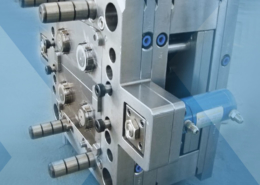
Engel Delivers Its Largest Ever Injection Molding Machines - biggest injection m
Author:gly Date: 2024-09-30
The following is an edited excerpt from The Business of Injection Molding, by Clare Goldsberry. The book is the first title in the IMM Book Club Injection Molding Management Series, published by IMM. While much of the focus in the book is on a custom injection molding operation, many of the points about plant layout, machinery and equipment required, and staffing apply to captive molding operations as well.
While many molding companies have rushed to implement the latest and greatest with regard to quality standards, others balk at the idea of so much money spent without the assurance that a particular level of quality is actually needed. In some ways, too, these so-called levels have made the playing field more uneven and are knocking smaller molding shops out of competition.
If material handling will be done manually, that is, by using forklifts to convey gaylords, or 1000-lb containers of resin, to presses, then adequate space must be allowed to accommodate the forklifts. If pneumatic conveying systems are to be used, then you might consider an enclosed material-storage aisle between the rows of presses, which keeps bags and gaylords of material out of sight yet handy to the presses.
Since the very first PM Titanium conference in Brisbane, Australia, in 2011, the PMTi series has been the essential meeting point where technical a...»
As far as molders and quality are concerned, size doesn't necessarily mean that a company is better. A large company or plant can be run poorly and have low productivity with below-average profits or ROI. A small plant can be well run and have high productivity and good profits. It's generally known, however, that all molders, whether they have $100 million or $1 million in production or sales, fight the same battles—only the scale is different. The bigger the company, the bigger the problems.
Quality Issues—What They're All About Finally, consider how your new plant will develop and assess product quality. During the past decade, quality issues as a part of good business operations have become a top concern for custom and captive molders. The OEM-custom molder relationship has always been one of interdependence, but until recently, custom molders had free rein when it came to matters of production.
Today, Ecrimesa is comprised of three companies: its investment casting segment, Ecrimesa; the MIM company Mimecrisa; and machining company Mecansa. The companies are located across seven locations in Santander, on the northern Spanish coast. The three companies work closely together, benefitting from one another’s capabilities and expertise; for example, the tool shop at Ecrimesa provides toolmaking and tool maintenance services to Mimecrisa, along with access to its metallurgical and measuring labs, while Mecansa carries out finishing operations for Ecrimesa and Mimecrisa as required, and both Mimecrisa and Mecansa make use of Ecrimesa’s heat treatment facilities.
The first versions of the MIM part that were injected and sintered showed some flow lines as a result of high binder levels. Some changes were needed following this first trial run to improve feedstock flow and avoid phase demixing, mainly at the injection areas with thin walls. Penetrant tests, used internally at Ecrimesa as a process control step during development, identified porosity areas in the first iteration of the part due to demixing and sintering deformation, pointing to the need to improve the strength of the green part using some additional ribs and extra wall thickness (Fig. 4).
While the original parts weighed around 100 g, and the MIM part close to 130 g, the cosmetic and mechanical properties achieved by transition to MIM allowed the customer to bring the product to higher quality markets. By cooperating closely with the customer, Mimecrisa was able to bring together the part’s necessary functionality with the required expertise in designing for MIM, and achieve the common goals of both parties. Where customer requirements can be fully agreed upon during the design phase, time to market and iteration cost can be reduced compared to collaboration carried out during the sampling process. The final assembled hinge set is shown in Fig. 7.
In recent years central material handling systems have grown in popularity. Such systems locate resin, dryers, hoppers, and blenders in one place, often in a basement below the presses, or on a mezzanine above the presses. Vacuum pumps and small pneumatic loaders at each machine move resin from the centrally located hoppers to the press via a network of tubing. Such a setup keeps bulky gaylords and dryers out of the way, allows machines to be spaced closer together on the floor, and makes material handling simpler as all resin can be managed from one location. A central system is more expensive to buy and install, but is usually more efficient in the long run.
Some molders elect to use storage silos for resin; these molders usually specialize in one or two closely related markets and mold large parts from one or two materials or millions of parts from the same material. Resin from a silo can be pneumatically pumped to a machine, so little or no shelf space is required for its storage. Other molders, because of the nature of their businesses, opt to store raw materials on the shelf, a procedure that has been known to lead to overcrowding.
The Molding Machine: Cost Justification More than just a purchase, an injection molding machine is an investment. As with any investment, you want to know what your return will be. What value will the machine contribute to your overall operation? Where will your break-even point be? Will the machine pay for itself in a year? Two years?
Extensive MIM, CIM industry and sinter-based AM industry news, plus the following exclusive deep-dive articles and reports:
In this case study, a part produced via die casting, typically produced with low-melting point alloys, was highlighted as a potential MIM candidate thanks to the customer’s need for higher mechanical and aesthetic properties. In order to transition the part successfully, a high degree of design work and process expertise was required in order to take full advantage of MIM’s capabilities and satisfy all of the customer’s requirements.
Finally, there are some additional criteria for deciding between investment casting and MIM. In general, it can be said that the development and production process of new parts is shorter with MIM, since there is no obligation to make multiple moulds and prototypes before starting production, which may be necessary when working with investment casting. In addition, the part design that a user begins with in the MIM process is generally closer to the final part, and machining processes are saved. Typically, parts manufactured by MIM have a very high surface quality without the need for finishing processes.
Other investment factors include the performance history for the machine under consideration, shot-to-shot repeatability, and whether the machine is geared toward high-volume, high-speed applications or low-volume, slow-cycle requirements. Ultimately, at the end of the day, what is its yield? Determining your ROI is application dependent. Some things can be quantified up front, but others can't until the mold is in the press and parts are running.
Finally, it's usually not enough to just mold parts anymore, package them in a box, and send them to the customer, traditionally called "shoot and ship." Many manufacturers go to molders now looking for design and engineering services, tooling assistance, and postmold decoration and assembly expertise. Captive molders, as well, are more likely to have several secondary functions integrated with the molding of the basic parts.
In 2020, Ecrimesa added Additive Manufacturing to its available technologies, enabling customers to manufacture wax prototypes for investment casting with short lead times, or additively manufacture parts using Fused Deposition Modelling (FDM), a form of Material Extrusion (MEX). The resulting parts can be sintered in Ecrimesa furnaces.
Don't miss any new issue of PIM International, and stay up to date with the latest industry news. Sign up to our fortnightly newsletter.
In general, most parts with a final weight of less than 15 g produced by Ecrimesa are – depending on the material – produced by MIM, since this technology allows thinner structures and is more material and energy efficient. However, there are still designers who, even for smaller parts, have a preference for investment casting.
The 2023 International Conference on Injection Moulding of Metals, Ceramics and Carbides (MIM2023), organised by the Metal Powder Industries Federa...»
Injection molding auxiliary equipmentThe central material drying/handling system, including five insulated drying hoppers, dehumidifying dryer, pumps, filters, and conveying system would cost about $115,000. Beyond that, at right are typical prices for other auxiliary equipment.
You should also consider whether or not cleanroom molding will be needed; if material handling will be done manually or via automatic pneumatic conveying systems (or a combination); where storage areas for materials will be; and whether the layout for manufacturing will promote production efficiency and minimize part handling in molding, assembly, and any other secondary operations.
By 1997, Ecrimesa’s MIM operation had gown to such an extent that the company’s management took the decision to establish the independent company Mimecrisa, which would be responsible for the group’s MIM production facilities and workforce. In 2005, Ecrimesa Group bought out one of its machining suppliers in order to increase the added value of its production in investment casting and MIM. In summer 2015, this machining plant was moved to its own building.
Ecrimesa Group, with facilities for both investment casting and MIM, used this expertise to fully understand the limitations and advantages of each process during the design transition, and bring this expertise to the customer. By taking advantage of the synergies between its different manufacturing capabilities, the group was able to accompany and support the customer across the full redesign and manufacturing process, from conception to finishing.
Almost exclusively commercially available feedstocks, designed for catalytic debinding, are used, avoiding the need to invest in and maintain equipment for feedstock preparation, or the specific knowledge and expertise that goes along with this. All incoming feedstock deliveries are checked for compliance with specifications in the company’s materials laboratory, where chemical composition is analysed and standard samples are used to determine shrinkage. Differential thermal analysis equipment is also used to analyse binder decomposition rates and the amount of binder in the feedstock.
The use of Additive Manufacturing technologies for prototyping, such as metal MEX or metal Binder Jetting, is expected to help further speed up the development of such complex parts. While filament-based MEX techniques are not accurate enough to accurately replicate the finest design features, they can be of help in carrying out sintering tests prior to production. Binder Jetting can more closely match the MIM design as a ‘brown part’ with just a ‘backbone’ binder (though potential demixing or ‘injection memory’ issues will not be highlighted in such prototypes). In future, Ecrimesa plans to utilise these techniques for prototyping new MIM parts. Simulation techniques can also offer some capability to predict the injection path inside the mould, but some other important aspects are not covered by these techniques.
Find a Niche and a Focus Most custom molders in business today have found a niche. Through experience, the molder became good at molding a particular type of part or at molding a particular kind of material, or became astute in working in a specific segment of the marketplace. In other words, he acquired an expertise and stuck with it. A captive molder inherits a market or a range of products, but must develop the same expertise and focus that a custom molder does.
Another factor to consider when investing in a molding press is the type of mold(s) it will be running. Will they be large, multicavity, hot runner molds that require larger-tonnage equipment, or single-cavity, conventional molds that require smaller-tonnage machines? Controls and the speed of system response must be also considered. Do you need a press that provides versatility, or are you investing in a press that will just run one job continuously?
Warehousing: A Hidden Requirement You will need space for storage of molds not in use, bags and gaylords of material, the finished-goods inventory customers most likely will request be held, and other equipment. Typically, molders use an average of 10 percent of their total floor space for warehousing. This will vary depending on the size of your molded parts, how many different materials must be kept on hand, and the size of the molds to be stored.
Two decades ago, a $30 million custom molding company was considered a top business. Today, as a result of mergers, acquisitions, and growth that has outpaced the national average, a company that size is considered small. So although an individual can set up a small injection molding operation for less than $1 million, unless the company has a special capability to offer or establishes a sound financial relationship with one or two customers, chances for success are slight.
Tritone’s MoldJet is unique as an Additive Manufacturing process – not Binder Jetting, Material Extrusion, nor Material Jetting, the MoldJet pr...»
Plant Layout Assuming you have the capital to support a startup, or have a budget from corporate headquarters, you start physical construction with the plant. Whether you build or buy, the layout of your plant is a crucial consideration if you're going to have an efficient, profitable operation. Allow approximately 1000 sq ft of space for each molding press; this accounts for offices, molding/production, secondary operations, quality control, storage of materials, and a mold maintenance and repair area.
The free-to-access PIM International magazine archive offers unparalleled insight into the world of MIM, CIM and sinter-based AM from a commercial and technological perspective through:
Generally, space for secondary operations is designed in one of two ways—either as a separate area or room designated for such activities, or beside the press. The choice depends on the types of secondary operations to be performed and the space available. Some molders prefer to do secondary operations alongside the press after each cycle in order to minimize handling and maximize operator time. This can also increase efficiency in that parts don't have to be boxed, moved, unpacked for the secondary operation, and then repacked. Less handling is also easier on the parts and results in lower scrap rates—another important consideration. This requires that all operations be considered together and set up in cells, usually dedicated to a single product or assembly, sometimes with multiple parts.
IMM made some big assumptions and got ballpark figures from a few manufacturers who were willing to share their cost data. The tables below list some basic prices for injection molding machines and auxiliary equipment. For the purposes of this list, we assumed this 15-press facility would orient the machines in two side-by-side rows on 15-ft centers. We also decided that material handling would be central, designed to accommodate five different resins, each used in equal amounts, each with an average drying time of 3 hours. Hypothetical average cycle time would be 60 seconds at maximum shot capacity for all machines, which would consume 562 lb/hr of resin. Material would be pulled from gaylords, dried centrally, and delivered to each machine via machine-mounted vacuum receivers.
How a facility is set up and attendant decisions depend on the type of markets you are serving, the type of parts you need to mold, and what your customers (internal or external) dictate you have. Right at the start, also consider future expansion, either of the plant itself or of production floor space. While a 10,000-sq-ft facility might seem enormous when it's empty, it can become crowded when 10 presses and auxiliary equipment are installed. A rule of thumb is to lease or purchase a building twice the size you figure you'll need to start.
In addition, entering custom injection molding with two or three presses and minimal capabilities means entering a highly competitive market already crowded at the low end with several thousand molders. Because many of these molders, with sales less than $1 million annually, offer little in the way of secondary services, they compete on the basis of price. This results in thin margins and a low survival rate.
For example, disposable medical components such as injection syringes are manufactured and used in the millions daily. However, the return from each one of these devices is in the tenths of a cent. Quality and manufacturing requirements are extremely stringent, and the parts generally are made from clear or clear-tinted material, which compounds the difficulty of molding. In order to make a profit, molders who choose this type of high-volume medical work must find ways to keep manufacturing costs at a minimum and efficiency high.
If you were starting a new facility, it would be unlikely you'd pay this list price for any of this equipment. If you are molding a highly sophisticated product mix, these prices might be low. They also don't represent the prices of the most basic imported molding machine, either. But these prices at least offer a glimpse at what a good starting point might be.
Machinery manufacturers say that molders use a variety of criteria when looking at a cost-justification evaluation. Some base their decision purely on the lowest price, without taking into consideration the "cost" of the machine. Price is what you pay for the machine now. Cost is what you will pay for the machine long-term, including such things as energy use and maintenance.
Today it's increasingly apparent that if you're starting a plant or a business, you are either given or must find a niche—a specific market or product line—and focus on molding for that market or customer. Will you mold large parts? Small parts? Do you want to be a molder of low-volume, high-dollar parts? Or high-volume, low-dollar parts? Most people would answer that they want to be a molder of high-volume, high-dollar parts. If only it worked that way.
The larger the press, the more it costs, so the size of the majority of parts that will be molded is an important consideration. In a custom operation try to give yourself some flexibility on either end of the spectrum to also mold somewhat smaller or larger parts. This is an area where your business plan and marketing strategy, which determine the direction of your business, will also help you decide on the size and amount of equipment you'll need.
Reach a truly international audience that includes component manufacturers, end-users, industry suppliers, analysts, researchers and more.
Traditionally, 90% of parts weighing more than 100 g at Ecrimesa Group are manufactured by investment casting, since, at that size, the cost of the fine powders used in the MIM process is high, as well as the energy/time required to sinter them. However, due to the experience the group has accumulated in MIM, and the performance of the materials used, more and more parts weighing more than 100 g are being produced by MIM. The supply of the tooling required for MIM has also improved, allowing the technology to be used in wider range of cases. There are, of course, limits: using investment casting, parts weighing up to 25 kg can be produced, whereas, with MIM, the maximum realistic weight of a part is around 250 g.
Founded in 1964 in Santander, Spain, the family-owned Ecrimesa Group began life as an industrial casting foundry. The name Ecrimesa is a compound of the Spanish Electro Crisol Metal S.A., translating as ‘Electric Metal Melting Crucible.’ The company was originally established for the production of steel and aluminium investment castings, but by 1994, Metal Injection Moulding was being developed at the location using the world’s first MIM-Master continuous furnaces for catalytic debinding and sintering, in collaboration with feedstock supplier BASF SE and the furnace’s manufacturer, Cremer Thermoprozessanlagen GmbH. MIM now comprises a major portion of the group’s offering.
Compared to investment casting, which represents one of the oldest applied metal forming processes, Metal Injection Moulding is a relatively new technology, first commercialised in the 1980s and seeing wider adoption in the 1990s. To this day, investment casting is still one of the most widely used precision forming technologies, with MIM remaining far less known and, where it is applied, primarily being used for the manufacture of small parts.
As with most any major capital purchase, the price you pay for a particular unit depends on a lot of variables. In injection molding the variables are too numerous to list here, but generally, whatever you buy will vary by application. Much depends on what kind of material you'll mold, how much you'll use, and how large the parts are. But let's say, just for grins, that you do want to start up your own molding shop, based on the list above. And let's say you make some broad generalizations about how material will be handled, how much material you'll use, how long your cycles will be, and other considerations. About how much would the primary equipment cost for such a startup facility?
Large OEMs—specifically, the automotive and computer industries—adopted the philosophy of manufacturing with quality as they began seeking greater market share for their products. They recognized, however, that the quality of their products could be no better than the quality of the products' component parts. For this reason, much of the responsibility for improving quality has been laid directly at the feet of custom injection molders who supply the vast number of components.
Ecrimesa is one of the few companies to be able to offer its customers a choice of between investment casting, machining and MIM. This brings the opportunity to truly find the best process for an application, or to offer a wider choice of solutions as a part’s specifications evolve.
Discover suppliers of these and more in our advertisers’ index and buyer’s guide, available in the back of PIM International.
While most molders accommodate the requirements of their customers, some question the necessity of all the quality bells and whistles like SPC, SQC, ISO 9000, and Six Sigma (a term coined by Motorola that refers to a quality level of three defective parts per million), given the variables of the molding process.
Selecting the Best Equipment Presses with up to 100 tons of clamping force, which mold small parts, constitute the second largest group of presses used by molders in the United States. The majority of molders operate with presses in the 100-ton to 350-ton range. Presses in the 350-ton to 750-ton range represent the third largest group. Most injection molders enter the business with small to midsized molding presses.
Both technologies are applied to manufacture small parts that are generally more complex in design and, therefore, processes such as forging cannot be used. One of the main differences between investment casting and MIM is the range of materials that can be processed. In general, investment casting allows for a wider variety of materials, as the MIM process can only be performed with alloys of a higher melting temperature. Materials such as aluminium, for example, do not work efficiently with MIM.
For higher-weight glass doors requiring a stronger hinge, a stainless steel version was developed for production by MIM (Figs. 2 and 3). A number of changes were made to adapt the design to MIM, focusing on the internal faces of the parts, which would not be visible to the user. These hinges are at the upper range of MIM’s size capabilities, with a typical weight of 50–80 g, and have very thin walls with a large surface area.
Some preliminary ceramic setters were also used to support the green part during sintering (Fig. 5). Coining – the final operation to ensure flatness – was carried out on internally developed coining devices (Fig. 6). This step is necessary, even if sintering setters are optimised, to achieve narrow tolerances and avoid machining. Ecrimesa’s experience, gained from investment casting, helped the team to develop this coining device in house.
If you require some level of cleanroom molding—often required by medical and electronics parts—then you must decide how you will achieve it. The various types of cleanrooms include Class 100, Class 1000, Class 10,000 and Class 100,000. Each level has its own criteria and must meet certain requirements as established by FDA guidelines. Class 100 is the most stringent and Class 100,000 is simply a "clean environment," and therefore the easiest to achieve.
The production floorspace at Mimecrisa is about 6,000 m2, staffed by around fifty employees, and all injection moulding machines are equipped with pick-and-place systems, some robotic. Using these pick-and-place systems, green parts are transferred to trays that fit into sinter boxes specifically designed for MIM-Master furnaces, meaning that green parts do not have to be handled until they exit the sintering furnace. In some cases, parts are placed on specially shaped ceramic supports, or setters, for improved dimensional stability. These supports are manufactured in-house.
When the demand for world-class molding facilities is added to state-of-the-art manufacturing capabilities, the bar for entry into the custom injection molding business rises considerably. Instead of being able to enter the molding business on a shoestring, as many did 30 years ago, a large financial investment is now required. This generally requires the cooperation of a bank, an equipment leasing or lending institution, and financial backing from private investors to pull together the funds needed to succeed. Likewise, the barriers to entry for a captive operation to provide a good return on investment are high. It's not enough to buy molding machines and auxiliaries and leave them in place without improvements for the long haul. Captive operations also must not only make an initial investment, but also be prepared to stay technologically attuned.
As an employer, you will also quickly discover what many molders know already: In 2001, finding and keeping reliable production employees is very difficult. The competitive job market is a significant challenge for many molders. One way to combat this problem is to rely more on robotics and automation to perform the tasks that might otherwise be done manually. Robots can be used to pull parts from the mold, remove sprues, and do some assembly work. Most robot systems mount on top of the press and by themselves may not affect plant layout. But you may elect to use conveyors or other parts handling equipment press-side in conjunction with robots. Make sure to allow enough space to accommodate such equipment.
The typical sintering conditions in Mimecrisa’s furnaces are suited to low-alloy steels, low-carbon FN08, low-alloy steel with elevated carbon 4605, 42CrMo4, 100Cr6, 17-4 PH and 316L stainless steel. A large proportion of its products are made from heat treated steels that require a higher carbon content; the production of these carbonaceous sintered steels poses a special challenge for many MIM manufacturers, as these materials require very precise control of the sintering atmosphere. In many cases, components made from these materials are hardened and tempered following sintering – an area in which Mimecrisa has a large deal of experience. Three carburising furnaces are available for case hardening and quench-and-temper heat treatments, with fine-tuned programs for MIM materials and small parts.
You must also determine what services you will offer, and what equipment will be needed to supply such capabilities. For example, even if you decide not to have a moldmaking facility in-house, you will need a certain amount of equipment for mold maintenance and repair. Will you do any type of secondary operations? If so, what type of equipment will that require? See the box above for a list of equipment in a 15-machine shop. Equipment costs are shown below.
In this case study, Mimecrisa was tasked with transitioning a pair of door hinges from die casting to MIM. These corrosion-resistant hinges were originally manufactured from a zinc alloy. For safety reasons, the hinges must be able to open at up to 270° and, for cosmetic reasons, they need to be polished to a mirror finish.
Aside from the choice of materials you want to work with, the decision between investment casting and MIM depends on other primary factors: the size of the part, the complexity of the part and the tolerances required, as well as the number of parts you want to manufacture. The ideal part for the MIM process has a length of less than 100 mm and is produced in batches of more than 5,000 pieces.
In 2021, in response to increasing demand for its MIM parts, the group invested €2 million in the commissioning of a new continuous MIM production line as part of its 2021/22 investment plan, to include a new continuous debinding and sintering furnace from Cremer, and injection moulding machines from Arburg, bringing its total installed MIM capacity to fourteen machines across four continuous lines and two vacuum sintering lines. The new line was scheduled to go into operation in the first quarter of 2022 and would allow Mimecrisa to process over 250 tons of MIM feedstock per year.
Some molders prefer lower-volume parts molded for high-dollar products, which tend to offer better profit margins. For example, the box that houses the instrumentation monitoring an IV drip must meet tough cosmetic standards, and it's only produced in quantities of 100,000 a year. Others prefer to mold component parts such as gears that remain out of sight, which means that although fit and function still are critical, cosmetic requirements are less stringent.
Several factors must be considered to determine the return on investment (ROI) for a press. One of the biggest factors driving machinery investment is the amount of energy used. Estimates put energy costs at about 5 to 7 percent of a molder's total operating budget. Considering the amount of energy a typical 15-press plant can consume, energy has become an enormous cost issue. A-c variable-speed pumps and motors offered on most newer equipment, and as a retrofit for older equipment, can save energy by using it only when called upon during the machine's cycle.
HP’s Metal Jet has undergone significant refinement in the years since it was first unveiled in 2018. Now, by incorporating nearly the whole Bind...»
Mimecrisa’s MIM plant operates fourteen injection moulding machines of different sizes, most of them electrical; four continuous MIM-Master debinding and sintering furnaces; and two batch vacuum furnaces and CIM furnaces. The facility also includes a fully equipped metallurgical and dimensional laboratory, and the principles of LEAN manufacturing and Industry 4.0 are evident throughout the business’s workflows.
Both the customer and Mimecrisa knew when this product was highlighted for transitioning to MIM that some work would be needed to optimise the part for the MIM process. Initially, the lack of obvious injection points was a particular challenge. Another consideration in the design’s adaption was the addition of ribs in place of some of the thin walls featured in the original design in order to lightweight the component and reduce material costs.
The external face of the part was not changed during these modifications. The first iteration, with a 4 g weight increase from the original part, was good enough to be functional, but the customer ultimately preferred a bigger fatigue margin. The final iteration, taking into account the necessary changes, saw a weight increase of 2 g, necessary to avoid defects in the thin walls, increasing the fatigue life of the product whilst remaining compatible with the hinge’s function.
In many instances, a design developed for a conventional manufacturing process may be better suited for production by MIM. For example, a part previously produced by plastic injection moulding or die casting may no longer offer the required strength as the demands of the application increase. In cases such as these, Mimecrisa is able to offer increased value to the customer and increase MIM’s market share by employing its expertise to transition suitable parts made by competing technologies to MIM.
For better shape retention during sintering, the parts were produced using feedstock based on 316L master alloy powder. After considering the results of mechanical and dimensional trials on the first sintered samples with the customer, MIM moulds were modified in house to meet the part specifications. Throughout this process, cosmetic and assembly limitations were identified and noted for the next modification of the MIM parts.
GETTING A QUOTE WITH LK-MOULD IS FREE AND SIMPLE.
FIND MORE OF OUR SERVICES:
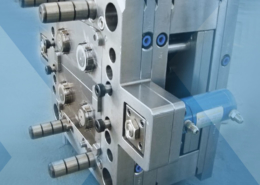
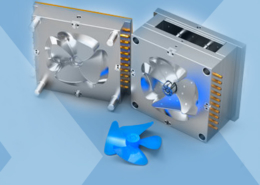
Plastic Molding

Rapid Prototyping
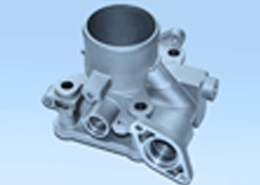
Pressure Die Casting
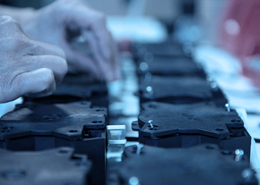
Parts Assembly
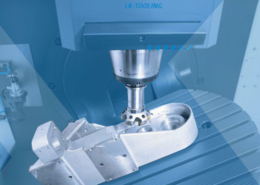