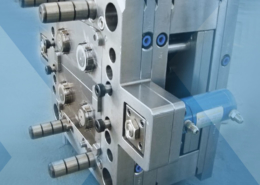
Exploring Plastic Injection Manufacturing: Revolutionizing Production Processes
Author:gly Date: 2024-06-08
Plastic injection manufacturing stands as a cornerstone of modern industrial processes, revolutionizing the way products are designed, developed, and mass-produced. In this comprehensive exploration, we delve into the intricacies of plastic injection manufacturing, examining its techniques, applications, environmental impact, and future prospects.
Techniques and Processes
Injection Molding Process
The injection molding process entails injecting molten plastic into a mold cavity, where it cools and solidifies to form the desired part. This technique allows for the production of complex geometries with high precision and repeatability. Various factors, such as temperature, pressure, and cooling rate, influence the final quality of the product.
Mold Design and Fabrication
Mold design plays a critical role in plastic injection manufacturing. Advanced CAD/CAM software enables engineers to create intricate mold designs, optimizing for factors like material flow, cooling efficiency, and part ejection. The fabrication of molds involves precision machining techniques, such as CNC milling and electrical discharge machining (EDM), ensuring the highest level of accuracy.
Material Selection and Processing
The choice of plastic material profoundly impacts the performance and characteristics of the final product. Engineers must consider factors such as strength, flexibility, thermal stability, and cost when selecting the appropriate resin. Material processing techniques, including compounding and blending, further enhance the properties of the raw plastic, tailoring it to specific application requirements.
Applications and Industries
Automotive Industry
Plastic injection manufacturing has revolutionized the automotive industry by enabling the production of lightweight, durable components. From interior trim panels to exterior body parts, injection-molded plastics play a crucial role in modern vehicle design, offering versatility, cost-effectiveness, and design freedom.
Consumer Electronics
The consumer electronics sector heavily relies on plastic injection manufacturing for the production of casings, connectors, and other intricate components. The ability to mass-produce complex parts with tight tolerances has driven innovation in devices such as smartphones, laptops, and home appliances, meeting consumer demands for sleek design and functionality.
Medical Devices
In the medical field, plastic injection manufacturing ensures the production of sterile, high-precision components used in diagnostic equipment, surgical instruments, and drug delivery systems. The biocompatibility of certain plastics, coupled with stringent quality control measures, makes injection molding indispensable for meeting the stringent regulatory standards of the healthcare industry.
Environmental Considerations
Sustainability Initiatives
Despite its numerous advantages, plastic injection manufacturing faces scrutiny due to its environmental impact. Manufacturers are increasingly adopting sustainable practices, such as using recycled materials, optimizing energy efficiency, and implementing closed-loop systems to minimize waste generation and carbon footprint.
Biodegradable Plastics
The development of biodegradable plastics presents a promising solution to mitigate the environmental concerns associated with traditional polymers. Bioplastics derived from renewable sources, such as corn starch or sugarcane, offer comparable performance to their petroleum-based counterparts while being compostable or biodegradable, thus reducing reliance on fossil fuels and minimizing pollution.
Life Cycle Assessment
A comprehensive life cycle assessment (LCA) is essential for evaluating the environmental impact of plastic injection manufacturing from cradle to grave. By analyzing factors such as raw material extraction, production processes, transportation, product use, and end-of-life disposal, manufacturers can identify opportunities for improvement and implement eco-friendly strategies across the entire value chain.
Future Outlook and Innovations
Industry 4.0 Integration
The integration of digital technologies, such as IoT sensors, artificial intelligence, and data analytics, is poised to revolutionize plastic injection manufacturing under the Industry 4.0 paradigm. Smart factories equipped with real-time monitoring and predictive maintenance capabilities will optimize production efficiency, minimize downtime, and enable agile response to market demands.
Additive Manufacturing Hybridization
The convergence of plastic injection molding with additive manufacturing processes, known as hybrid manufacturing, offers unprecedented design freedom and customization options. By combining the speed and scalability of injection molding with the complexity and versatility of 3D printing, manufacturers can efficiently produce low-volume, high-value parts with intricate geometries and tailored properties.
Advanced Material Development
The ongoing research and development efforts in material science are yielding novel polymers with enhanced properties, such as improved strength, heat resistance, and recyclability. From bio-based plastics to nano-composites, these advanced materials hold the key to unlocking new possibilities in plastic injection manufacturing, addressing performance requirements while minimizing environmental impact.
Conclusion: Shaping the Future of Manufacturing
In conclusion, plastic injection manufacturing stands as a cornerstone of modern industrial processes, offering unparalleled versatility, efficiency, and scalability. From automotive and electronics to medical and consumer goods, its applications are ubiquitous, driving innovation across various industries. However, as we navigate towards a more sustainable future, it is imperative for manufacturers to embrace eco-friendly practices, adopt innovative technologies, and collaborate towards minimizing environmental impact while maximizing efficiency and performance. By leveraging the latest advancements in materials, processes, and digitalization, plastic injection manufacturing is poised to continue shaping the future of manufacturing, ushering in an era of sustainable innovation and global competitiveness.
GETTING A QUOTE WITH LK-MOULD IS FREE AND SIMPLE.
FIND MORE OF OUR SERVICES:
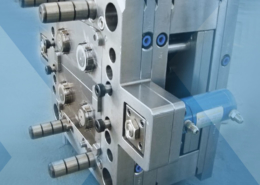
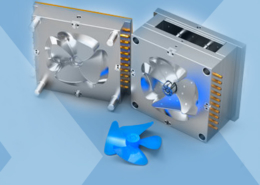
Plastic Molding

Rapid Prototyping
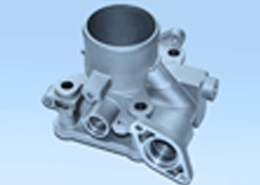
Pressure Die Casting
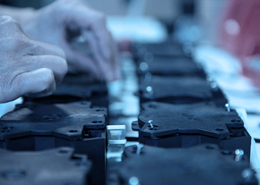
Parts Assembly
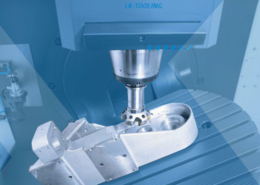