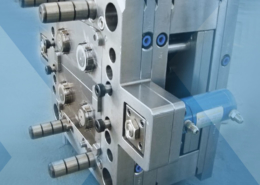
Formlabs says new 3D printer ‘rivals injection molding’ - molding over molding
Author:gly Date: 2024-09-30
In-mould part cooling is the most time-consuming part of the plastic injection moulding process – reduce the time for part cooling and you will increase production speed whilst achieving higher quality moulded parts with less scrap. A variety of techniques have been used to maintain even temperatures over the years, using methods such as bubblers, heat pipes and complex drilling operations using laminated blocks. These, however, are cumbersome, time consuming and can limit the useful life of a mould. Drilled cooling channels are also limited to straight lines, no matter what the part geometry.
Gifted with extraordinary technical know how and an authoritative yet plain English writing style, in this collection of articles Fattori offers his insights on a variety of molding-related topics that are bound to make your days on the production floor go a little bit better.
August 29-30 in Minneapolis all things injection molding and moldmaking will be happening at the Hyatt Regency — check out who’s speaking on what topics today.
Rauch is also confident that we are just seeing the start of what conformal cooling using AM can do for the plastic injection moulding industry. “Right now, the technology is constantly evolving as new materials and better machines become available. But I think we are still scratching the surface of what AM can truly do for the moulding industry. The big changes won’t begin to happen until the people accept change. Designers must learn to think differently and design differently. Applying system level thinking into the engineering process has the power to change everything. Engineers with an open mind will become innovators overnight, and tooling companies willing to use AM in the production environment will become pioneers in what I believe is going to be the next industrial revolution.”
Conformal cooling moulds have curved cooling channels that conform closely to part geometry and their use for an injection mould can reduce cycle time by anywhere from 10% to 40%. The low range gains are possible with little to no engineering analysis; the higher estimates reflect the use of flow analysis, computational fluid dynamics and finite element analysis.
Core Technology Molding turned to Mold-Masters E-Multi auxiliary injection unit to help it win a job and dramatically change its process.
Join this webinar to explore the transformative benefits of retrofitting your existing injection molding machines (IMMs). Engel will guide you through upgrading your equipment to enhance monitoring, control and adaptability — all while integrating digital technologies. You'll learn about the latest trends in IMM retrofitting (including Euromap interfaces and plasticizing retrofits) and discover how to future-proof your machines for a competitive edge. With insights from industry experts, it'll walk you through the decision-making process, ensuring you make informed choices that drive your business forward. Agenda: Maximize the value of your current IMMs through strategic retrofitting Learn how to integrate digital technologies to enhance monitoring and control Explore the benefits of Euromap interfaces and plasticizing retrofits Understand how retrofitting can help meet new product demands and improve adaptability Discover how Engel can support your retrofitting needs, from free consultations to execution
The correct software, believes Lindemann, is fundamental to achieving success in this sector and the designer needs support in ensuring both functionality and manufacturability. “Not all conformal cooling lines are good waterlines for their intended function or even good to be printed. There are design standards associated with all of this and having the right CAD software that works with these standards is invaluable. We recommend using Cimatron software for the mould design software that has dedicated functionality for conformal cooling that allows for consistent use of ‘printable’ waterlines and waterlines that are checked for consistent distance from the mould surfaces to hold the conformal effect.”
While prices moved up for three of the five commodity resins, there was potential for a flat trajectory for the rest of the third quarter.
“Up until now, most waterline passages were machined with some type of a drill bit – as all water circuits travelled in a straight line. So a blocked waterline just meant you had to run a drill bit back through the straight drilled hole to clear it out and everything’s good to go. With conformal cooling, it’s not so easy. The conforming line that follows the three-dimensional shape of the geometry makes it impossible to clean out in this way. I therefore urge all of our customers to invest in a closed-loop system so you have filtration options and much better control of the quality of water you are using. Once you have water quality in check you can then view conformal cooling as a perfect technological solution for injection moulding.”
Commenting on the increasing demand for injection moulding tooling with conformal cooling, and expectations of growth in the near term, Rauch stated, “Seeing the demand increase for AM with conformal cooling in the moulding industry has really been exciting. As with all disruptive technologies it takes some time for a new solution to become the new ‘norm’ and I believe we are still just scratching the surface of what Additive Manufacturing can do for the moulding world. B&J Specialty has seen the results and we know that conformal cooling is a huge game changer. I would say in the next five years almost all of the moulds we build will have some type of AM components with conformal cooling in them.”
Commenting on how 3D Systems is helping toolmakers embrace AM in order to develop their conformal cooling capabilities, Lindemann stated, “We have the software to assist and can work with the customers on a job by job basis and prove out the design. The customer may naturally hesitate to jump in with both feet and buy a metal AM system that he knows little about. We have services where we can print the mould core and prove out its viability and best case situation for printing. Once it is seen as a success, then the customer can move forward using this proven process on their own. They will be trained to use the software and the machine and start manufacturing their own cores per the proven process.”
As with any technology, conformal cooling can be applied well or applied poorly. Commenting on what sets a great solution apart from a poor solution, Rauch explained, “Not all conformally cooled tooling solutions are created equal. When you are designing a conformal cooling passage you are trying to achieve several different things. The number one goal when wanting to be successful with conformal cooling is figuring out how you can rapidly and uniformly dissipate the heat over the entire surface of the moulding geometry. One of the most important factors that comes into play when achieving this goal is confirming that the conformal circuit itself produces turbulent flow inside the water passage. The best way to achieve this is by using CFD analytical software that simulates the fluid’s flow through the line. The Reynolds Scale helps us determine if we are obtaining turbulent flow inside our additively manufactured waterline geometry. The Reynolds number scale is a scientific way to measure flow patterns in different situations. Fluid travels in three different ways; laminar, transitional and turbulent. Laminar flow is when the molecules are following a smooth and steady path in a parallel fashion. An example would be when you open a tap to the slowest flow you can get and the water comes crystal clear.”
Additive Manufacturing has been used to build moulds incorporating conformal cooling channels since the 1990s when the first metal powder-based AM systems came to market. The AM process in those early days used CO2 lasers and required metal powders coated with polymer binder, which would evaporate out after the part was built. The part would then be infiltrated with a second metal to remove the porosity. Today, the technology has moved on considerably, and the new generation of AM systems uses significantly more precise fibre lasers, high purity metal powders and an oxygen-free manufacturing environment.
Whilst conformal cooling solutions can significantly reduce the total cost of production by lowering mould cycle times, they also require sophisticated mould designs. A well-designed conformal cooling mould typically has a wide variety of unconventional curves, twists and shapes that must be precisely placed. Once designed, these complicated moulds must be manufactured to the same standards as any other mould.
Additive Manufacturing conferences rarely attract as many industry CEOs as New York's Additive Manufacturing Strategies event, let alone persuade t...»
Second quarter started with price hikes in PE and the four volume engineering resins, but relatively stable pricing was largely expected by the quarter’s end.
Lindemann believes that it is crucial to understand the limits of the technology and to apply it only as appropriate. He stated, “There certainly are many ‘upsides’ but this is when the conditions are right. There has to be a realistic expectation. Mould builders making extremely large muolds look at the additive process and say that it is not for them. Their moulds are simply to large. There is however a trend in applying additive in a limited degree by creating mould inserts that are of printable size for key areas of the mould where conformal cooling would be beneficial. This requires some creative engineering but many are getting good results.”
In this collection of content, we provide expert advice on welding from some of the leading authorities in the field, with tips on such matters as controls, as well as insights on how to solve common problems in welding.
In this three-part collection, veteran molder and moldmaker Jim Fattori brings to bear his 40+ years of on-the-job experience and provides molders his “from the trenches” perspective on on the why, where and how of venting injection molds. Take the trial-and-error out of the molding venting process.
Across all process types, sustainability was a big theme at NPE2024. But there was plenty to see in automation and artificial intelligence as well.
Resin drying is a crucial, but often-misunderstood area. This collection includes details on why and what you need to dry, how to specify a dryer, and best practices.
Don't miss any new issue of Metal AM magazine, and get the latest industry news. Sign up to our twice weekly newsletter.
Plastics Technology covers technical and business Information for Plastics Processors in Injection Molding, Extrusion, Blow Molding, Plastic Additives, Compounding, Plastic Materials, and Resin Pricing. About Us
Say “manufacturing automation” and thoughts immediately go to the shop floor and specialized production equipment, robotics and material handling systems. But there is another realm of possible automation — the front office.
Our audience includes component manufacturers, end-users, materials and equipment suppliers, analysts, researchers and more.
Exhibitors and presenters at the plastics show emphasized 3D printing as a complement and aid to more traditional production processes.
Rauch continued, “When other forces such as change in direction and obstructions disrupt the flow, it starts to change into what is known as transitional flow. Once the flow has become fully disrupted and a mixing and stirring action happens, turbulent flow has been achieved. This is the goal when I design conformal geometry, because once the fluid travelling inside the conformal passage becomes turbulent I know trapped heat within the steel AM part will start to rapidly dissipate. The mixing action from turbulent flow transfers heat away from the geometry it is travelling through more effectively because you are mixing the warmer fluid near the walls of the cooling passage with the relatively cooler interior fluid. It’s just like a hot cup of coffee – if you stir it with a spoon it will cool faster than just letting it sit still. If a designer takes all of these things into his thought process when designing a conformal cooling solution, they will be able to capitalise on the capabilities of what conformal cooling can do in the moulding industry.”
Despite the limitations of the early technology, tooling became one of the most important markets for the fledgling metal AM industry and the sector is regarded as one of the first real commercial applications of the technology. Whilst this success continues today, the use of Additive Manufacturing in the mould and die industry remains relatively niche compared to conventional toolmaking technologies.
Multiple speakers at Molding 2023 will address the ways simulation can impact material substitution decisions, process profitability and simplification of mold design.
Join KraussMaffei for an insightful webinar designed for industry professionals, engineers and anyone interested in the manufacturing processes of PVC pipes. This session will provide a comprehensive understanding of the technology behind the production of high-quality PVC pipes: from raw material preparation to final product testing. Agenda: Introduction to PVC extrusion: overview of the basic principles of PVC pipe extrusion — including the process of melting and shaping PVC resin into pipe forms Equipment and machinery: detailed explanation of the key equipment involved — such as extruders, dies and cooling systems — and their roles in the extrusion process Process parameters: insight into the critical process parameters like temperature, pressure and cooling rates that influence the quality and consistency of the final PVC pipes Energy efficiency: examination of ways to save material and energy use when extruding PVC pipe products
The Plastics Industry Association (PLASTICS) has released final figures for NPE2024: The Plastics Show (May 6-10; Orlando) that officially make it the largest ever NPE in several key metrics.
Commenting on what attracted B&J Specialty to 3D Systems’ technology offer, Rauch explained, “When we decided to invest in Additive Manufacturing, we looked at several different machine manufacturers, but when we considered what 3D Systems had to offer we were drawn to the fact that they not only focused on the printers themselves but also a complete line of design software that streamlines the conformal cooling development process. Having a good workflow simply makes good business and 3D Systems provides that with its end-to-end solutions for the tooling industry. From the start I can transition from design to build preparation and manufacturing, all from within the same piece of software. This is a huge time saver. We all talk about how AM can affect the supply chain because we can now take a digital design file and, in a matter of hours, have a finished product. 3D Systems seems to understand this, having the same mindset when developing its products. Other companies that we looked at had good machines but fell short when it came to having that smooth flow from the digital to the physical.”
B&J Specialty uses a portfolio of dedicated software solutions from 3D Systems to develop its conformal cooling solutions, including Geomagic® Design X™, Cimatron® and 3DXpertTM. The tool parts are then built on a 3D Systems ProX® DMP 300 Laser Powder Bed Fusion system.
Discover suppliers of these and more in our comprehensive advertisers’ index and buyer’s guide, available in the back of Metal AM magazine.
Rauch believes that the sector’s growth is coming from both a combination of customers who are demanding faster process times and from innovative toolmakers looking to gain a competitive advantage in terms of their technology offering. “At this point it has been almost a 50/50 split between these drivers, however I am starting to see a change as AM has become a real game changer in the moulding industry. Now I am seeing larger companies wanting to ‘go additive’ without a company such as ours trying to sell the technology. The door has opened and we are beginning an industry-wide transition.”
Take a deep dive into all of the various aspects of part quoting to ensure you’ve got all the bases—as in costs—covered before preparing your customer’s quote for services.
This Knowledge Center provides an overview of the considerations needed to understand the purchase, operation, and maintenance of a process cooling system.
When it comes to presenting a review of the world's largest international exhibition for AM, one can go about it in two ways: very broad generalisa...»
While the major correction in PP prices was finally underway, generally stable pricing was anticipated for the other four commodity resins.
Myers has also been innovating with 3D printing equipment, starting with a MakerBot and then moving to a Flash Forge FDM Creator, which allows him to use ABS, PLA, and PEI. He has used the latter to make the cavity and core used in molding the Cozmo mid-range and putter discs. He has also used FusionFX with 3D printing as a subcontractor for production of new sporting goods such as flying tubes, as well as pet items.
3D printing a core and cavity on machine from Gefertec, followed by machining, allowed for a complete mold tool to be produced in three days.
Myers has been using a 1981 Arburg 221E, 77-ton toggle horizontal molding machine that he acquired from a lab, and more recently bought a 1993 200-ton Toyo press. He’s running a 0.913 density EVA because it’s very clear and can run at very low temperatures—220 F maximum. He has used metallocene elastomers that provide extra clarity and flexibility for his higher-end discs. “The EVA is a very friendly material—slightly rigid but also offers flexibility and good gripping characteristics,” says Myers. Moreover, Myers says FusionFX masterbatch is easy to process. “I have turned down my backpressure so that it will disperse optimally as it does not disperse in the barrel. Rather, it blossoms when it hits some shear in the gate that enters the mold cavity.”
Introduced by Zeiger and Spark Industries at the PTXPO, the nozzle is designed for maximum heat transfer and uniformity with a continuous taper for self cleaning.
B&J Specialty, Inc., based in Wawaka, Indiana, USA, offers precision machining, engineering and mould and die services to customers in the US Midwest. With the support of technology from AM technology provider 3D Systems, headquartered in Rock Hill, South Carolina, USA, the company works to offer high performance plastic injection moulding tooling for customers through the implementation of additively manufactured conformal cooling solutions.
Ranging in size from 3.75 to 4.5 in. diam., Zing Mini’s product lineup includes: Aerofoil, the largest disc, with a throw distance of more than 250 ft; Microfoil, popular for indoor use, as a course marker, and as a promotional item; and Cozmo, a mid-range and putter disc, dubbed by Myers the “competitor killer.”
Supporting software is crucial to the successful and efficient development of all AM applications; however, this is especially true when it comes to the design of a conformal cooling mould. Rauch explained, “3D Systems’ Cimatron and 3DXpert packages have been phenomenal at giving me the tools needed for quickly navigating the process of designing an entire mould or just a single part for production by AM. I feel that, to be truly successful with additive, a designer has to completely change how they design – it is not a cliché that you have to design for additive. As tool designers we have all been taught to design a certain way. We had to design for how a tool would be manufactured but, with AM, all of the limitations put upon you by subtractive methods of manufacturing are almost completely removed. Cimatron and 3DXpert are very powerful modelling programs that give me the design freedom to quickly make that transition to designing for additive. The complexity of geometry I design with Cimatron and 3DXpert would be inconceivable using anything else. Tailored design tools assist me in the construction of the parts themselves and a complete suite of conformal cooling design tools automates much of the design process, allowing me to focus more on designing a part for its function rather than its ease of manufacturing. 3DXpert then takes it a step further. Once I move into build preparation I again have full freedom to design my support structures with ease because of the huge number of options I have for deciding which type of support structure will work best.”
Drivers for the use of conformal cooling are often application-specific, he continued, “What we see are production needs relating to the requirements of a specific product driving the decision to use conformal cooling. In some cases, moulds that have AM components with conformal cooling strategies are delivering a 30-50% increase in production at the moulding machine making the plastic parts. This dramatic increase in productivity alone will end up returning 100% or more of the entire mould’s cost over the life cycle of the tool.”
In this collection, which is part one of a series representing some of John’s finest work, we present you with five articles that we think you will refer to time and again as you look to solve problems, cut cycle times and improve the quality of the parts you mold.
Reach a truly international audience that includes component manufacturers, end-users, industry suppliers, analysts, researchers and more.
Successfully starting or restarting an injection molding machine is less about ticking boxes on a rote checklist and more about individually assessing each processing scenario and its unique variables.
“Roughly 20% of the tools we are currently producing have some type of AM component. So far, all tooling we make with AM has conformal cooling. The other 80% of our conventionally manufactured moulds would all benefit from the use of conformal cooling in certain areas due to the shape of the geometry and the inability to get a cooling passage into the location needed. AM is slowly gaining traction in the moulding industry and it’s just a matter of time before all of the moulds that B&J Specialty builds will have AM parts with conformal cooling passages.”
Formnext Chicago is an industrial additive manufacturing expo taking place April 8-10, 2025 at McCormick Place in Chicago, Illinois. Formnext Chicago is the second in a series of Formnext events in the U.S. being produced by Mesago Messe Frankfurt, AMT – The Association For Manufacturing Technology, and Gardner Business Media (our publisher).
Lindemann concurs with Rauch in that there are two drivers behind the growth of AM for conformal cooling, stating, “Right now the momentum is coming from end-users who want better quality parts at reduced cycle times. The end cost may be such that it is an economical advantage even if the mould with conformal costs more to make initially. In some cases we see mould makers wanting to have the option of offering this technology to their customers, the end-users, as they see a need to be more competitive. With this they can, in some cases, also offer a quicker turnaround time in mould repair. Now they can print replacement cores overnight or in a few days, harden and finish them and have the mould back up and running quicker than with a traditional process. I have to again use the disclaimer ‘in some cases’ – wisdom dictates that each part or mould be considered on a case by case basis and it is not a fair statement to suggest this is a blanket statement for everything.”
Additive technology creates air pockets in film during orientation, cutting down on the amount of resin needed while boosting opacity, mechanical properties and recyclability.
Mini-disc golf is an offshoot of Disc Golf—with a size difference. The small discs require a much smaller course—two to three acres for nine holes, compared with the 40-50 acres required for a regular disc golf course. The rules are similar to golf: Instead of holes, the discs are thrown into 3-4 ft tall wire baskets. The typical hole length ranges from 150 to 700 ft, with different discs often used for drivers, mid-range play, and putting.
Metal AM offers the jewellery industry significant creative and commercial opportunities. One such opportunity is the production of platinum and ti...»
Thousands of people visit our Supplier Guide every day to source equipment and materials. Get in front of them with a free company profile.
According to Myers, the initial inventory of the new random- effects discs quickly sold out online and through social media. This prompted him to produce custom minis that can be hot-stamped with names and logos for use in promotions or as wedding favors. Now, he’s innovating further with 2.5-in. discs that can be used as tags for disc bags and soda-can toppers or “soda savers” as promotional items for disc-golf enthusiasts.
Metal AM magazine, published quarterly in digital and print formats, is read by a rapidly expanding international audience.
Sustainability continues to dominate new additives technology, but upping performance is also evident. Most of the new additives have been targeted to commodity resins and particularly polyolefins.
Across the show, sustainability ruled in new materials technology, from polyolefins and engineering resins to biobased materials.
9T Labs continues to enhance the efficiency of its technology, which produces composite parts with intentionally oriented fibers.
After successfully introducing a combined conference for moldmakers and injection molders in 2022, Plastics Technology and MoldMaking Technology are once again joining forces for a tooling/molding two-for-one.
This month’s resin pricing report includes PT’s quarterly check-in on select engineering resins, including nylon 6 and 66.
In this collection of articles, two of the industry’s foremost authorities on screw design — Jim Frankand and Mark Spalding — offer their sage advice on screw design...what works, what doesn’t, and what to look for when things start going wrong.
Seasoned plastics engineer Craig Myers, who heads up Zing Mini, has developed a new line of highly customized discs made possible by Carnival special-effects colorant from Ampacet Corp.
Mike Sepe has authored more than 25 ANTEC papers and more than 250 articles illustrating the importance of this interdisciplanary approach. In this collection, we present some of his best work during the years he has been contributing for Plastics Technology Magazine.
A collaboration between show organizer PLASTICS, recycler CPR and size reduction experts WEIMA and Conair recovered and recycled all production scrap at NPE2024.
In a time where sustainability is no longer just a buzzword, the food and beverage packaging industry is required to be at the forefront of this innovation. By adopting circular packaging processes and solutions, producers can meet regulatory requirements while also satisfying consumer demand and enhancing brand reputation. Join Husky to learn more about the broader implications of the circular economy — as well as how leading brands are leveraging this opportunity to reduce costs, increase design flexibility and boost product differentiation. Agenda: The cost and operational benefits of embracing circularity Key materials in circular packaging — including rPET and emerging bioplastics How to design a circular food and beverage package Strategies for selecting sustainable closures to future-proof packaging solutions Optimization and streamlining of production processes for enhanced efficiency How Husky Technologies can enable your sustainable success
While prices moved up for three of the five commodity resins, there was potential for a flat trajectory for the rest of the third quarter.
Mixed in among thought leaders from leading suppliers to injection molders and mold makers at the 2023 Molding and MoldMaking conferences will be molders and toolmakers themselves.
Learn about sustainable scrap reprocessing—this resource offers a deep dive into everything from granulator types and options, to service tips, videos and technical articles.
Join Wittmann for an engaging webinar on the transformative impact of manufacturing execution systems (MES) in the plastic injection molding industry. Discover how MES enhances production efficiency, quality control and real-time monitoring while also reducing downtime. It will explore the integration of MES with existing systems, emphasizing compliance and traceability for automotive and medical sectors. Learn about the latest advancements in IoT and AI technologies and how they drive innovation and continuous improvement in MES. Agenda: Overview of MES benefits What is MES? Definition, role and brief history Historical perspective and evolution Longevity and analytics Connectivity: importance, standards and integration Advantages of MES: efficiency, real-time data, traceability and cost savings Emerging technologies: IoT and AI in MES
With Carnival, Myers can infuse random brightly colored confetti into his discs, with each one distinctly different as the color disperses randomly in a swirl pattern. Batches might include multi-colored flecks within a clear- or solid-color disc, and Myers has also added Carnival colors to black discs. “Our disc golfers are crazy about colors and they love having unique discs,” says Myers.
With advocacy, communication and sustainability as three main pillars, Seaholm leads a trade association to NPE that ‘is more active today than we have ever been.’
When, how, what and why to automate — leading robotics suppliers and forward-thinking moldmakers will share their insights on automating manufacturing at collocated event.
Whilst conformal cooling opens up a world of new possibilties for tool designers and plastic injection moulders, it brings a new level of complexity and its own unique requirements. Rauch explained, “If a designer has good design skills and a good understanding of fluid dynamics, additively manufacturing conformal cooling passages can dramatically improve cycle times and also improve part quality. However, it’s not that simple. People tend to have tunnel vision and focus solely on designing an optimised conformal circuit, but one thing that will cause AM tooling with conformal passages to fail – and fail rather quickly – is the quality of water that is circulating inside. Most people don’t initially think about this being an issue, but you have to remember that most moulding facilities’ water systems consist of open-loop systems, with large cooling towers outside that carry the water through pipes to each moulding machine. Large amounts of debris and deposits build up which end up inside the mould waterlines. Eventually these build-ups cause catastrophic issues during the moulding process and you have to remove deposits.”
Zing Mini, an eight-year-old startup company in Fishers, Ind., headed by mini-disc golf enthusiast and seasoned plastics engineer Craig Myers, has expanded its lineup of injection molded mini discs to include not only more colorful ones but those for players who want something just for themselves.
Join Engel in exploring the future of battery molding technology. Discover advancements in thermoplastic composites for battery housings, innovative automation solutions and the latest in large-tonnage equipment designed for e-mobility — all with a focus on cost-efficient solutions. Agenda: Learn about cutting-edge thermoplastic composites for durable, sustainable and cost-efficient battery housings Explore advanced automation concepts for efficient and scalable production See the latest large-tonnage equipment and technology innovations for e-mobility solutions
Mold maintenance is critical, and with this collection of content we’ve bundled some of the very best advice we’ve published on repairing, maintaining, evaluating and even hanging molds on injection molding machines.
While the melting process does not provide perfect mixing, this study shows that mixing is indeed initiated during melting.
Plastics Technology’s Tech Days is back! Every Tuesday in October, a series of five online presentations will be given by industry supplier around the following topics: Injection Molding — New Technologies, Efficiencies Film Extrusion — New Technologies, Efficiencies Upstream/Downstream Operations Injection Molding — Sustainability Extrusion — Compounding Coming out of NPE2024, PT identified a variety of topics, technologies and trends that are driving and shaping the evolution of plastic products manufacturing — from recycling/recyclability and energy optimization to AI-based process control and automation implementation. PT Tech Days is designed to provide a robust, curated, accessible platform through which plastics professionals can explore these trends, have direct access to subject-matter experts and develop strategies for applying solutions in their operations.
Discover how artifical intelligence is revolutionizing plastics processing. Hear from industry experts on the future impact of AI on your operations and envision a fully interconnected plant.
In addition to providing extensive industry news coverage, Metal AM magazine is known for exclusive, in-depth articles and technical reports.
Lindemann cautioned, however, that,“there is still a resistance to embracing conformal cooling and this likely will remain for some time. Not all moulded parts are suited for conformal cooling. I once heard an AM representative tell of how he felt mistakes were made at the beginning when metal AM began taking on popularity. He explained about how mould makers especially were being told that this technology would replace them and what they were doing. That has proven far from the case. Good mould making and mould design practice remain essential to the industry and, if anything, AM has proved to be another tool in the tool kit to getting the overall job done well, and not a replacement for everything.”
“We have seen some injection moulders and mould makers experiment with conformal cooling in that they will take an existing job that they know well and then create a version for conformal cooled inserts to use as a comparison. In some cases the difference was dramatic and the practice of conformal cooling was adopted. That is not to say it is the best or only solution for every job. It is being investigated on a subjective basis. This trend has grown in recent years and seems to be continuing to grow,” added Lindemann.
Processors with sustainability goals or mandates have a number of ways to reach their goals. Biopolymers are among them.
According to Jarod Rauch, B&J Specialty’s Information Technology and 3D Printing Manager, whilst the demand for tooling with conformal cooling is seeing strong growth, there is also some resistance to such a transformative technology in what can be seen as a very traditional industry.
“We see the most resistance to AM with customers that know nothing about it. It’s a major change and people will normally fear change. I believe they dig their heels in because we are disrupting the status quo. The moulding industry is mostly based around a set of standards that have been in place for decades and now, when you tell a customer we are throwing most of the manufacturing limitations out the window because of what AM brings to the table, they find it very hard to believe. Education is the key. You need to educate your customers on what they can gain through AM – and also help them realise that if you want major improvements things just have to change. Once a customer can accept this, you will then be heading down the path of success with Additive Manufacturing,” explained Rauch.
FusionFX Carnival colorant from Ampacet infuses random brightly colored confetti into these distinctly different mini discs.
Concluding, Lindemann believes that increases in the production speed of AM systems, combined with a move towards increased automation, will accelerate the adoption of AM conformal cooling solutions. He stated, “Right now the direction is to make AM systems capable of manufacturing larger parts, using multiple lasers during the build process, and developing a greater degree of automation. Imagine a production floor environment dedicated just for metal AM. Conformal tooling can certainly benefit from these factors. From there, honestly, who knows where it can go? The future promises to be exciting in the least.”
The aim of this presentation is to guide you through the factors and the numbers that will help you determine if a robot is a smart investment for your application. Agenda: Why are you considering automation? What problems are you trying to solve? How and why automation can help Crunch the numbers and determine the ROI
Rauch stated, “Most customers are eager to listen but very hesitant to make the decision to use AM. Mostly because you are telling them you will be changing both the established processes and the materials used to make the AM parts. Customers like to hear about new technologies but don’t seem to like it when they hear they will have to change. My best tools to convince them that this change is for the best are our own case studies, mould flow simulations and CFD analytical tools. These allow us to show things in black and white for them, so they can see first-hand what could be achieved if they decide to go down the path of change. After seeing the results, customers often think it’s too good to be true.”
Myers has more than 25 years of industry experience in automotive, medical, and consumer markets. For his latest innovation, he opted for the Carnival special-effects colorant from Ampacet Corp., Tarrytown, N.Y. This masterbatch is one among the FusionFX line of masterbatch four-color palettes for polyolefin consumer products, launched in late 2015, that use proprietary technology to produce random flow of color effects.
technotrans says climate protection, energy efficiency and customization will be key discussion topics at PTXPO as it displays its protemp flow 6 ultrasonic eco and the teco cs 90t 9.1 TCUs.
The free to access Metal Additive Manufacturing magazine archive offers unparalleled insight into the world of metal Additive Manufacturing from a commercial and technological perspective through:
The frenzy of media attention surrounding Artificial Intelligence (AI) dwarfs the past hype surrounding Additive Manufacturing (AM). Whether you lo...»
Despite price increase nominations going into second quarter, it appeared there was potential for generally flat pricing with the exception of a major downward correction for PP.
Providing 3D Systems’ perspective on the broader industrial use of conformal cooling, David Lindemann, Cimatron Application Engineer at 3D Systems, told Metal AM magazine, “The driving forces seem to be coming from automotive, aerospace, and medical. The reason is mostly to improve overall part quality and reduce warpage, this in turn improves part fit and functionality. As previously stated, another crucial reason is to reduce the cooling cycle time and thus reduce overall part cost.”
Plastics processors are finding applications for 3D printing around the plant and across the supply chain. Here are 8 examples to look for at NPE2024.
Ultradent's entry of its Umbrella cheek retractor took home the awards for Technical Sophistication and Achievement in Economics and Efficiency at PTXPO.
GETTING A QUOTE WITH LK-MOULD IS FREE AND SIMPLE.
FIND MORE OF OUR SERVICES:
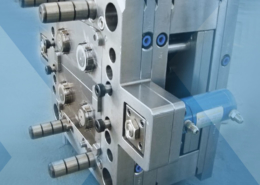
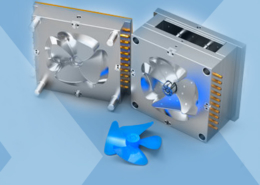
Plastic Molding

Rapid Prototyping
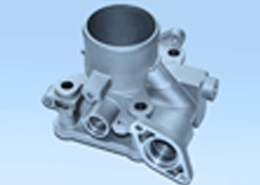
Pressure Die Casting
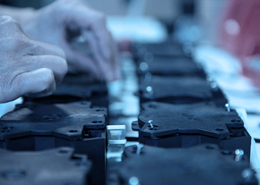
Parts Assembly
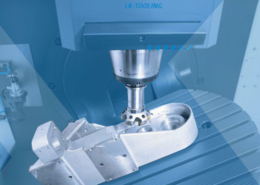