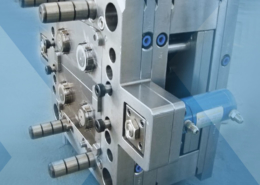
Exploring the World of Plastic Injection Parts
Author:gly Date: 2024-06-08
Introduction
Plastic injection parts represent a cornerstone in modern manufacturing, offering unparalleled versatility, precision, and cost-effectiveness in the production of a wide range of components. This article aims to unravel the intricacies of plastic injection parts, providing insights into their processes, applications, benefits, and future prospects.
Understanding Plastic Injection Parts
Plastic injection parts are manufactured using the plastic injection molding process, which involves injecting molten plastic material into a mold cavity under high pressure. Once the material cools and solidifies, it takes the shape of the mold cavity, resulting in a precise and detailed component. This method is widely employed due to its ability to produce complex geometries, tight tolerances, and high-volume production runs with consistency and efficiency.
The versatility of plastic injection parts makes them suitable for a myriad of applications across industries, ranging from automotive and aerospace to electronics, medical devices, and consumer goods.
Applications Across Industries
Plastic injection parts find extensive applications in various industries, each with unique requirements and specifications. In the automotive sector, plastic injection parts are utilized for interior and exterior components such as dashboards, bumpers, door panels, and trim. The lightweight nature of plastic components helps improve fuel efficiency and reduce vehicle weight, contributing to sustainability and cost-effectiveness.
Similarly, in the electronics industry, plastic injection parts are used for enclosures, housings, connectors, and structural components in devices such as smartphones, laptops, and appliances. The ability to integrate features such as snap fits, threads, and intricate details makes plastic injection parts ideal for electronic applications requiring precision and durability.
Advantages and Challenges
Plastic injection parts offer several advantages over other manufacturing methods, including high production efficiency, design flexibility, material versatility, and cost-effectiveness for large-scale production runs. Additionally, the ability to utilize a wide range of thermoplastic materials with varying properties allows manufacturers to tailor components to specific performance requirements, such as strength, flexibility, or heat resistance.
However, plastic injection molding also presents challenges such as tooling costs, material selection, and process optimization. Addressing these challenges requires careful consideration of factors such as mold design, material properties, processing parameters, and quality control measures to ensure optimal results.
Technological Advancements and Future Directions
Recent technological advancements in plastic injection molding have focused on enhancing process efficiency, reducing cycle times, and improving part quality. Innovations such as advanced mold designs, hot runner systems, and in-mold decoration techniques have enabled manufacturers to achieve higher productivity and greater design freedom.
Looking ahead, the future of plastic injection parts is poised for further innovation and development. Research efforts are underway to explore new materials, optimize processing techniques, and integrate digital technologies such as simulation software and IoT-enabled equipment to enhance process efficiency, reduce waste, and improve product quality.
Conclusion
In conclusion, plastic injection parts play a vital role in modern manufacturing, offering unmatched versatility, precision, and cost-effectiveness in producing a wide range of components across industries. Despite facing challenges, continuous innovation and technological advancements ensure that plastic injection parts remain at the forefront of product development and manufacturing. As industries evolve and demand for customized, high-quality components continues to grow, the role of plastic injection parts in accelerating innovation and driving competitive advantage will only become more significant. By embracing innovation, collaboration, and continuous improvement, manufacturers can unlock the full potential of plastic injection parts and shape the future of manufacturing.
GETTING A QUOTE WITH LK-MOULD IS FREE AND SIMPLE.
FIND MORE OF OUR SERVICES:
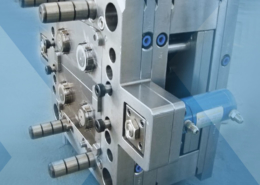
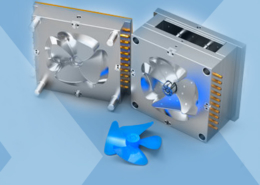
Plastic Molding

Rapid Prototyping
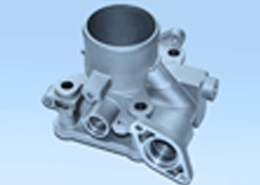
Pressure Die Casting
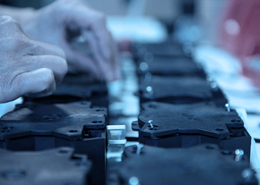
Parts Assembly
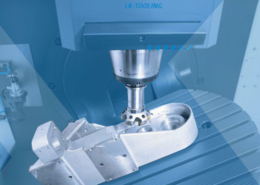