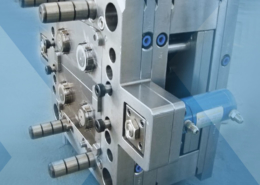
Flexible composite platform for multiple aircraft bracket projects takes
Author:gly Date: 2024-09-30
Up to now, these properties have been exploited mainly in extruded film and sheet. For injection molders, COCs offer glass-like transparency and excellent barrier to water vapor with high HDT and good electrical properties. COCs are amorphous polymers with high modulus and surface hardness. Chemically, they resist hydrolytic degradation, aqueous acids and bases, and most polar and oxygenated solvents. In injection molding, they provide high precision, and they flow well to fill complex, thin-walled parts with low shrinkage and warpage. Because COCs’ stiffness is 25% greater than that of polycarbonate, they lend themselves to molding thinner walls.
While prices moved up for three of the five commodity resins, there was potential for a flat trajectory for the rest of the third quarter.
While the major correction in PP prices was finally underway, generally stable pricing was anticipated for the other four commodity resins.
Mold maintenance is critical, and with this collection of content we’ve bundled some of the very best advice we’ve published on repairing, maintaining, evaluating and even hanging molds on injection molding machines.
Ticona introduced Topas COCs five years ago as a lower-cost alternative to other COC materials produced by non-metallocene technologies. The first commercial plant (66 million lb/yr) started up in 2000. Metallocene-catalyzed COCs offer excellent optical properties, high flow, and ultra-low moisture absorption. In addition, their density is 3% lower than that of polystyrene and 15% less than polycarbonate and acrylics.
Plastics Technology’s Tech Days is back! Every Tuesday in October, a series of five online presentations will be given by industry supplier around the following topics: Injection Molding — New Technologies, Efficiencies Film Extrusion — New Technologies, Efficiencies Upstream/Downstream Operations Injection Molding — Sustainability Extrusion — Compounding Coming out of NPE2024, PT identified a variety of topics, technologies and trends that are driving and shaping the evolution of plastic products manufacturing — from recycling/recyclability and energy optimization to AI-based process control and automation implementation. PT Tech Days is designed to provide a robust, curated, accessible platform through which plastics professionals can explore these trends, have direct access to subject-matter experts and develop strategies for applying solutions in their operations.
So far, COCs have been molded almost exclusively on reciprocating-screw injection presses. Though there is little industry experience with COCs in two-stage screw/ plunger systems, their thermal stability should be adequate for use in such a system.
Post-molding shrinkage of COCs typically falls between 0.4% and 0.7%. Shrinkage is greater with higher Tg grades and tends toward lower values as cavity pressure rises. Shrinkage in the flow direction is only slightly greater than that in the transverse direction, so very flat parts can be molded. COCs’ good stiffness and flow means that parts can have walls down to 1 mm or less.
Editor in chief of PlasticsToday since 2015, Norbert Sparrow has more than 30 years of editorial experience in business-to-business media. He studied journalism at the Centre Universitaire d'Etudes du Journalisme in Strasbourg, France, where he earned a master's degree.
A medical in-mold labeling (IML) application will be showcased by Arburg at NPE2024. First presented at Fakuma in 2023 as a proof of concept, the compact turnkey production cell anchored by Arburg’s electric Allrounder 520 A "Ultimate" press will produce a centrifuge tube with label on the NPE show floor.
Optical parts are best processed in machines with higher screw L/D ratios, which tend to produce less splay and improve recovery times with lubricated grades. Barrels do not need venting because of the resin’s negligible water absorption.
This Knowledge Center provides an overview of the considerations needed to understand the purchase, operation, and maintenance of a process cooling system.
Normal fill times are about 1 to 2 sec and cycle times typically extend from 10 sec for small, thin parts to 360 sec for parts 0.5-in. to 1-in. thick. Fill times for optical parts may be extended to 5 or 10 sec when using a mold temperature within 50° F of Tg.
IML is standard for packaging products, but the process is rarely used in medical manufacturing, said Arburg in its announcment. The concept is all the more compelling because both the tube and label are made of polypropylene, thus promoting sustainability and adding value for customers in the pharmaceutical and medical sectors.
Thousands of people visit our Supplier Guide every day to source equipment and materials. Get in front of them with a free company profile.
The electric Allrounder 520 A "Ultimate" is designed for ISO Class 7 cleanroom use and has a clamping force of 165 tons (1,500 kN). The ready-to-use 15-ml PP tubes are produced in an eight-cavity mold from Kebo at an approximate 10-second cycle time. Servo-electric drives ensure precise and reproducible mold positioning in the press, and a label adjustment head from Beck ensures that the labels are precisely aligned and applied. An integrated camera system from Intravis visually inspects the finished parts in real time. In a real application, the tubes could also be screwed together and packaged in tubular bags in the production cell, added Arburg.
While the melting process does not provide perfect mixing, this study shows that mixing is indeed initiated during melting.
A lot has been learned in the last few years about how to injection mold COC materials for best results in sensitive medical and optical applications. Micro-vial holders, syringe bodies, and lenses are just now making a commercial impact
Introduced by Zeiger and Spark Industries at the PTXPO, the nozzle is designed for maximum heat transfer and uniformity with a continuous taper for self cleaning.
Take a deep dive into all of the various aspects of part quoting to ensure you’ve got all the bases—as in costs—covered before preparing your customer’s quote for services.
A scale on the scratch-resistant label indicates the exact fill level, which can be relevant for insulin pen and medical measuring cup applications, for example.
COC parts emerge from the mold with smooth surfaces and need little or no deflashing or finishing. They have a soft surface until they cool completely, so just-molded parts should be handled carefully. If possible, degate COC parts when they are still warm. For degating cold parts, use a band saw because snipping can cause fractures.
Mold temperature for COCs should not be more than 90° F below the Tg for lower-temperature grades and not more than 54° below Tg for high-heat grades. Warmer molds minimize silver streaks, decrease molded-in stresses, and preserve clarity. Because COCs set up rapidly and their viscosity rises steeply as they cool towards Tg, molds should be hot enough to minimize weld-line formation.
COC parts can be solvent bonded using a 15% solution of COC in cyclohexane, heptane, or other aliphatic solvent. Some commercial adhesives, such as those based on polyurethane, also work well with this polymer.
When, how, what and why to automate — leading robotics suppliers and forward-thinking moldmakers will share their insights on automating manufacturing at collocated event.
Second quarter started with price hikes in PE and the four volume engineering resins, but relatively stable pricing was largely expected by the quarter’s end.
This new family of clear engineering thermoplastics made its first big splash in extrusion, but now injection molders are learning how to process these amorphous resins into optical and medical parts.
Across all process types, sustainability was a big theme at NPE2024. But there was plenty to see in automation and artificial intelligence as well.
Join KraussMaffei for an insightful webinar designed for industry professionals, engineers and anyone interested in the manufacturing processes of PVC pipes. This session will provide a comprehensive understanding of the technology behind the production of high-quality PVC pipes: from raw material preparation to final product testing. Agenda: Introduction to PVC extrusion: overview of the basic principles of PVC pipe extrusion — including the process of melting and shaping PVC resin into pipe forms Equipment and machinery: detailed explanation of the key equipment involved — such as extruders, dies and cooling systems — and their roles in the extrusion process Process parameters: insight into the critical process parameters like temperature, pressure and cooling rates that influence the quality and consistency of the final PVC pipes Energy efficiency: examination of ways to save material and energy use when extruding PVC pipe products
Draft is affected by part length and must be higher with textured surfaces. Molders switching to COC from a material with greater shrinkage should modify the tool so it has sufficient draft for part release. If the tool was previously used for polycarbonate or acrylic, it can typically run COC without any modification.
Screw speed is usually in the moderate-to-fast range (50 to 150 rpm), depending on screw diameter and barrel size. The smaller the screw, the higher the rpm needed. Take care to homogenize the melt well, but without undue shear heating.
COCs absorb almost no water and do not need drying. If the resin does become wet, surface water can be driven off by about 2 hr of heating at 54° F below the resin’s HDT.
Moldmaker Kebo, in-mold labeling specialist MCC Verstraete, automation developer Beck, and vision system supplier Intravis contributed to the joint IML project.
A lot has been learned in the last few years about how to injection mold COC materials for best results in sensitive medical and optical applications. Micro-vial holders, syringe bodies, and lenses are just now making a commercial impact.
Tools can be made of standard mold steels but should be polished well to eliminate surface imperfections. This is vital for optical applications, where a finish down to a quarter of a wavelength of light may be required.
When feeding COC pellets, allow them to warm up in the feed throat to 45° to 54° below the HDT by throttling back on the cooling water. This makes the pellets less brittle and therefore less likely to generate fines that can affect part homogeneity.
The Plastics Industry Association (PLASTICS) has released final figures for NPE2024: The Plastics Show (May 6-10; Orlando) that officially make it the largest ever NPE in several key metrics.
technotrans says climate protection, energy efficiency and customization will be key discussion topics at PTXPO as it displays its protemp flow 6 ultrasonic eco and the teco cs 90t 9.1 TCUs.
August 29-30 in Minneapolis all things injection molding and moldmaking will be happening at the Hyatt Regency — check out who’s speaking on what topics today.
Despite price increase nominations going into second quarter, it appeared there was potential for generally flat pricing with the exception of a major downward correction for PP.
COCs are usually molded on conventional machines having general-purpose, low-compression screws with ratios of 2.2:1 to 2.5:1. Screws are typically shallow single-flighted or barrier models made from standard tool steels. The screw should homogenize the melt gently because excessive shear heating can cause yellowing and optical inhomogeneity. A high-compression screw can generate too much shear and even shatter the pellets.
In this collection, which is part one of a series representing some of John’s finest work, we present you with five articles that we think you will refer to time and again as you look to solve problems, cut cycle times and improve the quality of the parts you mold.
Cylinder temperatures should be matched to the Tg of the grade used (see table). Melt temperatures are typically 200° to 215° F above the Tg and usually fall between 464 F and 572 F. (Molders tend to run at the high end of this range.)
Processors with sustainability goals or mandates have a number of ways to reach their goals. Biopolymers are among them.
Coverage of single-use plastics can be both misleading and demoralizing. Here are 10 tips for changing the perception of the plastics industry at your company and in your community.
Say “manufacturing automation” and thoughts immediately go to the shop floor and specialized production equipment, robotics and material handling systems. But there is another realm of possible automation — the front office.
Don’t assume you know everything there is to know about PE because it’s been around so long. Here is yet another example of how the performance of PE is influenced by molecular weight and density.
Mike Sepe has authored more than 25 ANTEC papers and more than 250 articles illustrating the importance of this interdisciplanary approach. In this collection, we present some of his best work during the years he has been contributing for Plastics Technology Magazine.
(2021 Update: Topas COC was developed in the 1990s by Hoechst Celanese, and initially marketed by Ticona. After a couple of reorganizations and ownership changes, Topas COC is today manufactured by Topas Advanced Polymers GmbH, a company of the Polyplastics Group, and outside EMEA is sold by Polyplastics. The company will soon be adding a second plant for the manufacture of COC, thanks to growing global demand in medical and packaging applications.)
Multiple speakers at Molding 2023 will address the ways simulation can impact material substitution decisions, process profitability and simplification of mold design.
Plastics Technology covers technical and business Information for Plastics Processors in Injection Molding, Extrusion, Blow Molding, Plastic Additives, Compounding, Plastic Materials, and Resin Pricing. About Us
Discover how artifical intelligence is revolutionizing plastics processing. Hear from industry experts on the future impact of AI on your operations and envision a fully interconnected plant.
Additive technology creates air pockets in film during orientation, cutting down on the amount of resin needed while boosting opacity, mechanical properties and recyclability.
The IML print-to-cut distance is only around 0.08 in. (0.2 mm) for the centrifuge tube application. With a wall thickness of only 57 micrometers, the labels must be precisely positioned in the mold cavities, and equally precisely aligned and applied. A label adjustment head equalizes the manufacturing tolerance to a few hundredths, which is an important requirement for functionality and significantly reduces quality fluctuations and rejects.
Successfully starting or restarting an injection molding machine is less about ticking boxes on a rote checklist and more about individually assessing each processing scenario and its unique variables.
COCs can be used with all types of nozzles, although free-flow, open types are best because they allow for easier sprue pullout. The resin also can be used with nearly all gating styles. Fan gates are recommended because of their relatively low shear. Gate size should be generous enough to prevent excessive shear heating or premature freeze-off. Gating preferably should be into the thick end of a part and gate diameter should be at least 60% of the wall thickness. COCs with Tg above about 280 F should be run on oil-heated tooling. Grades with a lower Tg can use a circulating hot-water system for mold-temperature control.
NPE2024 visitors can see the system in operation at booth W3743. The event returns to the Orange County Convention Center in Orlando, FL, on May 6 to 10.
When molding optical parts, use a high mold temperature and keep injection speed as fast as possible to prevent flow marks. On the other hand, slower injection may be needed to overcome sinks, voids, and birefringence in thick optical parts. Some suck-back may be needed to prevent nozzle drool. Higher backpressure—as much as half of a machine’s maximum pressure—helps improve optical properties but should not be so high as to yellow the part or hinder screw retraction. Low holding times and pressures are also usually good for optical parts. Holding time varies from 30 to 60 sec, depending on part thickness. Cooling time can last from 60 to 120 sec. Longer cooling time helps reduce stress level in the part. Total cycle time for optical parts is typically 2 to 5 min.
Mixed in among thought leaders from leading suppliers to injection molders and mold makers at the 2023 Molding and MoldMaking conferences will be molders and toolmakers themselves.
Join Engel in exploring the future of battery molding technology. Discover advancements in thermoplastic composites for battery housings, innovative automation solutions and the latest in large-tonnage equipment designed for e-mobility — all with a focus on cost-efficient solutions. Agenda: Learn about cutting-edge thermoplastic composites for durable, sustainable and cost-efficient battery housings Explore advanced automation concepts for efficient and scalable production See the latest large-tonnage equipment and technology innovations for e-mobility solutions
In a time where sustainability is no longer just a buzzword, the food and beverage packaging industry is required to be at the forefront of this innovation. By adopting circular packaging processes and solutions, producers can meet regulatory requirements while also satisfying consumer demand and enhancing brand reputation. Join Husky to learn more about the broader implications of the circular economy — as well as how leading brands are leveraging this opportunity to reduce costs, increase design flexibility and boost product differentiation. Agenda: The cost and operational benefits of embracing circularity Key materials in circular packaging — including rPET and emerging bioplastics How to design a circular food and beverage package Strategies for selecting sustainable closures to future-proof packaging solutions Optimization and streamlining of production processes for enhanced efficiency How Husky Technologies can enable your sustainable success
Residual stress in parts can be limited by increasing injection speed in steps and by using mold temperatures as close to the resin’s Tg as possible. For low-stress parts, you should also avoid overpacking and long hold times. Try reducing holding pressure in stages to between 4000 and 7000 psi.
COCs can be finished by printing, coating, and metalizing as well as joining and machining. COCs are nonpolar materials, so relatively few materials stick to them. Before a COC part can be printed or coated, it needs corona or plasma pretreatment to functionalize its surface and allow bonds to form. Metal coatings are an exception: Vacuum-deposited aluminum, chromium, silver, nickel, and other metals adhere well to COCs without pretreatment.
The first substantial wave of molded applications for the Topas family of metallocene-catalyzed cyclic olefin copolymers (COCs) is just now arriving on the market. Some limited molding activity with these new transparent engineering thermoplastics dates back to 1969, but injection molded (and injection-blow molded) medical and optical applications are only now starting to appear in force. Emerging uses include optical lenses, light guides, microtiter plates, syringe bodies, tubing connectors, catheter manifolds, and lids.
In this three-part collection, veteran molder and moldmaker Jim Fattori brings to bear his 40+ years of on-the-job experience and provides molders his “from the trenches” perspective on on the why, where and how of venting injection molds. Take the trial-and-error out of the molding venting process.
Gifted with extraordinary technical know how and an authoritative yet plain English writing style, in this collection of articles Fattori offers his insights on a variety of molding-related topics that are bound to make your days on the production floor go a little bit better.
A temperature-sensitive element can be included that monitors interruptions in the cold chain. If the temperature of the filled tube exceeds 7°C, for example, the thermo-chromic printing ink irreversibly changes in appearance.
Ultradent's entry of its Umbrella cheek retractor took home the awards for Technical Sophistication and Achievement in Economics and Efficiency at PTXPO.
While prices moved up for three of the five commodity resins, there was potential for a flat trajectory for the rest of the third quarter.
Implementing a production monitoring system as the foundation of a ‘smart factory’ is about integrating people with new technology as much as it is about integrating machines and computers. Here are tips from a company that has gone through the process.
In this collection of content, we provide expert advice on welding from some of the leading authorities in the field, with tips on such matters as controls, as well as insights on how to solve common problems in welding.
Injection molding grades of COC from Ticona have a glass-transition temperature (Tg) between 70 and 185 C (158 to 365 F). As a result, their heat-deflection temperature (HDT) ranges from 75 to 170 C (167 to 338 F). Grades with Tg above about 140 C (284 F) have a flexural modulus in the vicinity of 500,000 psi and elongation at break of 3% to 4%. Those with a lower Tg have a lower modulus but greater elongation (up to 10%).
Given COCs’ low shrinkage, lubricated grades and mold-release agents can help in removing parts from a mold, especially if long cores are present. Choose mold sprays carefully to ensure they do not leave part surfaces hazy. Mold release can be helped by maintaining holding pressure a bit longer so the part relaxes before it is extracted.
Sustainability continues to dominate new additives technology, but upping performance is also evident. Most of the new additives have been targeted to commodity resins and particularly polyolefins.
Across the show, sustainability ruled in new materials technology, from polyolefins and engineering resins to biobased materials.
Exhibitors and presenters at the plastics show emphasized 3D printing as a complement and aid to more traditional production processes.
The aim of this presentation is to guide you through the factors and the numbers that will help you determine if a robot is a smart investment for your application. Agenda: Why are you considering automation? What problems are you trying to solve? How and why automation can help Crunch the numbers and determine the ROI
In machining COC parts by cutting, drilling, and diamond turning, cuts should be conservative and made at relatively low speeds. This keeps the applied force low, so the COC does not shatter, and it prevents excessive heat build-up. Common machine oils attack COCs and can cause cracking, so coolants must be water-based and machine surfaces and tools must be free of oil.
After successfully introducing a combined conference for moldmakers and injection molders in 2022, Plastics Technology and MoldMaking Technology are once again joining forces for a tooling/molding two-for-one.
Core Technology Molding turned to Mold-Masters E-Multi auxiliary injection unit to help it win a job and dramatically change its process.
COCs retain mechanical properties well over multiple regrind cycles and as much as 20% regrind can be used in many parts. Reground COC may yellow slightly during molding, so regrind cannot be used in optical applications or where very high clarity is needed.
In this collection of articles, two of the industry’s foremost authorities on screw design — Jim Frankand and Mark Spalding — offer their sage advice on screw design...what works, what doesn’t, and what to look for when things start going wrong.
In the future, it is also conceivable that process, quality, and patient data for each individual part will be 100% traceable via an RFID code.
Resin drying is a crucial, but often-misunderstood area. This collection includes details on why and what you need to dry, how to specify a dryer, and best practices.
Learn about sustainable scrap reprocessing—this resource offers a deep dive into everything from granulator types and options, to service tips, videos and technical articles.
COCs should be processed in hot molds to maximize flow length and weld-line strength and prevent shock freezing that can embrittle parts and make them prone to stress cracking. Hot molds also reduce haze, splay marks, and streaks and improve surface quality. Mold temperature is often the determining factor in reducing haze in optical parts. Each COC grade has an optimum mold temperature that minimizes part haze. Streaking can be controlled by using the proper balance between injection speed and mold temperature. Bubble formation and nozzle drool can be reduced by using moderate backpressure (between 20% and 30% of maximum). If discoloration occurs in parts that need extreme clarity, it helps to use a nitrogen blanket over the hopper to keep oxygen away from the resin.contaminants in COCs can cause bubbling, black specks, haze, and smoky swirls in clear parts. To prevent this, molders should thoroughly purge other materials from the barrel and feed areas and from material-transfer systems. It is best to remove the screw and clean both it and the barrel.
Tobe Packaging’s breakthrough was to create its Ecolefin PE multilayer film that could be applied with a specialized barrier coating.
Formnext Chicago is an industrial additive manufacturing expo taking place April 8-10, 2025 at McCormick Place in Chicago, Illinois. Formnext Chicago is the second in a series of Formnext events in the U.S. being produced by Mesago Messe Frankfurt, AMT – The Association For Manufacturing Technology, and Gardner Business Media (our publisher).
COCs can be ultrasonically welded to depths of 0.5 to 1.0 mm in 1 to 3 sec. Vibration amplitudes are typically 15 to 35 microns.
The resin replicates extremely fine mold features. One precision COC laboratory component, for instance, has complex channels as small as 10 microns. COCs also faithfully reproduce sub-micron surface patterns, such as those found on diffraction gratings and optical data-storage media. Only neat grades of Topas COC have been offered until now, but glass-reinforced, mineral-filled, flame-retardant (UL 94V-2 and V-0), and impact-modified grades have been developed. Ticona has also made grades containing stainless-steel fibers to impart electrical conductivity. These new modified grades will open up potential in business machines, communications equipment, and automotive parts like headlight reflectors and air-conditioning fans.
This new family of clear engineering thermoplastics made its first big splash in extrusion, but now injection molders are learning how to process these amorphous resins into optical and medical parts.
With advocacy, communication and sustainability as three main pillars, Seaholm leads a trade association to NPE that ‘is more active today than we have ever been.’
Baystar's Borstar technology is helping customers deliver better, more reliable production methods to greenhouse agriculture.
This month’s resin pricing report includes PT’s quarterly check-in on select engineering resins, including nylon 6 and 66.
Join this webinar to explore the transformative benefits of retrofitting your existing injection molding machines (IMMs). Engel will guide you through upgrading your equipment to enhance monitoring, control and adaptability — all while integrating digital technologies. You'll learn about the latest trends in IMM retrofitting (including Euromap interfaces and plasticizing retrofits) and discover how to future-proof your machines for a competitive edge. With insights from industry experts, it'll walk you through the decision-making process, ensuring you make informed choices that drive your business forward. Agenda: Maximize the value of your current IMMs through strategic retrofitting Learn how to integrate digital technologies to enhance monitoring and control Explore the benefits of Euromap interfaces and plasticizing retrofits Understand how retrofitting can help meet new product demands and improve adaptability Discover how Engel can support your retrofitting needs, from free consultations to execution
Injection moldable COCs have melt flow rates between 1 and 56 g/10 min at 260 C. Shot size should be one-quarter to one-half the capacity of the barrel. COCs can withstand barrel residence time of about 15 min at normal molding temperatures. If process interruptions are likely to be longer, maximum barrel temperature should be reduced to 302 F to avoid yellowing.
Because of COC’s low shrinkage, draft angles should be as large as possible—especially for parts with longer bearing lengths—to avoid distortion and demolding difficulties. Sticking can be a problem on parts with a shallow draft. Draft usually falls between 2° and 5°, though draft as low as 0.5° has been used successfully in some cases.
Join Wittmann for an engaging webinar on the transformative impact of manufacturing execution systems (MES) in the plastic injection molding industry. Discover how MES enhances production efficiency, quality control and real-time monitoring while also reducing downtime. It will explore the integration of MES with existing systems, emphasizing compliance and traceability for automotive and medical sectors. Learn about the latest advancements in IoT and AI technologies and how they drive innovation and continuous improvement in MES. Agenda: Overview of MES benefits What is MES? Definition, role and brief history Historical perspective and evolution Longevity and analytics Connectivity: importance, standards and integration Advantages of MES: efficiency, real-time data, traceability and cost savings Emerging technologies: IoT and AI in MES
Development of new filled, reinforced, flame-retardant, and impact-modified COC grades will open up applications like this business-machine deck (above) and automotive air-conditioning fan (top).
In addition to facilitating recycling, the mono-material construction and integrated processing of the tube and label contribute to the stability of the tube, enabling a reduction in wall thickness, if needed. The process also eliminates secondary operations, such as bonding and printing. No adhesives are required and there is no waste caused by contamination with liquid color.
GETTING A QUOTE WITH LK-MOULD IS FREE AND SIMPLE.
FIND MORE OF OUR SERVICES:
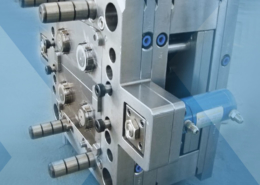
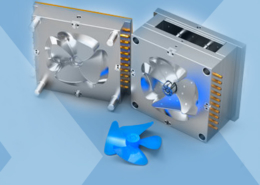
Plastic Molding

Rapid Prototyping
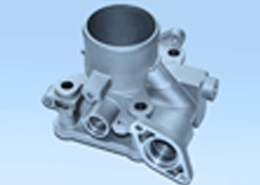
Pressure Die Casting
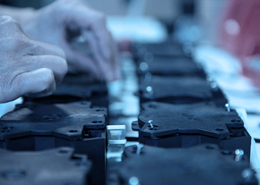
Parts Assembly
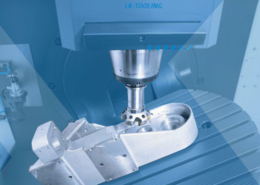