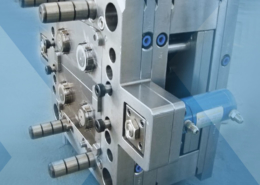
Engel Delivers Its Largest Ever Injection Molding Machines - plastic moulding di
Author:gly Date: 2024-09-30
When [Michael] over at the Teaching Tech YouTube channel bought a hobby injection molding machine a long time ago, one of the plans he had with it was to use it for grinding up waste bits of PLA filament for injection molding. Since the machine was bought from a US shop and [Michael] is based in Australia it required some modifications to adapt it to the local 220+ VAC mains, followed by adding a PID temperature controller and a small compressor to provide the compressed air rather than from a large shop compressor.
Quality management and quality assurance is essential in the medical industry as companies manufacture highly sensible products. Regulations such as Good Manufacturing Practice (GMP) in the US and Medical Device Regulations (MDR) in Europe require companies to comply with strict and ever more extensive standards. They have to keep an impeccable paper trail throughout the entire production processes, just as the saying goes: “If it hasn’t been documented, it doesn't exist.” This need for full documentation puts a lot of pressure on companies. It increases the demand for integrated process solutions that both document and optimise all relevant process parameters. The ComoNeo process monitoring system by Kistler, for instance, accurately measures the pressure in all cavities and compares the resulting curve with the nominal curve. ComoNeoPREDICT uses artificial intelligence to predict product quality based on cavity pressure and temperature curves. All things considered, I believe that there is still a lot of untapped potential for digital solutions.
I suspect the cost of not doing the change has been much much higher than the cost of doing it would have been.. The same with metric. I remember when Aus changed, and yes it was a lot of work. But it was done, and after 50 years nobody would think any different – the US should have done it inthe same time frame.. But yes, I agree, voltage is different, but if you look around the world the US is the only major economy with the low voltage..
With the split-phase system, the US has 220 availabe for all major appliances. You can even get 220 outlets installed for larger window AC units.
Currently, there are software modules and algorithms that allow injection moulders to automatically adjust process parameters if the measurement curve deviates from a previously defined ideal curve. For instance, if the cavity pressure measured by direct, indirect or non-contact sensors is too high or too low, the system can adjust the switch-over point automatically. The Multiflow software module by Kistler balances filling multiple cavities very efficiently. It analyses fill-time differences between the cavities based on cavity pressure. It then adjusts the tip temperature of the hot runner automatically to achieve a more simultaneous filling. Using automation is becoming ever more relevant as we look at a growing shortage of skilled workers on the shop floor.
Within our focus industries, the circular economy and especially the use of recyclates are currently the most pressing topics. While we don’t see the latter reflected in the medical field yet due to regulations, this could change soon if we can provide a solution which reliably and automatically compensates process fluctuations. When companies start to use larger percentages of recyclates in their manufacturing processes, measuring technology becomes even more important, while it will not change as such. Melts containing recyclates have a fluctuating viscosity and as a result, parameters which indicate viscosity changes such as cavity pressure need to be constantly monitored to ensure a high product consistency. Again, AI could also come into play to detect and even predict anomalies.
110V is somewhat safer than 230V. The US had to much invested in 110V by the time 230V was available to make a switch over economical.
The first major electrical power plant in the US (and probably the world) was 110VDC. That was partially a limitation of the equipment and partially a safety limit – 110V was considered low enough to not be immediately deadly if you touched it.
Secondly, education is crucial. Educational opportunities are not only helping companies to see the benefits of a digital solution for their specific use case, but also to support employees on different levels in using them. That is why we have established the Kistler Plastics Academy. Here, we support our customers’ digital journey on three levels. On the basic level, we provide training for machine operators, application engineers and mould makers on how to install sensors, how to use the ComoNeo process monitoring system and the data base. On the advanced level, process engineers and production experts learn what is really happening inside the injection mould. On the expert level, data managers and quality engineers get insights into the potential of data management and data analysis.
During my time in the medical devices industry, I have seen several major changes. In 2010, when I started out, companies were still skeptical towards cavity pressure measurement. Those that went on to integrate the technology were mainly interested in using it for straightforward process monitoring, ignoring more sophisticated opportunities. When I joined Kistler, one major project was the creation of ComoNeo, a system which was a serious level-up to the previous solution ComoInjection. As a software designed specifically for injection moulders, ComoNeo provided a much better user experience and was quickly very successful on the market. It also attracted a lot of interest from the medical field. To meet the needs of medtech companies, we created a company-internal group to unite experts from the areas of plastics applications and advanced manufacturing. While the former bring a lot of material expertise, the latter have extensive knowledge in the monitoring of joining and assembly processes. Joining forces, the team saw the immense potential of gathering and analysing meaningful data in the medical field. This has lead to Kistler becoming the sole provider of the process navigator Stasa QC by Stasa, which enables the process monitoring system to provide efficient, automated documentation of the test plans and also to perform the corresponding process analyses. Most recently, we have also presented AkvisIO IME (Injection Moulding Edition), our inhouse process data solution to the broader public at Fakuma.
Over the last ten years, measuring quality assurance throughout production has become industry standard because it provides reliable information about the quality of both process and product. Equally, digitalisation and automation of process monitoring have come a long way. Daniel Kormann, head of business development for plastics at Kistler, discusses the state of process monitoring and process control in the light of current developments such as AI and new regulations.
Although [Michael] had discussed using the machine for PLA with the seller to confirm that this would work, a user error meant that the now defective unit had been sitting idly for many years, until recently.
In this first installment, [Michael] cleaned up the machine and restored it to a working state. In the next part injection molding will be attempted again, which should give some idea of the feasibility of turning scraps of PLA and failed 3D prints into smooth injection molded parts, assuming you have the CNC machine or patience to carve out the requisite molds, of course.
While algorithm-based systems are already in use, there are two areas where we can improve and promote their reception. Firstly, when it comes to convincing companies of a solution they haven’t tried yet it is important to demonstrate that automated systems for the shopfloor are easy to set up and use. We will be working more closely with our customers to learn from their experiences, to improve our products as a whole and, as a result, to enhance their user experience.
Aus was always 240V – indeed I often measure my power at 250V or so…. a while ago they theoretically changed it to ” 230 V (+10% to -6%), therefore providing an allowable voltage supply range between 253 V to 216 V” but I’m yet to ever see anything under 240..
When AC equipment became available, the US stuck with 110VAC. The 110VDC light bulbs and other appliances could run on 110VAC easily enough.
As in many things, the US was ahead of the times. The solutions were suboptimal, but were kept because switching to a better system would have cost too much. The rest of the world followed, but learned from the mistakes made in the US.
One way to make use of AI certainly lies in the analysis of data and automated predictions based on them. The key here would be a data platform such as Kistler’s akvisIO. It integrates production and measurement equipment such as sensors or field devices and collects their raw data. It then processes it and overall makes data from different sources comparable to each other. Machine learning algorithms can then use the data to draw larger conclusions on the performance of the overall production set-up, to predict maintenance needs and even anomalies. Our vision is that eventually, the algorithm will be able to foresee events that have never occurred before. To make that vision a reality and to also get users on board with the new way of utilising data, our large team of data scientists focus on usability and user experience in our continuous development. AkvisIO processes and analyses process data to be directly used as a basis for decision making. This eliminates the additional step of interpretation and makes the data more accessible. Of course, the user can also add their own interpretation of the data to the results based on their own experience. As the need for AI continues to develop within the industry, we’ve set up akvisIO in a modular way. Working with customers and identifying their specific needs will allow us to add features, or specific modules tailored to a particular application or user group. One area of application could be advanced process control including trends and prediction, which could make processes even more efficient and robust, especially in terms of energy and raw material consumption.
By using our website and services, you expressly agree to the placement of our performance, functionality and advertising cookies. Learn more
Since the machine had been gathering dust and rust in the garage, fixing the machine up took a complete teardown to remove corrosion and resolve other issues. After this the original fault was identified, which turned out to be a shorted wire near the heater which had been turned up to a too high temperature, leading to the release of magic smoke and banishment of the machine to the Pit of Despair, AKA the shadowy depths of one’s garage.
We are still very firmly stuck at the barely useable (for workshop and large appliance use) 100V here in Japan. You can get 200V split phase if you need more power, but that’s still significantly less than what my toaster ran on back in Australia…
Industrial injection molding press machine for the manufacture of conditioner parts using polymers in the management of worker
GETTING A QUOTE WITH LK-MOULD IS FREE AND SIMPLE.
FIND MORE OF OUR SERVICES:
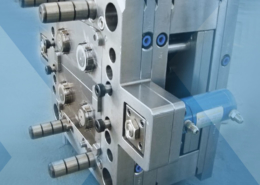
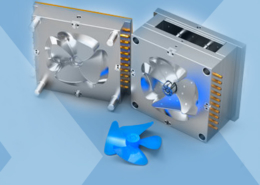
Plastic Molding

Rapid Prototyping
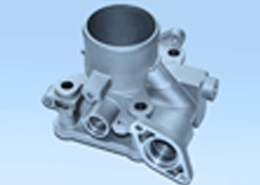
Pressure Die Casting
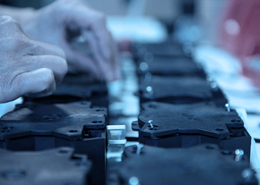
Parts Assembly
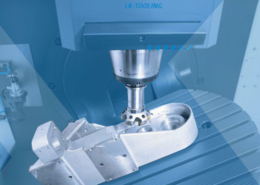