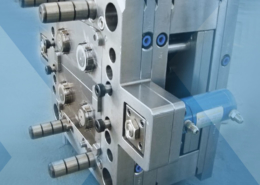
Engel Installs World's Largest Tech Center Injection Molding Machine - shot mold
Author:gly Date: 2024-09-30
Establishing an Irish office is also part of a post-Brexit insulation strategy that will moderate any potential concerns Irish moulders may have about dealing with a UK machinery supplier. A permanent in-country service and support base will facilitate timely spare parts sourcing and trading in euros without incurring hefty exchange fees. We firmly believe that Ireland’s talent base and this supportive infrastructure will continue to make Ireland very attractive to inward investment, especially in medical and biotechology R&D.
Researchers continue to introduce complex new TPEs like metallocene-catalyzed polyolefin plastomers (POPs) and elastomers (POEs). These very-low-molecular weight, linear low-density polyethylenes (VLMW-LLDPE) are becoming common in flexible packaging films and in molded goods that see light-duty and moderate temperatures.
TPEs can also be engineered for barrier applications like dynamic-seal gaskets and static-seal stoppers. Potential applications include syringes and intravenous delivery systems, and blood-collection devices.
Copolymerizing thermoplastic olefins (TPOs) in a reactor rather than through melt-blending polypropylene (PP) with an elastomer is another relatively recent move.
Fewer potential avenues for failure means engineers need to do fewer tests to prove the assembly will safely perform its function. In highly regulated industries, like the medical-device arena, this can mean a quicker, less-costly route to regulatory approval.
To enhance patient safety, there’s a drive towards using new and more innovative regulated materials with a better flow and high impact strength to mould components. The EU Medical Device regulations came into force 26 May 2021, following a one-year extension due to the pandemic. In Vitro Diagnostic medical device regulations (known as IVDR) become effective 26 May 2022. In the UK, the market is currently regulated by the UK Medicines and Healthcare products Regulatory Agency (MHRA).
TPEs also have good colorability and accept special visual effects. Designers can overmold a clear TPE onto a patterned or colored substrate or use a pearlescent or tinted material to create the desired look. Custom-colored TPEs, which can be formulated to have a shiny or matte finish, let manufacturers skip secondary operations like painting or coating.
New TPVs have also been engineered to resist the heat and oil contamination that go with underthe- hood automotive applications where thermoset rubbers have traditionally dominated.
Understanding TPEsThermoplastic elastomers are low-modulus, flexible materials. Their building-block polymers vary and can include styrenic block copolymers, olefins, thermoplastics, and other materials.
On a basic level, TPEs combine the processing advantages and recycling potential of thermoplastics with the flexibility, low modulus, and soft touch of elastomers. TPEs have made their way into industries including medical, electronics, sporting goods, consumer products, and automotive. The polymers’ softness and suppleness, in particular, add consumer appeal to products made with TPEs.
Sumitomo (SHI) Demag recently supplied a 75 tonne IntElect all-electric injection moulding machine to Avenue, a Nolato Company, in Sligo, Ireland. The investment supports the growth in the company’s healthcare division, providing dedicated capacity to mould precision parts during the product development phase. With demand for its medical device injection moulding and tool-building services increasing, Avenue recently installed a new 100 sqm ISO Class 8 cleanroom area.
The variety of chemistries available lets designers tailor materials for properties like clarity, injection moldability, and abrasion resistance. But all TPEs have room-temperature elasticity. Most TPEs can stretch repeatedly to at least twice their original length, some up to 10 times their length, without significant permanent deformation.
The IntElect machine met Avenue’s brief for a small footprint machine for carrying out test runs during the development phase of projects.
In addition to the varied properties that can be compounded into TPEs, the materials can also cut finished part cost by up to 30%. Although TPEs themselves can cost as much as 50% more than thermosets, greater processing efficiency gives the materials better cost-effectiveness overall.
For example, TPEs from GLS Thermoplastic Elastomers, a PolyOne Co., can be customized to provide a unique flow, hardness, UV resistance, degree of transparency, and meet regulatory requirements such as FDA or USP Class VI.
Authored by: Joe KutkaTechnology Launch ManagerGLS Thermoplastic Elastomers, a PolyOne Co.McHenry, Ill.Edited by Jessica Shapiro[email protected]
A two-phase molecular structure gives TPEs their combination of strength and flexibility. Amorphous areas, or blocks, in the polymer are soft and provide its elastomeric nature, making the material supple and flexible. The harder crystalline blocks give tensile strength and resistance to chemicals and heat.
One example of TPE overmolding is a vial stopper for medical applications. The original part consisted of a polypropylene (PP) sleeve that positioned a separate thermoset elastomer button over the vial. Engineers developed a single two-shot part where TPE is overmolded and fuse-bonded to PP via two-shot injection molding. In addition to halving the number of parts, the fuse-bonding cut down on the potential for leakage failures.
For example, when parts are being produced on multi-cavity tools, like pipettes, robots are programmed to remove and place the components into cavity-assigned racks. This means that if an issue with cavity 1 arises, the rack containing all corresponding cavity 1 parts can be isolated and the rack recalled, with all the production information stored in the MES.
TPEs gain their strength from this type of physical cross-linking; they are not chemically cross-linked or vulcanized, as thermoset rubber is. The lack of chemical cross-linking means TPEs are appropriate for recycling.
In tension, most TPE blends can withstand 400 to 1,000 psi while specially formulated TPEs, like thermoplastic polyurethanes (TPUs), can exceed 5,000-psi tensile strength. The range of strengths reflects the myriad chemistries TPEs encompass.
This creates some complications in relation to the CE marking process on medical devices as the UKCA (UK Conformity Assessed) mark will replace the longstanding CE mark for goods, including medical devices, sold within England, Wales and Scotland. As there’s no hard border in Ireland, the CE mark still applies there.
Advanced batch tracking, contact-free inspection using cameras, and highly automated assembly are among the latest developments to meet the medical device market’s precision and quality control requirements. Traceability is not just about mandatory information and supply chain tracking. Real-time traceability is about being able to call up data and verify the exact settings used on the injection moulding machine when that individual plastic part was made, making connectivity to a Management Executive System (MES) vital.
Chemical joining over the larger surface area of the part helps prevent separation over a long lifespan of rigorous use. Designers can use single, seamless assembly overmolding to reduce breakage or leakage that can occur when joining components with adhesives or mechanical fasteners. Another option with overmolding is to create an additional mechanical interlock between the substrate and overmolded polymer.
Some TPEs are engineered to provide 10 times lower oxygen permeation than standard TPEs, about the same as butyl rubber. These materials can provide an excellent defense against water loss or absorption, according to a presentation given by Masahiro Asada at the 2006 TPE Conference in Akron, Ohio.
For example, styrene-ethylene/butylene- styrene (SEBS), a styrenic block copolymer (SBC), is made of a styrene hard phase and a butadiene elastomer phase. The crystalline areas form physical crosslinks in the polymer structure while the amorphous phase provides the material’s elastic properties.
TPEs like GLS’ Versaflex form a transparent overmold layer on various substrates, including polycarbonate (PC), acrylonitrile-butadiene-styrene (ABS), and nylon (PA6). The material is designed for insert and two-shot molding. Some grades let process designers skip a step in drying the TPE and the substrate onto which it will be overmolded, saving process time and money.
Plastic moulding continues to be used for many medical applications, including manufacturing implantable medical device components, test tubes, beakers, casings and housings for laboratory and medical equipment, drug delivery components and surgical equipment. With demand for medical devices at an all-time high across hospitals and laboratories thanks to COVID-19, this has had a positive impact on market growth.
Processors can also skip the aftermold vulcanization step thermosets need. Depending on the raw materials, premold mixing can also be shortened or eliminated.
To meet multiple customer requirements, TPE suppliers alloy and compound polymer building blocks. Engineers can tailor TPEs to have a softer feel, more vibrant color, a nonslip surface, or vibration damping properties.
Part consolidation is also a key concern for engineers replacing assemblies that include metal components and separate thermoset rubber gaskets. Overmolding a barrier layer onto a high-strength substrate keeps metal ions, rubber compounds, and additives from leaching into drugs or other formulations, according to a presentation David Marshall and Hideki Ishikawa gave at Antec 2006.
Some compounders, including GLS, have developed clear, nonplasticized products that can be sterilized. These grades let manufacturers lay aside concerns about the migration of regulated plasticizers from packaging into the package contents.
Gerard Henn, Avenue’s general manager, said: “All medical programmes are lengthy as it can take two to three years to obtain approvals from the authorities, so there are many months of testing before a component or mould is ready to be scaled up to mass production.”
TPEs can also be sterilized using other standard methods such as steam, ethylene oxide (EtO), e-beam, and gamma radiation.
Working with TPEsTPEs can be extruded, blow molded, and thermoformed. Manufacturers can also injection mold them. High-pressure injection molding can yield thin-walled TPE parts. Some grades of the material also support insert molding and one and two-shot molding.
Any of these conventional processing techniques work with TPEs using conventional molding equipment. Thus, designers often substitute TPEs for traditional materials to improve product performance, cut down on cycle time, lower equipment costs, or eliminate secondary operations.
That efficiency comes from cycling waste and defective parts back into raw material feeds, shortening process cycles, reducing equipment requirements, and the potential for part consolidation.
Adding TPE’s resilience and softer touch can improve comfort, cushioning, ergonomics, and safety for a part’s end users. Using TPEs, designers can ensure that equipment is safer to operate and easier to handle by helping to improve grip, provide better nonskid surfaces, and maintain flexibility at lower temperatures. The materials can also supply vibration damping to help minimize motor noise, vibration transmission, or impact shock.
Darren Herron, UK national sales manager at Sumitomo Demag, analyses the injection moulding market and what is driving new developments for medical applications.
Manufacturers looking to TPEs should understand the broad range of thermoplastic elastomers, each of which has unique attributes and deficiencies. By working with a knowledgeable supplier, engineers can take advantage of a large portfolio of engineered TPEs to identify the best material and processing techniques for a given final product.
TPE targetsIn 2009 global TPE demand is expected to grow more than 6% to 3.1 million metric tons for a market value of approximately $11.4 billion. Part of this growth comes from applications where TPEs have directly displaced more traditional materials like thermoset rubbers. But much of the expansion is due to the Chinese market.
High-performance TPEs can also be overmolded onto rigid plastic parts. Overmolding eliminates potential points of failure by creating a chemical bond between a plastic substrate and the TPE.
Key points• Compounders can give TPEs a variety of properties, from a soft touch to high-temperature-sterilization resistance.• TPEs are physically, not chemically, cross-linked, so they are easy to process and recycle.• Many TPEs are plasticizer-free and adhere to new federal and international regulations.
For example, TPEs replace lowdensity polyethylene (PE) in the blow-fill-seal process for making eye and nasal-drop bottles. With TPEs, the bottles can be transparent and more flexible than with PE.
Bottles made with TPEs can also survive higher temperatures. This gives packagers the option of autoclave sterilization at 121°C, a temperature close to the melting point of many grades of PE. The U.S. Food and Drug Administration (FDA) favors high-temperature sterilization.
The global medical injection moulding market size was valued at $1.38 billion in 2019 and is expected to grow at a compound annual growth rate (CAGR) of 8.2% between 2020 and 2027. Much of this is being driven by advances in the home healthcare sector and an ageing population, which WHO predicts will double by 2050.
The automotive industry remains the largest market for TPEs where it finds a home in the soft-touch overmolding ubiquitous in automotive interiors. TPO and thermoplastic vulcanizate (TPV) use inside vehicles also continues to expand. The two material classes tend to cost less than more commonly used TPUs. They can also be processed with lower-cost two-shot molding.
In other industries, stricter regulations aimed at product safety are driving companies to change their end products. FDA and European Union rules regarding additives which are potentially environmentally harmful — like phthalate plasticizers and bisphenol A — are forcing engineers to innovate. TPEs enable manufacturers to replace traditional materials that have become problematic with nonplasticized ones that meet the same needs.
Thermoplastic elastomers (TPEs) are showing up in more and more places these days. The array of polymers that fall under the TPE umbrella, not to mention the color, texture, and property options they offer designers, can be truly bewildering. But sorting out the TPE universe can help a designer cut part count, shorten process time, and improve product durability.
With a large proportion of Sumitomo (SHI) Demag’s Irish customers in the medical market in Ireland, we last year opened a service and support office in Limerick, Ireland. This was to support its installed base of predominantly all-electric machines, providing on-the-ground preventative and reactive machine maintenance and troubleshooting support.
ResourcesGLS Thermoplastic Elastomers, glscorporation.com “How to develop a soft touch,” MACHINE DESIGN, June 2, 2005“Hard rules for soft-touch overmolding,” MACHINE DESIGN, May 9, 2002
The machine’s small footprint is down to the use of its own motors and drives. The model also has wide tie bar spacing and high clamp force for its size, allowing the use of larger moulds than would normally be accommodated by a 75-tonne machine.
China, which is already the world’s largest TPE market in terms of metric tons, is expected to scale up in many industries for a predicted 20% growth rate through 2012.
Additionally, TPE properties such as softer touch and ergonomic grip can also brings ease-of-use to medical devices. Home-use medical products, a growing market segment where minimally trained users depend on ergonomic products, is another good fit for TPEs.
GETTING A QUOTE WITH LK-MOULD IS FREE AND SIMPLE.
FIND MORE OF OUR SERVICES:
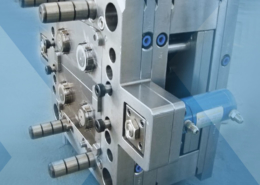
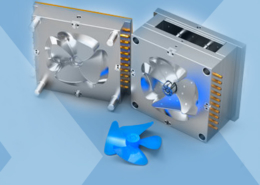
Plastic Molding

Rapid Prototyping
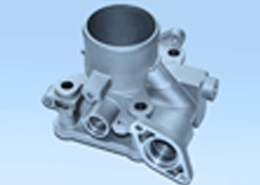
Pressure Die Casting
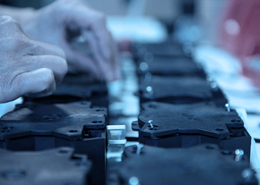
Parts Assembly
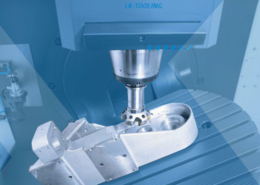