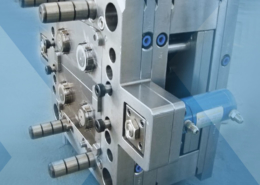
Fu Yu breaks the mould, redefines precision plastic manufacturing with
Author:gly Date: 2024-09-30
Together with Tier 1 supplier Faurecia, Engel is demonstrating the potential of structural foam molding technology at its K booth. Sample parts with a sophisticated surface structure are being produced on an Engel duo 1000 injection molding machine. The new MicroJect Advanced process developed by Faurecia Interiors (Hagenbach, Germany) and Eschmann Textures International (Gummersbach, Germany) is being used in this application. The process makes it possible to produce lightweight, visible components with a high-quality Class A surface using only structural foam molding.
If you’re looking to experience the magic of a Mold-A-Rama (or its cousin, the Mold-A-Matic) for yourself, here is a list of 10 locations where you can see these marvelous machines in action. If you happen to be in the Chicagoland area, take a trip to the Museum of Science and Industry and check out their latest exhibit, Mold-A-Rama: Molded for the Future.
The Mold-A-Rama machine was invented by J.H. “Tike” Miller and debuted at the 1962 Seattle World’s Fair. The initial batch of models included a monorail, a Buddha, and a 3D sculpture of the Fair’s logo. The 1964 World’s Fair in New York City, however, made Mold-A-Rama a household name. It is said that as many as 150 machines were installed over the Fair’s two-year timeframe, and models included various dinosaurs, Disney characters, animals, and presidential busts. After being featured at the Montreal World’s Fair, Expo ’67, Mold-A-Rama machines became staples at museums, zoos, amusement parks, and anywhere that sold souvenirs.
In general, structural foam molding requires less energy and raw material, and uses lower clamping forces, than conventional injection molding. The dissolved blowing agent improves flowability of the molten plastic. In addition, the foam molding pressure, which is independent of the location, enables molding of thicker ribs. These effects can be used to reduce wall thickness, which has a positive effect on the required cooling time and, in turn, on the cycle time.
Alexis Gajewski has over 15 years of experience in the maintenance, reliability, operations, and manufacturing space. She joined Plant Services in 2008 and works to bring readers the news, insight, and information they need to make the right decisions for their plants. Alexis also authors “The Lighter Side of Manufacturing,” a blog that highlights the fun and innovative advances in the industrial sector.
What happens when you combine a vending machine with plastic injection molding and add in a pinch of mid-century flair? You get a Mold-A-Rama machine. If you’re not a Midwesterner, then you might not know what I am talking about. But for those of us who grew up in Illinois, Minnesota, Michigan, or Wisconsin, Mold-A-Rama holds a special place in our nostalgic hearts. Every time I went to the Brookfield Zoo or the Field Museum of Natural History, I would drag my parents to the closest machine and beg them to buy me a tiny plastic statue. The real magic, however, was in watching the figurine being created right in front of our eyes in less than one minute. This became many kids’ first introduction to manufacturing.
Here's how it works. First, insert your money into the machine. (Back in my day, each statue cost $1. The current price per figurine is $5. Thanks, inflation.) Next, two thick aluminum plates are pushed together, creating the mold. Polyethylene pellets, heated up to approximately 250°F, are then injected into the mold, while a blast of air works to hollow out the piece. Unnecessary plastic is removed through a drainage hole in the bottom of the mold. The statue is then cooled and hardened before the plates pull apart and the piece is pushed into the pick-up box.
Whereas each injection molding machine previously required its own gas supply, Engel now offers the e-foam XL multi, a central unit for supplying several injection molding machines with highly compressed nitrogen for structural foam molding. Only the plasticizing and control technology remain decentralized on the individual machines. This new solution sees Engel significantly reduce the capital outlay for structural foam molding and makes a major contribution to reducing unit costs. The new modular Engel e-foam XL multi systems, based on Trexel's MuCell technology, are offered exclusively by Engel.
In addition, new materials developed by Faurecia Interiors for structural foam molding contribute to the surface quality. An IniCycle talc-filled polypropylene grade with 30% recycled material content will be processed during the K show. IniCycle is suitable for all physical and chemical foam molding processes.
Engel is improving the cost effectiveness of structural foam molding with its new e-foam XL gas supply units that support multiple production cells.
Further, the combination of new system technology by Engel and MicroJect Advanced leverages unprecedented efficiency and sustainability potential in structural foam molding, according to Engel. Structural foam molded parts no longer need to be painted, and there is no need for additional energy-intensive process technology, such as intermittent mold heating, for parts in customer-facing applications.
The mid-century machines remain popular to this day. According to the current owner, one in 10 people who pass a machine buy a model, and the company uses about 640 55-pound bags of plastic pellets a year. Each Mold-A-Rama machine hold a gallon of hot liquid plastic and can produce up to 150 figures a day.
Structural foam molding is more popular than ever. It saves raw material, energy, and weight, supporting the objective of producing and using plastic parts in a more sustainable way. At K 2022, Engel (hall 15, booth C58) is presenting a new technology for plastics processors who produce parts in parallel on several production cells using the structural foam molding process.
Among other things, a new tool technology is responsible for this leap in development. Ceramic coatings in the cavities prevent the otherwise typical foam streaks, weld lines, tiger stripes, or gloss differences from appearing on the surface of the foam molded part. Additionally, different surface structures can be created directly in the injection mold via the cavity coating.
GETTING A QUOTE WITH LK-MOULD IS FREE AND SIMPLE.
FIND MORE OF OUR SERVICES:
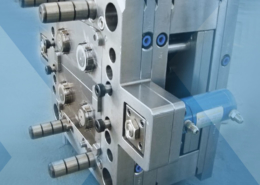
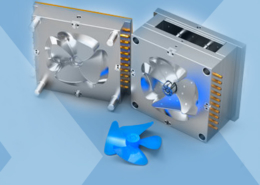
Plastic Molding

Rapid Prototyping
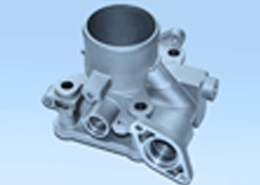
Pressure Die Casting
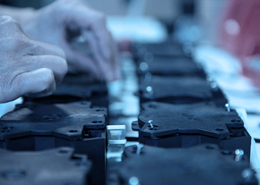
Parts Assembly
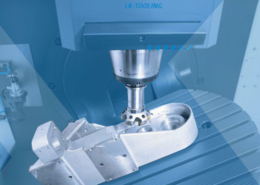