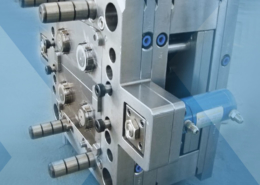
Fictiv Launches Nearshoring Solution for Production Injection Molding - molding
Author:gly Date: 2024-09-30
Plasdan’s end-to-end automated cycle moves products quickly through the cycle, eliminating the cost of unfinished work-in-process inventory. The company’s multi-injection molding solutions ultimately save operating costs and reduce environmental impact.
During live demos at Nissei America’s booth at NPE2024, Plasdan will discuss with attendees how they can integrate the company’s solutions into existing manufacturing setups. The demo will feature two add-on Ergoline injection units, which Plasdan designed in a slim footprint to overcome assembly constraints. These units can be mounted angular on tool, vertical on a fixed platen, or horizontal on the non-operator side.
As well as being well on track to becoming carbon neutral, Bloom-in-Box is well-placed to expand its garden, scoops and measures ranges and to develop new medical and PPE products.
“When the equipment starts to decelerate and the motor is no longer required to drive a process, it automatically switches to being a generator, feeding the electricity that is generated back through the system to another location on the machine where it is needed,” said Raine.
Plasdan’s equipment will be integrated with a Nissei NEX360V-100LE all-electric molding machine to function in a single cycle — without the need for multiple machines or manual assembly. The setup reduces machine time, labor and energy requirements, and uses less floor space.
“Our goal at Bloom-in-Box is to become carbon neutral over the next 12-18 months. We have been working with all-electric machines for the last 20 years to reduce power consumption and emissions. Solar installations and our new Fanuc Roboshot were the next steps to achieving this. Thanks to these latest investments, our current carbon emissions as a business are estimated to be less than 10 tonnes of CO2 per year, with our ultimate goal to achieve net zero,” said Tom Reardon, production coordinator and robotics engineer at Bloom-in-Box.
“We build our own [servo drives], meaning they are as energy efficient as is physically possible. This also enables us to specify servo drives that are the perfect match for each machine’s target performance, ensure they deliver exactly the amount of power to the motor that it needs,” said David Raine, Roboshot sales manager UK and Ireland.
The 150T clamp force Roboshot S150iA in operation at Bloom-in-Box runs at 2.9-3kW per hour for a six-second cycle (the longer the cycle the less energy consumed), reducing energy consumption by 20% versus previous generation electric machines in the plastic processor’s fleet.
Following its investment in a Fanuc Roboshot injection moulding machine, eco-conscious plastic products manufacturer Bloom-in-Box says it is well on the way to becoming carbon neutral. By means of servo technology and ‘intelligent power regeneration’ capabilities, the Roboshot S150iA installed at Bloom-in-Box’s Burscough facility uses 3kW per hour, permitting it to be powered exclusively by renewable solar energy.
Geoff Giordano is a tech journalist with more than 30 years’ experience in all facets of publishing. He has reported extensively on the gamut of plastics manufacturing technologies and issues, including 3D printing materials and methods; injection, blow, micro and rotomolding; additives, colorants and nanomodifiers; blown and cast films; packaging; thermoforming; tooling; ancillary equipment; and the circular economy. Contact him at [email protected].
The plastic injection molding system from Plasdan with an integrated Nissei press reduces cycle times and labor and energy requirements.
In addition, the Roboshot’s power regeneration feature enables intelligent energy recovery: when an axis decelerates, energy returns to the power source, adding to the overall savings.
Nissei touts its NEX-V series and its “N-Constellation” IoT technology as turning the injection molding machine into a network hub that connects auxiliary equipment and collects real-time operation data.
Bloom-in-Box has been involved in injection moulding for more than 20 years and has always been an advocate of electric moulding machines on the basis that they use up to 80% less energy than their hydraulic counterparts. When significant growth meant the company had reached maximum production capacity last year, it took the decision to invest in a new electric machine that would enable it to increase capacity by 25-40%.
Therefore, when it came to deciding which injection moulding machine to invest in, Bloom-in-Box wanted this machine purchase to support its carbon emission reduction ambitions and to be powered exclusively by the new solar panels.
At the same time, the company had embarked on a roadmap to become carbon neutral, starting with an assessment of its carbon footprint. This revealed electricity accounted for 95% of its total carbon emissions. To address this situation, in November 2021, Bloom-in-Box installed a 40kWp solar system that feeds directly into the factory. During daylight hours this generates on average 10kW per hour, with the potential to produce even more electrical energy during the summer months.
“We had reached a plateau. Our older machines were slower, causing production bottlenecks, and lacked the precise temperature control needed for working with biodegradable plastics,” said David Reardon, director of Bloom-in-Box.
“This system represents a significant leap forward in injection molding technology,” said Plasdan CEO Paulo Silva. “It delivers efficiency gains and productivity improvements, crucial for manufacturers aiming to optimize their operations and minimize environmental impact. The single-machine approach not only cuts operational costs but also supports the industry's move toward more sustainable practices.”
See Plasdan’s equipment at Nissei America’s booth, W2401, at NPE2024 at Orlando’s Orange County Convention Center from May 6 to 10.
Bloom-in-Box is a third-generation, family-run plastic injection moulding business focused on designing and moulding recyclable products from recycled materials. In 2018 Bloom-in-Box earned a place in the final of Best Recycled Plastic Product of the Year for its Bloomie floristry box. The Bloomie is made from 99% recycled material and is 100% recyclable. Any boxes that mould incorrectly are chopped up, passed through a grinder and made into security spikes. Other products made by the business include laundry pegs, scoops and measures.
Fanuc says the machine's energy efficiency is attributed to a combination of Fanuc’s proprietary servo technology and smart energy recovery.
A three-material molding system from Plasdan will demonstrate the production of complex assemblies with two add-on injection units and in-mold robotics at NPE2024.
GETTING A QUOTE WITH LK-MOULD IS FREE AND SIMPLE.
FIND MORE OF OUR SERVICES:
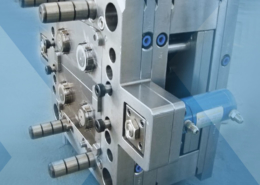
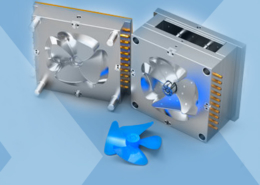
Plastic Molding

Rapid Prototyping
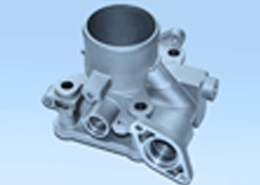
Pressure Die Casting
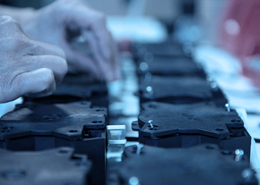
Parts Assembly
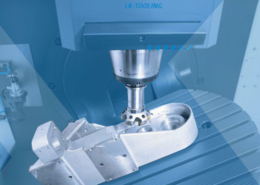