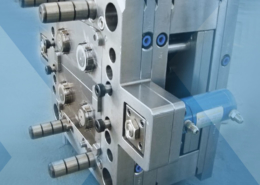
Ewikon Pro Edge VG: Innovative Valve Gate Nozzles for Precise Injection
Author:gly Date: 2024-09-30
“EPS and other plastics have done so well in the market is because they're inexpensive, versatile, and can be made into many shapes and forms,” says Horne. “Our products are comparable, though perhaps slightly higher in cost because of the value-added attributes.”
In considering composting from a regulator's viewpoint, Horne suggests “we likely don’t want everyone to have a compost heap in the backyard.”
And there’s one more distinction. “Because of the way it’s made, a unique feature of the packaging is that there’s a circle molded on the bottom,” he points out. “That could help distinguish our compostable products from other types of packaging at a municipal waste facility.”
Until she retired in September 2021, Clare Goldsberry reported on the plastics industry for more than 30 years. In addition to the 10,000+ articles she has written, by her own estimation, she is the author of several books, including The Business of Injection Molding: How to succeed as a custom molder and Purchasing Injection Molds: A buyers guide. Goldsberry is a member of the Plastics Pioneers Association. She reflected on her long career in "Time to Say Good-Bye."
The environmental benefits of installing solar are “as appealing as the financial benefit.” Tall added, “the solar energy system will reduce the amount of carbon dioxide in the air by 412,800 pounds per year, which is equivalent to taking 39 cars off the road, or planting almost 150 acres of trees.”
To finance the solar, Alpha Rho opted for a seven-year traditional lease from LFC Capital Inc., which eliminated any upfront capital investment. Instead, Alpha Rho will make 100% tax-deductible fixed monthly payments, creating a low-cost path to ownership at a substantially reduced price.
The product color can be a white like a standard EPS or gray or look like a brownie, depending on what type of fiber is used.
Evanesce Packaging Solutions offers another highly sustainable product: the first mass-produced biodegradable straws made of modified polylactic acid (PLA) that are on par or cheaper than paper straws, offer significantly improved durability, and home-compost within 90 days. The company’s South Carolina plant will be capable of producing millions of compostable straws daily.
“The return on investment with solar is phenomenal,” commented Tall. “The low cost of ownership thanks to the LFC lease, plus the SREC income and electricity savings, add up to a significant impact on our bottom line profitability, while we do something good for the planet at the same time.”
A dough is created from a mix of 60% starch, 35% fiber, and 5% other ingredients that Horne indicates is the “secret sauce” that makes this work.
“I generate what I need for the plant and whatever I generate and don’t use goes back into the grid,” Tall said. “However there is some controversy currently in the legislature. Some want to increase the cap on the amount of unused electricity that goes back into the grid. Others, primarily the utility companies, are in opposition to raising the cap. That’s an issue. We’re on a waiting list for the net metering program, and I don’t know whether I’ll get it, but I’ll probably use most of what I generate, which will still give me a reduced electric bill through credits.”
Alpha Rho (Fitchburg, MA), an injection molder of rigid plastic boxes of various sizes and shapes, has decided to go solar. The company will produce more than 80% of its power requirements to run the company’s manufacturing, warehousing and administrative operations, according to President David Tall, who discussed this decision with PlasticsToday.
“I don’t see FPI members as competitors,” Horne says. “I see them as future partners, and I see us growing by licensing our technology and gaining widespread adoption as quickly as possible.” He’s in discussions with a highly interested, major foodservice packaging supplier.
The R&D operations are in Vienna, Austria. However, having manufacturing capability in the US is critical, Horne emphasizes. “We’ll move to new molded starch production in early 2022 after we upgrade to our full-scale machines to make millions of units next spring.”
The word evanesce means to disappear. “That defines the company and our product: Evanesce Molded Starch technology is the essence of what we do,” he explains.
Tall explained that he has looked at solar a couple of times as a way to save money on his energy bills for the 12-press company. “Two previous times we looked at it, and it’s always seemed too good to be true,” said Tall. “This time we looked seriously at solar and decided that it is that good to be true. We’re a small business, so I wear a lot of hats and there are always so many things to think about other than solar power. On the third pitch, we looked more closely at what we can save and decided that financially it makes sense.”
Different fiber sources may be used that are often considered waste from food production operations, for example, bagasse or rice husks.
Because of the rebates and SREC, Massachusetts is a solar-friendly state to be in, even though it’s one of the more costly states for energy in the country. And while it’s not exactly the “sunshine state,” Tall said there are on average enough sunny days to make solar energy worthwhile.
He believes there will be more industrial composting infrastructure in the coming months, driven by the popularity of corn-based polylactic acid (PLA) and other compostable biopolymers and as the circular economy continues to develop.
“The amount of energy required during production is similar to thermoforming processes,” says Horne. “We employ heat recovery systems in our baking process that have evolved. Our environmental footprint is kept to a minimum.”
Company founder Douglas Horne was an elected government official in British Columbia, Canada, when he came across the technology. It so profoundly changed his way of thinking about packaging that it prompted Horne to change careers.
“Another exciting aspect of the technology is that the starch and fiber don’t have to come from a specific source,” Horne divulges. “The ingredients are a variable supply-and-demand factor to further keep costs low by using the cheapest available fiber source.”
Tall figures he’ll save about $64,000 annually if the numbers work. “There’s definite savings to be had, but until you get up and running, you never really know,” he said.
A dough made from starch, fiber, and little else that’s baked into compostable packaging using patented technology by Evanesce Packaging Solutions is a breakthrough recipe for sustainable packaging.
“We've been working with partners on coating systems as well,” Horne says. “For those that require longer oxygen barriers, we've worked with a couple of partners, which is how we started on the biopolymer side. Depending on the requirements, we can either coat, laminate, or simply add the barrier as a raw ingredient.”
“One of the exciting that we're getting into now is a deeper product: cups that look like they’re made of EPS,” discloses Horne. “These cups offer insulative properties for foodservice markets.”
The novel packaging is a molded starch-and-fiber product different than everything else including thermoformed fiber products, according to Horne. “It looks and feels like a traditional thermoformed plastic tray."
Evanesce’s durable food trays and cups made from a starch and fiber dough are "baked like a cookie” and home compostable in 90 days.
There will be some maintenance costs for the solar panels. The converters that turn the sunlight into energy tend to fail like any piece of equipment, which will require replacing them from time to time, Tall explained.
“At that time, I felt that we should ban expanded polystyrene (EPS) packaging because of this elegant alternative solution,” he relates. “The technology is so fantastic I left politics to acquire it then surrounded myself with great people to take it to a commercial level. One of the things that always worried me as a regulator was the fact that many of the products that were considered sustainable weren’t. This is.”
Rick Lingle is Senior Technical Editor, Packaging Digest and PlasticsToday. He’s been a packaging media journalist since 1985 specializing in food, beverage and plastic markets. He has a chemistry degree from Clarke College and has worked in food industry R&D for Standard Brands/Nabisco and the R.T. French Co. Reach him at [email protected] or 630-481-1426.
The technology adapts standard food processing equipment.“We’re taking technology that's been around for years and adapting it to use a different dough for making packaging,” says Horne. “The dough is formed by a ‘waffle-iron’ type of molding system into a tray or other packaging shape using the same kind of tried-and-true machinery that makes Twix candy bars, cookies, and other food products. We have a mechanized batch process using equipment from Bühler to produce hundreds of items at a time that are then baked in an oven.”
The solar energy system will be installed by New England Clean Energy on the roof of Alpha Rho’s 36,000-square-foot facility in April. It will have 745 Canadian Solar 320-watt panels, SolarEdge inverters with optimizers under each panel and Sollega racking and mounting hardware. The system is projected to deliver electricity savings of more than $1.6 million over 25 years (factoring in inflation). In addition, Alpha Rho will benefit from a new revenue stream created by the sale of solar renewable energy certificates (SRECs), arranged by New England Clean Energy.
Tall did his homework before deciding to put in solar. “I called around and talked to people in this business park who have solar and no one had anything negative to say. Everybody ran the numbers; on paper, it’s supposed to really save me a lot of money.”
GETTING A QUOTE WITH LK-MOULD IS FREE AND SIMPLE.
FIND MORE OF OUR SERVICES:
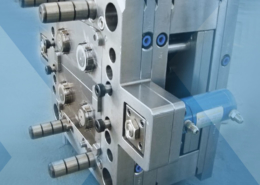
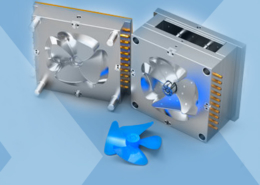
Plastic Molding

Rapid Prototyping
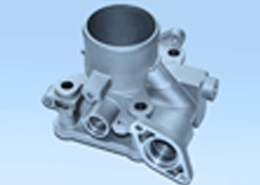
Pressure Die Casting
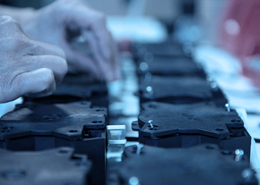
Parts Assembly
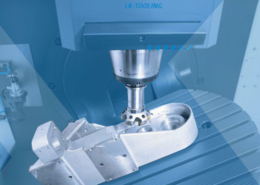