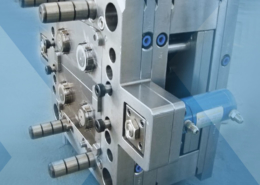
Plastic Injection Molding Cost: Understanding the Economics Behind the Process
Author:gly Date: 2024-06-08
Plastic injection molding stands as a cornerstone in the manufacturing industry, offering unparalleled versatility, efficiency, and cost-effectiveness in producing a wide array of plastic parts and products. However, understanding the intricate cost dynamics of this process is essential for manufacturers aiming to optimize their production strategies and remain competitive in today's market.
Introduction: Unveiling the Cost of Plastic Injection Molding
Plastic injection molding is a manufacturing process wherein molten plastic is injected into a mold cavity, forming a desired shape upon cooling and solidification. The cost considerations encompass various factors, ranging from material selection to tooling expenses and operational overheads. By delving into these aspects, one can unravel the complexities that dictate the overall cost structure of plastic injection molding.
Material Selection: Balancing Performance and Affordability
The choice of plastic resin significantly influences the cost and performance of injection-molded parts. Engineering-grade resins offer superior mechanical properties but often come at a higher cost compared to commodity-grade alternatives. Moreover, factors like material availability and market demand exert additional pressure on material costs, necessitating a meticulous balance between performance requirements and budget constraints.
Tooling Costs: Investing in Precision and Longevity
Tooling represents a substantial upfront investment in plastic injection molding, encompassing the design and fabrication of molds tailored to specific part geometries. The complexity of the mold, including features like undercuts and intricate details, directly impacts tooling costs. Additionally, considerations such as mold material, lifespan, and maintenance requirements play a pivotal role in determining the overall cost-effectiveness of the injection molding process.
Production Volume: Economies of Scale and Cost Optimization
The volume of production exerts a profound influence on the per-unit cost of injection-molded parts. High-volume production runs enable manufacturers to leverage economies of scale, spreading fixed costs across a larger output quantity and reducing the per-unit overhead. Conversely, low-volume production entails higher per-unit costs due to the inability to fully amortize fixed expenses, highlighting the importance of strategic planning and forecasting in optimizing production costs.
Operational Efficiency: Streamlining Processes for Cost Savings
Efficient operation of injection molding machinery is paramount in minimizing production costs and maximizing throughput. Factors such as cycle time optimization, scrap reduction, and energy-efficient equipment contribute to overall operational efficiency. Additionally, the implementation of lean manufacturing principles and process automation can further drive down costs while enhancing productivity and quality consistency.
Market Dynamics: Navigating Price Fluctuations and Supply Chain Risks
The volatility of resin prices, influenced by factors such as raw material availability, geopolitical tensions, and market demand, poses a significant challenge for manufacturers reliant on plastic injection molding. Mitigating supply chain risks through strategic sourcing, supplier diversification, and forward contracting is essential to stabilize costs and ensure uninterrupted production operations amidst market uncertainties.
Environmental Sustainability: Balancing Cost Efficiency with Eco-Conscious Practices
In an era of increasing environmental awareness, the pursuit of cost-effective plastic injection molding must align with sustainable practices and regulatory compliance. Innovations in recyclable materials, energy-efficient processes, and waste reduction strategies offer not only environmental benefits but also potential cost savings through resource conservation and operational optimization.
Conclusion: Navigating the Complexities of Plastic Injection Molding Cost
Plastic injection molding cost remains a multifaceted aspect of manufacturing, shaped by a myriad of factors spanning material selection, tooling expenses, production volume, operational efficiency, market dynamics, and environmental considerations. By comprehensively analyzing these facets and implementing strategic measures to optimize cost-effectiveness, manufacturers can unlock the full potential of plastic injection molding as a cornerstone of modern industrial production.
In conclusion, understanding and managing the cost dynamics of plastic injection molding is imperative for manufacturers striving to maintain competitiveness, achieve sustainable growth, and contribute to a resilient and efficient manufacturing ecosystem.
Whether through advancements in material science, process innovation, or supply chain optimization, continuous research and development efforts are essential to address emerging challenges and drive further cost efficiencies in plastic injection molding. By embracing a holistic approach that balances economic considerations with environmental stewardship and technological progress, the industry can chart a course towards a more sustainable and cost-effective future.
GETTING A QUOTE WITH LK-MOULD IS FREE AND SIMPLE.
FIND MORE OF OUR SERVICES:
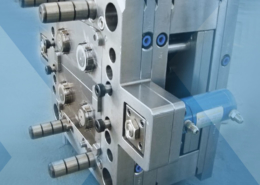
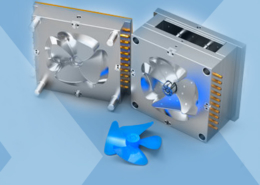
Plastic Molding

Rapid Prototyping
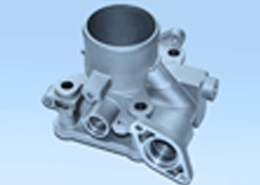
Pressure Die Casting
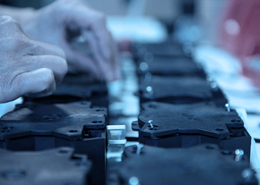
Parts Assembly
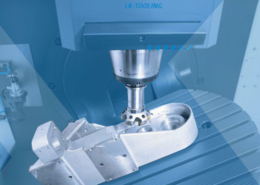