sad fact that like nearly every other human activity, our hobby has a carbon footprint and an impact on the environment. Admittedly, it’s probably a small footprint in comparison to other industries but, as the old saying goes, ‘if you ain’t part of the solution…’
Besides the impact of logistics, arguably one of the biggest areas of environmental impact is the use of plastic to make miniatures. Plastic is an almost ideal material for miniatures; it’s soft enough to cut, holds primer well, doesn’t degrade and is easy to glue. The main problem with plastic miniatures, however, is the amount of waste material they produce in the form of leftover sprues.
GETTING A QUOTE WITH LK-MOULD IS FREE AND SIMPLE.
FIND MORE OF OUR SERVICES:
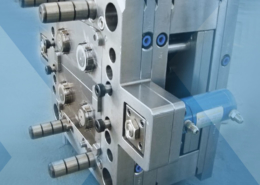
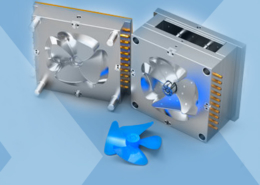
Plastic Molding

Rapid Prototyping
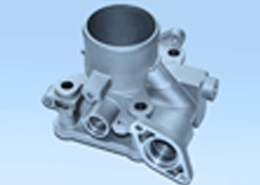
Pressure Die Casting
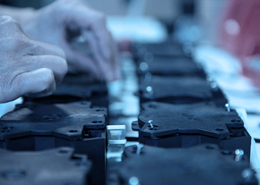
Parts Assembly
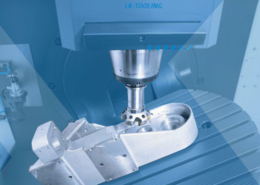