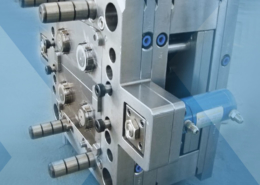
Fit-LINE’s GrabLOC double containment fittings engineered for demanding
Author:gly Date: 2024-09-30
Second quarter started with price hikes in PE and the four volume engineering resins, but relatively stable pricing was largely expected by the quarter’s end.
In cooperation with machine builder Netstal, StackTech showed a transparent, thin-wall PET containers that aims to displace polyolefins normally used for such applications. Source: StackTec
In another TRIM demo at the booth of Italian injection molding machine maker BMB, StackTeck displayed lightweighted 16-oz containers running on a 600-ton BMB eKW55pi/5500H injection molding machine. The 14.5-g PP tub was molded on a 2X8 stack tool, achieving weight savings of 5%, with takeout via a high-speed, side-entry Muller Technology robot. Robertson also had sample lids on hand to show how different technologies and materials could be combined for lightweight containers. These included a clarified PP lid only 0.020 inch thick. He also displayed a 0.013-inch-thick clarified PP lid made with an injection compression process. Finally, applying recycled resin for further sustainability, he showcased a package that combined a 30% rPET container paired with a 100% rPP lid.
The company’s other product lines, Lifecycled polyol and TPU, are produced by chemically recycling HDPE and LDPE postconsumer materials, via thermal oxidative decomposition, into dicarboxylic acids. Production of the Lifecycled products is in pilot phase at Novoloop’s site in India.
Discover how artifical intelligence is revolutionizing plastics processing. Hear from industry experts on the future impact of AI on your operations and envision a fully interconnected plant.
Jordan Robertson, vice president of business development & marketing at StackTeck, told Plastics Technology that the tool utilized sequential valve-gate control for the mold’s hot runners to control the melt injection and shorten the flow length. The part was designed with seven gates on the bottom of the container — one in the center of the bottom and six around the edge of the container. In molding, the center gate is opened first, filling the bottom of the container and, once the melt reaches the outer gates, those are opened.
Novoloop has introduced the Recycled+ line of thermoplastic polyurethane (TPU) manufactured from postindustrial scrap sourced and compounded in the U.S.
Unlike many molding companies in Portugal, which historically have tended to specialize in specific activities—tooling design, polishing, the fabrication of precision molds, and so forth—Muroplás chose to invest in its own machining department and build molds as well as provide injection molding services.
This month’s resin pricing report includes PT’s quarterly check-in on select engineering resins, including nylon 6 and 66.
inmold-labeling (IML) of a thin PET label to create a 450-ml IML container weighing only 15 g in a 4-second cycle. The system also utilized a StackTeck IML Robot, vision and stacking system.
“StackTeck has now built large stack molds with TRIM technology for thinwall containers, as well as expanding the range of applications to include rectangular, tamper evident and ice cream applications,” Robertson says. “As compared to other lightweighting approaches, it has proven to be simple and reliable, while also working well with other technologies such as multigating.”
Processors with sustainability goals or mandates have a number of ways to reach their goals. Biopolymers are among them.
UBQ has found material applications in durable and semidurable goods, including secondary packaging and automotive components. UBQ plants are certified under the IATF (International Automotive Task Force) quality system.
The company operates Class 7 cleanrooms on site for the production of infusion, transfusion, and hemodialysis kits. It runs Krauss Maffei and Negri Bossi molding systems in its 4500-sq-m production space. Muroplás also has developed an IT system to help maximize the production of precision parts for medical applications. One investment that has contributed to its success is the purchase early on of PowerMILL CAM software from Delcam plc (Birmingham, UK), which it has used to develop its own range of medical devices. Muroplás carries on a tradition, in fact: Back in 1983, a Portuguese company was the first European moldmaker to install CAD/CAM technology, according to industry association Cefamol.
While the melting process does not provide perfect mixing, this study shows that mixing is indeed initiated during melting.
Gifted with extraordinary technical know how and an authoritative yet plain English writing style, in this collection of articles Fattori offers his insights on a variety of molding-related topics that are bound to make your days on the production floor go a little bit better.
“For people who want fast adoption of recycled TPU — and it doesn’t have to be postconsumer — this is the solution,” says Wang. Recycled+ material offers near-virgin mechanical properties and can be used with very high recycled content percentages.
“If you have a question off the top of your head and are trying to learn more, it will be able to provide a good starting place to get at that more fundamental knowledge. If you are asking to get into the nitty gritty or ‘what just happened today?’, that’s something for the market expert,” says Emily Friedman, recycled plastics senior market editor at ICIS. “We have a lot of data, and this provides an easy way for it to be collated and accessible.”
The aim of this presentation is to guide you through the factors and the numbers that will help you determine if a robot is a smart investment for your application. Agenda: Why are you considering automation? What problems are you trying to solve? How and why automation can help Crunch the numbers and determine the ROI
What’s more, the line was furnished with Macchi I.o.T., a digital solution that performs OEE monitoring, breakdown analytics and predictive maintenance to verify production efficiency in real time. Also in action was the Macchi W.i.S. (Web Inspection System), an innovative solution for film defects mapping.
Portugal has a storied moldmaking tradition that dates back to the beginning of the 20th century, when companies in the town of Marinha Grande, about 95 miles north of Lisbon, started manufacturing molds for glassware rather than importing them. After World War II, plastic injection molds gained a foothold and, with the inevitable ups and downs, that has continued ever since. Automotive OEMs have been reliable customers; medical device manufacturers, not so much. Muroplás, located in Muro-Trofa, about 130 miles north of Marinha Grande, is the exception that proves the rule.
Novoloop’s Recycled+ line of thermoplastic polyurethane (TPU) is manufactured from postindustrial scrap sourced and compounded in the U.S. Source: Novaloop
“You don’t need to reinvent the wheel. You can start with existing equipment and processes, and start dropping in UBQ right away,” says Albert Douer, executive chairman and co-CEO at UBQ.
Alpek is partnering with Husky, manufacturer of the HyCAP beverage closure system, for its development runs. Bottles have been filled and capped on an industrial bottle filler and capper, and subsequent testing is showing they can be capped and unscrewed, and is subjecting samples to the challenges of drop impact and environmental stress cracking.
Colines’ AllRollEx line ran intermittently through the exhibit. In collaboration with ExxonMobil, it produced high-tenacity hand wrap film at a thickness of 8 microns containing 35% postconsumer recycled (PCR) material along with Enable 1617, which ExxonMobil launched at the NPE2024.
Says Gambarotto, “Nowadays when someone purchases a blown film line and invests millions, they want to be sure not only about the technology but also about the company they are buying from, how strong it is, how committed they are to the market. We’re confident that what we will be demonstrating will be interesting to the audience and also be positive for Bandera.”
“We’re quality controlling this material, we’re compounding to enhance the performance and improve the melt strength, and the products can be used straight up, it’s nearly 100% recycled content,” says Miranda Wang, founder and CEO at Novoloop. Recycled+ TPU is available with high percentages of recycled content and with near-virgin mechanical properties without the need to blend with virgin resin. The product is available now in full-container quantities.
technotrans says climate protection, energy efficiency and customization will be key discussion topics at PTXPO as it displays its protemp flow 6 ultrasonic eco and the teco cs 90t 9.1 TCUs.
The Plastics Industry Association (PLASTICS) has released final figures for NPE2024: The Plastics Show (May 6-10; Orlando) that officially make it the largest ever NPE in several key metrics.
The Ask ICIS tool compiles all pricing data, news and capacity information in one place, sourcing answers from over 500 million data points. According to ICIS, this tool will complement the expertise of its analysts by providing quick turnaround on any question that may arise for ICIS customers.
This Knowledge Center provides an overview of the considerations needed to understand the purchase, operation, and maintenance of a process cooling system.
Ultradent's entry of its Umbrella cheek retractor took home the awards for Technical Sophistication and Achievement in Economics and Efficiency at PTXPO.
UBQ materials are miscible with polymer resins, including polyolefins and styrenics, and can be used in injection molding and extrusion operations. As with any biobased material, processing temperatures should be chosen to avoid burning. UBQ recommends processing below 190-200°C. UBQ materials are hydrophilic, so they should be dried and/or used with vented extruders.
Novoloop is offering five varieties of Recycled+ TPU, with recycled content from 77% to more than 96%, and with Shore A durometer ratings from 86 to 96.
UBQ has created a portfolio of materials manufactured from unsorted municipal waste. Around 80-90% of the waste is organic, including cellulose and other fibrous materials. Only metals and minerals are removed, and the remaining mixture is processed to create a new, thermoplastic material that can be substituted for polymers or other materials.
In this three-part collection, veteran molder and moldmaker Jim Fattori brings to bear his 40+ years of on-the-job experience and provides molders his “from the trenches” perspective on on the why, where and how of venting injection molds. Take the trial-and-error out of the molding venting process.
The new, patented process requires simply molding an oval-shaped bottle and then clipping and welding the base. If a barrier is required, the inside of the bottle can be plasma coated — Delta Engineering is in the process of patenting an improved organic coating that is said to provide up to 40 times greater oxygen barrier than PET alone. Besides being easy to print, the PET ISBM tube offers new decorating options via embossing, not available on extruded tubes.
Coverage of single-use plastics can be both misleading and demoralizing. Here are 10 tips for changing the perception of the plastics industry at your company and in your community.
In this collection, which is part one of a series representing some of John’s finest work, we present you with five articles that we think you will refer to time and again as you look to solve problems, cut cycle times and improve the quality of the parts you mold.
StackTeck’s TRIM technology, where application of thinner panels reduce material usage, has been demonstrated to lightweight conventional thinwall designs by 10% to 40% of part weight. Applying TRIM panels all over the part can compromise container strength, so StackTeck has conceived of an alternative approach that applies TRIM to the bottom only, leaving alone the sidewall and corner wall thicknesses. In this way, top-load performance and other performance criteria are met but 5% light weighting can still be achieved.
Join Engel in exploring the future of battery molding technology. Discover advancements in thermoplastic composites for battery housings, innovative automation solutions and the latest in large-tonnage equipment designed for e-mobility — all with a focus on cost-efficient solutions. Agenda: Learn about cutting-edge thermoplastic composites for durable, sustainable and cost-efficient battery housings Explore advanced automation concepts for efficient and scalable production See the latest large-tonnage equipment and technology innovations for e-mobility solutions
The composition of the material varies, depending on the municipal source and throughout the year. UBQ uses its knowledge about this variation, along with processing adjustments, in formulating products with different characteristics for different applications. UBQ material is available as ClimaPOS (a sustainability additive), Q Series (a material replacement) and UBQ Industrial (for high durability operational uses).
Across all process types, sustainability was a big theme at NPE2024. But there was plenty to see in automation and artificial intelligence as well.
Macchi has run lines at the last several NPEs. At NPE2024, it ran a 5-layer polyolefin-dedicated line featuring 5 extruders; a continuous flow hydraulic screen changers to better accommodate the introduction of reclaim; a triple-flow air ring with an integrated automatic profile control system; a wax drainage system for the air ring; a frost line scanner; a smoke suction system on bubble guide; a Centro Freeze-supporting basket with cooling function; a double station automatic winder; and an inline system for side trim recovery.
The material has a negative carbon footprint because of the diversion of solid waste. For each ton produced, 11.7 tons of CO2eq emissions are averted, so even a small percentage of UBQ added to a product can have a significant impact toward meeting sustainability goals.
Learn about sustainable scrap reprocessing—this resource offers a deep dive into everything from granulator types and options, to service tips, videos and technical articles.
Another novel application at NPE2024 was a squeeze tube of PET in place of the usual PP. Developed by Delta Engineering of Belgium (U.S. office in Norcross, Georgia), the most striking element of the new tube is that it is made by injection stretch-blow molding (ISBM) on single-step Nissei ASB machines, rather than extrusion. According to Delta Engineering managing director Danny De Bruyn, the usual multistep process involves coextrusion or laminating to make a cylinder, which is cut off and fitted with an injection molded shoulder by molding or bonding.
Despite price increase nominations going into second quarter, it appeared there was potential for generally flat pricing with the exception of a major downward correction for PP.
The global commodities intelligence provider ICIS announced its generative AI product, Ask ICIS. Ask ICIS will provide answers to commodity questions for decision-makers in plastics as well as other global petrochemical markets. The company is often referred to as a third-party source for pricing information, increasing transparency and facilitating negotiations.
Mike Sepe has authored more than 25 ANTEC papers and more than 250 articles illustrating the importance of this interdisciplanary approach. In this collection, we present some of his best work during the years he has been contributing for Plastics Technology Magazine.
While builders of injection molding and blow molding machinery conventionally operate machines at trade shows, many manufacturers of extrusion lines have trended toward static displays — in particular at NPE, but of late at the K Show as well — due to cost, line size and complexity, more restrictive ceiling heights, potential processing complications and numerous other factors.
In the case of Bandera, NPE2024 marked the first time ever it ran a line at a show outside Europe. The machine builder, which recently opened a new office in the U.S. in Charlotte, N.C., operated its 5-layer Techno Flex line in Orlando, running a variety of polyolefin-based structures for shrink film, lamination, printing and gusseted film. Bandera ran at thickness from 20 to 200 μm at output rates of 880 lbs/hr. The line was shipped to the show after it debuted at an open house in January at Bandera’s headquarters in Busto Arsizio, Italy (near Milan). At the show, the line was purchased by Reliance Packaging, part of Sigma Plastics Group.
Bandera ran a blown film line for the first time ever at NPE. It sold the all-polyolefin system at the show to Reliance Packaging. Source: Plastics Technology
In this collection of articles, two of the industry’s foremost authorities on screw design — Jim Frankand and Mark Spalding — offer their sage advice on screw design...what works, what doesn’t, and what to look for when things start going wrong.
In this collection of content, we provide expert advice on welding from some of the leading authorities in the field, with tips on such matters as controls, as well as insights on how to solve common problems in welding.
Join Wittmann for an engaging webinar on the transformative impact of manufacturing execution systems (MES) in the plastic injection molding industry. Discover how MES enhances production efficiency, quality control and real-time monitoring while also reducing downtime. It will explore the integration of MES with existing systems, emphasizing compliance and traceability for automotive and medical sectors. Learn about the latest advancements in IoT and AI technologies and how they drive innovation and continuous improvement in MES. Agenda: Overview of MES benefits What is MES? Definition, role and brief history Historical perspective and evolution Longevity and analytics Connectivity: importance, standards and integration Advantages of MES: efficiency, real-time data, traceability and cost savings Emerging technologies: IoT and AI in MES
Alpek debuted a PET called CaPETall for making bottle caps, and is collaborating with Husky on development. Source: Alpek
Portugal has a storied moldmaking tradition that dates back to the beginning of the 20th century, when companies in the town of Marinha Grande, about 95 miles north of Lisbon, started manufacturing molds for glassware rather than importing them. After World War II, plastic injection molds gained a foothold and, with the inevitable ups and downs, that has continued ever since. Automotive OEMs have been reliable customers; medical device manufacturers, not so much. Muroplás, located in Muro-Trofa, about 130 miles north of Marinha Grande, is the exception that proves the rule.
In a time where sustainability is no longer just a buzzword, the food and beverage packaging industry is required to be at the forefront of this innovation. By adopting circular packaging processes and solutions, producers can meet regulatory requirements while also satisfying consumer demand and enhancing brand reputation. Join Husky to learn more about the broader implications of the circular economy — as well as how leading brands are leveraging this opportunity to reduce costs, increase design flexibility and boost product differentiation. Agenda: The cost and operational benefits of embracing circularity Key materials in circular packaging — including rPET and emerging bioplastics How to design a circular food and beverage package Strategies for selecting sustainable closures to future-proof packaging solutions Optimization and streamlining of production processes for enhanced efficiency How Husky Technologies can enable your sustainable success
Bandera, however, decided to invest in running an actual blown film line at the show to demonstrate its commitment to the North American market, notes Mattia Gambarotto, general manager of Bandera’s North American operation. The line featured a 20-component gravimetric dosing system with an automatic cleaning system; 5 extruders (one 85 mm; the other four 65 mm); a 5-layer 300-mm coextrusion die head with IBC; a high-efficiency dual-lip air ring; automatic film thickness control; flattening and gusseting devices; calibration cages; an oscillating haul-off, 1,800-mm roller width; the company’s Trim Flex edge reclaim system; a two-station face-to-face winder featuring contact/axial winding modes with automatic reel extraction; and a complete tower frame. The line is designed and supplied on 480-volt components.
Resin drying is a crucial, but often-misunderstood area. This collection includes details on why and what you need to dry, how to specify a dryer, and best practices.
Across all process types, sustainability was a big theme at NPE2024. But there was plenty to see in automation and artificial intelligence as well.
UBQ has created a portfolio of materials manufactured from unsorted municipal waste. Around 80-90% of the waste is organic, including cellulose and other fibrous materials. Source: UBQ
The resin is Solon PHA from RWDC Industries. It is produced by microbial fermentation of vegetable oils, including waste cooking oil, and is said to break down in commercial composting and in soil, freshwater and marine environments.
The ALLrollEX lines also feature an inline edge folding system, which Colines says makes them well suited for processing of high PCR content films for automatic machine use. Colines adds the Mastermind AI control package provides a dramatic reduction in setup and startup times of the extrusion line; in stretch film production, 2 sigma 1% is achieved in 180 seconds, says the machine builder. The system is also said to provide consistent production quality over time. It’s also billed as safe and user friendly, as even less experienced operators can easily manage the system.
While prices moved up for three of the five commodity resins, there was potential for a flat trajectory for the rest of the third quarter.
A collaboration between show organizer PLASTICS, recycler CPR and size reduction experts WEIMA and Conair recovered and recycled all production scrap at NPE2024.
The show’s overall theme of sustainability was evident in two apparently unique blow molding applications. One of them was heralded as a potential breakthrough for biopolymers in blow molding: It’s said to be the world’s first biodegradable water bottle, molded in PHA. The bottle comes from a company called Cove , founded in 2018 and based in Irvine, California. In late 2022, Cove launched a test market in Los Angeles of still water in 20-fl-oz (591-ml) single-use bottles with injection molded PHA caps. The off-white, opaque bottles have no labels, but are printed with biodegradable, algae-based ink.
Exhibitors and presenters at the plastics show emphasized 3D printing as a complement and aid to more traditional production processes.
Across the show, sustainability ruled in new materials technology, from polyolefins and engineering resins to biobased materials.
Thousands of people visit our Supplier Guide every day to source equipment and materials. Get in front of them with a free company profile.
Cove has been producing its own bottles, using Bekum and Magic shuttle machines. At the end of last year, Cove founder and CEO Alex Totterman announced that his company was shifting its business model from producing its own products to collaborating with global brands interested in adopting Cove’s technology. Cove will retain its California R&D lab, but has started to open up its technology — from materials formulation to bottle design and manufacturing — to a select group of partners.
Contrary to common belief, the major reason suppliers of injection molding services incorporate moldmaking and mold repair into their portfolio typically is not a matter of economics but delivery time, according to Delcam. Time and reputation is lost when a company has to wait for a mold to be repaired or parts shipment is delayed because molds have not been delivered within the planned timeframe. Being able to implement small changes or improvements to the mold on site also improves customer service, and intellectual property ceases to be an issue when molds are built in house, says the company.
While the major correction in PP prices was finally underway, generally stable pricing was anticipated for the other four commodity resins.
August 29-30 in Minneapolis all things injection molding and moldmaking will be happening at the Hyatt Regency — check out who’s speaking on what topics today.
Additive technology creates air pockets in film during orientation, cutting down on the amount of resin needed while boosting opacity, mechanical properties and recyclability.
Muroplás is always attuned to the needs of its customers and continues to invest in the necessary resources to produce complex molds and optimize production, says Baptista, and that is the simple secret of its ongoing success. "R&D is an obsession at Muroplás," says Baptista. "We exist for our customers, and we are proud to have forged a relationship based on quality."
Introduced by Zeiger and Spark Industries at the PTXPO, the nozzle is designed for maximum heat transfer and uniformity with a continuous taper for self cleaning.
Over a dozen companies emphasized sustainability with use of foam and recycle, lightweighting and energy savings, along with new capabilities in controls, automation and quick changeovers.
Perhaps most interesting to packagers, according to de Bruyn, is the ability to fill the new tubes just like a regular bottle, which enables filling to a higher level of the tube’s capacity than with standard tubes. The end result is the ability to downsize the tube and use 20-30% less plastic for the same volume of content, De Bruyn claims.
Plastics Technology covers technical and business Information for Plastics Processors in Injection Molding, Extrusion, Blow Molding, Plastic Additives, Compounding, Plastic Materials, and Resin Pricing. About Us
Once viewed by injection and blow molders as a necessary evil, machine vision technology today can continuously monitor and improve production while reducing costs.
Join KraussMaffei for an insightful webinar designed for industry professionals, engineers and anyone interested in the manufacturing processes of PVC pipes. This session will provide a comprehensive understanding of the technology behind the production of high-quality PVC pipes: from raw material preparation to final product testing. Agenda: Introduction to PVC extrusion: overview of the basic principles of PVC pipe extrusion — including the process of melting and shaping PVC resin into pipe forms Equipment and machinery: detailed explanation of the key equipment involved — such as extruders, dies and cooling systems — and their roles in the extrusion process Process parameters: insight into the critical process parameters like temperature, pressure and cooling rates that influence the quality and consistency of the final PVC pipes Energy efficiency: examination of ways to save material and energy use when extruding PVC pipe products
Mixed in among thought leaders from leading suppliers to injection molders and mold makers at the 2023 Molding and MoldMaking conferences will be molders and toolmakers themselves.
Core Technology Molding turned to Mold-Masters E-Multi auxiliary injection unit to help it win a job and dramatically change its process.
When, how, what and why to automate — leading robotics suppliers and forward-thinking moldmakers will share their insights on automating manufacturing at collocated event.
Sustainability continues to dominate new additives technology, but upping performance is also evident. Most of the new additives have been targeted to commodity resins and particularly polyolefins.
Applying its Thin Recess Injection Molding (TRIM) and other advances, toolmaker StackTeck Systems Ltd., sought to push PET to its limits — and into new areas of packaging — at NPE2024.
Join this webinar to explore the transformative benefits of retrofitting your existing injection molding machines (IMMs). Engel will guide you through upgrading your equipment to enhance monitoring, control and adaptability — all while integrating digital technologies. You'll learn about the latest trends in IMM retrofitting (including Euromap interfaces and plasticizing retrofits) and discover how to future-proof your machines for a competitive edge. With insights from industry experts, it'll walk you through the decision-making process, ensuring you make informed choices that drive your business forward. Agenda: Maximize the value of your current IMMs through strategic retrofitting Learn how to integrate digital technologies to enhance monitoring and control Explore the benefits of Euromap interfaces and plasticizing retrofits Understand how retrofitting can help meet new product demands and improve adaptability Discover how Engel can support your retrofitting needs, from free consultations to execution
After successfully introducing a combined conference for moldmakers and injection molders in 2022, Plastics Technology and MoldMaking Technology are once again joining forces for a tooling/molding two-for-one.
PHA biopolymer bottles made by Cove in California are said to the world’s first 100% biodegradable water bottles. Cove is working with major brands to develop biopolymer beverage bottles. Source: Matthew Naitove
Alpek Polyester has introduced CaPETall resin, enabling the molding of 100% PET bottle cap closures for water and carbonated sodas. According to Alpek, the material formulation reduces the friction between the threaded surfaces of the cap and bottle, while meeting the requirements of the PET resin identification code 1. An all-PET design for beverage bottles would facilitate recycling by eliminating the need to separate cap flakes into a different, lower value, recyclate stream.
Because of the differences in thermal contraction between PET and polyolefins traditionally used to mold caps, some tooling changes are necessary to accommodate. But otherwise, the material will run on standard injection molding, filling and capping equipment, according to Alpek. The material can be used to make colored or clear caps.
Italian machine builders Luigi Bandera and Macchi are bucking the trend among suppliers of blown film machinery by running blown-film production lines during NPE2024. And Italy’s Colines operated a cast stretch line with an artificial intelligence (AI) control package called Mastermind. Even grizzled veterans of NPE can’t recall the last time a stretch film line was ever operated at the show.
Editor’s Note: More than 50,000 attendees packed the halls of the Orange County Convention Center in Orlando, Florida, May 6-10, for NPE2024, the first NPE since 2018 (NPE2020 was shelved due to the COVID-19 pandemic). Here, we cover developments in the major process segments not previously reported in previous issues of Plastics Technology. Please refer to the February, March, April, May and June issues for pre-show coverage. We will continue our reporting of NPE2024 in August.
Take a deep dive into all of the various aspects of part quoting to ensure you’ve got all the bases—as in costs—covered before preparing your customer’s quote for services.
Editor in chief of PlasticsToday since 2015, Norbert Sparrow has more than 30 years of editorial experience in business-to-business media. He studied journalism at the Centre Universitaire d'Etudes du Journalisme in Strasbourg, France, where he earned a master's degree.
In cooperation with injection molding machine supplier Netstal, StackTeck introduced a transparent, thin-walled PET container, seeking to displace polyolefins normally applied for such packaging. Using a 1 × 2 TRIM multigated tool, the 350-ton Elion machine applied
Plastics Technology’s Tech Days is back! Every Tuesday in October, a series of five online presentations will be given by industry supplier around the following topics: Injection Molding — New Technologies, Efficiencies Film Extrusion — New Technologies, Efficiencies Upstream/Downstream Operations Injection Molding — Sustainability Extrusion — Compounding Coming out of NPE2024, PT identified a variety of topics, technologies and trends that are driving and shaping the evolution of plastic products manufacturing — from recycling/recyclability and energy optimization to AI-based process control and automation implementation. PT Tech Days is designed to provide a robust, curated, accessible platform through which plastics professionals can explore these trends, have direct access to subject-matter experts and develop strategies for applying solutions in their operations.
Formnext Chicago is an industrial additive manufacturing expo taking place April 8-10, 2025 at McCormick Place in Chicago, Illinois. Formnext Chicago is the second in a series of Formnext events in the U.S. being produced by Mesago Messe Frankfurt, AMT – The Association For Manufacturing Technology, and Gardner Business Media (our publisher).
The company expects the product lines to complement each other well. “Our overall vision is taking linear plastics and putting them into loops, so we are building these two arms in parallel,” Wang says. “We want to be materials-as-service, so for our customers who buy our Lifecycled product, we’ll buy their manufactured scrap, reprocess it and sell it as another product. We’ll offer this as a package deal.”
Founded in 1989, Muroplás initially produced precision parts for the automotive industry. Shortly after setting up shop, however, "domestic companies that needed components for infusion systems challenged us to produce parts," says Dinis Baptista, International Sales/Information Systems. The company never looked back, and has been a national pioneer in plastic injection molding for medical device OEMs since the 1990s. Medical technology applications now represent 90% of the company's business, and it has cemented its reputation by investing in R&D and new technologies, and embracing change.
Mold maintenance is critical, and with this collection of content we’ve bundled some of the very best advice we’ve published on repairing, maintaining, evaluating and even hanging molds on injection molding machines.
Say “manufacturing automation” and thoughts immediately go to the shop floor and specialized production equipment, robotics and material handling systems. But there is another realm of possible automation — the front office.
Robertson notes this effectively cuts flow length in half for the second tier of gates, giving the thinwalled parts a much better flow length-to-wall thickness, or L/t, ratio. Robertson says that as a rule of thumb, PET when used in packaging is generally two times more thick and double the weight or more than, say, PP, which is typically used in these containers, making the 15 g weight quite appealing. In addition, Robertson said PET’s crystallinity typically precludes undercuts, but StackTeck was able to create one for the lid to snap onto the container.
Multiple speakers at Molding 2023 will address the ways simulation can impact material substitution decisions, process profitability and simplification of mold design.
The company describes Recycled+ TPU as an entry point for customers to get recycled content into their TPU now, while the company continues to build its capabilities in its other product lines of upcycled TPU.
Successfully starting or restarting an injection molding machine is less about ticking boxes on a rote checklist and more about individually assessing each processing scenario and its unique variables.
"We believe that combining the conception and manufacture of molds with injection molding of precision plastic parts offers our customers unique benefits," Dinis Baptista, International Sales/Information Systems, told PlasticsToday. "The use of high-speed machining technology and a dedication to improving the form, function, and manufacturability of molds has allowed us to provide medical device manufacturers with the best of both worlds: accuracy and precision at less cost," adds Baptista.
While prices moved up for three of the five commodity resins, there was potential for a flat trajectory for the rest of the third quarter.
GETTING A QUOTE WITH LK-MOULD IS FREE AND SIMPLE.
FIND MORE OF OUR SERVICES:
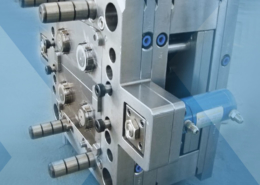
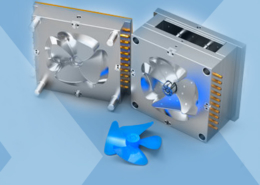
Plastic Molding

Rapid Prototyping
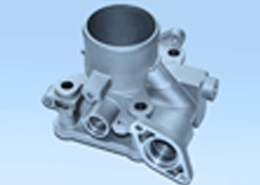
Pressure Die Casting
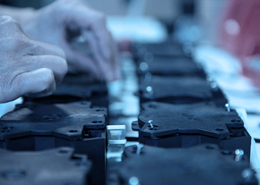
Parts Assembly
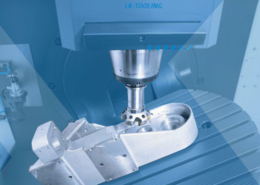