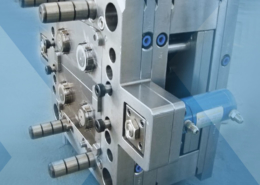
Engel Delivers Its Largest-Ever Molding Machines to US Company - us injection mo
Author:gly Date: 2024-09-30
Currently, Prism operates four molding facilities: In addition to the plant at its Chesterfield headquarters, the company has a molding footprint in Port Huron, MI; Harlingen, TX; and Meadville, PA. Prism serves the automotive and industrial markets with various components including safety parts, connectors and sensors, electronics housings and steering and drivetrain parts.
Those are just two examples of how Prism’s Technology First approach solves problems, but the benefits are far reaching. It helps Prism maintain lean operational costs, which allows the company to compete on a global scale and win back jobs back from Europe, China and Mexico.
As a fluorescent marker has been added to the thermoplastic component, the box – which is not identifiable by the end consumer – is clearly marked. Even a fraction is enough to clearly identify it with a laser detector through its characteristic fluorescence. This technology from Arburg's partner Polysecure allows products to be clearly traced, distinguished from counterfeits and, if necessary, sorted by material.
The arburgXworld customer portal gives you access to a wide range of digital apps and features that make your daily work easier.
For reliable performance, a slimline design, and an unbeatable price, there is only one choice: the new ALLROUNDER 720 E GOLDEN ELECTRIC!
For reliable performance, a slimline design and an unbeatable price, there is only one choice: the new ALLROUNDER 720 E GOLDEN ELECTRIC!
Prism recently installed a new molding line with three collaborative robots. One robot hands a part to another robot, which hands it off to a third robot, which performs a final inspection and places the part in a box.
Benefit from our expertise and lower the costs for your injection moulding production by optimising your energy requirement.
“Because of NAFTA, we’re in great shape and can boast that our components are 100% made in the USA,” Ignatowski added. “We can compete with low-cost countries because of our approach to technology, lean operations and designing in quality throughout the process. In fact, while others are shipping parts from China, we’re shipping products to China.”
The company’s “Technology First” approach allows it to compete on a global scale and win back jobs from Europe, China and Mexico.
Ignatowski told of a recent high-level meeting with a customer in Prism’s Texas plant. The customer told Prism that it was “one of the best suppliers but that it wanted to put as much business in Mexico, as possible.” They wanted us to site a plant in Mexico, said Ignatowski. “I told them we’ll do that, but we’ll have to add cost to the components because we have no labor content at the Texas plant, which means we won’t realize any labor savings, and the infrastructure costs are higher in Mexico. We’re now getting a significant amount of business from the customer as it localizes its requirements in Texas, and we’re shipping parts to its plant in Mexico. We’re able to do that because of our automation and subsequent quality record. It comes down to the right jobs for the right work.
Technology has also brought another benefit to Prism. Because of its rapid growth, the company identified a need for additional warehouse space. While some companies might knock out a wall and add on a brick-and-mortar solution, Prism resolved its problem with technology. “We came up with the Very Narrow Aisle Racking system that greatly reduced the space separating rack units,” Ignatowski explained. “Pallets are placed and retrieved using an automated forklift that follows an embedded wire in the floor. An operator drives the fork lift, but in the aisle they can only go forward and backward. That system allows us to have three inches of clearance on the fork lift in the aisle. We implemented this in Chesterfield and the new acquisition in Pennsylvania, as well.”
As Prism wins more programs, keeping manufacturing on American soil, the result is more high-tech jobs for skilled American workers.
The “Technology First” mindset has been a constant at Prism Plastics (Chesterfield, MI ) since the day the custom injection molding company was founded in 1999. “That was a time when molders were plentiful,” said Jeff Ignatowski, Director of Marketing, during a phone interview with PlasticsToday. “We decided then that we’d use technology. We chose the highest technology available in molding machines and robotics. We then standardized equipment: By blending automation and the human element, we have become efficient and cost effective. That mindset exists across the board, so that each of our plants operates exactly the same way.”
As manufacturing became global, Prism relied on its automation technology to remain competitive. Under the Technology First banner, the company has removed almost all manufacturing labor costs from its cost model. “We’re not showing labor in our cost model breakout—that is what technology has done for us,” said Ignatowski.
An ALLROUNDER MORE 2000 in the Comfort performance variant and with two electric injection units will produce a two-component multifunctional box made of thermoplastic and self-adhesive liquid silicone. The two components are injected directly via a cold or hot runner system, resulting in waste-free production. The associated LSR dosing unit is integrated via OPC UA and the Euromap interface 82.3 into the GESTICA controller. The cycle time is around 60 seconds. First to be produced is the PBT pre-moulded part, which is then converted in the 1+1-cavity mould so that the LSR component can finally be injected. The complex 3D contour of the component and precise positioning of the pre-moulded part in the second mould station place high demands on the gripper and robotic system. The 164-gram box is finally removed by a MULTILIFT V 30 linear robotic system and placed on a conveyor belt.
One advantage of Prism’s operating philosophy is that it has allowed the company to build its human resource requirements around its installed automation technology. Ignatowski explained that while some companies might hire a large number of people at first, then decide to automate and lay off 80% of their work force, Prism deployed automation technology from the get go.
At Fakuma 2023, an ALLROUNDER MORE 2000 with two electric injection units will demonstrate how functional integration can save time and costs in multi-component injection moulding.
Until she retired in September 2021, Clare Goldsberry reported on the plastics industry for more than 30 years. In addition to the 10,000+ articles she has written, by her own estimation, she is the author of several books, including The Business of Injection Molding: How to succeed as a custom molder and Purchasing Injection Molds: A buyers guide. Goldsberry is a member of the Plastics Pioneers Association. She reflected on her long career in "Time to Say Good-Bye."
“We’ve not eliminated jobs and, in fact, automation has increased the number of jobs we have,” said Ignatowski. He acknowledges that the jobs are more technical in nature: “The people who run the plants are called Process Technicians. Robotics do the repetitive tasks while people perform the technical jobs, [but] we have never replaced a person because of the implementation of technology,” stressed Ignatowski.
GETTING A QUOTE WITH LK-MOULD IS FREE AND SIMPLE.
FIND MORE OF OUR SERVICES:
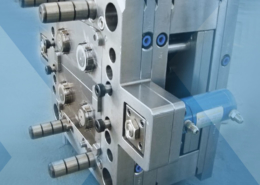
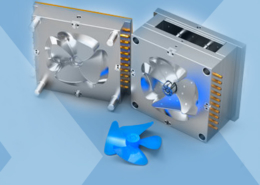
Plastic Molding

Rapid Prototyping
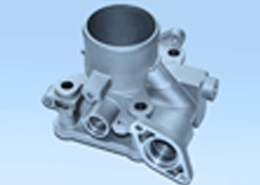
Pressure Die Casting
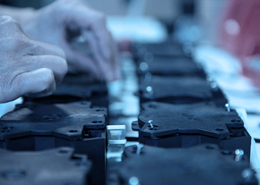
Parts Assembly
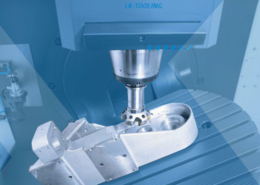