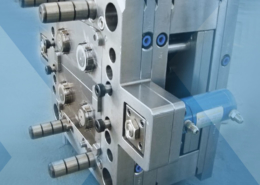
Plastic Injection Mold Tooling: Precision Engineering at Its Finest
Author:gly Date: 2024-06-08
Plastic injection mold tooling stands as the cornerstone of modern manufacturing, facilitating the mass production of intricate plastic components that populate our everyday lives. From the casing of electronic devices to the interior components of automobiles, plastic injection mold tooling underpins the production of countless consumer and industrial goods. In this article, we delve into the world of plastic injection mold tooling, exploring its intricacies, applications, and future prospects.
Understanding Plastic Injection Mold Tooling
At its core, plastic injection mold tooling involves the creation of precise molds or dies that are used to shape molten plastic into desired forms. These molds typically consist of two halves, known as the cavity and the core, which are precisely machined to mirror the intended shape of the final product. The molten plastic is injected into the mold under high pressure, where it cools and solidifies, taking on the shape of the cavity. Once the plastic has set, the mold opens, and the finished part is ejected, ready for further processing or assembly.
Key Components and Materials
The success of plastic injection mold tooling hinges on the quality and precision of its components. Molds are typically made from hardened steel or aluminum alloys, chosen for their durability and thermal conductivity. The design of the mold is crucial, with factors such as gate placement, cooling channels, and ejector mechanisms all playing a critical role in the quality of the finished part. Advances in materials science and machining technology continue to push the boundaries of what is achievable, enabling the production of increasingly complex and intricate molds.
Applications Across Industries
The versatility of plastic injection mold tooling lends itself to a wide range of industries and applications. In the automotive sector, it is used to manufacture everything from interior trim components to under-the-hood parts. In the consumer electronics industry, it enables the production of sleek and lightweight casings for smartphones, tablets, and laptops. Even in the medical field, plastic injection mold tooling is employed to create sterile and precise components for devices and equipment.
Challenges and Innovations
Despite its widespread use, plastic injection mold tooling is not without its challenges. Issues such as warping, sink marks, and parting line defects can all compromise the quality of the finished part. However, ongoing research and innovation are addressing these challenges head-on. From advanced simulation software that optimizes mold designs to novel materials that enhance performance and durability, the future of plastic injection mold tooling is bright.
Conclusion
In conclusion, plastic injection mold tooling is a cornerstone of modern manufacturing, enabling the mass production of precise and intricate plastic components across a wide range of industries. From automotive to electronics to healthcare, the applications of plastic injection mold tooling are virtually limitless. As technology continues to advance, so too will the capabilities of plastic injection mold tooling, ushering in a new era of innovation and possibility.
GETTING A QUOTE WITH LK-MOULD IS FREE AND SIMPLE.
FIND MORE OF OUR SERVICES:
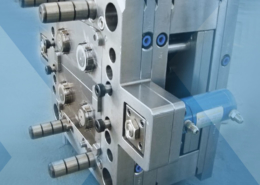
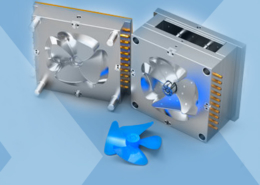
Plastic Molding

Rapid Prototyping
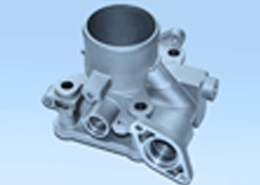
Pressure Die Casting
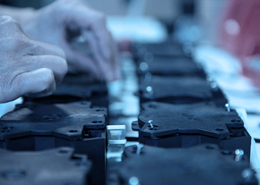
Parts Assembly
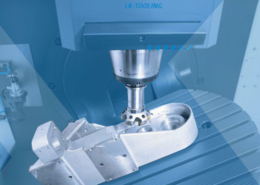