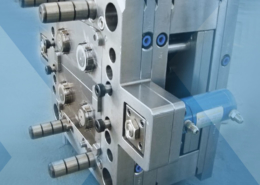
Envisioning high-volume, 100% composite wheels - rim plastic molding
Author:gly Date: 2024-09-30
3D printing’s sweet spot is in high-value, low-volume production, the opposite of injection molding. Here’s the good, bad, and ugly of both technologies, and advice on when it makes sense to pivot from one to the other.
Join this webinar to explore the transformative benefits of retrofitting your existing injection molding machines (IMMs). Engel will guide you through upgrading your equipment to enhance monitoring, control and adaptability — all while integrating digital technologies. You'll learn about the latest trends in IMM retrofitting (including Euromap interfaces and plasticizing retrofits) and discover how to future-proof your machines for a competitive edge. With insights from industry experts, it'll walk you through the decision-making process, ensuring you make informed choices that drive your business forward. Agenda: Maximize the value of your current IMMs through strategic retrofitting Learn how to integrate digital technologies to enhance monitoring and control Explore the benefits of Euromap interfaces and plasticizing retrofits Understand how retrofitting can help meet new product demands and improve adaptability Discover how Engel can support your retrofitting needs, from free consultations to execution
Please note: You do not duplicate set points; you duplicate actual measured values. Use your machine’s data table to tabulate and follow these few during production. Keep it simple; you cannot keep track of too many. Yes, a computer can, but you will never make production watch more than roughly six.
August 29-30 in Minneapolis all things injection molding and moldmaking will be happening at the Hyatt Regency — check out who’s speaking on what topics today.
In a time where sustainability is no longer just a buzzword, the food and beverage packaging industry is required to be at the forefront of this innovation. By adopting circular packaging processes and solutions, producers can meet regulatory requirements while also satisfying consumer demand and enhancing brand reputation. Join Husky to learn more about the broader implications of the circular economy — as well as how leading brands are leveraging this opportunity to reduce costs, increase design flexibility and boost product differentiation. Agenda: The cost and operational benefits of embracing circularity Key materials in circular packaging — including rPET and emerging bioplastics How to design a circular food and beverage package Strategies for selecting sustainable closures to future-proof packaging solutions Optimization and streamlining of production processes for enhanced efficiency How Husky Technologies can enable your sustainable success
Introduced by Zeiger and Spark Industries at the PTXPO, the nozzle is designed for maximum heat transfer and uniformity with a continuous taper for self cleaning.
Today’s 3D printing is an indisputably industrial suite, though, with attainable production-level efficiency. Together with the processes, the ways in which we refer to the technology have matured. No longer is “3D printing” or the original “rapid prototyping” the phrase bandied about in most professional labs; now, “additive manufacturing” or, more casually, AM, is the go-to terminology, placing these layer-by-layer processes squarely in the manufacturing realm.
Sarah Goehrke is the founder of AM-specific contract services company Additive Integrity and sits on the Board of Advisors for the Additive Manufacturing Coalition. She focuses in the additive manufacturing industry on advances in diversity, sustainability, and ecosystem positioning with a heightened focus on messaging. Goehrke has been a leader in the 3D-printing industry since 2014, previously serving as the Managing Editor of Fabbaloo; Editor-in-Chief of 3DPrint.com; and Senior Director, Strategic Communications and Ecosystems at ultrafast 3D-printing leader Nexa3D. Through Additive Integrity, she has worked with more than two dozen companies across the industry, contributed to publications including Forbes.com, and keynoted across three continents. She is deeply and actively passionate about advancing diversity, equity, and inclusion in the 3D-printing industry. Goehrke holds bachelor’s degrees in English and Theatre from Muskingum College, as well as a certificate in Diversity & Inclusion for HR from Cornell University.
Plastics Technology covers technical and business Information for Plastics Processors in Injection Molding, Extrusion, Blow Molding, Plastic Additives, Compounding, Plastic Materials, and Resin Pricing. About Us
Despite price increase nominations going into second quarter, it appeared there was potential for generally flat pricing with the exception of a major downward correction for PP.
Ultradent's entry of its Umbrella cheek retractor took home the awards for Technical Sophistication and Achievement in Economics and Efficiency at PTXPO.
You can better visualize the melting process by “flipping” the observation point so the barrel appears to be turning clockwise around a stationary screw.
Well-known as it may be, the design for manufacturing process for IM is lengthy and often non-linear. As a molding-based technology, IM relies on removable molds, which stifle the ability to design for low part counts and complex internal geometries. Further, creating those molds can add weeks to months to a production timeline.
Join Wittmann for an engaging webinar on the transformative impact of manufacturing execution systems (MES) in the plastic injection molding industry. Discover how MES enhances production efficiency, quality control and real-time monitoring while also reducing downtime. It will explore the integration of MES with existing systems, emphasizing compliance and traceability for automotive and medical sectors. Learn about the latest advancements in IoT and AI technologies and how they drive innovation and continuous improvement in MES. Agenda: Overview of MES benefits What is MES? Definition, role and brief history Historical perspective and evolution Longevity and analytics Connectivity: importance, standards and integration Advantages of MES: efficiency, real-time data, traceability and cost savings Emerging technologies: IoT and AI in MES
Here are the top six variables to watch for in injection molding and the reasons why. The accompanying chart also shows the allowable range for acceptable parts. If you want your processes to make identical parts, you must duplicate the following processing conditions.
After successfully introducing a combined conference for moldmakers and injection molders in 2022, Plastics Technology and MoldMaking Technology are once again joining forces for a tooling/molding two-for-one.
I find it strange that in this day and age there is no practical way to measure actual melt temperature in the barrel. Same for mold temperature. We can control the water temperature, but most temperature controllers vary gallons/minute (gpm) output and often have pressure variations which change the gpm going through the mold. Plus, you have the quality/cleanliness issues of the water, such as cleanliness, scale, rust and more.
Mixed in among thought leaders from leading suppliers to injection molders and mold makers at the 2023 Molding and MoldMaking conferences will be molders and toolmakers themselves.
Injection molding is a well-understood and go-to manufacturing process, but naturally isn’t without its limitations. The learning curve and expense of setting up an IM installation are significant, as is the ramp-up time to actually producing a new design.
I have found that few molders monitor gpm, which is critical to keep the Reynolds number above 5,000 for turbulent flow, which in turn provides uniform and consistent cooling.
With capabilities in polymers, metals, pastes, and even bio-materials, there are few material areas that 3D printing hasn’t begun to explore. There is, naturally, a hefty chasm between lab exploration and real-world application, and that’s one that 3D printing has begun to bridge tidily.
Sustainability continues to dominate new additives technology, but upping performance is also evident. Most of the new additives have been targeted to commodity resins and particularly polyolefins.
About the author: John Bozzelli is the founder of Injection Molding Solutions/Scientific Molding in Midland, Michigan, a provider of training and consulting services to injection molders, including LIMS and other specialties. Contact: john@scientificmolding.com.
In so many ways, AM remains an unknown quantity. Fewer materials, lower adoption, less training, and slower absolute per-part speeds combine into a difficult formula for adoption. The perception for some “big players” to keep their AM investment and use close to the vest as a “secret sauce” competitive secret also holds back the capability for many AM suppliers to tout their biggest success stories.
Resin drying is a crucial, but often-misunderstood area. This collection includes details on why and what you need to dry, how to specify a dryer, and best practices.
The Plastics Industry Association (PLASTICS) has released final figures for NPE2024: The Plastics Show (May 6-10; Orlando) that officially make it the largest ever NPE in several key metrics.
In this collection, which is part one of a series representing some of John’s finest work, we present you with five articles that we think you will refer to time and again as you look to solve problems, cut cycle times and improve the quality of the parts you mold.
The single most important thing to keep in mind when adopting AM is a simple one: Just because you can doesn’t always mean you should. It makes the most sense to stick with injection molding for:
Additive technology creates air pockets in film during orientation, cutting down on the amount of resin needed while boosting opacity, mechanical properties and recyclability.
Coverage of single-use plastics can be both misleading and demoralizing. Here are 10 tips for changing the perception of the plastics industry at your company and in your community.
Processors with sustainability goals or mandates have a number of ways to reach their goals. Biopolymers are among them.
What had been overblown promises about a decade ago are now deliverables: Production, scale, quality, validation, and volume are now end-use realities.
Overall, IM can reliably produce parts with known quality at high quantity — but it takes a while. When lower-volume end-use product runs are required, injection molding may add time and molding costs that counterbalance desirable ROI.
Standards, while also coming more into play, are also lagging. Many potential adopters cannot even consider 3D printing, as defense and other government-mandated organizations are limited in the scope of processes on the table. Until more standards are recognized and more support comes from all levels — such as with President Biden’s 2022 AM Forward initiative expanding reach nationally, locally, and internationally — adoption will remain lower than theoretically possible.
When, how, what and why to automate — leading robotics suppliers and forward-thinking moldmakers will share their insights on automating manufacturing at collocated event.
technotrans says climate protection, energy efficiency and customization will be key discussion topics at PTXPO as it displays its protemp flow 6 ultrasonic eco and the teco cs 90t 9.1 TCUs.
Thousands of people visit our Supplier Guide every day to source equipment and materials. Get in front of them with a free company profile.
Gifted with extraordinary technical know how and an authoritative yet plain English writing style, in this collection of articles Fattori offers his insights on a variety of molding-related topics that are bound to make your days on the production floor go a little bit better.
This Knowledge Center provides an overview of the considerations needed to understand the purchase, operation, and maintenance of a process cooling system.
This month’s resin pricing report includes PT’s quarterly check-in on select engineering resins, including nylon 6 and 66.
Say “manufacturing automation” and thoughts immediately go to the shop floor and specialized production equipment, robotics and material handling systems. But there is another realm of possible automation — the front office.
As some of today’s largest applications, like the adidas 3D-printed midsole, highlight, the best ultimate solution is to use the technologies that make sense where they make sense. Often, this is a complementary, rather than an either-or, solution. 3D-printed injection molds, for instance, offer an interesting combination of desirable traits for an overall fitting solution.
Multiple speakers at Molding 2023 will address the ways simulation can impact material substitution decisions, process profitability and simplification of mold design.
While an IM setup can be a huge upfront investment, the ROI is huge as its use scales. Indeed, peer-reviewed research indicates that “Injection molding is the best way to mass-produce small, precise polymer components with complex shapes.”
For all the new materials coming into AM — with giants like Arkema, BASF, Evonik, Henkel, Sabic, and many more dipping their toes in the 3D-printed waters — the overall portfolio is exponentially smaller compared to what’s available for traditional manufacturing.
Across the show, sustainability ruled in new materials technology, from polyolefins and engineering resins to biobased materials.
While the major correction in PP prices was finally underway, generally stable pricing was anticipated for the other four commodity resins.
There are hundreds of variables in the injection molding process. Which ones are the most important? A guy named Dr. E. Deming taught us that in any process, watch only the minimum number of variables. His theories (14 Points of Management) beat Six Sigma, ISO 9000, Factory 4 and more.
A quick checklist of when it makes sense to pivot production toward AM would include parts that fall under some of these categories:
Core Technology Molding turned to Mold-Masters E-Multi auxiliary injection unit to help it win a job and dramatically change its process.
While prices moved up for three of the five commodity resins, there was potential for a flat trajectory for the rest of the third quarter.
Successfully starting or restarting an injection molding machine is less about ticking boxes on a rote checklist and more about individually assessing each processing scenario and its unique variables.
Discover how artifical intelligence is revolutionizing plastics processing. Hear from industry experts on the future impact of AI on your operations and envision a fully interconnected plant.
Mass production with 3D printing is making inroads in areas where it commercially makes sense, with hearing aids the most significant area of early widespread adoption. Consumers are walking on shoes with 3D printed midsoles, purchased at retail, or with personalized insoles made to fit their feet via a smartphone app. Medical products, like prosthetics and orthotics, can also be made specifically for a wearer. Produced together with traditional techniques, 3D printing supplements an overarching process to create next-generation end-use products.
Join KraussMaffei for an insightful webinar designed for industry professionals, engineers and anyone interested in the manufacturing processes of PVC pipes. This session will provide a comprehensive understanding of the technology behind the production of high-quality PVC pipes: from raw material preparation to final product testing. Agenda: Introduction to PVC extrusion: overview of the basic principles of PVC pipe extrusion — including the process of melting and shaping PVC resin into pipe forms Equipment and machinery: detailed explanation of the key equipment involved — such as extruders, dies and cooling systems — and their roles in the extrusion process Process parameters: insight into the critical process parameters like temperature, pressure and cooling rates that influence the quality and consistency of the final PVC pipes Energy efficiency: examination of ways to save material and energy use when extruding PVC pipe products
Tried and true, injection molding (IM) has made its stand for decades. Patented in the late 1800s, IM boomed decades later as WWII demanded low-cost, high-volume production. It can hardly be said to have slowed since. Nearly ubiquitous in modern manufacturing environments, IM is perhaps best described as the devil you know; it has its kinks and limitations, but it’s familiar and generally reliable. Could IM, though, be displaced by newcomer AM?
Exhibitors and presenters at the plastics show emphasized 3D printing as a complement and aid to more traditional production processes.
A collaboration between show organizer PLASTICS, recycler CPR and size reduction experts WEIMA and Conair recovered and recycled all production scrap at NPE2024.
As with any tool in a toolbox, nuance is vital to the appropriate application of solution to challenge. When all you have is a hammer, after all, everything looks like a nail. Today’s toolbox is substantially more robust, leaving us with options and the wherewithal to make informed decisions: When do I need a hammer? When do I need something else?
Plastics Technology’s Tech Days is back! Every Tuesday in October, a series of five online presentations will be given by industry supplier around the following topics: Injection Molding — New Technologies, Efficiencies Film Extrusion — New Technologies, Efficiencies Upstream/Downstream Operations Injection Molding — Sustainability Extrusion — Compounding Coming out of NPE2024, PT identified a variety of topics, technologies and trends that are driving and shaping the evolution of plastic products manufacturing — from recycling/recyclability and energy optimization to AI-based process control and automation implementation. PT Tech Days is designed to provide a robust, curated, accessible platform through which plastics professionals can explore these trends, have direct access to subject-matter experts and develop strategies for applying solutions in their operations.
The strongest use case for any manufacturing process is, at its heart, straightforward. Use what makes sense. There is no single solution to meet every challenge. Each part, each end-use product, has unique specifications and, in an ideal world, should be approached individually. Take the time to understand the exact needs, explore available solutions, and narrow down to what makes the most sense for your application in terms of expense, time, expertise, and final product.
The aim of this presentation is to guide you through the factors and the numbers that will help you determine if a robot is a smart investment for your application. Agenda: Why are you considering automation? What problems are you trying to solve? How and why automation can help Crunch the numbers and determine the ROI
In this three-part collection, veteran molder and moldmaker Jim Fattori brings to bear his 40+ years of on-the-job experience and provides molders his “from the trenches” perspective on on the why, where and how of venting injection molds. Take the trial-and-error out of the molding venting process.
Mike Sepe has authored more than 25 ANTEC papers and more than 250 articles illustrating the importance of this interdisciplanary approach. In this collection, we present some of his best work during the years he has been contributing for Plastics Technology Magazine.
While prices moved up for three of the five commodity resins, there was potential for a flat trajectory for the rest of the third quarter.
Across all process types, sustainability was a big theme at NPE2024. But there was plenty to see in automation and artificial intelligence as well.
In this collection of articles, two of the industry’s foremost authorities on screw design — Jim Frankand and Mark Spalding — offer their sage advice on screw design...what works, what doesn’t, and what to look for when things start going wrong.
Second quarter started with price hikes in PE and the four volume engineering resins, but relatively stable pricing was largely expected by the quarter’s end.
With advocacy, communication and sustainability as three main pillars, Seaholm leads a trade association to NPE that ‘is more active today than we have ever been.’
The AM benefits for production are many. Complex internal structures can be incorporated directly into a single finished piece as the full product is produced at one time, reducing part counts as well as weak points of connection. Lightweighting, such as with lattice structures or simply through reduced part count, is desirable in weight-conscious industries like aerospace and automotive, where every ounce matters. A faster time-to-market is also a prime consideration as 3D printers can localize production. Importantly, 3D printing also forestalls the need for tooling, removing a time-intensive stage of many manufacturing processes. More validated materials are coming to market all the time, as well, bringing familiar materials to a new stable.
In this collection of content, we provide expert advice on welding from some of the leading authorities in the field, with tips on such matters as controls, as well as insights on how to solve common problems in welding.
With newer solutions coming to market and proving out their claims, injection molding is poised to lose some of its dominance in production.
Take a deep dive into all of the various aspects of part quoting to ensure you’ve got all the bases—as in costs—covered before preparing your customer’s quote for services.
Scale, speed, uniformity — injection molding ticks the right boxes for high-volume production. Able to reliably handle a huge array of materials, injection molding offers predictability and quality.
Sarah Goehrke is the founder of AM-specific contract services company Additive Integrity; serves on the Board of Directors and as the Head of DEI at Women in 3D Printing; and sits on the Board of Advisors for the Additive Manufacturing Coalition. She focuses in the additive manufacturing industry on advances in diversity, sustainability, and ecosystem positioning with a heightened focus on messaging. Goehrke has been a leader in the 3D-printing industry since 2014, previously serving as the Managing Editor of Fabbaloo; Editor-in-Chief of 3DPrint.com; and Senior Director, Strategic Communications and Ecosystems at ultrafast 3D-printing leader Nexa3D. Through Additive Integrity, she has worked with more than two dozen companies across the industry, contributed to publications including Forbes.com, and keynoted across three continents. She is deeply and actively passionate about advancing diversity, equity, and inclusion in the 3D-printing industry. Goehrke holds bachelor’s degrees in English and Theatre from Muskingum College, as well as a certificate in Diversity & Inclusion for HR from Cornell University.
The new kid on the production block, 3D printing, can be an exciting meet-cute — new shapes, complex forms, high-value/low-volume production, all built layer by layer to increasingly exacting standards. Ideated since the 19th century, with modern patents tracing to the 1980s, 3D printing rethinks manufacturing from the first layer. More oversight, standards, and validation are seeing the technology move more into the production world and finally, finally begin fulfilling what had been overblown early promises.
Formnext Chicago is an industrial additive manufacturing expo taking place April 8-10, 2025 at McCormick Place in Chicago, Illinois. Formnext Chicago is the second in a series of Formnext events in the U.S. being produced by Mesago Messe Frankfurt, AMT – The Association For Manufacturing Technology, and Gardner Business Media (our publisher).
Further, bridge production is increasingly showing its value as 3D printing begins what injection molding can finish at scale. Especially critical during early days of the COVID-19 pandemic, when personal protective equipment (PPE) and necessary parts for ventilators were in short supply and need-it-now high demand, 3D printing stepped up to outfit medical professionals and patients with what they needed while IM ramped up to meet broader demand. Some remain in use, as 3D printing may have enhanced testing devices’ efficacy.
AM remains a nascent technology, for all its recent growth and maturation. Adopting the technology for the first time requires a major learning curve as product designers well versed in DFM have a new skill set to gain in DfAM — design for additive manufacturing. Risk-averse sectors where validation is critical and new installations expensive in terms of training and investment are hesitant to adopt before they understand a full ROI. Often, adoption relies on a single internal champion, and AM-using departments tend to run as something of a startup inside an established company.
While the melting process does not provide perfect mixing, this study shows that mixing is indeed initiated during melting.
The biggest pro for additive manufacturing is perhaps also its biggest con: The sweet spot is in high-value, low-volume production. This is counterbalanced by injection molding’s sweet spot, which is just the opposite.
Learn about sustainable scrap reprocessing—this resource offers a deep dive into everything from granulator types and options, to service tips, videos and technical articles.
3D printing first made headlines as a half-Star Trek, half-everyman technology that brought science fiction to the kitchen table. Gassed-up media reports positioned the technology as an “anyone can make anything” process. Unsurprisingly, no such process exists with push-button precision. Mainstream perceptions dimmed, dismissing the technology.
Join Engel in exploring the future of battery molding technology. Discover advancements in thermoplastic composites for battery housings, innovative automation solutions and the latest in large-tonnage equipment designed for e-mobility — all with a focus on cost-efficient solutions. Agenda: Learn about cutting-edge thermoplastic composites for durable, sustainable and cost-efficient battery housings Explore advanced automation concepts for efficient and scalable production See the latest large-tonnage equipment and technology innovations for e-mobility solutions
Mold maintenance is critical, and with this collection of content we’ve bundled some of the very best advice we’ve published on repairing, maintaining, evaluating and even hanging molds on injection molding machines.
Establishing and understanding the break-even point of cost-versus-quantity will often inform the decision for when to adopt which manufacturing process. Considerations obviously differ from batch sizes of 2 to 25 to 250 to 250,000.
GETTING A QUOTE WITH LK-MOULD IS FREE AND SIMPLE.
FIND MORE OF OUR SERVICES:
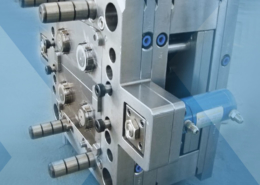
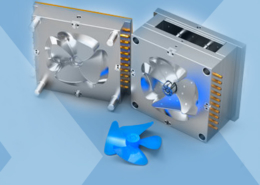
Plastic Molding

Rapid Prototyping
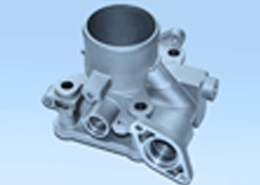
Pressure Die Casting
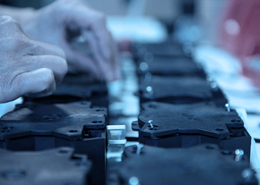
Parts Assembly
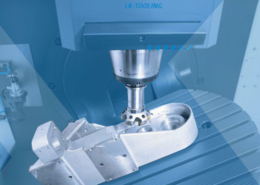