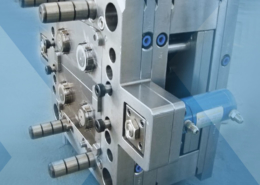
European research group creates injection molding plastic solar cells - thermopl
Author:gly Date: 2024-09-30
"The Industry Prints initiative has been working with the NHS to provide an agreed, printable face mask design that the NHS can use to keep them safe.
"Noviun are aiming to produce 300 masks a week to be shipped to both providers in the hope that we can have a positive impact on helping frontline NHS battle the virus and stay safe."
Thank you for your support. Here are some frequently asked questions you might find helpful to know why you are contributing?
Be part of a vibrant community focused on making a positive impact. Connect, share, and contribute to meaningful discussions.
National World encourages reader discussion on our stories. User feedback, insights and back-and-forth exchanges add a rich layer of context to reporting. Please review our Community Guidelines before commenting.
Rhino Machines was founded in 1984 by Manish’s father as a project consultant engineering firm. Later, Manish graduated as a Mechanical Engineer and registered the firm as a company in 1996. They have been catering to the technological needs of the foundry industry for years.
Gujarat-based entrepreneur Manish Kothari came up with an ingenious solution to this pertinent problem. The owner and managing director of Rhino Machines, a project consultancy firm, presents Rhino bricks, made from foundry dust and waste plastic!
Through the initial tests, a lot of merits came to be known. For instance, conventional clay bricks can sustain between 3.5-7 kg per cm square, while Rhino bricks can sustain about 14-15 kg per cm square because of the compressive strength of the ingredients.
Further, the manufacturing process releases zero emissions into the environment, and the bricks are ready for use after being rested for 30 minutes.
Foundry dust (comprises silica, clay and carbon) is a significant waste for the foundry industry; it is also difficult to dispose of as the particles are extremely light and can remain suspended in the air, causing pollution.
He said: “It is also allowing me to make some small mask clips to donate to local hospitals from my workshop in Shoreham.
“I visited their unit in March and was happy with how they utilised waste to make the bricks. Currently, we have sent them 300 kg of foundry dust to make about 900 bricks,” he says.
“We have designated areas for the collection of biomedical and other plastic waste. Since we don’t have an autoclave machine on-site, we provide them with plastic bottles, packets, wrappers, etc. Once we can sterilise biomedical waste on our own, we plan on supplying that too,” informs Rupesh.
Manish knew that fly ash was being used to make bricks, so he decided to approach manufacturers who were doing the same. But on experimentation, he found that it only used tiny amounts of the foundry dust, which defeated the purpose.
Also, while conventional bricks tend to disintegrate when divided into smaller sizes, Rhino bricks retain their shape and strength even if a hole were drilled in the middle.
He then found that plastic could act as an excellent binding agent with the foundry dust and arrived at the perfect composition for the bricks by mixing 25 per cent plastic with 75 per cent foundry dust. Thus, the first version of the Rhino bricks came into being in late 2018.
If you found our stories insightful, informative, or even just enjoyable, we invite you to consider making a voluntary payment to support the work we do at The Better India. Your contribution helps us continue producing quality content that educates, inspires, and drives positive change.
“By supplying these in huge numbers (60,000 with another 140,000 to go... at the moment) we can hopefully support the NHS with the high pressure and high demand of supplies at this time.
Another challenge was accessing plastic. “This may sound ironic, perhaps since there is so much plastic waste everywhere, but the problem is with segregation. When plastic waste is mixed with wet waste, it is very difficult for us to use it to make the bricks,” Manish informs.
The initial hiccups were to set up their plant, doing something new. “Although we have built a plant that can process about 600 kg of waste in a day, building it required an investment of nearly Rs 30 lakh. Still, not all aspects of our production are mechanised, and we are looking at ways to reduce the workforce,” he says.
Since transporting foundry dust would not be feasible in the long run, AIA Engineering decided to take help from Rhino Machines to set up a plant.
Associate Dan Smith said: “At the practice we have utilised our 3D printers to help provide face shields for local and national NHS in collaboration with the Makers Guild in Portsmouth and also Industry Prints.
Steve Dyke, managing director Automotive and Industrial said: “As a world-leading engineering consultancy, Ricardo is known for its expertise and capability in innovating, adapting and bringing products to market at pace, and as engineers we live to solve challenging problems for our customers. Our people have been anxious to use their engineering capabilities, skills and knowledge to find solutions to help protect frontline staff in the NHS and other key workers. The team has worked tirelessly to enable us to be able to go into production in a matter of days, and we are proud to be in a position to use our engineering capabilities for this essential task.”
To overcome this, Manish is spreading awareness among schools and society buildings to segregate waste. Collaborating with these stakeholders, he has been able to bring plastic to his factory in small amounts.
Claire Kentish Barnes is the distiller and owner, she said: “We heard that other bigger distilleries were supplying the NHS and emergency services with hand sanitiser and we thought it would be great if we could do the same.
India is the second-largest brick manufacturer in the world, with the Indo-Gangetic plains producing more than 65 per cent of the total production in the country. But, did you know that brick kilns are also major contributors to environmental pollution?
Now, Manish is looking to diversify the applications of the bricks. “We are exploring this new technology where we make interlocking bricks, which essentially work like Lego. This will eliminate the use of cement and mortar in construction processes, making the product more eco-friendly,” he says.
Ricardo has used its manufacturing supply chain expertise to engage with an injection moulding partner, to create a tool capable of high-volume manufacture.
“I was on their factory site and saw a bag of foundry dust. I asked Manish about it, and he told me about how he was planning on converting the dust into bricks. Once they finally got their composition right, we collaborated on fixing the dimensions, weight, and other characteristics for the bricks,” shares architect Shridhar Rao.
Chetan Shah, business head at AIA Engineering, informs that he learned about Rhino bricks in February 2020 when he met Manish at an exhibition. As a manufacturing company that dabbles in making castings (in addition to other design and development verticals), they had a lot of foundry dust in their factory units in Ahmedabad.
In order for us to continue to provide high quality and trusted local news, I am asking you to please purchase a copy of our newspapers.
To understand the advantages of the brick, Manish needed expert advice. For this, he decided to consult with R+D Studio, which was setting an on-site plant for Rhino Machines.
The industry is the largest user of coal (used to fire the bricks) in the country and a significant cause of air pollution, and also leads to the loss of fertile topsoil.
Facilities at Ricardo technical centres at Shoreham-by-Sea have been repurposed as assembly and logistics centres for the new face shields.
Manish, on the other hand, says that the collaboration has been helping them navigate the application of the bricks in the architectural space. “We could understand the usability of the bricks and Shridhar’s network helped spread awareness in the architectural community,” he says.
R+D Studio is a design and architectural firm in Gurugram, founded by partners Shikha Doogar and Shridhar Rao. After several years of practice in Dubai and the US, the husband-wife duo decided to return to India and start their firm. Shikha is Manish’s niece, and often consults with Manish’s firm for his design needs.
“At Rhino Machines, we provide the technology to break down large sand moulds. Moreover, we also set up plants for clients in the foundry industry to clean and process the sand, so it can be reused through the green sand reclamation process. While 70 per cent of the total sand can be reused, the other 30 per cent, in the form of foundry dust, is too fine to be used again,” he explains.
A number of businesses from across the Sussex area have been putting on hold their usual production and are instead turning their focus to making masks, sanitiser and a whole range of and a whole range of other protecting equipment.
Eliott Flack, who owns Direct Foam, said: “We felt that by changing our line of work and customer base temporarily, we could contribute towards the hard work that NHS workers are currently facing.
National trade body the Builders Merchants Federation (BMF) co-ordinated a national response across its membership, appealing for donations .
Later, Shridhar founded R+D Labs, their architectural research and testing vertical, in June 2020. “We were conducting tests for quite some time and planned on testing the bricks further to understand how they fare in comparison to conventional ones,” he says.
Graham McKnight from Durrington works at Worthing Hospital as a Macmillan Clinical Support Worker, his fiancée Erin Gee’s mother, Christine from Worthing, is making bandanas for care home staff.
As opposed to clay brick, Rhino bricks are 2.5 times stronger and 25 per cent lighter. They are also reasonably priced at Rs 10 per piece, making them cost-effective.
Rhino Machines also helps quite a few institutions get rid of their plastic waste. One such is the Sri Krishna Hospital in Ahmedabad, that has gotten rid of over 3,600 kg of waste. Rupesh Prakash Nagpure, 46, Head of Housekeeping and Waste Management at the hospital, says that waste is being picked up for free twice a week since September 2019.
“We asked via local social media forums whether there was a need in our local communities and the response was overwhelming.”
Martin Starkey, managing director Performance Products added: “Our people are renowned for their expertise in high value manufacturing, and they have brought their trademark passion, care, dedication and commitment to assembling face shields. We are proud of our people’s response in volunteering to be part of this work, and also that we are able to make the most of our facilities at the Ricardo Shoreham Technical Centre. We look forward to delivering these much-needed PPE products to the NHS and care homes as soon as possible.”
“Although foundry dust is generated in large amounts, it is difficult to access as and when we want, which is why I have mapped out all the foundries so that the process continues,” informs Shridhar.
It is an unprecedented situation but it is reassuring to see how businesses and individuals are coming together to support key workers, volunteers and the NHS.
Rhino Machines manufactures these bricks and paver blocks (made from the same mixture of plastic and foundry dust) in collaboration with R+D Labs (an offshoot of R+D Studio, an architectural firm) that helps them with research and development. Launched in February 2020, they have already received orders of over 1,000 bricks and 650 paver blocks. They have also received inquiries from Chile, Colombia, and China.
“The foundry industry in India is the second-largest in the world after China. India produces almost 10-12 million castings every year. For every tonne of casting that the industry makes, about 800 kg of sand is used,” explains Manish.
With the coronavirus lockdown having a major impact on many of our local valued advertisers - and consequently the advertising that we receive - we are more reliant than ever on you helping us to provide you with news and information by buying a copy of our newspapers.
While conventional bricks tend to disintegrate when divided into smaller sizes, Rhino bricks retain their shape and strength even if a hole were drilled in the middle.
This has resulted in him having to shut down landscaping, but he has started a woodworking business making small gifts and bespoke furniture.
“Clients started telling me how they wanted to get rid of this 30 per cent foundry dust to have zero discharge on-site,” informs Manish.
By paying for the stories you value, you directly contribute to sustaining our efforts focused on making a difference in the world. Together, let's ensure that impactful stories continue to be told and shared, enriching lives and communities alike.
“The work with the clips has spiralled. I got a large batch made for Worthing Hospital and through the power of Facebook, other people have been asking, which ended up with me doing a small GoFundMe page aimed at friends to help chip in for materials and it’s all growing.
Our journalists are highly trained and our content is independently regulated by IPSO to some of the most rigorous standards in the world. But being your eyes and ears comes at a price. So we need your support more than ever to buy our newspapers during this crisis.
The face shields will be donated free of charge to front line NHS workers and care homes and is being produced to a bespoke Ricardo design, leveraging its design, engineering and manufacturing expertise. A prototype was delivered by the company’s in-house rapid prototyping team and facilities. However, it was quickly realized that rapid prototyping would not provide the volumes of face shields needed or at the speed required.
Using this bespoke tooling, and its engineering design expertise, the team took the opportunity to refine the original rapid prototype design of the face shield for enhanced comfort over extended periods of wear, inviting local NHS doctors to test the new face shield design for comfort and wearability.
“There is no use of water in the making of these bricks. Also, more water is saved during the construction process, as the walls built with these bricks do not need to be cured with water,” explains 52-year-old Manish.
He is also looking forward to setting up plants on the sites of different foundry factories so that waste can be managed at source. At the same time, Shridhar hopes that there is more government collaboration where schools and hospitals can be built with these bricks. The bricks can be used in all constructions.
The family-run business, which last year celebrated its 90th anniversary, has its headquarters in Forest Row and further branches in Crowborough, East Grinstead and Haywards Heath.
“I have telephoned the New Grange Care Home (10-16 Homefield Road, Worthing), who said that they would happily accept and use Christine’s headbands, as care staff there also use PPE that may irritate behind the ears.”
“Our objective is to manage waste effectively and efficiently. We want to stay true to these values. The larger picture is to look at new ways of converting waste into wealth, and that motivates us,” says Manish.
Mid-Sussex Timber (MST) - has provided a range of items, including goggles, safety glasses and face masks, in a bid to tackle the shortages faced in the healthcare sector.
He started researching possible solutions and speaking to academicians and researchers to understand how foundry dust could be used.
GETTING A QUOTE WITH LK-MOULD IS FREE AND SIMPLE.
FIND MORE OF OUR SERVICES:
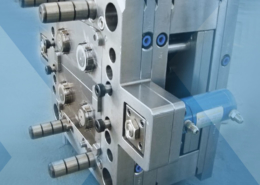
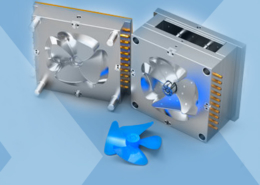
Plastic Molding

Rapid Prototyping
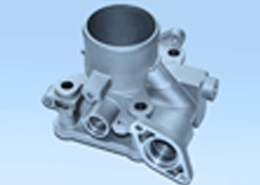
Pressure Die Casting
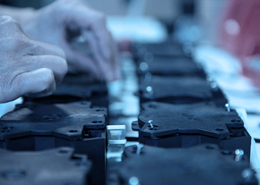
Parts Assembly
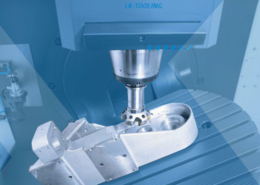