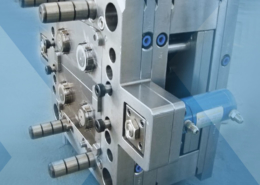
Engel Delivers Its Largest Ever Injection Molding Machines - large injection mol
Author:gly Date: 2024-09-30
Servo electric calibration stations with self-adjusting height compensation allows for consistent shear ring cutting. In addition, Siemens IPC477E Industrial PC with 15.0-in TFT touchscreen provides for an intuitive controls system that is focused on easy navigation. Meanwhile, remote access of the machine for technical support is achieved via an Ewon system, which is easily integrated within a customer’s IT system.
The new all-electric shuttle also offers in-machine deflashing with “centre of machine” scrap removal which keeps the conveyor behind the clamping/moulding stations and allows for a more open area when performing mould changes or machinery maintenance. The in-machine servo electric part takeout system includes a “centre of machine” takeaway conveyor that provides for a single-point container exit.
In general, structural foam molding requires less energy and raw material, and uses lower clamping forces, than conventional injection molding. The dissolved blowing agent improves flowability of the molten plastic. In addition, the foam molding pressure, which is independent of the location, enables molding of thicker ribs. These effects can be used to reduce wall thickness, which has a positive effect on the required cooling time and, in turn, on the cycle time.
“This new all-electric shuttle expands our all-electric offering and gives customers another option that provides a smaller footprint, flexibility, and greater efficiency to meet today’s demanding packaging requirements,” said Fred Piercy, president and general manager of R&B.
Together with Tier 1 supplier Faurecia, Engel is demonstrating the potential of structural foam molding technology at its K booth. Sample parts with a sophisticated surface structure are being produced on an Engel duo 1000 injection molding machine. The new MicroJect Advanced process developed by Faurecia Interiors (Hagenbach, Germany) and Eschmann Textures International (Gummersbach, Germany) is being used in this application. The process makes it possible to produce lightweight, visible components with a high-quality Class A surface using only structural foam molding.
Among the machine’s key features are a heavy-walled steel tube and steel plate frame construction with “walk-in” moulding area and “top of machine” access platforms for long life and easy maintenance. Access platforms can also be used for mounting a mould changing crane if required.
Among other things, a new tool technology is responsible for this leap in development. Ceramic coatings in the cavities prevent the otherwise typical foam streaks, weld lines, tiger stripes, or gloss differences from appearing on the surface of the foam molded part. Additionally, different surface structures can be created directly in the injection mold via the cavity coating.
Structural foam molding is more popular than ever. It saves raw material, energy, and weight, supporting the objective of producing and using plastic parts in a more sustainable way. At K 2022, Engel (hall 15, booth C58) is presenting a new technology for plastics processors who produce parts in parallel on several production cells using the structural foam molding process.
R&B Plastics Machinery, a manufacturer of all-electric extrusion blow moulding (EBM) shuttle machines, hydraulic accumulator machines, and single-screw extrusion systems, will launch its newest all-electric EBM shuttle model at the NPE 2024 exhibition May 6-10 at the Orange County Convention Center in Orlando, Florida. At its booth, R&B will demonstrate the new Model RBS-E550D All-Electric shuttle unit while also displaying one of their MAX Series Single-Screw Extruders.
Further, the combination of new system technology by Engel and MicroJect Advanced leverages unprecedented efficiency and sustainability potential in structural foam molding, according to Engel. Structural foam molded parts no longer need to be painted, and there is no need for additional energy-intensive process technology, such as intermittent mold heating, for parts in customer-facing applications.
The new model is the first R&B shuttle equipped with Yaskawa X absolute servo motors and drives. The servo motors and controllers offer some of the fastest and smoothest machine motions available in the industry. W. Müller’s Model WM-096 manual screen changer is easily accessed for screen pack changes or system maintenance. The system can also be driven via a cordless screwdriver without effort.
R&B also offers both hydraulic and hybrid Accumulator Blow Moulding Machines with different single- and dual-head configurations. R&B accumulator machines are deployed in automotive and industrial chemical markets, and in a range of specialty applications throughout the large-part blow moulding market. It also performs extensive rebuilds and modernisation of all competitive equipment.
Engel is improving the cost effectiveness of structural foam molding with its new e-foam XL gas supply units that support multiple production cells.
Whereas each injection molding machine previously required its own gas supply, Engel now offers the e-foam XL multi, a central unit for supplying several injection molding machines with highly compressed nitrogen for structural foam molding. Only the plasticizing and control technology remain decentralized on the individual machines. This new solution sees Engel significantly reduce the capital outlay for structural foam molding and makes a major contribution to reducing unit costs. The new modular Engel e-foam XL multi systems, based on Trexel's MuCell technology, are offered exclusively by Engel.
In addition, new materials developed by Faurecia Interiors for structural foam molding contribute to the surface quality. An IniCycle talc-filled polypropylene grade with 30% recycled material content will be processed during the K show. IniCycle is suitable for all physical and chemical foam molding processes.
The company serves a diverse customer base with many business segments and markets including food and beverage, personal care, household, pharmaceutical, motor oil and lubricants, automotive, lawn and agricultural chemicals, and industrial specialties. Modernisation and upgrade services bring older machinery up-to-date, thus providing measurable productivity improvements, faster cycle time, energy savings, improved quality, and greater efficiency and consistency. Cost savings benefits usually include decreased labour, utility, and materials usage variance improvement.
R&B’s Model RBS-E550D All-Electric EBM Shuttle machine will be configured with a W. Müller 2 x 250mm CD tri-layer die-head with individual servo electric wall thickness controls. Housed between the main extruder and die-head is W. Müller’s new melt filtration technology, the WM-096 Manual Screen Changer System.
R&B will also statically display one of their standard 3-1/2” x 32:1 L/D MAX Extruders with a vented-to-atmosphere barrel. This MAX™ Extruder includes standard Allen-Bradley Compact Logix-based controls with a 15.0-in TFT touchscreen. The control system allows for simplified integration of various downstream equipment so long as the downstream equipment is configured with the proper electrical components. Optional features include a Nordson Hydraulic Screen Changer with extruder base mounted Hydraulic Power Unit. R&B MAX™ Extruders are available in sizes as small as 1-1/2-in to 10-in diameter.
In a tri-layer application displayed at NPE, the new all-electric shuttle machine will be outfitted with a main extruder size of 100mm x 26:1 L/D ratio and designed for processing regrind PE-type resins. The satellite extruders, for inner and outer layers, are sized at 70mm x 24:1 L/D ratio, respectively.
GETTING A QUOTE WITH LK-MOULD IS FREE AND SIMPLE.
FIND MORE OF OUR SERVICES:
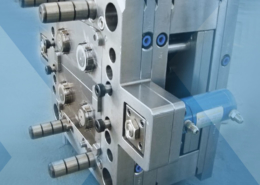
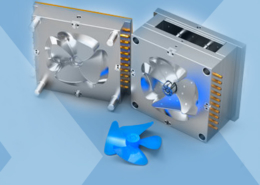
Plastic Molding

Rapid Prototyping
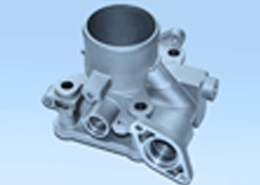
Pressure Die Casting
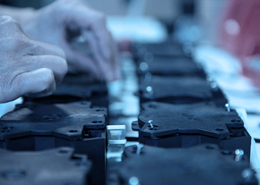
Parts Assembly
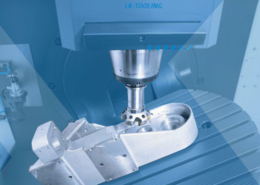