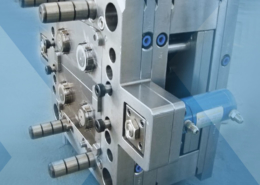
Finding a Niche in LSR Tooling - plastic mold maker
Author:gly Date: 2024-09-30
While prices moved up for three of the five commodity resins, there was potential for a flat trajectory for the rest of the third quarter.
For example, if a part design has sharp outside corners (meaning sharp inside corners in the mold) and is subjected to high injection pressures, it’s longevity could be very short due to the potential of fracturing. I’ve seen well-built, class 101 hot-runner molds fail after the first five minutes because the manifold filled up with plastic—snapping bolts and splitting plates apart. I have also seen dead-soft aluminum molds run trouble-free for well over a decade.
The new U.S. subsidiary, called Stork IMM USA LLC, builds upon Stork IMM’s 25-year history in the North American market. The company manufactures injection moulding machines ranging in size from 200 to 2,000 tons for high-speed packaging applications.
Discover how artifical intelligence is revolutionizing plastics processing. Hear from industry experts on the future impact of AI on your operations and envision a fully interconnected plant.
Let’s do some simple math. Assume a sub-gated part leaves 1/16-in. diam. flakes on the parting line. A 1/16-in. diam. flake has an area of 0.0031 in.2. The mold is in a 500-ton press. Pressure = Force ÷ Area so in this case:
When, how, what and why to automate — leading robotics suppliers and forward-thinking moldmakers will share their insights on automating manufacturing at collocated event.
While it’s true that heat-treated tool steels with high compressive strength can delay the amount or severity of flash damage, it cannot make the mold impervious to damage. Figure 4 shows a severely hobbed parting line of a pre-hardened 28-32 Rockwell C mold caused by nozzle strings. Generally speaking, the harder the tool steel is, the more brittle it is. Obviously, there is a tradeoff when it comes to the physical properties of metals. Depending on several factors, you might need to consider using a more ductile material, or making a spare cavity set as insurance.
Core Technology Molding turned to Mold-Masters E-Multi auxiliary injection unit to help it win a job and dramatically change its process.
Stork IMM has sold injection moulding machines in North America for more than 25 years. The company’s robust, high-speed injection moulding machinery is a superior solution for the production of food-grade, thin-wall packaging made of polyolefins (PE and PP). Key applications include closures, tubs, containers, and cups along with flower pots, and paint pails and buckets.
1. What is the expected annual quantity? This helps the moldmaker decide the mold classification and the number of cavities required to meet those annual quantities.
Join Engel in exploring the future of battery molding technology. Discover advancements in thermoplastic composites for battery housings, innovative automation solutions and the latest in large-tonnage equipment designed for e-mobility — all with a focus on cost-efficient solutions. Agenda: Learn about cutting-edge thermoplastic composites for durable, sustainable and cost-efficient battery housings Explore advanced automation concepts for efficient and scalable production See the latest large-tonnage equipment and technology innovations for e-mobility solutions
I have a 1982 edition of the Classifications of Injection Molds for Thermoplastic Materials by the Society of the Plastics Industry (now the Plastics Industry Association, or PLASTICS). My edition defines the construction requirements for various types of molds for machines up to 400 tons and labels them type 101 through 105. It also has three types of quick-change mold inserts, which are labeled type I through III. It specifies similar classifications for molds that require machines with 400 tons or more of clamp pressure. Each type has a specific number of cycles a mold is capable of producing. Table 1 summarizes these classifications and lifespan quantities.
Take a deep dive into all of the various aspects of part quoting to ensure you’ve got all the bases—as in costs—covered before preparing your customer’s quote for services.
The hardness of the plastic, as well as the hardness of the mold can dictate how quickly and how severely the mold will get damaged. If a hot bushing is drooling Ultem PEI in a P-20 mold, it won’t be long before you are grinding a few thousandths off the parting line to clean it up. I know moldmakers that intentionally make the mold cores 0.005 in. taller because they believe they will be grinding the parting line a couple of times over the life of the mold. But the hardnesses of the plastic and the steel are not the only factors that promote flash. The list of potential causes is exhaustingly long. Here are some of the more common ones:
Exhibitors and presenters at the plastics show emphasized 3D printing as a complement and aid to more traditional production processes.
Acknowledgement: I want to thank Brenda Clark of Hasco America; Patricia Miller of Uddeholm; Roy Glenn, retired mold builder and designer; and Rick DeBeer, retired from LyondellBasell, for their knowledge and insight, which helped me compose this article.
To support the North American business, Stork IMM has also hired two new directors of business development, George Kotzeff and Scott Molnar.
The Plastics Industry Association (PLASTICS) has released final figures for NPE2024: The Plastics Show (May 6-10; Orlando) that officially make it the largest ever NPE in several key metrics.
Formnext Chicago is an industrial additive manufacturing expo taking place April 8-10, 2025 at McCormick Place in Chicago, Illinois. Formnext Chicago is the second in a series of Formnext events in the U.S. being produced by Mesago Messe Frankfurt, AMT – The Association For Manufacturing Technology, and Gardner Business Media (our publisher).
The only time a mold is considered unusable or has reached the end of its lifespan is when the repair cost exceeds its worth.
If the injection or packing pressure is excessive, or if the clamp pressure is insufficient, the plastic will try to ooze out of the cavity. This usually results in the sharp-edged perimeter of the cavity starting to look like someone added a small radius to it. Over time, the cavity will have more and more flash growing around it. The problem with flash is that once the surface of a mold is indented, it never gets better. It can only get worse. It needs to be repaired and the root cause determined and corrected when it’s first noticed. Giving an operator a razor blade or some other tool to remove the flash is not an appropriate corrective action.
A pre-hardened stainless-steel mold base is an even better solution. The thermal conductivity of stainless isn’t as good, but it usually doesn’t matter for a mold base. I always wondered about moldmakers who prefer steel types that have good weldability. While that is a good property to have, it shouldn’t be a guiding factor. Some steel preferences are based on years of experience. Some are based on how easy they are to machine, or how much they change size or warp during heat treatment. Usually, the commonly used steels are more than adequate for most parts. But occasionally the properties of the steel should be given greater consideration.
Additive technology creates air pockets in film during orientation, cutting down on the amount of resin needed while boosting opacity, mechanical properties and recyclability.
Across all process types, sustainability was a big theme at NPE2024. But there was plenty to see in automation and artificial intelligence as well.
The aim of this presentation is to guide you through the factors and the numbers that will help you determine if a robot is a smart investment for your application. Agenda: Why are you considering automation? What problems are you trying to solve? How and why automation can help Crunch the numbers and determine the ROI
Just like an airplane, car, boat or motorcycle, a mold can potentially last forever if it is maintained properly and repaired when necessary. The only time a mold is considered unusable or has reached the end of its lifespan is when the repair cost exceeds its worth. In addition to the part and mold complexity, the mold’s longevity is based on many other factors, including (but not limited to) the mold design, steel selection, quality of the mold components and construction, the molding machine it runs in, molding material type and molding process used to make the parts, as well as the mold installation, removal, maintenance and storage.
Thousands of people visit our Supplier Guide every day to source equipment and materials. Get in front of them with a free company profile.
Resin drying is a crucial, but often-misunderstood area. This collection includes details on why and what you need to dry, how to specify a dryer, and best practices.
• Inferior mold design • Inferior mold construction • Insufficient mold-plate thicknesses • Insufficient support-pillar area • Lack of parting-line relief • Improper mold setup • Insufficient clamp pressure • Excessive clamp pressure • Cavity imbalance • Poor processing parameters • Excessive injection or pack pressures • Low material viscosity • Insufficient venting • Excessive vent depth • Using adhesive labels as vents • Machine bushing wear • Machine platen wear • Lack of alignment • Worn shutoffs • Abrasive molding material • Abrasive material fillers • Nozzle stringing • Sub-gate flaking • Sticking parts or runners • Rust or corrosion • Lack of preventive maintenance
Netherlands-based Stork IMM (Stork Plastic Machinery B.V.), a manufacturer of injection moulding machines for the packaging market, announced the opening of a sales and service operation in Swedesboro, N.J.
Every customer I’ve ever had always asked how many parts their mold could make. Most moldmakers will respond to that question by saying something like, “Well, you paid for a Class 101 mold, so it should produce up to 1 million cycles.” Obviously, that answer is based on the PLASTICS mold classifications. While the classifications and the requirements for those classifications are excellent, I don’t agree with specifying the number of cycles each type of mold should be able to produce.
If the material is highly abrasive, such as those with glass fillers, all the surfaces in contact with the plastic need to be through-hardened—the harder the better. That includes the sprue bushing and runner inserts, not just the cavities and cores. Abrasive materials can also dictate that the gate(s) be inserted because they will be the first thing(s) to wear out. Steels with high concentrations of carbon and chrome typically have good wear resistance. If the material is extremely abrasive, such as a thermally conductive material with silicon carbide filler, then one of the powdered-metal tool steels with a typical hardness value of about 60 Rockwell C could be best suited.
After successfully introducing a combined conference for moldmakers and injection molders in 2022, Plastics Technology and MoldMaking Technology are once again joining forces for a tooling/molding two-for-one.
In this three-part collection, veteran molder and moldmaker Jim Fattori brings to bear his 40+ years of on-the-job experience and provides molders his “from the trenches” perspective on on the why, where and how of venting injection molds. Take the trial-and-error out of the molding venting process.
The PLASTICS document is meant to be a guideline for purchasers of injection molds, and it should be renamed accordingly—guideline. The problem is that many people consider the stated minimum cycle counts to be factual, if not contractual. And that can lead to problems down the road. What happens to a class 101 mold at a million and one cycles? The customer pays for all the maintenance and repairs to the mold—regardless of how small or how large the cost? What happens at 999,000 cycles if a cavity cracks? Does the moldmaker have to replace it at his cost? As unpleasant as this topic is, it may be worth setting some initial ground rules with your customers.
Despite price increase nominations going into second quarter, it appeared there was potential for generally flat pricing with the exception of a major downward correction for PP.
These humble but essential fasteners used in injection molds are known by various names and used for a number of purposes.
“We envision significant business opportunities in the U.S. and we’ve now laid the groundwork so we can build on our customer base,” said Gert Boers, CEO of Stork IMM. “With the establishment of domestic service and spare parts, we’re now uniquely positioned to scale up and grow our business.”
The real mold killer—for any mold, of any complexity—is parting-line flash. When plastic or other debris adheres to the parting line of a mold, it can deform the mold by leaving an impression or indentation. If you think about it, when debris is sandwiched between two flat surfaces and is exposed to a few hundred tons of clamp pressure, it has nowhere to go but in.
An uncommon, but very serious crash can occur when a large mold is hung in the machine in two halves. If one of the halves is accidentally oriented 180° out of position and the setup man overrides the low-pressure setup mode because the mold won’t close, really bad things happen. On a couple of occasions, I have seen a molding machine with a bad hydraulic valve. The mold closed at full velocity and shook the entire building. But accidental mold crashes are thankfully infrequent and one-time events.
Join this webinar to explore the transformative benefits of retrofitting your existing injection molding machines (IMMs). Engel will guide you through upgrading your equipment to enhance monitoring, control and adaptability — all while integrating digital technologies. You'll learn about the latest trends in IMM retrofitting (including Euromap interfaces and plasticizing retrofits) and discover how to future-proof your machines for a competitive edge. With insights from industry experts, it'll walk you through the decision-making process, ensuring you make informed choices that drive your business forward. Agenda: Maximize the value of your current IMMs through strategic retrofitting Learn how to integrate digital technologies to enhance monitoring and control Explore the benefits of Euromap interfaces and plasticizing retrofits Understand how retrofitting can help meet new product demands and improve adaptability Discover how Engel can support your retrofitting needs, from free consultations to execution
Join KraussMaffei for an insightful webinar designed for industry professionals, engineers and anyone interested in the manufacturing processes of PVC pipes. This session will provide a comprehensive understanding of the technology behind the production of high-quality PVC pipes: from raw material preparation to final product testing. Agenda: Introduction to PVC extrusion: overview of the basic principles of PVC pipe extrusion — including the process of melting and shaping PVC resin into pipe forms Equipment and machinery: detailed explanation of the key equipment involved — such as extruders, dies and cooling systems — and their roles in the extrusion process Process parameters: insight into the critical process parameters like temperature, pressure and cooling rates that influence the quality and consistency of the final PVC pipes Energy efficiency: examination of ways to save material and energy use when extruding PVC pipe products
While prices moved up for three of the five commodity resins, there was potential for a flat trajectory for the rest of the third quarter.
Supposedly, the classifications were updated back in 1996. More recently, there was an article in the August 19, 2021, edition of Plastics News mentioning that these standards are once again in the process of being updated by a team of industry leaders, association members and select members of the American Mold Builders Association. We should applaud their efforts to further improve this important document.
Implementing a production monitoring system as the foundation of a ‘smart factory’ is about integrating people with new technology as much as it is about integrating machines and computers. Here are tips from a company that has gone through the process.
Introduced by Zeiger and Spark Industries at the PTXPO, the nozzle is designed for maximum heat transfer and uniformity with a continuous taper for self cleaning.
technotrans says climate protection, energy efficiency and customization will be key discussion topics at PTXPO as it displays its protemp flow 6 ultrasonic eco and the teco cs 90t 9.1 TCUs.
Mixed in among thought leaders from leading suppliers to injection molders and mold makers at the 2023 Molding and MoldMaking conferences will be molders and toolmakers themselves.
A moldmaker’s objective is to maximize the performance of a mold to achieve the lowest possible total cost per part based on the intended lifespan of the project. That analysis should include the goal of minimizing the cost to maintain the mold. Therefore, when reviewing a new project, moldmakers will wisely ask:
This month’s resin pricing report includes PT’s quarterly check-in on select engineering resins, including nylon 6 and 66.
Say “manufacturing automation” and thoughts immediately go to the shop floor and specialized production equipment, robotics and material handling systems. But there is another realm of possible automation — the front office.
This Knowledge Center provides an overview of the considerations needed to understand the purchase, operation, and maintenance of a process cooling system.
Sustainability continues to dominate new additives technology, but upping performance is also evident. Most of the new additives have been targeted to commodity resins and particularly polyolefins.
Multiple speakers at Molding 2023 will address the ways simulation can impact material substitution decisions, process profitability and simplification of mold design.
Personally, I have a passion for using thermally conductive materials, especially in hard-to-cool areas. Not because they are great at reducing cycle time, but because they are great at achieving uniform cooling. Non-uniform part cooling invites part warpage, and warped parts are often a rejectable condition. Table 2 gives approximate thermal-conductivity values for various mold materials. These values can vary widely depending on the manufacturer, heat treatment and operating temperature.
In this collection, which is part one of a series representing some of John’s finest work, we present you with five articles that we think you will refer to time and again as you look to solve problems, cut cycle times and improve the quality of the parts you mold.
Stork IMM has partnered with Valley Group Inc., Fishersville, Va., to provide machine installation and field service and maintenance support for Stork IMM’s existing and new customers. “This partnership will ensure blanket support across the U.S. for all our customers,” said Boers. The company’s 2500-m2 facility includes spare parts, office, and warehouse space.
I have already mentioned polishability, thermal conductivity, hardness and corrosion resistance. But what about toughness, compressive strength, wear and abrasion resistance? These are important properties to consider as well, especially when two pieces of steel slide against each other, like a cam, lifter or shutoff. The old rule of thumb says that if different steel types are used and there is a 10-point Rockwell C differential between them, everything will be fine. That rule of thumb doesn’t always hold true—especially if the forces are high and the contact area is large. O-6 and A-10 steels are good for sliding applications because these two steels have high concentrations of graphitic particles in their microstructure. O-1, O-2, D-2 and S-1 are also good steel types for sliding applications.
Wear and galling explain why there has been a lot of attention given to various surface coatings and surface treatments, as well as the metallurgical compatibility of different types of mating steels.
Driven by brand owner demands and new worldwide legislation, the entire supply chain is working toward the shift to circularity, with some evidence the circular economy has already begun.
Successfully starting or restarting an injection molding machine is less about ticking boxes on a rote checklist and more about individually assessing each processing scenario and its unique variables.
Mike Sepe has authored more than 25 ANTEC papers and more than 250 articles illustrating the importance of this interdisciplanary approach. In this collection, we present some of his best work during the years he has been contributing for Plastics Technology Magazine.
Toughness, which is basically a combination of strength and ductility, is important for tall, free-standing cores, as well as cavities with sharp inside corners where cracking from molding pressures is a concern. H-13 has very good toughness properties. S-7 is also good.
In this collection of content, we provide expert advice on welding from some of the leading authorities in the field, with tips on such matters as controls, as well as insights on how to solve common problems in welding.
While the melting process does not provide perfect mixing, this study shows that mixing is indeed initiated during melting.
3. What is the molding material? If it’s a corrosive resin, such as rigid PVC, the only good option is to make the mold out of stainless steel. I say the only good option because nickel and other coatings do not protect carbon steels from PVC gases for very long. If you think that stainless is too expensive, consider the cost to remove the worn or flaking plating, re-polishing the cores and cavities and then re-plating the mold.
4. Is there a dimensioned 2D drawing of the part? I have seen too many jobs quoted strictly based on a 3D CAD model. CAD models do not specify the tolerances for critical dimensions. Nor do they specify the surface finish, aesthetic areas that cannot have gate or ejector-pin marks, secondary operations, mating parts, etc. 2D drawings almost always help the moldmaker decide the best way to design and build a mold—or if the part is even moldable to the stated specifications.
A very common cause of mold damage is due to galling. When two pieces of steel rub or slide against each other, there is a risk of them metallurgically bonding together. You can usually hear the components squeaking shortly before they seize up. Galling can occur at any time—from the initial mold sampling up to 1 million cycles later. Everyone from the machine operator to the plant manager should be aware of what this sound means. Recognizing a galling situation early can reduce the amount of mold damage.
Second quarter started with price hikes in PE and the four volume engineering resins, but relatively stable pricing was largely expected by the quarter’s end.
Stork IMM’s personnel hires have held leadership roles at some of the world’s leading machine and converting companies. Kotzeff, based in California, has worked in key account manager roles at both Husky Injection Molding Systems and Sidel Inc. Most recently, he worked as a consultant with packaging companies including Rplanet, Power Hydration, and INOSIP. He holds a Bsc Engineering-Mechanical degree from the University of Guelph.
Ultradent's entry of its Umbrella cheek retractor took home the awards for Technical Sophistication and Achievement in Economics and Efficiency at PTXPO.
Mold maintenance is critical, and with this collection of content we’ve bundled some of the very best advice we’ve published on repairing, maintaining, evaluating and even hanging molds on injection molding machines.
Molnar, based in Toronto, was formerly president of Molding Excellence (TM) Inc. in Toronto and has held leading roles in executive management, business development, and coaching/mentoring with leading companies in injection moulding, hot runners, automation, and mould cooling. Molnar has served in key leadership positions at RJG Inc, Mold-Masters, and Husky Injection Molding Systems. He holds a Bachelor of Science in mechanical engineering from the University of Waterloo, and an MBA from the Wilfrid Laurier University.
Join Wittmann for an engaging webinar on the transformative impact of manufacturing execution systems (MES) in the plastic injection molding industry. Discover how MES enhances production efficiency, quality control and real-time monitoring while also reducing downtime. It will explore the integration of MES with existing systems, emphasizing compliance and traceability for automotive and medical sectors. Learn about the latest advancements in IoT and AI technologies and how they drive innovation and continuous improvement in MES. Agenda: Overview of MES benefits What is MES? Definition, role and brief history Historical perspective and evolution Longevity and analytics Connectivity: importance, standards and integration Advantages of MES: efficiency, real-time data, traceability and cost savings Emerging technologies: IoT and AI in MES
5. Is there a target price for the molded part? This is a common question for thin-walled and commodity parts, such as caps and closures, where cycle time is critical and the need for a hot-runner system is paramount. High-thermal-conductivity materials such as copper alloys may be required. Unfortunately, too few moldmakers ask this question—unless they are also going to be the molder.
Figure 1 shows a cavity set for a toy soldier. It was made in 1955 by hobbing blocks of copper. Hobbing is a manufacturing method rarely used today. Non-alloyed copper is also rarely used today because it is extremely soft. The figurine in Fig. 2 (left) was originally molded out of PS. The figurine in Fig. 2 (right) was cast out of liquid silicone material a few weeks ago on my desk. There’s a little flash on the cast part, but the “clamp pressure” was only about 10 lb—generated by a few rubber bands. The point is that part geometry is where it all begins, and oftentimes, defines when it all ends.
August 29-30 in Minneapolis all things injection molding and moldmaking will be happening at the Hyatt Regency — check out who’s speaking on what topics today.
Learn about sustainable scrap reprocessing—this resource offers a deep dive into everything from granulator types and options, to service tips, videos and technical articles.
Proper steel selection plays a critical role in the longevity of a mold. Most moldmakers have their “go-to” types, such as 1030 or 4130 for the mold base and P-20, 420 or H-13 for the cavities and cores. 1030 and 4130 are good steel types for mold bases, but if the project needs to last for several years, or if the water quality in the molding facility is prone to calcium deposits, the mold base should be electroless nickel plated.
Some of the common causes for a mold’s decreased longevity are due to accidents on the production floor. The folks in the trenches describe such events as “crashes.” One of the most common crashes involves a cam that is out of position—usually after cleaning the parting line or removing a part, or simply because the cam retention device was too weak, and the cam slid out of position. When a cam is out of position, the angle pin does not line up with the hole in the cam and then—crash—it snaps like a twig. If the angle pin hits the top of the cam, it’s usually not a big deal. Simply replace the pin. But if it hits any cavity impression, that’s going to end the production run and cost a lot more to repair. Another common type of crash is handling a mold with one eyebolt and no safety strap. An unsecured mold half can easily hit the ground well before you can yell “Look out!”
Across the show, sustainability ruled in new materials technology, from polyolefins and engineering resins to biobased materials.
Plastics Technology’s Tech Days is back! Every Tuesday in October, a series of five online presentations will be given by industry supplier around the following topics: Injection Molding — New Technologies, Efficiencies Film Extrusion — New Technologies, Efficiencies Upstream/Downstream Operations Injection Molding — Sustainability Extrusion — Compounding Coming out of NPE2024, PT identified a variety of topics, technologies and trends that are driving and shaping the evolution of plastic products manufacturing — from recycling/recyclability and energy optimization to AI-based process control and automation implementation. PT Tech Days is designed to provide a robust, curated, accessible platform through which plastics professionals can explore these trends, have direct access to subject-matter experts and develop strategies for applying solutions in their operations.
The yield strength of P-20 steel is about 125,000 psi. The yield strength of 1030 and 4130 steel is about 64,000 psi. This equation doesn’t even include the added force applied to the debris due to the closing speed and momentum of the moving platen. Figure 3 shows what gate flakes can do to a mold when the applied pressure is considerably greater than the yield strength of the steel.
In a time where sustainability is no longer just a buzzword, the food and beverage packaging industry is required to be at the forefront of this innovation. By adopting circular packaging processes and solutions, producers can meet regulatory requirements while also satisfying consumer demand and enhancing brand reputation. Join Husky to learn more about the broader implications of the circular economy — as well as how leading brands are leveraging this opportunity to reduce costs, increase design flexibility and boost product differentiation. Agenda: The cost and operational benefits of embracing circularity Key materials in circular packaging — including rPET and emerging bioplastics How to design a circular food and beverage package Strategies for selecting sustainable closures to future-proof packaging solutions Optimization and streamlining of production processes for enhanced efficiency How Husky Technologies can enable your sustainable success
There are many factors that determine the longevity of a mold. Part complexity, which dictates mold complexity, is probably the biggest factor. A mold that produces a flowerpot, 5-gal bucket or a Frisbee can last a very long time. But more complex molds, such as those with cam action, unscrewing mechanisms, collapsible cores, contoured parting lines, sliding shutoffs, etc., will not last nearly as long because there are more component parts that can wear, break, gall, or seize. Just because a mold is made of heat-treated tool steel doesn’t mean it’s going to pump out hundreds of thousands of parts.
Plastics Technology covers technical and business Information for Plastics Processors in Injection Molding, Extrusion, Blow Molding, Plastic Additives, Compounding, Plastic Materials, and Resin Pricing. About Us
Compounders face a number of processing challenges when incorporating a high loading of low-bulk-density mineral filler into polyolefins. Here are some possible solutions.
While the major correction in PP prices was finally underway, generally stable pricing was anticipated for the other four commodity resins.
To properly understand the differences in performance between PET and PBT we need to compare apples to apples—the semi-crystalline forms of each polymer.
In this collection of articles, two of the industry’s foremost authorities on screw design — Jim Frankand and Mark Spalding — offer their sage advice on screw design...what works, what doesn’t, and what to look for when things start going wrong.
Processors with sustainability goals or mandates have a number of ways to reach their goals. Biopolymers are among them.
ABOUT THE AUTHOR: Jim Fattori is a third-generation molder with more than 40 years of experience in engineering and project management for custom and captive molders. He is the founder of Injection Mold Consulting LLC in Pennsylvania. Contact: jim@injectionmoldconsulting.com; injectionmoldconsulting.com
The thickness of the molded part is important when it comes to selecting the best material out of which to make the cavities and cores. If the part is thin-walled, selecting a material with extremely high thermal conductivity may not be the best choice. The material can solidify too quickly during injection, and you can end up with a lot of short shots or injection pressures that exceed the machine’s capabilities. Conversely, if the part is extremely thick, the thermal conductivity of the cavity and core material is not nearly as important because the molded part forms an exterior skin, which acts as an insulating barrier. That’s why a graph of cooling time vs. wall thickness is not a straight line. It is an upwardly projecting curve.
2. What is the part used for? If it’s a medical, optical or automotive part, there’s a very good chance that the mold is required to be made of ESR (electroslag reduction) stainless steel for cleanroom conditions and optical polishing or mold texturing.
Gifted with extraordinary technical know how and an authoritative yet plain English writing style, in this collection of articles Fattori offers his insights on a variety of molding-related topics that are bound to make your days on the production floor go a little bit better.
GETTING A QUOTE WITH LK-MOULD IS FREE AND SIMPLE.
FIND MORE OF OUR SERVICES:
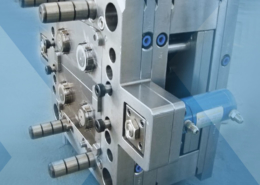
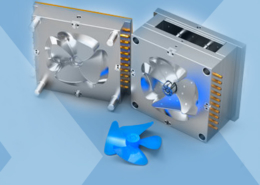
Plastic Molding

Rapid Prototyping
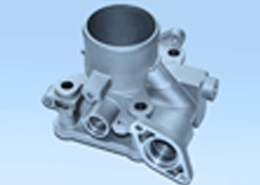
Pressure Die Casting
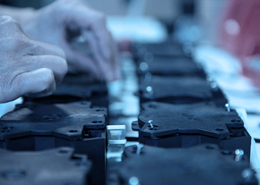
Parts Assembly
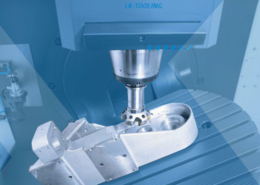