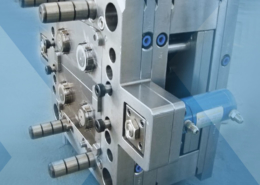
Engel Solutions at NPE2024: Empowering Workforce & Driving Efficiency - engel in
Author:gly Date: 2024-09-30
Rotation in two axes (typically at one to five revolutions per minute) does an excellent job of averaging out small variations in heat intensity, and of course steel or aluminium moulds convey heat laterally across the mould surface to even out temperatures. But most importantly, our patented control systems actively speed up and slow down the mould as each face passes through the solar heat beam to achieve target temperatures - to the extent that we can heat certain mould faces more (producing thicker plastic in that area) or heat other faces less (forming a thinner part in that area). This per-face thickness control is difficult to achieve in traditional moulding, yet we can do it ‘programatically’. An example of how this is useful: we can mould water tanks with extra thick bottoms for durability, but thin upper walls to save plastic.
“Asahi Kasei introduces new possibilities of foam materials by launching the PA Foam with unprecedented high heat resistance to the market,” commented Takauji Namatame, Senior Manager of the Corporate R&D Division at Asahi Kasei Europe. “In Europe, where environmental awareness is strong, the need for lightweight applications is expected to further increase in the future, especially in the automotive industry. Our foam opens new doors for applications, which at the same time require lightweight and heat resistance. In addition, the noise reduction properties resulting from the special shape of the beads will meet the growing demand regarding applications that reduce noise, vibration and harshness (NVH).”
In contrast, we radiatively heat the mould using the solar beam and largely avoid heating anything else in the chamber. Thus, we can use servo and stepper motors in the chamber, put active temperature monitoring systems permanently in the chamber, and generally use a wide range of sensors and electronics not available in traditional machines. We can monitor mould surface and internal mould air temperatures, mould position, beam intensity, and much more.
These noise reduction qualities of the foam also contribute to enhanced comfort inside the car. With the rising popularity of car sharing and the expected introduction of autonomous driving, the automotive interior is becoming more and more important as a space for relaxation and comfort – a space of living. PA Foam can significantly contribute to the quality of this new in-vehicle living space via the insulation and reduction of noise radiating from the car itself, as well as reducing noise coming from the outside. Possible applications can be found in the roof and hood, but also in the seat and floor structure.
Production volume varies greatly with product size, wall thickness, can multiple tools be mounted at once, etc. Cycle times are similar to traditional gas fired moulding (that is to say, heating times are similar - cooling times tend to be faster because we radiatively target the tool, not the surrounding machinery and thus there is less mass to cool).
Foam beads made of PA can be processed using the steam molding process on standard polystyrene molding equipment. Furthermore, a significant reduction of resin for the production process can be achieved, contributing to an overall cost reduction.
Arrays of sun-tracking mirrors called heliostats concentrate thousands of watts of heat onto the mould, heating it quickly without the emissions and cost of natural gas. Depending on local market conditions product cost 15-30% less to make with SRM than traditional equipment.
Due to low CapEx (@ 10% of a traditional factory/machine) it is cost effective to run multiple systems in parallel during sunlight hours, then if needed do secondary operations on a second shift.
Asahi Kasei is one of only four fully integrated PA manufacturers worldwide – and is able to produce PA 66 from monomer to compound. Based on this expertise, the company is currently developing the foam bead material PA Foam– the first of its kind worldwide. It is offering solutions to both aforementioned challenges in the automotive industry – stiffness, mechanical strength and heat resistance for use in structural lightweight applications of cars, and noise reducing characteristics.
At the same time these materials have to live up to the high safety standards of the automotive industry, and to provide solutions to changing and tightening regulations worldwide. Plastics and foams, with their broad range of properties, will become a key in this field according to Asahi Kasei, contributing to a reduction of CO2 emissions of conventional passenger cars with combustion engines, and a longer driving distance for electric cars.
PA Foam features the typical heat, chemical and oil resistant properties of polyamide, combined with outstanding rigidity or noise reducing quality depending on the shape of the beads. PA Foam consisting of round-shaped beads features strong rigidity, making it a promising alternative material for aluminum and metal in structural applications, as well as for use for insulators, ducts, spacers, or other lightweight parts of the battery case of electrified vehicles.
LightManufacturing is a company innovating in sustainable plastic moulding with its Solar Rotational Moulding (SRM) process. Unlike traditional methods that heat moulds with fossil fuels, SRM uses a system of mirrors (heliostats) to concentrate sunlight. This process significantly reduces the environmental impact of plastic production.
Our CONEX containerised systems are transported like any other shipping container (crane/truck/forklift etc) and don’t require infrastructure - e.g. a building with a poured concrete floor, utilities, etc. They are placed directly on the ground, and our heliostats deploy on weighted ‘pods’ which require no digging. This factory in a box approach is highly scalable, and even re-deployable if market conditions change. No sunk costs!
Our Solar Rotational Moulding (SRM) systems reflect heat from the sun onto a rotational mould to eliminate the need for fossil fuels.
Editor Rebekah Jordan spoke to LightManufacturing's CEO Karl von Kries to learn more about the company's SRM systems that can achieve even heat distribution through a combination of mould rotation and controlled heating during sunlight hours. The interview also delves into the technology's high level of automation, which allows for precise temperature control and consistent part quality.
Any thermoplastic used in traditional rotomoulding can be used in SRM - most common resins are polyethylene and polypropylene, but PVC, Nylon, and Polycarbonate are also rotomolded.
With ongoing disruptive megatrends in the automotive industry, auto OEMs and suppliers are facing strong pressure to innovate according to materials supplier Asahi Kasei. “New, innovative solutions are in high demand,” the Japanese firm says. The company claims that its newly developed polyamide (PA) beads foam offers unique possibilities for lightweight and noise reducing applications.
Another challenge for the automotive industry is the tightening of noise regulations. With Regulation No. 51-031 issued by the United Nations in 2016, the noise level emitted to the outside must be continuously reduced in newly manufactured vehicles.
Disruptive CASE (Connected – Autonomous – Shared – Electrified) megatrends are leveraging the pressure to innovate on the automotive industry to new heights. In addition to changing consumer needs, EU legislation concerning the reduction of CO2 emissions has been significantly pushing demand for new and innovative lightweight materials as a substitute for metal and aluminum parts.
Stephen has been with PlasticsToday and its preceding publications Modern Plastics and Injection Molding since 1992, throughout this time based in the Asia Pacific region, including stints in Japan, Australia, and his current location Singapore. His current beat focuses on automotive. Stephen is an avid folding bicycle rider, often taking his bike on overseas business trips, and is a proud dachshund owner.
As mentioned above, we estimate CapEx for SRM is @ 10% of traditional moulding systems including building / infrastructure costs. This is important, but quickly dwarfed by the reduction in product cost. Also important is our ability to supply customers and markets from nearby locations; because deploying SRM does not require infrastructure but just ‘raw land’ we deploy near-to-the-need and greatly reduce transportation costs and associated emissions. LightManufacturing currently does not offer SRM systems for sale, but rather provides moulding-as-a-service for partner brands.
This is a key point: our system are ~highly~ automated in a way not possible with traditional systems. Recall that traditional moulding systems have the mould in a 300C+ oven, deadly to servo motors, complex electronics, many sensors etc. It’s a harsh environment. As a result most traditional moulding systems temporarily monitor plastic temperatures using a sensor package in a chilled box, then use a ‘best guess’ for how long to cook the part.
Our machines adapt cycle times to varying solar conditions and always produce a well-cured part - likewise the machines automatically begin cooling with fans, cool the parts to an ideal de-moulding temperature then ‘beep’ and stop, waiting for the operator to remove the finished product.
Further, PA Foam with a C- or macaroni-shape provides noise insulation in addition to the typical polyamide properties. Potential applications can be found everywhere around the car, especially in the engine compartment, where the material can unfold its unique qualities. Used for engine covers, for example, it not only contributes to lightweight, but also significantly reduces the radiating engine noise, making the car quieter overall.
In some markets like Hawaii LM sell product B2C (direct to customer); there we sell water tanks at prices 30-40% less than our traditional rotomoulding competitors.
GETTING A QUOTE WITH LK-MOULD IS FREE AND SIMPLE.
FIND MORE OF OUR SERVICES:
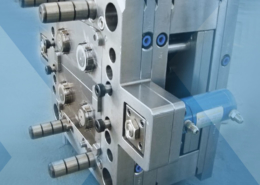
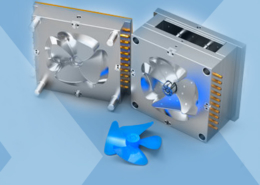
Plastic Molding

Rapid Prototyping
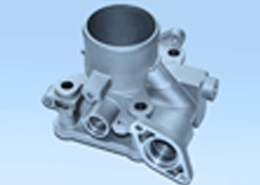
Pressure Die Casting
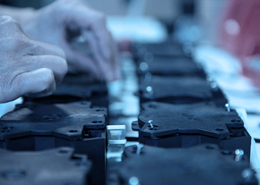
Parts Assembly
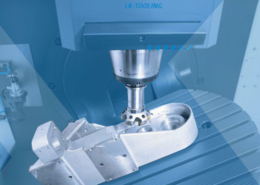