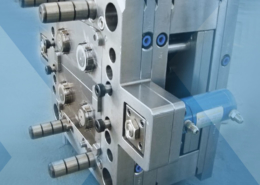
Faster Neck Changes Add Flexibility to Aseptic PET Blow Molding - flexible injec
Author:gly Date: 2024-09-30
A.J. Pruitt, technology manager at Accumold discusses the impact of the company’s successful drive towards the efficient micromoulding of previously extruded thin walled cannulas, and what this means for industry.
Accumold's apability to scale quickly and produce very high volumes is also a key advantage. Our expertise allows us to efficiently ramp up production to meet large demands, making it possible to produce tens of millions of components without compromising on quality. This scalability ensures that we can meet the needs of large-scale manufacturers while maintaining cost-effectiveness. The ability to produce high volumes consistently and efficiently makes Accumold's micromoulding method a superior choice for industries requiring precise and reliable components, such as wearable diabetes devices.
The Informa Markets Engineering network of B2B media sites includes Design News, Battery Technology, Medical Device & Diagnostic Industry (MD+DI), Packaging Digest, PlasticsToday, and Powder & Bulk Solids.
Accumold's new method addresses these issues by streamlining the production process and enhancing precision. By utilising advanced micromoulding techniques, we eliminate the need for the tipping process and reduce the reliance on fluing. This results in a more consistent product with significantly lower fallout rates. The integrated approach ensures that each step is optimised for efficiency, reducing the number of stages and associated costs. This innovation not only improves the quality and reliability of thin-walled cannulas but also makes high-volume production more feasible and economical.
AJP. The innovation in micromoulding thin-walled cannulas is poised to significantly impact the medical device market, particularly for diabetes management. As the market becomes increasingly saturated, there is a pressing need for cost-effective solutions that do not compromise on quality. Accumold's advanced moulding techniques offer a way to reduce production costs while maintaining high standards of quality and reliability. This ability to provide high volumes of consistently superior components allows manufacturers to meet the growing demands of their patients efficiently.
Our ability to shape products to exact specifications played a pivotal role in this development. Accumold's design team worked closely with the client to ensure the right gating and injection strategies were employed, guaranteeing a high-quality end product. By focusing on precision and customisation, Accumold was able to overcome the technical challenges associated with moulding thin-walled cannulas, ultimately advancing the field of wearable diabetes devices and demonstrating our commitment to meeting complex client needs with innovative solutions.
Non-medical applications could also benefit from this innovation. Industries such as biotechnology, pharmaceuticals, and even aerospace require highly precise, small-scale components. For instance, in biotechnology, these cannulas could be used in microfluidic devices for lab-on-a-chip applications, enabling precise control of fluids at a microscopic level. In the pharmaceutical industry, they could facilitate the development of advanced drug delivery systems, enhancing the effectiveness of new medications. The aerospace industry might use them in systems requiring the precise management of fluids or gases in confined spaces. The versatility and precision of Accumold's micromoulding technology make it applicable to a diverse array of fields beyond medical devices.
This recent development aligns with Accumold's long-term vision of being at the forefront of micromoulding innovation. By continuously pushing the boundaries of what is possible with moulding technology, we strive to offer solutions that meet the evolving needs of our clients across various industries. The focus on reducing manual intervention and enhancing automation reflects Accumold’s commitment to optimising production processes and delivering high-quality components at competitive prices. As the company expands its expertise and capabilities, Accumold is poised to set new standards in the micromoulding industry, ensuring we remain a trusted partner for companies seeking innovative and efficient manufacturing solutions.
AJP. We were inspired to develop a new method for micromoulding thin-walled cannulas when a client approached us with a specific challenge — moulding a product with an exceptionally thin wall. Recognising that this request aligned well with our core competencies, the Accumold team saw an opportunity to leverage our expertise in precision moulding. This realisation prompted a collaborative effort to explore innovative solutions, drawing on our extensive experience and advanced capabilities in micromoulding to meet the client's unique requirements.
AJP. Accumold maintains the high quality and precision required for thin-walled cannulas through a dedicated and highly skilled quality team. This team acts as an extension of the client's project team during the design process, ensuring that all specifications are met at each phase of the project and into full-scale production. By integrating quality assurance into every step of the design and manufacturing process, we ensure that the final products adhere to the strict tolerances and standards necessary for medical devices.
Custom injection molder Viking Plastics announced today that current president Shawn Gross will succeed Kelly Goodsel as CEO, effective Nov. 1, 2024, as part of a larger succession strategy. Goodsel will continue in the role of chairman until the end of October and remain involved as a trusted advisor and business ambassador, the company said.
AJP. Accumold's new micromoulding method offers significant advantages in terms of production efficiency, cost-effectiveness, and scalability. By eliminating secondary processes and multistep procedures — which often lead to rework or failed assemblies — the method streamlines production. This reduction in steps not only enhances efficiency but also lowers the likelihood of defects, resulting in a more reliable and consistent product. The streamlined approach ensures that each component meets the stringent quality standards required for medical devices, thereby reducing overall production costs.
Additionally, Accumold's capability to produce high volumes, in the tens of millions, with consistent quality means that manufacturers can rely on a steady supply of uniform components. This consistency is crucial for the final device's performance, as it ensures that each unit operates as intended, reducing variability and increasing the overall reliability of wearable diabetes devices. The ability to maintain such high standards at scale makes these devices more accessible and dependable for users managing diabetes.
AJP. Traditional production processes for thin-walled cannulas often face significant drawbacks, including high fallout rates and the need for multiple complex steps. The tipping process, essential for shaping the tips of traditionally made cannulas, frequently results in inconsistent quality and increased wastage. In addition, traditional methods require fluing, a process of attaching plastic or metal hubs, which can further complicate production and add to the overall costs. These steps not only increase the risk of defects but also drive up expenses, particularly when manufacturing in high volumes, making the process inefficient and costly.
AJP. Thin-walled cannulas are crucial in modern wearable diabetes devices due to their ability to deliver insulin or other medications with minimal discomfort and high precision. These devices require components that are both small and efficient to ensure patient compliance and comfort. Thin-walled cannulas allow for a less invasive experience, reducing pain and irritation during insertion and while worn, making them ideal for continuous or frequent use. Their micro-sized design also helps maintain the compactness of wearable devices, which is essential for user convenience and discretion.
AJP. Accumold's future plans for innovation in micromoulding are centred around challenging traditional manufacturing methods and exploring the potential of moulding to enhance product quality, reduce costs, and increase production volumes. The success of our thin-walled cannula project has demonstrated that the old ways of manual or automated assembly are not always the most efficient or effective. By leveraging advanced moulding techniques, Accumold aims to provide solutions that simplify production processes, improve product integrity, and scale up manufacturing capabilities. This approach is being extended to various projects involving overmoulding and lead frame moulding, where we have already achieved significant cost and time savings for our customers.
Calling it an honor to lead such an exceptional team at Viking Plastics, Goodsel said he is “confident the company is well-positioned for continued growth and success. Shawn is a well-rounded executive with a proven track record, and I’m certain he, along with the management team, will further strengthen Viking’s position as the partner of choice across all areas of the business."
“I am excited to welcome Shawn as the next CEO of Viking Plastics,” said Geoff Hoffmann, co-CEO of Hoffmann Family of Companies, in a prepared statement. “Shawn’s extensive plastics expertise, intensive focus on quality, and unwavering commitment to driving a culture of continuous improvement will take the company to new heights. Under Kelly’s leadership, Viking Plastics has seen tremendous growth, establishing itself as a leader in the injection molding and assembled products industry with a trusted brand and strong financial foundation. We wish Kelly all the best in this next chapter of his life.”
Current president Shawn Gross will succeed Kelly Goodsel as CEO, part of a larger succession strategy for the custom injection molder.
The company's extensive experience with a wide range of products has given it a deep understanding of the intricacies involved in micromoulding. This knowledge ensures that we can consistently produce high-quality, reliable components that meet stringent industry standards. The ability to mould such fine and consistent structures sets Accumold apart, allowing the company to meet the specific needs of clients and advance the capabilities of wearable medical devices. This innovative process not only improves the performance and reliability of thin-walled cannulas but also demonstrates Accumold's leadership in the field of micromoulding technology.
Founded in 1972 and headquartered in Corry, PA, Viking Plastics was acquired by the Hoffmann Family of Companies in August of this year. Viking operates more than 50 injection molding machines and multiple automated assembly cells in Kentucky, Indiana, and Pennsylvania for a global customer base. A specialty is sealing closures for automotive and HVAC applications.
AJP. Accumold's new micromoulding process for thin-walled cannulas is unique primarily because it utilises moulding rather than extrusion. This approach allows for greater precision and control over the final product's dimensions and quality. Our expertise, honed over 40 years and more than 7000 projects, enables us to achieve micro tolerances and thicknesses as fine as .0006 inches or less. This level of precision is critical for medical devices, where even the smallest deviations can impact functionality and patient safety.
AJP. Accumold's innovation significantly improves the functionality and reliability of wearable diabetes devices by reducing overall costs and minimising potential issues associated with traditional production methods. By eliminating the need for glued components, which can come loose and compromise the device's integrity, the new micromoulding process ensures a more secure and durable assembly. This advancement leads to fewer failures in the field, enhancing the user experience and trust in the device's reliability.
“On behalf of Viking Plastics’ stakeholders — including our customers, employees, shareholders, suppliers, and community members — I want to sincerely thank Kelly for his 24 years of dedicated service, during which he held key roles as President, CEO, Chairman and owner,” said incoming CEO Gross. He praised Goodsel’s two-decade-long leadership, emphasizing his guidance through the 2008-2009 recession, the challenges of COVID, ownership transitions, and domestic and international expansions. “Most notably, he helped implement an exceptional culture rooted in 2-Second Lean, a book written by Paul Akers, transforming the way we operate,” added Gross.
Furthermore, the assurance of high-quality, reliable components is crucial for medical devices used in diabetes management. Patients rely on these devices for their daily health and well-being, making reliability and precision paramount. Accumold's innovation addresses these needs by ensuring that every component meets rigorous standards, thereby enhancing the overall trust and effectiveness of wearable diabetes devices. This not only helps manufacturers stay competitive in a crowded market but also ultimately benefits patients by providing them with more reliable and affordable medical solutions.
Thin-walled cannulas also enhance the accuracy and reliability of drug delivery. The precision in their manufacturing ensures consistent lumen size, which is vital for accurate dosing and maintaining the effectiveness of the treatment. This reliability is particularly important in managing chronic conditions like diabetes, where precise medication administration directly impacts health outcomes. The innovation in micromoulding techniques for producing these cannulas, as developed by Accumold, addresses the limitations of traditional extrusion processes (which often require secondary processes such as tipping, flaring, and even gluing which adds to costs and chances of failure), leading to improved performance and broader adoption of advanced wearable diabetes management solutions.
Accumold's commitment to quality is reinforced by its ISO 13485 certification, which underscores our adherence to international standards for medical device manufacturing. This certification ensures that the company follows rigorous guidelines and best practices for quality management systems, enhancing our ability to produce reliable and precise components consistently. By combining our expert quality team with adherence to ISO standards, Accumold can deliver thin-walled cannulas that meet the highest levels of precision and reliability, crucial for the efficacy and safety of medical devices.
AJP. Beyond wearable diabetes devices, the ability to micromould thin-walled cannulas holds significant potential for a wide range of medical and non-medical applications. As the wearable device market grows, there is an increasing demand for smaller, more precise components that can deliver medications or other therapeutic agents efficiently. Any device requiring precise delivery, such as insulin pumps, pain management systems, and drug delivery implants, can benefit from these advanced cannulas. Their small size and high precision make them ideal for minimally invasive procedures, improving patient comfort and treatment efficacy.
GETTING A QUOTE WITH LK-MOULD IS FREE AND SIMPLE.
FIND MORE OF OUR SERVICES:
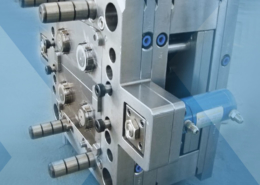
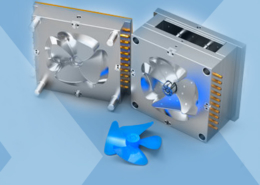
Plastic Molding

Rapid Prototyping
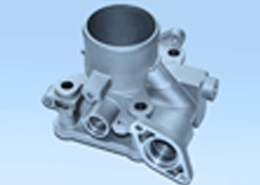
Pressure Die Casting
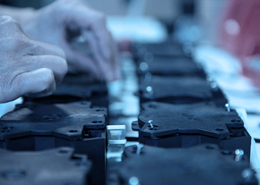
Parts Assembly
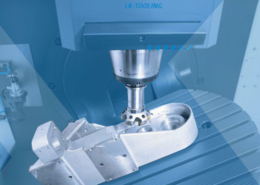