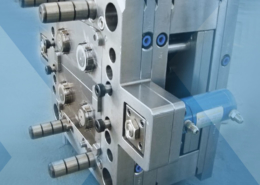
Engel Delivers Its Largest-Ever Molding Machines to US Company - large plastic m
Author:gly Date: 2024-09-30
Clark said he provides a separate quote for the mold qualification and validation requirements, and breaks it all out separately. "It gets complicated," he said.
Paper over plastic, freeze over refrigerate, and bread boxes galore. Madelyn Osten, former head baker at Sullivan Street Bakery's Miami outpost, reveals the biggest tips for successfully storing bread, so you can get the most out of your favorite loaf while avoiding unwanted mold, crust, and moisture.
"A fresh loaf of bread is best eaten within two to three days. If you plan on devouring it right away, then keeping it in a paper bag on the counter is the move. While storing in plastic seems like the right idea, this actually encourages mold growth, resulting in the bread going bad much faster. I also save the heels of my bread and use them as covers for the cut side of my loaf. Keeping the cut side of your loaf as unexposed as possible will also help retain its freshness."
"Where you store your loaf can be just as important as how you store it. Bread goes on top of the refrigerator, right? Try again! Keeping bread on the fridge will cause paper-bagged bread to dry out, and plastic-bagged bread to mold faster. This comes from all the heat your fridge is putting out. Same for storing near a dishwasher; the excess heat and moisture these appliances give off is not bread-friendly. Try to store bread in a cool and dry area of your kitchen. If not out on the counter, then in a cabinet or a deep drawer."
It was only a couple of decades ago - what many call the "good old days" - when moldmakers would take a part print, design and build the mold. They would then provide a quick tryout - usually at a local molding company - to prove the dimensional capabilities of the mold's cavities to make conforming parts, and then ship the mold to the customer all within a 12 to 16-week timeframe.
New York-based Sullivan Street Bakery, founded in 1994 by James Beard Award-winning baker Jim Lahey, brought its highly acclaimed bread down south in 2017. Today, it operates a production facility in Miami's Little Haiti neighborhood, baking and distributing its rustic bread to a number of restaurants, hotels, country clubs, and venues in the South Florida region. The bakery's retail partnerships with shops like Milam's Market make bread storage even more important to its operation.
Moldmakers are known to be creative people who can come up with innovative solutions to sometimes very complex mold and molding challenges. OEMs depend on the moldmaker to take what is often a "draft" design of a plastic component and, using their expertise, re-design the part to accommodate a more optimal geometry for molding. "We can do it, yes we're problems solvers, creative people, but how do we get paid for it?" Peterson said. "The trick is to get compensated for it correctly."
Westminster Tool Inc. in Plainfield, CT, created a technology center and installed three injection molding presses over the past year to accommodate mold qualification from its customers, primarily in the medical and consumer packaging markets that the company serves. "We see this as a trend," said Mark Ypsilantis, VP of sales & marketing. "While our consumer packaging customers have required this service offering from time-to-time, with our medical customers, it has become the norm. For us to provide mold qualification and process validation is critical to their speed-to-market."
To do that, mold manufacturers must increase their capabilities and services particularly in the area of mold qualification and process validation.
"Bread boxes are a great way to keep bread, and a fun way to add style to your kitchen. They have small holes in them, which allow just a little air to circulate, keeping bread from molding. If you have pest concerns and prefer to keep bread in an airtight container, try tossing in a slice of bread with your loaf. The slice with more surface area will attract water and help control the moisture content in your container."
Until she retired in September 2021, Clare Goldsberry reported on the plastics industry for more than 30 years. In addition to the 10,000+ articles she has written, by her own estimation, she is the author of several books, including The Business of Injection Molding: How to succeed as a custom molder and Purchasing Injection Molds: A buyers guide. Goldsberry is a member of the Plastics Pioneers Association. She reflected on her long career in "Time to Say Good-Bye."
Today's mold manufacturers are asked to go beyond simple mold sampling "tryout." Those services often begin with dimensional shrinkage, cooling and warp analysis and studies on the melt flow balance, just to mention a few. In some cases, OEMs require the mold manufacturer to validate the molding process by running full production for 24-hour periods, and perform CPKs. Another service some OEMs require includes building the entire molding cell, complete with automation, which means that designing and building the mold is the easy part.
A mold for an undisclosed customer in the sampling press at Westminster Tool's Technology Center, awaiting qualification.
Tim Peterson, VP of Industrial Molds Group, comprised of Industrial Molds and custom injection molder Pyramid Plastics, concurs with Clark and Ypsilantis: "Our customers are pushing a lot more responsibility downhill to the tool maker. I think it's something that every customer is looking for - they're pushing for it," Peterson told PlasticsToday. Industrial Molds qualifies and validates its customers' molds at sister company Pyramid Plastics, located not far from the Industrial Molds facility.
Today's injection mold manufacturers are much more than 'just moldmakers.' As OEMs - particularly those in the medical and automotive industries - become more and more dependent upon their supply chain to go the extra mile in engineering and developing new products, the moldmaker plays a larger role in ensuring these molds are production-ready.To do that, mold manufacturers must increase their capabilities and services particularly in the area of mold qualification and process validation.
Mold qualification and process validation is "a growing part of our business," said Wade Clark, president of Electroform Co. Inc. With seven presses up to 600 tons to accommodate the various sized molds the company designs and builds, Clark has invested heavily to provide theses additional services customers are demanding.
Industrial Molds recently did an extensive mold validation for an automotive customer and quoted the entire program as a turnkey job. "It wasn't the tryout that was the biggest expense, it was the part inspection. In just the measurement portion we had $10,000 into it. It's a new twist on us and we didn't realize the expense that was involved. It often costs us $15,000 to validate a tool, but the customer doesn't want to pay for it. If it cost them $20,000 to validate a tool, they're getting a bargain."
Ypsilantis acknowledges that the additional resources needed to provide these services can be extensive. In addition to its staff of mold designers, programmers, and moldmakers, Westminster hired two RJG certified Master Molders on board to provide a scientific molding process that can be replicated in any production facility. However, Westminster provides this particular service upon request.
"One of the issues for us is that we do tooling with extreme geometry, and 2- and 3-shot tooling, which means that not many molders can sample for us. They often don't have the right size press so that forced me into multi-shot and multiple presses to do sampling. Just about every tool we build now needs FAT [Factory Acceptance Testing] and qualification. Each customer has their own procedures they want us to follow so we have to abide by that."
While these added services are an additional source of revenue, Clark told PlasticsToday that the disadvantage is that "so many more customers expect us to do more for them" which requires a big investment in machine resources and personnel. "When you have the presses like we have it can get away from you do. It's a convenience but also a detriment cost wise. It's very expensive to do all that that we do."
Store and/or access information on a device. Use limited data to select advertising. Create profiles for personalised advertising. Use profiles to select personalised advertising. Create profiles to personalise content. Use profiles to select personalised content. Measure advertising performance. Measure content performance. Understand audiences through statistics or combinations of data from different sources. Develop and improve services. Use limited data to select content. List of Partners (vendors)
Today's injection mold manufacturers are much more than 'just moldmakers.' As OEMs - particularly those in the medical and automotive industries - become more and more dependent upon their supply chain to go the extra mile in engineering and developing new products, the moldmaker plays a larger role in ensuring these molds are production-ready.
"Freezing bread is the best way to preserve that crusty loaf for the longest time possible. Wrap tightly in a freezer bag, either whole or sliced. I like to put wax paper between slices when I freeze, as this makes it easier to take out just what I need. Defrosting a whole frozen loaf in the refrigerator overnight is the best way; out on the counter it can get soggy, and while it will toast just fine, it makes for a better loaf in the fridge. Also, don't forget to unwrap from the freezer bag when defrosting. This keeps any water from pooling while it defrosts. And if defrosting seems daunting, not to worry: You can always reheat bread straight from the freezer. For a whole loaf, try baking at 325 degrees for 25 to 30 minutes, while slices can be popped right in the toaster."
While mold manufacturers have been able to reduce the mold design and build time thanks to cutting edge software and advanced, high-speed machine tool technology, mold manufacturers are now receiving requests for services from customers that go far beyond just building the mold. In fact, several mold manufacturers say that in many cases, depending on the requirements of the customer, it takes longer to qualify a mold and validate the process than it does to design and build the mold - sometimes stretching the lead time for a program out as long as six months.
"While we can't do PPAP for our automotive customers, we've given them a tremendous leg up with get initial mold qualification done - it's more like a tool transfer at that point," Peterson said. "We'll dial in the process and they go with it - they'll buy off on our process."
"If you're looking for a more versatile or eco-friendly way to preserve your bread, try a reusable bread bag. There are more on the market these days and many are machine washable and work great in the freezer. Take them with you to the store and toss that fresh loaf right in. These can be a nice alternative to a paper bag that can get torn and always seems to let crumbs escape onto the counter. Reusable bags are made of breathable materials, so they behave like paper bags without the waste. Ranging from $7 to $20, they're a great investment for a bread (and environment) lover at any level."
"We sample and debug almost every single mold that we manufacture," Ypsilantis said. "The initial mold qualification is identified in our quotation and is typically included in the price of the mold. Process validation services beyond this are identified and line-itemed in the quotation. All of this process data is provided to the customer as part of the injection molding binder/manual created for every mold we build."
GETTING A QUOTE WITH LK-MOULD IS FREE AND SIMPLE.
FIND MORE OF OUR SERVICES:
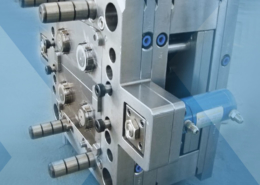
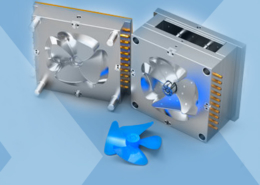
Plastic Molding

Rapid Prototyping
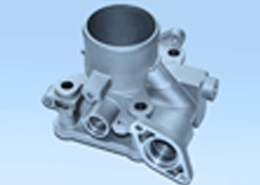
Pressure Die Casting
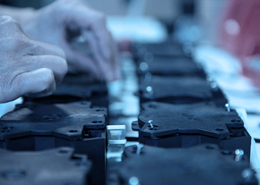
Parts Assembly
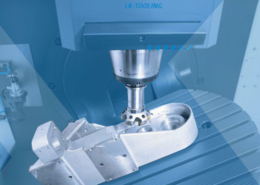