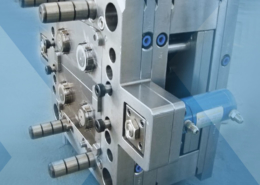
From rapid prototyping to rocket engines: The evolution of 3T Additive
Author:gly Date: 2024-09-30
Milacron has aggressively expanded its rebuild and remanufacture capabilities for LPIM machines for customers. There are a large number of old LPIM machines in the field that were purchased in the late 1980s and 1990s that need rebuilds and upgrades to control systems and new motor and drive selections, moving away from DC to AC drives which provide better energy efficiency. Milacron’s full remanufacturing consists of fully rebuilding the machine to current model specifications, including full teardown and inspection, platen refurbishment, full re-painting of the machine, new controls, electrical system, and hydraulics. The major tonnage and injection cylinders and hydraulic accumulators are sent out for refurbishment and resealing. New screws, barrels, and injection melt accumulators are also included as part of this program.
Parts molded with LPIM can replace many rotational molded or industrial blow molded parts with better aesthetics and better cycle times.
A spokesperson for the company, which manufactures plastic-injection molding for products used in a variety of sectors, views the move as a smart step to meet the needs of regional customers.
At NPE, 20/20 entered into an agreement with Milacron to refurbish and upgrade two of their existing 400-ton LPIM machines to 500-ton LPIM machines, and one of their 500-ton LPIM machines to 750-ton LPIM machines. 20/20 is also having Milacron rebuild and upgrade five of their 750-ton LPIM machines. The machines will undergo a complete remanufacture and rebuild process at Milacron’s Batavia, OH manufacturing plant and be returned like new machines.
Ernsberger added, “Milacron worked closely with our entire team at 20/20 to identify the upgrades to the existing machines to be rebuilt that will put these machines above today’s current machine specifications and give us the widest capabilities for these size machines in the industry.” Ernsberger continued, “We also had Milacron integrate some proprietary technologies into their machines that allow us to have the most versatile LPIM Structural Foam machine fleet in the custom molding market. It’s a great partnership between the companies, as all equipment at 20/20 CMP is 100% Milacron.”
In total, Milacron is currently rebuilding eight LPIM machines as well as four HPIM machines. “Milacron’s commitment to the LPIM side of the industry, their quality, performance, and service is second to none and is the reason that we made this decision to have them rebuild and upgrade this equipment,” said Ron Ernsberger, President, 20/20 Custom Molded Plastics.
Ideal for injection molding large, lightweight, durable structural plastic parts, the Milacron LPIM Structural Foam Technology creates a cellular foamed core surrounded by integral skins, forming a total integral and rigid structure. In this process, a foaming agent (nitrogen) is mixed with the polymer melt and short-shot through a modular multiple nozzle system into a mold (or multiple molds) in a volume less than is required to fill a solid part. The injection pressure and expanding gas/polymer cellular mixture act to fill the mold. The mold cavity pressures are 10–20 times lower than conventional injection molding which permits the use of lower cost aluminum molds with no additional hot runner system since the hot runner manifold and nozzle system is integral to the machine. Many molds and large parts of different sizes can be molded at the same time. The multi-nozzle machine design allows for multiple molds to be run simultaneously allowing for higher productivity.
Atlantis is moving to the park after 40 years of operations in Milton, where it has produced plastic parts used in the military, medical, automotive, consumer and industrial markets in a 35,000-square-foot space. Its products range from underbody panels on cars, to plastic restaurant tumblers that can be found at the Miltonian restaurant in Milton. Atlantis also produces parts used by companies such as ILC Dover, a Frederica-based maker of products for the pharmaceutical, aerospace and bulk packaging industries.
The markets driving the increased level of activity are material handling (pallets and boxes), underground enclosures for telecommunications and utilities, drainage and irrigation products, all-terrain vehicle (ATV) components, commercial/institutional, and industrial and safety products. Milacron is also seeing other new products being developed that are conversions from concrete, metal, and wood in the building and infrastructure market as well.
The 74 new acres in the park previously comprised the King Farm, which Sussex County purchased in order to offer space to 10 to 12 new tenants, in addition to the 20 businesses that already employ about 900 people at the industrial park. The complex has now been renamed the Delaware Coastal Business Park and is adjacent to Delaware Coastal Airport.
“One of the biggest advantages is being central to our primary customer base,” said Atlantis Industries General Manager Chuck McClure. “With the exception of a couple of customers, we are within a one-day drive to them. This allows us to provide another level of customer service and respond quickly to changing needs.”
Guy said other light-manufacturing operations may look favorably on the site because it is shovel-ready, with infrastructure in the ground, and also offers limited permit review. “The goal is to offer a site and review process that allows businesses to get off the ground faster and be up and running sooner,” Guy said.
Eric Hallstrom, Business Manager, Milacron LPIM added, “Milacron has been promoting our proprietary Structural Web technology that allows for multi-point gas assist molding that can be added to as an option to our standard LPIM machine. The process allows for a cosmetic part appearance for large projected area parts and can reduce part weights by up to 20%. The gas assist process also creates an inherently strong and durable part, molded with low internal stresses and a dual wall thickness which can replace many rotational molded or industrial blow molded parts with better aesthetics and better cycle times for higher volume parts.”
Hallstrom added, “Essentially we are updating machines that have been in production for over 30 years and bringing them up to the same specifications as our new machines. This has been especially popular since we started to promote this capability to our customers, as they see a significant enough savings since we are re-using the most expensive parts of these large machines, being the bases, platens, and cylinders. The customer gets back a machine that outperforms the machine’s original specifications and is as reliable as a new machine with the same warranty.”
In March, Sussex County officials spent $2.2 million to add 74 acres to Sussex County Industrial Park, demonstrating their optimism for the future of light manufacturing in the Cape Region.
Machine builder Milacron Holdings Corp. has seen demand increase for its Low Pressure Injection Molding (LPIM) Structural Foam machines following a successful NPE 2018 in Orlando, FL, including machine rebuilds. Milacron had a dedicated space in the NPE booth focusing on LPIM technologies and large part molding. An eye-catching display showed a replica platen of the massive Cincinnati 6,750 ton machine sold to 20/20 Custom Molded Plastics of Holiday City, OH.
By the end of January, Atlantis Industries will become the first tenant to occupy the expanded area, bringing 35 full-time employees from the company’s site in Milton.
Milacron CEO Tom Goeke stated, “Stories like 20/20’s machine retrofits reinforce the fact that Milacron has an unrivaled aftermarket offering. Our aftermarket offerings aren’t only spare parts, we can literally take an older machine and transform it to like new condition. Milacron has set the standards, driven innovation and led the industry in Multi-Nozzle Low-Pressure Injection Molding Technologies for more than four decades. These machines can be used for Structural Foam, Structural Web, Gas Assist, Solid Molding, or combinations of these technologies depending on the application.” Goeke added, “The LPIM market is strong for our customers that require either new or rebuilt machines in both North America and Europe, and we have a number of solid inquiries both domestically and internationally including many from Latin America and India.”
Machines delivered in the 1980s and 1990s are being upgraded to outperform their original specifications, while new machine deals also are accelerating.
Atlantis constructed a new, 40,000-square-foot production facility in the park. The workforce at the new site will initially remain the same as in Milton, but McClure said Atlantis expects to add more jobs by the end of 2018 or early in 2019.
“The county is currently in negotiations with one interested tenant, with the hope of securing the second lease shortly,” he said. “We have also had several inquiries, including from one group out of Virginia looking to expand its current enterprise,” Guy said, noting company representatives flew in to meet with county representatives to discuss the park.
Stephen has been with PlasticsToday and its preceding publications Modern Plastics and Injection Molding since 1992, throughout this time based in the Asia Pacific region, including stints in Japan, Australia, and his current location Singapore. His current beat focuses on automotive. Stephen is an avid folding bicycle rider, often taking his bike on overseas business trips, and is a proud dachshund owner.
GETTING A QUOTE WITH LK-MOULD IS FREE AND SIMPLE.
FIND MORE OF OUR SERVICES:
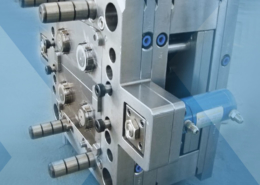
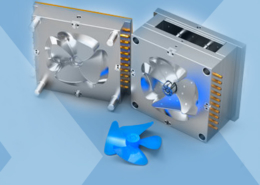
Plastic Molding

Rapid Prototyping
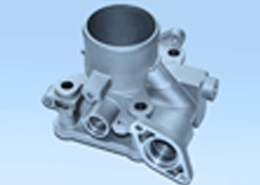
Pressure Die Casting
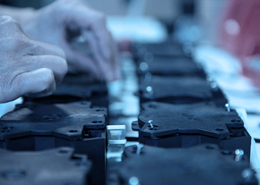
Parts Assembly
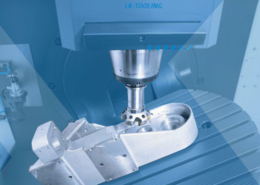