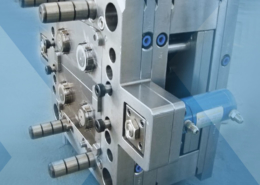
Plastic Mould Parts: Precision Engineering at Its Core
Author:gly Date: 2024-06-08
Plastic mould parts are the unsung heroes of modern manufacturing, facilitating the production of countless consumer and industrial products. From intricate electronic components to everyday household items, these components play a crucial role in shaping our world. In this article, we delve into the world of plastic mould parts, exploring their significance, applications, and the precision engineering behind their production.
1. Precision Engineering
Precision is the cornerstone of plastic mould part manufacturing. These components are meticulously designed and crafted to exact specifications, ensuring consistency and reliability in mass production. Advanced CAD/CAM technologies, coupled with high-precision machining processes, enable manufacturers to achieve tight tolerances and intricate geometries demanded by modern applications.
Precision Design:
The design phase is where the foundation of a plastic mould part is laid. Engineers leverage cutting-edge software to create detailed 3D models, considering factors such as material properties, part geometry, and production constraints. Iterative prototyping and simulation help refine designs before they proceed to manufacturing.
Machining Excellence:
Once the design is finalized, state-of-the-art machining centers come into play. CNC machining, EDM (Electrical Discharge Machining), and other advanced techniques are employed to transform raw materials into finished mould components with unparalleled accuracy. Every cut and contour is executed with precision, ensuring dimensional accuracy and surface finish.
Quality Assurance:
Quality control is paramount in plastic mould part production. Advanced metrology tools, including CMM (Coordinate Measuring Machines) and optical inspection systems, are used to verify dimensions and detect any deviations from the design specifications. Strict adherence to quality standards minimizes defects and ensures the reliability of the final product.
2. Diverse Applications
The versatility of plastic mould parts makes them indispensable across various industries, ranging from automotive and aerospace to electronics and healthcare. Their ability to be customized to suit specific requirements makes them ideal for a wide array of applications.
Automotive Industry:
Plastic mould parts find extensive use in the automotive sector, where they contribute to lightweighting efforts, improve fuel efficiency, and enhance vehicle aesthetics. From interior trim components to exterior body panels, these parts play a vital role in modern automotive design and performance.
Consumer Electronics:
In the fast-paced world of consumer electronics, plastic mould parts enable the production of sleek and compact devices. They form the backbone of smartphones, laptops, and wearables, housing intricate circuitry and providing structural support while maintaining a slim profile.
Medical Devices:
The medical industry relies on plastic mould parts for the fabrication of life-saving equipment and devices. From surgical instruments to diagnostic tools, these components must meet stringent regulatory requirements and biocompatibility standards to ensure patient safety and efficacy.
3. Material Innovation
Advancements in material science have expanded the horizons of plastic mould part manufacturing, opening up new possibilities in terms of performance, durability, and sustainability.
Engineering Plastics:
Traditional materials like ABS, polycarbonate, and polypropylene continue to dominate the plastic moulding landscape, offering a balance of mechanical properties and cost-effectiveness. However, emerging engineering plastics such as PEEK (Polyether Ether Ketone) and ULTEM™ (Polyetherimide) are gaining traction due to their superior heat resistance, chemical stability, and mechanical strength.
Bio-based Polymers:
With growing concerns over environmental sustainability, there is a rising interest in bio-based polymers derived from renewable sources such as corn, sugarcane, and cellulose. These eco-friendly alternatives offer comparable performance to conventional plastics while reducing carbon footprint and dependency on fossil fuels.
Composites and Nanomaterials:
The integration of reinforcements such as carbon fibers, glass fibers, and nanoparticles enhances the mechanical properties of plastic mould parts, making them stronger, stiffer, and more lightweight. Composite materials offer a compelling solution for applications where high strength-to-weight ratio and dimensional stability are paramount.
4. Future Outlook
As technology continues to evolve, the landscape of plastic mould part manufacturing is poised for further innovation and advancement.
Industry 4.0 Integration:
The integration of IoT (Internet of Things), AI (Artificial Intelligence), and additive manufacturing technologies is revolutionizing the way plastic mould parts are designed, produced, and monitored. Smart factories equipped with real-time data analytics and predictive maintenance capabilities enhance efficiency, flexibility, and quality control.
Additive Manufacturing Revolution:
Additive manufacturing, or 3D printing, is disrupting traditional mould-making processes by offering unparalleled design freedom, rapid prototyping, and on-demand production capabilities. While still in its infancy for mass production, advancements in materials and printing technologies hold promise for the future of plastic mould part manufacturing.
Circular Economy Initiatives:
The shift towards a circular economy model necessitates the development of recyclable and biodegradable materials for plastic mould parts. Closed-loop systems that promote material recovery, reprocessing, and reuse offer a sustainable solution to mitigate environmental impact and reduce waste generation.
In conclusion, plastic mould parts epitomize the marriage of precision engineering, versatility, and material innovation. From automotive to healthcare, these components play a pivotal role in shaping diverse industries and driving technological progress. As we look to the future, embracing emerging technologies and sustainable practices will pave the way for continued growth and innovation in plastic mould part manufacturing.
GETTING A QUOTE WITH LK-MOULD IS FREE AND SIMPLE.
FIND MORE OF OUR SERVICES:
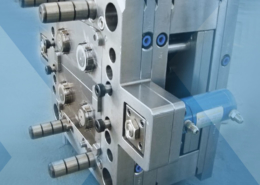
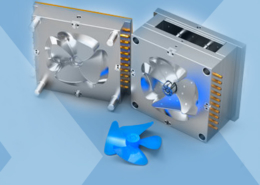
Plastic Molding

Rapid Prototyping
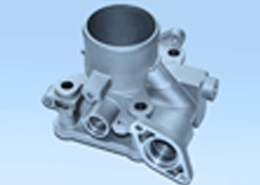
Pressure Die Casting
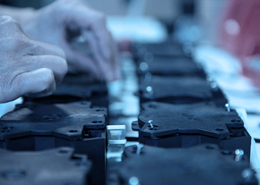
Parts Assembly
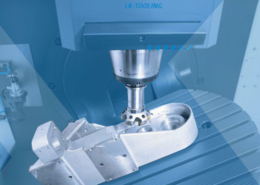