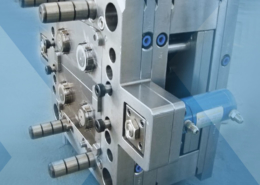
Ford is recycling McDonald’s coffee waste into car parts - mcdonalds plastic mol
Author:gly Date: 2024-09-30
Well, I know how to use the right side of my brain. A lot of people in the business world have a tendency to use the left side, I think, but the right is just as important. It allows me to see certain problems multidimensionally, approach issues from a different angle or perspective and find new creative solutions. I’m a person who can give ideas just by looking at things. I'm not an engineer, and have no experience in a plastic molding factory but I can make decisions and give ideas of how to look at things differently. I’m trying to change the culture for new development in the future. If we can’t make it happen, the future is going to be much more difficult than it needs to be. We don’t need to be huge innovators like Apple, but we can create micro innovations. Kaizen to me, is micro innovation. There’s an expression in Japanese, “if the dust gathers, it becomes like a mountain”. I really believe that small things can build to something much greater.
He decided to keep the records for every product, even scribbling them on a piece of paper. It was a great way to leave the process of solution making, not just the end result. When it comes to plastic molding we want to avoid any kind of defect, so even when we are using customer designs we have a library of information of what kind of things have worked and what kind of problems we have encountered in the past.
We just started discussion with an American company about a potential international partnership for the production of specimen holders for TEM (trans-electron microscopy). It’s quite an interesting project as the key device of that microscopy can be created with our mold making technology. So we match up with them very well. They luckily have almost the exact kind of machine tools that we’re using. They share many of our views. It’s quite nice to hear American people not just talking about the business performance but also talking about the machine tools, expertise and passion for the work.
First of all, our defect rate is about 1 ppm (parts per million). We carry 3000 different items every month and our defect rate is extremely low, which is very nice for us, but nice for our customers too. They are much more at ease to accept our products. Some clients don’t even check, they just go directly into their lines. We also try to reduce scrap materials and recycle. We have many ideas about creating our own new product using recycled plastic and making it in house. Reducing costs is also very important. Because in the 1980s and 90s we enjoyed a very great market because we didn’t have many competitors but now reducing costs has become a really big theme for us to stay competitive. For example we have two factories that just merged this year as a cost cutting measure. It’s much easier now to manage manpower and costs. I am expecting to increase our productivity by 10-15%. We also had a groupware server which has been really good for us. We’re also trying to create more opportunities for education, so that people can actually learn here not just by working but by going out for seminars and through our own teaching programs. Because we are so focused on small parts and have been for so long, there is so much more for us to learn about all the different parts of plastic molding as an industry. We’ve also started English courses here and are asking managers to join societies like scientific societies, which has been very effective. We’ve put a lot of effort into our facilities to maintain their condition.
Well that is a long story. It wasn’t easy at all for us to start from scratch. It was a big challenge and took us more than 10 years to do that. I thought, by utilizing this technology to create plastic molds, maybe we can serve society in many ways and create solutions for many people. This is very difficult to digitize because the material is not a digital material. Air conditioning is very critical, we have to maintain a temperature of 23° C plus or minus .05° C, in order to maintain the precision of machining. Plastic molding in general is not as precise compared to what we do. Usually, mold making technologies advance, and plastic mold making follows. We are still struggling to duplicate perfectly, there are so many elements that can create defects.
Juken Kogyo fully leverages its expertise in micro- and nano-precision technologies to produce plastic components, offering micro-gram (one millionth of a gram) gears and nano-machined products through its precision injection molding. Founded in 1965, today many of the company’s plastic parts are used for various products that support the Japanese manufacturing industry, whilst also supplying micro parts to manufacturers all over the world. We speak with president, Naoki Matsuura, to learn more about how Juken Kogyo contributes to key sectors of the economy that require such meticulousness and quality, with precision molding technology, as well as his insight into the plastics manufacturing industry.
My father had a problem when he was maybe 30, 35 years old. He had a dispute with his customers. Who is causing the trouble? The designer, the mold maker, molders, producers? He wanted to find a way to avoid such troubles, almost like an insurance. With our Juken system, when customers call us we can readily access technical information for them about whatever products of ours they may be using. We can then discuss and find solutions that we otherwise may not be able to.
In the last 25 years we have seen the rise of cheaper competitors such as China, South Korea, and Taiwan replicating the Japanese monozukuri process and doing so at a cheaper labor cost. They have been providing the world with cheaper products at the expense of quality. Yet despite this stiff competition Japan has been able to maintain its leadership as it relates to advanced machining, and niche fields. Can you please tell us about the essence of the Japanese monozukuri? How are companies such as yourselves able to compete internationally despite such stiff competition?
It’s been wonderful. IT technology development has just been wonderful. Combining traditional methods with new technology has been really very good. This way we can pick the best of each to make much better systems and solutions. For example, we do have a physical filing system, but we also have a database. Because many of our products are so small, the corresponding physical file often actually contains the product in question. It’s more than just data. We have been using data for checking or reviewing, but it's time to start using it as prospective tools as well, even for SMEs.
We are now in the 4th industrial revolution and are seeing the rise of new innovative technology such as IoT, AI, and Big Data. As a company that specializes in the IT field, can you please tell us what the impact of these new technologies has been on your company and how you are adapting them to your products?
The Worldfolio provides business, industrial and financial news about global economies, with a focus on understanding them from within.
In 1985 you took your first steps to go overseas. You went to Singapore, China, India, Switzerland, Thailand, Taiwan, S. Korea, I could go on. In our research we found that you expanded through joint ventures. Can you tell us about your international strategy? What benefits have joint ventures brought to your company?
A new low-friction, high-hardness coating is poised to expand the range of surface treatments to help tooling stand up to tough moulding challenges. The new diamond-like coating can increase the mould service life by up to 10 times compared to the state of the art.
It’s not so much a strategy but more of a vision I’m looking to not just be a parts supplier but to be a unit supplier. I’d like to have an assembly line, actually we’ve already started. We’re making some catheter key parts, and are also assembling handles and things like that. So that’s the direction we’re headed in.
You’ve mentioned the necessity to gather information. In preparing our report we’ve interviewed many companies and they’ve all agreed on one thing, that research and development plays a major role for Japanese companies. In fact the R&D expenditure for 2019 in Japan stood at 19 trillion yen which shows that Japanese companies are investing massively to be competitive both domestically and globally. We are also seeing a trend where Japanese are shifting overseas to find partners for co-creation and innovation. Can you please tell us about your R&D capabilities? In the future are you looking to find any co-creation or joint venture partners for the gathering or sharing of information overseas?
You became the CEO in 2015 and are the 2nd generation as your father started the company as you told us. In the distant future when you hand over the company to the next generation, what legacy or vision to leave behind to your successor?
That’s a good question, and it's something I've been thinking about a lot recently. What is good for the people who work here? How well can they make a living, have a better quality of life, that’s the key point of what to do next for me. At this moment I haven’t decided anything yet, there are so many choices going forward. A company can choose the future but people as well. I used to think that all people want to be promoted but many don't. Some people just want to stay as they are and that’s their choice. I think it’s very important to provide choices for the people who work here. I want to leave a legacy of sincerity, gratitude, and the idea that Japanese Chuken Kigyo can give people the power to make choices about their future.
Logging out of EU Login will log you out of any other services that use your EU Login account. Use the CORDIS log out button to remain logged in on other services.
We supply intraocular lens molds as well. Intraocular lenses are basically the implanting lens’ for cataract surgery. As my father got old and he started losing his sight he had to change his lens and it changed his life. He came to me and told me, you did a great job. It was great encouragement, a big payoff and a great joy of working. It connects back to your first question, as to how monozukuri feels, the mentality, it’s not just the money, but the value to society you create and the role you can play to serve people. My father’s comment was really fulfilling because we spent 10 years getting into that market and it was very tough. No blueprint, no friends, and were still able to break through.
First of all, there is no strategy. It’s quite interesting because my father never had a vision to grow his business too big, he rather wanted to enjoy the work. And so do I. I really enjoy working here. He was very excited about having foreign friends, and real colleagues, who are the people he could trust and do business with. For those local business owners, it was much easier for them to start their own businesses and to get involved with us, so joint ventures happened very naturally. We are still good friends but right now we don’t have too much contact with former joint venture partners.
Right now I'm researching if there’s anything for agriculture. Biodegradable plastic is a big thing that I’ve been looking at for more than 10 years but it’s not really a good application for us at the moment. In the future plastic will have to be biodegradable, especially for agriculture. Believe it or not we actually started as an agriculture business. My father started with making small planting pots and since then we had to change our direction to focus on chemical parts, and then even smaller parts which led him to create his own molding machines since no one had molds small enough for the parts he wanted to make.
This is a machine translation provided by the European Commission’s eTranslation service to help you understand this page. Please read the conditions of use.
Permalink: https://cordis.europa.eu/article/id/418344-diamond-like-carbon-coating-offers-relief-to-plastic-injection-moulds
We know that injection molding and 3D printing are standard when it comes to plastic parts but there are some limitations. They cannot go under 20 microns in terms of resolution. To solve this problem we have nano injection molding that allows the creation of nanometer scales such as your company is able to provide, up to 0.5 microns. We know that your company Juken Kogyo provides nanometer ultra precision machinery and also nano technology. Can you please tell us about the synergy you are able to create between the machinery and the technology, and how you are able to provide solutions to your customers when it comes to nano technologies?
Telephones, PC parts, toys, electrical plugs, and other everyday products like shoes and pens are made with plastics using a process called injection moulding. The technology can produce identical parts at high volumes at a low cost per part. However, its start-up cost is relatively high, mainly because custom tooling is needed. An injection mould can cost anywhere between EUR 100 000 and EUR 300 000, depending on its complexity, material and accuracy.
When we interviewed the president of Nissei Plastic Industrial, which is one of the leading companies in injection molding, Mr.Yoda san, he mentioned three main trends affecting the plastic manufacturing sector. The first was, as you’ve mentioned, the increased popularity of sustainable products. The second was surging demand for lighter materials, and the third was cost efficiency. As a company that has been involved with injection molding for the past 50 years can you please tell us how you’re adapting to these trends?
A key attribute of the diamond-like carbon coatings is the ability to resist wear by lowering the friction between sliding surfaces. This largely eliminates the need for surface lubrication and post-finishing, which are deemed primary sources of pollutant releases to the atmosphere for certain industries such as pharmaceutical and food. The coatings are applied using a physical vapour deposition process called magnetron sputtering at temperatures as low as 180 °C. Due to this advanced deposition process, the diamond-like carbon coatings can maintain a very thin, uniform finish (1-5 μm) over the entire mould independently of its geometry. “cleanMOULD’s novel coatings optimise both surface hardness and lubricity to minimise the impact of fretting,” notes Hvam. The high hardness of the newly demonstrated diamond-like carbon coatings, which are 8 times harder compared to other coatings, allows the surfaces to become more resistant to scratches that occur during operation. It goes without saying that the absence of oil lubricants makes mould cleaning much easier: it only requires applying ethanol to a cloth for less than 10 minutes. cleanMOULD’s ‘mould breaking’ has the potential to become a key enabling technology for the entire plastics industry. Overall, the return on investment for cleanMOULD users is expected to be over 20 times the expected coating costs, thus providing a compelling value proposition. Pilot-test results demonstrated a sixfold decrease in the maintenance interval compared to state-of-the-art coatings. No fretting corrosion has been observed on any coated moulds. What’s more, “cleanMOULD’s coating demonstrated a decrease in the moulding cycle time of screw lids from 40 to 36 seconds, which is equivalent to an 11 % increase in productivity,” concludes Hvam.
That’s a very difficult question because the answer is kind of broad. From my point of view, the mentality of professionalism or expertise is the same across all sectors or occupations. When it comes to plastic molding, I don’t really consider plastic molding manufacturing as much as service providing. When it comes to providing a service, the product must be very reliable, with strong quality control. We have spent many years developing our system and are always trying to be better than perfect. To go beyond being a placeholder and totally exceed expectations. This attitude is the direction of our monozukuri.
Prolonging tooling service life is of paramount importance for any moulding project since downtime for repairs jeopardises profit margins. According to estimates, around EUR 10 billion are spent each year for maintenance operations worldwide. During the moulding process, the friction forces developed between the closing surface and those contacting the injected plastic largely account for the damage caused to the surfaces. Ultimately, the mould needs to be scrapped. Put together, these significantly affect the mould’s service life. The EU-funded cleanMOULD project demonstrated novel coatings based on a multilayer diamond-like carbon formulation that prolong the life of injection moulding tools, offering corrosion protection, reduced wear and resistance to friction. “Importantly, our novel coating solutions increase mould performance and extend its operation before the need to take it out of service for preventive maintenance,” reports project coordinator Michael Hvam.
We don’t have a particular R&D section. I wish I had one, but it’s difficult for an SME like us. I’ve changed our approach to be project based. If something interesting comes up, I call some people and say, “let’s do this project together” and see what happens. Even if we don’t achieve our goal we are still able to gather lots of useful information. For example the clic disk for a (compact linear collider of CERN), is an accelerator part. There are only 5 or 6 companies in the world that are qualified to produce these. We like to challenge that. It can be very fun and exciting to join a program like that. We would never be able to have this kind of experience just by making molds, because it’s a scientific project so we can work with actual scientists which is inspiring and enriches our own work. This may help solve all of our energy problems. Maybe not for our generations, but for the future.
GETTING A QUOTE WITH LK-MOULD IS FREE AND SIMPLE.
FIND MORE OF OUR SERVICES:
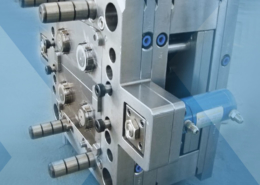
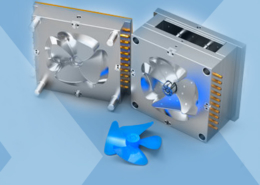
Plastic Molding

Rapid Prototyping
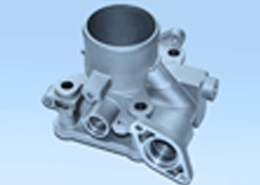
Pressure Die Casting
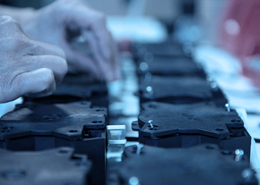
Parts Assembly
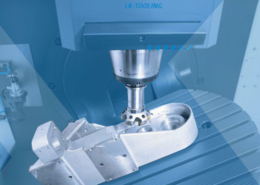