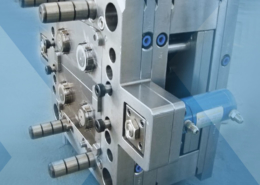
Feed-Throat Temperature Control - plastic granules for injection molding
Author:gly Date: 2024-09-30
When you’re done learning about mold design, you’ll be itching to build your own injection mold machine. Precious Plastic’s tutorial looks dead simple, but this machine looks a little more capable. And why CNC your molds when you can just 3D print them?
3D printing has made one off designs cheaper and that’s been a huge change. Smaller CNC machines (including lasers) have helped make the shorter run or makerspace types of idea evolution easier. But injection molding is something I really have not seen become easier or cheaper to do much at all, despite well over a decade of work by a great number of people. It’s something that needs to work right, be cheap and the downside of it needing to produce five figures of something to break even but once that’s done, the price per unit is almost trivial. It’s like ill informed people saying they would 3D print things like disposable cutlery or cups because they fail to understand any of the details about how 3D printing or injection molding actually work.
While the major correction in PP prices was finally underway, generally stable pricing was anticipated for the other four commodity resins.
Uhh. There are plenty of reasons why a fairly complex mold couldn’t be produced by the home gamer. They would have to already have high end CNC equipment and knowledge of how to use it just to start with, even if you set aside the mold design software part of thing and started with finished CAD drawings.
Join KraussMaffei for an insightful webinar designed for industry professionals, engineers and anyone interested in the manufacturing processes of PVC pipes. This session will provide a comprehensive understanding of the technology behind the production of high-quality PVC pipes: from raw material preparation to final product testing. Agenda: Introduction to PVC extrusion: overview of the basic principles of PVC pipe extrusion — including the process of melting and shaping PVC resin into pipe forms Equipment and machinery: detailed explanation of the key equipment involved — such as extruders, dies and cooling systems — and their roles in the extrusion process Process parameters: insight into the critical process parameters like temperature, pressure and cooling rates that influence the quality and consistency of the final PVC pipes Energy efficiency: examination of ways to save material and energy use when extruding PVC pipe products
A few questions for you then: – what happened to the mold? (do they keep it or ship it to you or destroy it?) – how did the initial run work, they sent prototypes or someone had to travel to China? – what material did you use? – who designed/”debugged” the mold? (certain features are hard/impossible to or significantly increase the cost, so the design of the part tends to be optimised)
I would agree with you there. But SLS is still a slow and somewhat expensive process. It’s nice for custom quantity of maybe one to perhaps a few dozen parts. Maybe a few more. But it’s certainly not cheap nor quick and it is never going to compete with injection molding if you need greater quantities. It can certainly make sense if the parts are simply no longer available though and the market is somewhat limited in size.
3D printing is great for prototyping, and not bad for limited runs of parts. Unfortunately though it really doesn’t scale well beyond a few pieces, so when you’re ready for the mass market you will need to think about injection molding your parts. But something like that has to be farmed out, right? Maybe not, if you know a thing or two about designing your own injection molds.
The small mold pictured in the video is…well…small… and made of aluminium, so there should be a lot more shops to choose from, possibly even “western” ones, if you’re willing to spend around $500 for it…
Second quarter started with price hikes in PE and the four volume engineering resins, but relatively stable pricing was largely expected by the quarter’s end.
The cost of a mold rarely makes sense for small batch parts, and designs normally include the maximum number of part copies possible specific to a factory machine’s per-injection-cycle (the time limiting factor).
hmmmm… everybody seems to be forgetting one thing. I’m sure that for most people around here, at least for me, there is the following problem:
Looking at the site, I would recomend looking at their shredder design, very DIY-friendly… the screw extruder looks reasonable as well, provided they’ll be able to supply the screw at the advertised €250 a piece…
Let’s do the math. The initial block has to be degassed (H2), so that there aren’t any voids during machining. The blocks have to be machined to very tight tolerances. Once both of these things are done, you’ve still got to contend with a limited number of shots based upon mold wear. Let’s be very friendly, and suggest a few hundred dollars for a block of good aluminum, a thousand for machining time and finishing, with an overall cost of $1500 once the press apparatus is constructed. If you sell each case at $3, and a profit of $2, that means without labor you break even at 750 cases. Factor in finishing labor, and you might break even at 1000 cases sold. I’m being generous on the estimation of a lot here.
When I was a young pup, I made a HO slot car chassis, similar to a Aurora car by making a mold from aluminum plates that I machined on a Bridgeport mill in my high school shop. The design was made on paper. This was before CNC existed, or CAD programs for that matter. I had lots of threaded holes to force the mold sections apart and I had to cut flash off in places. The shop had a simple injection mold machine that could shoot Nylon. I could get the mold to fill more reliably by heating it in an oven before placing in the mold machine. No, the mold was not as nice as the one in the video, but the final part looked better than what I see 3D printed today. I only say this to encourage people. Even if you don’t have a mill, a mold can be machined with a drill press and files. The accuracy is whatever you find your hands capable of doing.
Why should anyone give a crap about what I say? This is an exercise in technology, right? All of DYI is bespoke, and thus better than buying enmasse.
After successfully introducing a combined conference for moldmakers and injection molders in 2022, Plastics Technology and MoldMaking Technology are once again joining forces for a tooling/molding two-for-one.
Join this webinar to explore the transformative benefits of retrofitting your existing injection molding machines (IMMs). Engel will guide you through upgrading your equipment to enhance monitoring, control and adaptability — all while integrating digital technologies. You'll learn about the latest trends in IMM retrofitting (including Euromap interfaces and plasticizing retrofits) and discover how to future-proof your machines for a competitive edge. With insights from industry experts, it'll walk you through the decision-making process, ensuring you make informed choices that drive your business forward. Agenda: Maximize the value of your current IMMs through strategic retrofitting Learn how to integrate digital technologies to enhance monitoring and control Explore the benefits of Euromap interfaces and plasticizing retrofits Understand how retrofitting can help meet new product demands and improve adaptability Discover how Engel can support your retrofitting needs, from free consultations to execution
While prices moved up for three of the five commodity resins, there was potential for a flat trajectory for the rest of the third quarter.
Resin drying is a crucial, but often-misunderstood area. This collection includes details on why and what you need to dry, how to specify a dryer, and best practices.
You can have stuff machined in China, even to reasonable tolerances and finish while being reasonably priced… the mold looks like it’s from aluminum (judging not only by the look, but also by the way they handle the completed mold, steel would not be so light to to move around like that), so the machining shouldn’t be all that expensive.
THINGS ARE NEVER RIGHT THE FIRST TIME!! Therefore you must be willing to go through multiple iterations of your project, be prepared to accept this OR outsource the entire project to professionals and let them reduce the risks, in the end the results will be more professional. Which is the look you are looking for when going through all the trouble of injection molding. Though I could be wrong (I have that a lot).
-It depends on your agreement with the company. If you specify that the mold is for export, it will cost more. If you specify that it will stay there, then they’ll give you a cheaper price because they’re making up the rest by making your parts for you. Usually they’ll store your mold for you when not in use up to a certain amount of time, and then they’ll destroy it if you don’t order any more parts. If you had it made for export, they’ll ship it to you, but if you didn’t, then they have no reason to give it back. -The mold quote usually involves two sets of samples, which they will send to you by air; first the unfinished version, to make sure all the dimensions are correct. Once that is accepted, then they’ll put the surface finish on and send you a second sample. -You’ll have to specify the material from the beginning because they account for plastic shrinkage when they cut the mold (so the mold will actually be a couple % larger than the final part dimensions). Common materials are ABS, PP, PS, acrylic, there’s lots. You’ll also have to specify the color and any additives required (like UV stabilizers or flame retardant). -After the quote and before they cut the mold, their engineers will look at the part and start designing the mold. They’ll send you a document with lots of pictures and arrows that say “need radius here” “2 degree draft here”, etc. You’ll make the changes to the mold and negotiate with them. They’ll also tell you where the parting line is, where the gate is, the ejector pins, etc. You can negotiate this as well, but their recommendations are usually best. There have been times where I had to have a snap feature onto another part but I couldn’t prototype properly to figure out the dimensions for best snap, so I sent them the thing it had to snap on to. They cut the mold appropriately, then removed metal until it snapped properly. That avoided a bunch of shipping for experimentation.
Plastics Technology covers technical and business Information for Plastics Processors in Injection Molding, Extrusion, Blow Molding, Plastic Additives, Compounding, Plastic Materials, and Resin Pricing. About Us
In this three-part collection, veteran molder and moldmaker Jim Fattori brings to bear his 40+ years of on-the-job experience and provides molders his “from the trenches” perspective on on the why, where and how of venting injection molds. Take the trial-and-error out of the molding venting process.
Additive technology creates air pockets in film during orientation, cutting down on the amount of resin needed while boosting opacity, mechanical properties and recyclability.
Formnext Chicago is an industrial additive manufacturing expo taking place April 8-10, 2025 at McCormick Place in Chicago, Illinois. Formnext Chicago is the second in a series of Formnext events in the U.S. being produced by Mesago Messe Frankfurt, AMT – The Association For Manufacturing Technology, and Gardner Business Media (our publisher).
As others have said, injection molding is stupid. It’s a technology meant to have a large initial investment, with payback from consistent quality and large production volumes. This entire article glorifies using a tractor trailer to drive an impaired person throughout an airport. The right tool is an electric cart, but because the tractor trailer can still do the job it’s an…interesting proof of concept.
From a design perspective, let’s note only the big stuff. 1) Where’s the parting line? You need to vent mold gasses, but there’s no mention of this at all. A highly pressurized chamber is a recipe for disaster. 2) Awful materials. Maybe this is the point, but the products in question appear to have more splay than reasonable, and they seem to be rather brittle. Reclaimed material can be quite strong, but only when controlled. 3) That gate. You’ve got a cosmetic piece, and put the gate in the center of the largest uninterrupted surface. The better design would be two fan gates on the sides or bottom/top, with design work being done to make sure flow fronts properly knit (assuming that tonnage couldn’t be applied to use a single gate). Less gate trim, better aesthetics, and an order of magnitude more difficult than a single flow calculation. 4) Lack of flexibility. Shot volume is determined by the preloaded material. Cost is prohibitively high on a gigantic finely machined block. Time to creation is just nuts, namely mold design relies upon relatively wide finish tolerances and conditions.
While the melting process does not provide perfect mixing, this study shows that mixing is indeed initiated during melting.
PMT is an ISO 9001, ISO 14001 and IATF 16949-certified manufacturer of precision-engineered, injection molded plastic components. The business was founded in 1973 by Charles E. Sholtis, father to Charles A. Sholtis, former CEO who will remain as an advisor to the business under Tide Rock. In 1973, the company began life as Prototype Molding Co. and was based in Bridgeport, Conn. In 2001, PMT opened a satellite facility in El Paso, and eventually it completely shifted operations to Texas in 2004.
Seriously, please don’t do this. The entire exercise is stupid. It demonstrates an interesting capability, but not a thoughtful one. Injection molding is awesome, for high volume parts. Using it like this is fundamentally not understanding the technology, Please, please, stop doing this. Seriously, “because I can” is not a justification. If you are doing enough volume to justify injection molding you shouldn’t be running reground random bits (seriously, moisture readings matter). Either choose a process that fits the scope of production, or admit this is insane.
Introduced by Zeiger and Spark Industries at the PTXPO, the nozzle is designed for maximum heat transfer and uniformity with a continuous taper for self cleaning.
Join Engel in exploring the future of battery molding technology. Discover advancements in thermoplastic composites for battery housings, innovative automation solutions and the latest in large-tonnage equipment designed for e-mobility — all with a focus on cost-efficient solutions. Agenda: Learn about cutting-edge thermoplastic composites for durable, sustainable and cost-efficient battery housings Explore advanced automation concepts for efficient and scalable production See the latest large-tonnage equipment and technology innovations for e-mobility solutions
Exhibitors and presenters at the plastics show emphasized 3D printing as a complement and aid to more traditional production processes.
As far as I am concerned the second anything is modelled in solidworks it is not homegamer stuff. Pisses me off when people give tutorials using software that costs 4000usd per seat about things that if you have a licence for you can do in your sleep. What’s the point.
In a release, Sholtis said he hopes to work with Tide Rock on building off what PMT has created. “I look forward to having the ability to expand our capabilities and capacity as a Made-in-USA manufacturer,” Sholtis said. The spokesperson noted that Sholtis and Engler are in the process of evaluating what investment needs PMT might require in infrastructure, equipment and people to continue to grow.
Processors with sustainability goals or mandates have a number of ways to reach their goals. Biopolymers are among them.
Gifted with extraordinary technical know how and an authoritative yet plain English writing style, in this collection of articles Fattori offers his insights on a variety of molding-related topics that are bound to make your days on the production floor go a little bit better.
In a time where sustainability is no longer just a buzzword, the food and beverage packaging industry is required to be at the forefront of this innovation. By adopting circular packaging processes and solutions, producers can meet regulatory requirements while also satisfying consumer demand and enhancing brand reputation. Join Husky to learn more about the broader implications of the circular economy — as well as how leading brands are leveraging this opportunity to reduce costs, increase design flexibility and boost product differentiation. Agenda: The cost and operational benefits of embracing circularity Key materials in circular packaging — including rPET and emerging bioplastics How to design a circular food and beverage package Strategies for selecting sustainable closures to future-proof packaging solutions Optimization and streamlining of production processes for enhanced efficiency How Husky Technologies can enable your sustainable success
technotrans says climate protection, energy efficiency and customization will be key discussion topics at PTXPO as it displays its protemp flow 6 ultrasonic eco and the teco cs 90t 9.1 TCUs.
Though the business model is what I think is the last bit to get this project a break trough. Ther is little to no money in it as the normal people will continue to buy bowels made for cents. It’s like ‚third world shops‘ where only wealthy and idealistic people are willing to buy their stuff. What I think is needed is something that would even make the big guys interested in recycled plastic. But if they continue to optimize their processes and machines and get the word out, they could enable a huge number of people to be the first in that rising industry of recycled from plastic waste products.
The only advice the guy could tolme is to make a steel frame to avoid the resin to be crushed by the pressure of the injector
Across the show, sustainability ruled in new materials technology, from polyolefins and engineering resins to biobased materials.
When, how, what and why to automate — leading robotics suppliers and forward-thinking moldmakers will share their insights on automating manufacturing at collocated event.
Sustainability continues to dominate new additives technology, but upping performance is also evident. Most of the new additives have been targeted to commodity resins and particularly polyolefins.
Join Wittmann for an engaging webinar on the transformative impact of manufacturing execution systems (MES) in the plastic injection molding industry. Discover how MES enhances production efficiency, quality control and real-time monitoring while also reducing downtime. It will explore the integration of MES with existing systems, emphasizing compliance and traceability for automotive and medical sectors. Learn about the latest advancements in IoT and AI technologies and how they drive innovation and continuous improvement in MES. Agenda: Overview of MES benefits What is MES? Definition, role and brief history Historical perspective and evolution Longevity and analytics Connectivity: importance, standards and integration Advantages of MES: efficiency, real-time data, traceability and cost savings Emerging technologies: IoT and AI in MES
Basic injection molding is not that tough to do. Melt plastic and force it into a mold under pressure. Of course, your results are going to be limited without access to high end machines, tooling, and software, but the idea that you can’t do it without a five to six figure investment is false. Large, complex molds will probably always be out of reach for the home shop. I’ve seen guys make small parts with hand made molds and manual presses though. There are frequently some imperfections, but that doesn’t mean no one should try it. Just like everything else, you learn from your mistakes and try again. This is Hackaday after all.
Ultradent's entry of its Umbrella cheek retractor took home the awards for Technical Sophistication and Achievement in Economics and Efficiency at PTXPO.
The aim of this presentation is to guide you through the factors and the numbers that will help you determine if a robot is a smart investment for your application. Agenda: Why are you considering automation? What problems are you trying to solve? How and why automation can help Crunch the numbers and determine the ROI
Plastics Technology’s Tech Days is back! Every Tuesday in October, a series of five online presentations will be given by industry supplier around the following topics: Injection Molding — New Technologies, Efficiencies Film Extrusion — New Technologies, Efficiencies Upstream/Downstream Operations Injection Molding — Sustainability Extrusion — Compounding Coming out of NPE2024, PT identified a variety of topics, technologies and trends that are driving and shaping the evolution of plastic products manufacturing — from recycling/recyclability and energy optimization to AI-based process control and automation implementation. PT Tech Days is designed to provide a robust, curated, accessible platform through which plastics professionals can explore these trends, have direct access to subject-matter experts and develop strategies for applying solutions in their operations.
This Knowledge Center provides an overview of the considerations needed to understand the purchase, operation, and maintenance of a process cooling system.
Amazing work .. about as good as Social Impact technology gets. They have simple, well thought out machines and methods, and a corresponding business model that can work in countries with fairly modest infrastructure.
Successfully starting or restarting an injection molding machine is less about ticking boxes on a rote checklist and more about individually assessing each processing scenario and its unique variables.
Maybe somebody will start selling somewhat lower cost base molds that can support custom UV printed molds for people who want to do a few dozen test runs? It’s a somewhat more time consuming in the beginning hybrid possibility that has some merit for some applications but you will still need a full sized injection mold plus mold setup time at the very least.
5. The lip around the edge reduces overflow Flash, but allows air to escape as the cavity fills. These guys get a B- for the video ad, and a F- for suggesting it is easy to improvise these designs.
Mold maintenance is critical, and with this collection of content we’ve bundled some of the very best advice we’ve published on repairing, maintaining, evaluating and even hanging molds on injection molding machines.
Tide Rock Holdings (Cardiff-by-the-Sea, Calif.) is continuing its acquisition streak, purchasing Plastic Molding Technology (PMT), a full-service precision injection molding company located in El Paso, Texas. PMT joins Colorado-based molders Pikes Peak Plastics and Altratek as portfolio holdings in a new plastics injection molding company that serves the industrial, energy, electronics, medical, telecommunications and automotive industries.
Students have access to the finest tools available in industry, Autodesks fusion 360 is free for home users and small startups and could quite possible become way better then Solidworks in just a few years. Open Source Tools are getting better and better. So, just wait a little longer :)
Now, let’s do some other math. A silicon mold costs a few dollars. It’s a few hours of effort to create a positive, that the silicon negative can be used with. I continue to make the silicon negative from the positive, creating a small initial investment of labor. The same exact product can sell for $3, with a $1 profit. Rounding up, maybe 50-100 parts made this way would break even on production monetary investments.
Although these guys referral service is interesting, there is always something to be learned by talking directly with tool and die makers.
This month’s resin pricing report includes PT’s quarterly check-in on select engineering resins, including nylon 6 and 66.
1. Molten plastic is nasty stuff, at minimum both gloves and a full face shield should be worn (burns look similar to napalm victims).
Tide Rock’s broader plastics manufacturing and electro-mechanical contract manufacturing portfolio also includes Interconnect Solutions Company (Fountain Valley, Calif.) and Plastics Design and Manufacturing (Centennial, Colo.) and it will be led by Michael Engler, Group CEO. In a release, Engler said the PMT acquisition expands its highly skilled workforce and brings it to a total of 95 molding machines ranging in clamp force from 20 to 500 tons.
August 29-30 in Minneapolis all things injection molding and moldmaking will be happening at the Hyatt Regency — check out who’s speaking on what topics today.
While prices moved up for three of the five commodity resins, there was potential for a flat trajectory for the rest of the third quarter.
For test runs, the mold halve generic cavity are usually a truncated chamfered pyramid shape to prevent the epoxy dies jamming in the cavity or cracking under pressure changes. For small <3" molds, the generic designs are usually a 1/2" to 2" thick walled structural aluminum box (expect $30 for the metal, and $200 for a machinist to rough it out on a mill).
Determining the source of streaking or contamination in your molded parts is a critical step in perfecting your purging procedures ultimately saving you time and money.
Mike Sepe has authored more than 25 ANTEC papers and more than 250 articles illustrating the importance of this interdisciplanary approach. In this collection, we present some of his best work during the years he has been contributing for Plastics Technology Magazine.
Across all process types, sustainability was a big theme at NPE2024. But there was plenty to see in automation and artificial intelligence as well.
To date, Tide Rock’s investments have targeted the western U.S., but a company spokesperson said its purchase of CableMaster Corp. has extended its presence into the Midwest. “The reason for that focus is that we’re looking for synergies and addressing what our customers need,” the spokesperson said, “and the locations in Colorado and Texas are strategic for us.”
The Plastics Industry Association (PLASTICS) has released final figures for NPE2024: The Plastics Show (May 6-10; Orlando) that officially make it the largest ever NPE in several key metrics.
In this collection of articles, two of the industry’s foremost authorities on screw design — Jim Frankand and Mark Spalding — offer their sage advice on screw design...what works, what doesn’t, and what to look for when things start going wrong.
By using our website and services, you expressly agree to the placement of our performance, functionality and advertising cookies. Learn more
3. Heating the mold to just below the plastics melting temperature is highly recommended. Even pro shops will usually toss the initial few cycles as the machine warms up to operating temperatures. The surface texturing and 2mm thick limit for the article’s cold process means these guys need to do a bit more research.
Mixed in among thought leaders from leading suppliers to injection molders and mold makers at the 2023 Molding and MoldMaking conferences will be molders and toolmakers themselves.
A few years ago we took out first steps to have a 2-part wall mount type enclosure (3.5″ x 5″ x 1.25″) injection molded in China and the results were amazing. The mold cost (using NAK80 Steel) was about $4000 USD… and the parts cost was about $0.50 each for 2000 pieces… This translated to an amortized cost of about $3 USD per unit… over the initial 2000 units… which was cheap given that it was a custom design and looked perfect! The total time from design submital to actually having parts was 6 weeks (including Ocean shipping).
Thousands of people visit our Supplier Guide every day to source equipment and materials. Get in front of them with a free company profile.
I am looking for someone who can make me a aluminum Mold for fishing… slow fall, I have a picture for a copy, is this company capable of doing it, I would love one to be done.
4. Epoxy composite injection molds require no machining, and are good for 800+ pieces. Aluminum is usually good for 8000+pcs, and EDM carbon steel can handle over 50000+pcs.
Take a deep dive into all of the various aspects of part quoting to ensure you’ve got all the bases—as in costs—covered before preparing your customer’s quote for services.
That all said, if there are any examples that people know about regarding injection molding becoming cheaper or more home friendly and want to share, please do so! I would really like for that to change, I just haven’t seen much progress on that front at all. Despite the somewhat poorly researched or hyper inflated promises by the author. Yes, you can sort of 3D print some injection molds. On $100,000 printers. The molds might last for a dozen or two runs and the molds cost at least several hundred dollars and take 20+ hours to print. It works great as a final test before committing to a five figure mold run but it’s hardly a replacement. Sorry, but 3D printing is not exactly a viable alternative to CNC machining a proper mold.
Say “manufacturing automation” and thoughts immediately go to the shop floor and specialized production equipment, robotics and material handling systems. But there is another realm of possible automation — the front office.
Discover how artifical intelligence is revolutionizing plastics processing. Hear from industry experts on the future impact of AI on your operations and envision a fully interconnected plant.
Setting aside the fact that you have to design a proper mold as well as deal with all of the other nuances of injection molding plastic, hand-waving this and just saying it can be done with a 3D printer is not just inaccurate but unprofessional.
That all said, I would really like it if injection molding were to become easier to do and much less expensive. But unlike a mill, CNC molding doesn’t really scale down in the same way because the pressures involved don’t suddenly change when you scale things down, necessitating proper, high quality equipment that doesn’t really drop much in price unless you were to cut out basically everything and make it a few thousand dollars of nearly all manual work. At least the controls and such are getting easier to deal with and less expensive.
Core Technology Molding turned to Mold-Masters E-Multi auxiliary injection unit to help it win a job and dramatically change its process.
From a safety point, let’s check where we are. 1) Molten plastic degasses and lungs are prone to not liking those gasses. 2) Cold mold, hot plastic, and manual force; what could possibly go wrong? 3) Clamp tonnage. If you’ve never seen a mold blow out consider yourself lucky.
Despite price increase nominations going into second quarter, it appeared there was potential for generally flat pricing with the exception of a major downward correction for PP.
You don’t even know the entire processes they go through. This was merely a quick show of it being possible. Perhaps they have a process for pre treating their recycled materials or perhaps not. To simply make so many generalizations, malassumptions, and more or less a derogatory response to someone’s success is typical of those who are not the go getters in life and enjoy the narcissistic belittling of others who achieve beyond average individuals. It’s too bad you make these comments and yet go on a rant of excessive rudimentary thoughts that are essentially meaningless to the success of diy injection molding. I don’t recall that they suggested any intention of mass production and with the gingerly injection molding process it is meant as a hobby of sorts for the home brewer. Many like myself have needs for such device for small prototype or miniature production parts that could be done in a dozen small parts in one particular mold where the application is a low volume component to their home business where justification of outsourcing would not necessitate the actual demand. So suggesting to give up the thought or dream in developing that product they desire to potentially support their wives and children and afford that mortgage payment where spending tens of thousands filling a garage half full of useless excess is less than proper in terms of creating and/or launching a business venture or conceding an existing one or the mere desire for hobby experimenting. We’re the gentleman in the video using all aspects of safety? That’s less the point than to recommend to those interested to use common sense, wear eye protection, long sleeved gloves, and heavy boots. The point being is why not ravel in someone’s successes and make positive reinforced suggestions that actually improve the concept instead of pulling the rig from under the feet of a few potentially researching who may think you actually know what you’re talking about. I did injection molding for a living years back, never had a blowout on a 75 ton press, never lost a finger, nor a serious injury where pressures far exceed with risks than a simple hand lever requiring 500lbs of pressure ona fulcrum. Even if they had used a large pnuematic cylinder the same as I’d intend to use in achieving higher pressures being properly dressed and shielded is no more or less safe than sitting face first in front of the die having 75 tons of forced high temp polymer forced into it. Degassing? None of our dies had any type of ventilation in them however they did crack slightly apart when molding and ooze between the dies leaving a flashing that had to be filed off. Never once did it ever blow through and cause physical injury. Anyone who wants to do this I would further say donuour research and use proper safety measures and please by all means show us your finished project. Ingenuity is rare these days. I’m sure many would rather sit on the couch and bitch about others success and complain that they shouldn’t even ever consider approaching anything experimental and should be a lavish couch sloth the remainder of their lives leaving these experiments to the myth busters whil drinking beer and eating chips until they roll off a round ball at a ripe old age realizing the regrets had they only tried.
Learn about sustainable scrap reprocessing—this resource offers a deep dive into everything from granulator types and options, to service tips, videos and technical articles.
Multiple speakers at Molding 2023 will address the ways simulation can impact material substitution decisions, process profitability and simplification of mold design.
In this collection of content, we provide expert advice on welding from some of the leading authorities in the field, with tips on such matters as controls, as well as insights on how to solve common problems in welding.
Your typical home 3D printer certainly leaves a lot to be desired in terms of finish but get your designs printed on a commercial sls machine and the results are rather spectacular. I know of a few parts now been made this way in low volumes for the VW bus restoration scene.
Another option for making molds is using the electro erosion technique, you can make some prety complex shapes this way with some really intricate designs. the process can give just as much detail as etching PCB’s
Just FYI, Autodesk Moldflow Adviser Premium 2017 costs around $1,750 USD PER YEAR for a year long subscription. Are there even any open source or lower priced mold simulation products out there? This would just help get you part of the CNC design simulation done, setting aside all of the prior CAD work necessary before that. Again, extremely skeptical that somehow injection mold making has suddenly become a quick, cheap or easy thing.
The video below comes from [Dave Hakkens] by way of his Precious Plastic project, whose mission it is to put the means of plastic recycling into the hands of individuals, rather than relying on municipal programs. We’ve covered their work before, and it looks like they’ve come quite a way to realizing that dream. This tutorial by [Dave]’s colleague [Jerry] covers the basic elements of injection mold design, starting with 3D modeling in Solidworks. [Jerry] points out the limitations of a DIY injection molding effort, including how the thickness of parts relates to injection pressure. Also important are features like gentle curves to reduce machining effort, leaving proper draft angles on sprues, and designing the part to ease release from the mold. [Jerry] and [Dave] farmed out the machining of this mold, but there’s no reason a fairly complex mold couldn’t be produced by the home gamer.
You dont need a CNC machine to make molds. You can make reasonable molds with hand tools using some old techniques. Scraping and Shaping is one of the oldest techniques and was done well before there were CNC machines. Admittedly it takes a lot more time but you can make a really nice multi part mold this way.
In this collection, which is part one of a series representing some of John’s finest work, we present you with five articles that we think you will refer to time and again as you look to solve problems, cut cycle times and improve the quality of the parts you mold.
2. A Sprue can be quite large most of the time if using a rubber washer seal… we often used a 1/4″ port for higher flow-rates and lower pressures.
One time i needed a mould for inyecting Kraton, and the guy at the workshop told me that it was possible to make them with Epoxy, but i could’t find much info on the process. Can you give me advice or info about how to desing and make them? It is better if the mould has metal charge like steel or aluminum? Are the moulds casted from epoxy resin?
Not personally, but I was witness to a China-made, mid-sized (slightly below 1t assembled) tool steel injection mold for a modern plastic injection machine… while several times cheaper, it also had to be sent several times back, because it had defects/missing features/didn’t work, so ultimately it cost the company slightly more then if they used a domestic mold maker…depends who you choose obviously, you (don’t) get what you (don’t) pay for…
GETTING A QUOTE WITH LK-MOULD IS FREE AND SIMPLE.
FIND MORE OF OUR SERVICES:
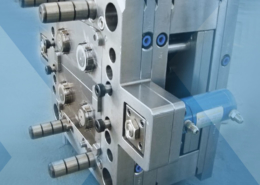
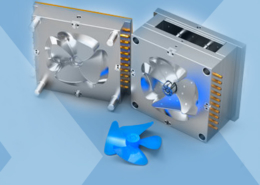
Plastic Molding

Rapid Prototyping
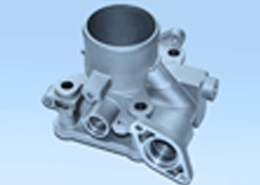
Pressure Die Casting
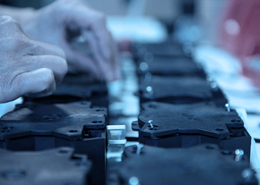
Parts Assembly
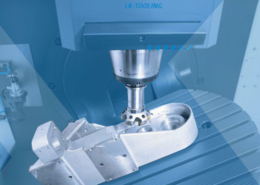