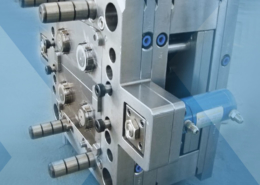
Unveiling the Craftsmanship of Plastic Bucket Moulds
Author:gly Date: 2024-06-08
Introduction: Delving into Precision Engineering
Plastic bucket moulds stand as a testament to the ingenuity of modern manufacturing, showcasing the intricate craftsmanship required to produce everyday essentials with precision and efficiency. From household cleaning to industrial applications, plastic buckets serve myriad purposes, and behind each reliable bucket lies a meticulously designed mould. In this article, we embark on a journey to unravel the intricacies of plastic bucket moulds, exploring their design principles, manufacturing processes, applications, and future prospects.
1. Design Principles
The design of a plastic bucket mould is a culmination of engineering expertise, material science, and ergonomic considerations. Each aspect of the mould, from the cavity geometry to the cooling system, is meticulously crafted to ensure the production of high-quality buckets with consistent dimensions and performance.
The cavity design of the mould dictates the shape, size, and features of the plastic bucket, including handle placement, wall thickness, and bottom structure. Advanced CAD software and simulation tools enable engineers to optimize the mould design for manufacturability, part quality, and cycle time efficiency.
Furthermore, considerations such as material selection, gate design, and ejection mechanism play crucial roles in ensuring smooth moulding operations and minimizing defects. By adhering to sound design principles, manufacturers can achieve optimal performance and longevity from their plastic bucket moulds.
2. Manufacturing Processes
The manufacturing of plastic bucket moulds involves a series of precision machining and fabrication processes, each contributing to the final quality and functionality of the mould. CNC machining is commonly used to mill the mould cavity and core inserts to precise tolerances, ensuring dimensional accuracy and surface finish.
Additionally, EDM (Electrical Discharge Machining) is employed to create intricate features and details within the mould cavity that may be difficult or impossible to achieve with traditional machining methods. Surface treatments such as polishing and coating enhance the durability and release properties of the mould, prolonging its service life and reducing maintenance requirements.
Moreover, the assembly of the mould components, including inserts, slides, and cooling channels, requires meticulous attention to detail to ensure proper alignment and functionality during moulding operations. By leveraging advanced manufacturing techniques and quality control measures, manufacturers can achieve superior performance and reliability from their plastic bucket moulds.
3. Applications Across Industries
Plastic bucket moulds find applications across a wide range of industries, catering to diverse needs and requirements. In the consumer goods sector, plastic buckets are used for packaging household cleaning products, paints, adhesives, and gardening supplies, where durability, leak-proofing, and ease of handling are essential.
Similarly, in the food and beverage industry, plastic buckets are utilized for storing and transporting bulk ingredients, sauces, and condiments, ensuring food safety and hygiene standards are met. Additionally, in industrial settings, plastic buckets serve as versatile containers for chemicals, lubricants, and construction materials, providing a reliable solution for storage and transport.
4. Future Prospects and Innovations
Looking ahead, the future of plastic bucket moulds holds promise for continued innovation and advancement. Emerging trends such as additive manufacturing, multi-material moulding, and Industry 4.0 integration are reshaping the landscape of mould manufacturing.
Additive manufacturing techniques such as 3D printing offer new possibilities for rapid prototyping, customized tooling, and on-demand production of mould components. Multi-material moulding enables the integration of different plastics or additives within a single bucket, offering enhanced functionality and performance.
Furthermore, the integration of data analytics, IoT connectivity, and AI-driven optimization algorithms holds the potential to enhance mould performance, productivity, and predictive maintenance. By embracing these innovations and collaborating across the value chain, stakeholders can unlock new opportunities for efficiency, sustainability, and competitiveness in the plastic bucket manufacturing industry.
Conclusion: Precision, Performance, and Progress
In conclusion, plastic bucket moulds embody the intersection of precision engineering, advanced manufacturing, and practical utility, serving as indispensable tools in modern society. Through meticulous design, precision manufacturing, and continuous innovation, plastic bucket moulds enable the production of high-quality buckets that meet the diverse needs of consumers and industries.
As we navigate the challenges and opportunities of the 21st century, let us continue to push the boundaries of innovation and sustainability in plastic mould manufacturing. By embracing new technologies, materials, and design methodologies, we can unlock new possibilities for efficiency, performance, and environmental responsibility, ensuring a brighter future for generations to come.
GETTING A QUOTE WITH LK-MOULD IS FREE AND SIMPLE.
FIND MORE OF OUR SERVICES:
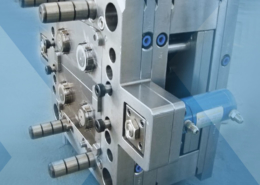
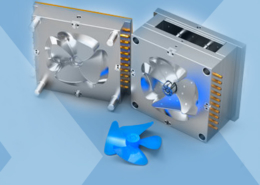
Plastic Molding

Rapid Prototyping
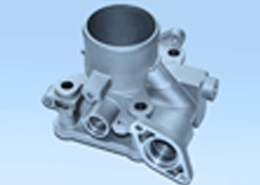
Pressure Die Casting
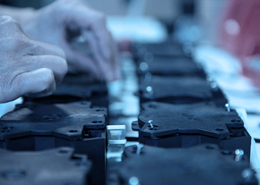
Parts Assembly
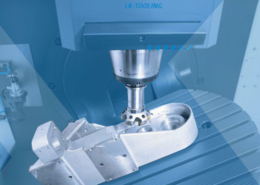