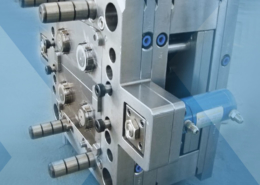
DIY Injection Mold Design For The Home Shop - small scale injection molding
Author:gly Date: 2024-09-30
This website uses cookies so that we can provide you with the best user experience possible. Cookie information is stored in your browser and performs functions such as recognising you when you return to our website and helping our team to understand which sections of the website you find most interesting and useful.
We use tracking pixels that set your arrival time at our website, this is used as part of our anti-spam and security measures. Disabling this tracking pixel would disable some of our security measures, and is therefore considered necessary for the safe operation of the website. This tracking pixel is cleared from your system when you delete files in your history.
With its presentation of an EcoPower 180/750+ B8X DC machine, WITTMANN BATTENFELD France will demonstrate to its visitors the WITTMANN Group’s expertise in the field of utilising renewable energies. This machine, operating with a solar power storage unit, is also equipped with a WX142 robot in DC version.
We manufacture bioplastics from the hurd and cellulose of the hemp plant. Hemp bioplastics are biodegradable, and take up to a maximum of 6 months to completely decompose; by contrast, normal fossil-fuel-based plastic takes up to 1000 years to decompose.
Energy measurements using the IMAGOxt software will be carried out on all injection moulding machines shown at the WITTMANN BATTENFELD booth. IMAGOxt, a program developed by WITTMANN Digital, will be used to display the energy consumptions of all injection moulding machines exhibited at the fair, and the auxiliaries connected to them. The program also calculates the CO2 consumption. All values calculated can be recorded in quality reports and thus remain available for long-term analyses. IMAGOxt is available as a web application, as an optional extension of the WITTMANN TEMI+ MES system, or as a stand-alone program.
The SmartPower B8X to be presented comes equipped with all-electric injection units, thus combining the advantages of the servo-hydraulic SmartPower’s flexible, generous mould space with the all-electric EcoPower’s excellent performance and high precision.
We have a project we are working on and are currently employing consultants to work up our methodology the project is based on a circular economy model I would like to connect and discuss some Ideas that your article has Inspired, we see Africa as a truly magnificent opportunity to change things right now and sequestering carbon in the process.
With an increasing number of nations banning non-biodegradable and petroleum-based plastics in certain uses, the choices at hand have naturally led to bioplastics. Bioplastics are a major ingredient of the renewable packaging industry. We derive them from various renewable agricultural crops, of which hemp is among the chief examples.
Rick where are you based? I am presently living in Malawi where I believe the cultivation of industrial hemp would be a game changer. I would like to think that much of the plant matter could be used for sustainable packaging or similar and need to engage with persons who may be able to assist.
The future of packaging is ripe for capitalization by the drivers of sustainability culture. With the battle lines drawn and forces at play in motion, change is now inevitable. The question arises: how quickly can the industry grow in the space of the next decade?
This is a substance found in plant cell walls. We use cellulose to manufacture a broad range of unique plastics, including celluloid, rayon and cellophane. These plastics are usually entirely organic. We mix cellulose and its variations (such as nanocellulose, made from cellulose nanocrystals) with other ingredients, such as camphor, to produce thermoplastics and the like. Using natural polymer, we process a broad range of bioplastics and corresponding polymers. The difference in their chemical properties is down to the nature of the polymer chains and the extent of crystallization.
The range of dryers on display at the FIP will include a Drymax primus und a Drymax plus dry air dryer, as well as a Card primus compressed air dryer. The dry air dryers from the Drymax series are each equipped with two desiccant cartridges and therefore deliver a continuous flow of process air with consistent dry air quality for perfect drying of plastic granulate. The Drymax plus offers high operating comfort with a generously dimensioned touch display panel. Card compressed air dryers are small and effective and ideally suited for simple drying applications directly next to the machine’s feed zone.
From its range of robots, WITTMANN BATTENFELD France will exhibit at the FIP a WX138T with AC servo axis and a Primus 128 model with the new R9 robot control unit. With its control cabinet flange-mounted to the horizontal axis and its internal power chain, the WX138T is particularly suited for compact production cells. It is driven by toothed belts to reduce its operating noise to a minimum. The Primus 128 for pick-&-place applications offers a robust axle design thanks to its vertical Y axis supported by a steel profile. A lubrication system for the vertical axis included as standard ensures a continuous supply of lubricant and consequently quiet operation of the drive system with minimal wear.
Very thoughtful article indeed. I am looking for making hemp products like food additives, medicinal CBD and packaging material as a replacement of non-biodegradable plastics. Can you please guide me to get raw materials and some process plants for such hemp raw materials?
A composite of polypropylene (PP), reinforced with natural hemp fibers, showed that hemp has a tensile strength akin to that of conventional fiberglass composites. Furthermore, malleated polypropylene (MAPP) composites, fortified with hemp fibers, significantly improved stress-enduring properties compared to conventional fiberglass composites.
Why is the crop unanimously superior in the aspect of eco-friendliness? Its growing requirements are frugal: water, soil nutrients and pesticides are not needed in large quantities. It absorbs great quantities of carbon dioxide from the atmosphere, and uses it to create 65-75% cellulose content within its biomass. Cellulose is vital in the manufacture of bioplastics. Hemp is also flexible within crop cycles, due to its small harvesting period of only 4 months.
We have already generated several bioplastics entirely from natural plant substances like hemp. Hemp fibers, when made alkaline with diluted sodium hydroxide in low concentrations, exhibit superior tensile strength. We have produced materials from polylactic acid (PLA) fortified with hemp fibers. These plastic materials showed superior strength than ones containing only PLA. For heavy-duty packaging, manufacturers use hemp fibers reinforced with biopolyhydroxybutyrate (BHP), which are sturdy enough.
Greetings Vishal. I am currently at the early stages of setting up large scale natural soap and cosmetic production in Gambia, in collaboration with Gambia Environmental Alliance. The objective is, among other aims, to obsolete imported plastic packaged – chemical laden commodities, which are at present an insidious threat to the environment ( as with all other countries ) where there is close to zero contingency or infrastructure to deal with the growing problem. We are currently at the R&D stage and among other things are seeking cost effective packaging solutions. We are aiming to make our products exportable and thus create industry and employment as well as garnering support from The Gambian Ministry etc. Ideally packaging would also be manufactured in The Gambia. I would be very grateful for you advice and direction.
Thus, farmers use it as a rotational crop, allowing them to also cultivate other crops after its harvest. High-quality crops like cotton, though superior in cellulose content and fibrous softness, require far more water quantities, soil nutrients and pesticides. Farmers face greater difficulties in cultivating cotton as a rotational crop, because it requires far more space and time.
Furthermore, WITTMANN BATTENFELD France will exhibit a selection from the WITTMANN Group’s range of materials handling technology. In addition to central conveyors and stand-alone conveyors, such as the Feedmax S3 net, the exhibits will also include the new Feedmax Clean with dedusting function, which has been specially developed in response to the more and more stringent demands of the circular economy and the resulting increase in plastic granulates containing dust. The program will be rounded off with an XMB filter station and a Codemax RFID-controlled coupling station, which in combination with the M8 network control system ensures correct material feeding.
A further highlight of the presentation will be a selection from the range of granulators manufactured locally at WITTMANN BATTENFELD France. The exhibits will include G-Max 9 and G-Max 23 grinders as well as the screenless granulator models S-Max 2 and the new S-Max Dual 6. The S-Max Dual 6 is the ideal granulator for central grinding of reject parts, but it can also be used for in-line recycling of sprue from injection moulding machines. For use beside the press, the footprint of the S-Max Dual 6 has been reduced by about 25% compared to its predecessor model.
The future of packaging is ripe for capitalization by the drivers of sustainability culture. With the battle lines drawn and forces at play in motion, change is now inevitable. The question arises: how quickly can the industry grow in the space of the next decade?
I would like to see a hemp based compostable baby diaper. If it were to compost naturally, it could be used as fertilizer. Currently pampers, huggees, etc. will be around long after the baby and his or her decedents have passed. These diapers are also very expensive. There is a huge market for baby diapers. With water shortages, washing cloth diapers is not a great option. I think hemp offers a great alternative to plastic based diapers.
Farmers are now able to cultivate the plant in the U.S., due to its removal from the list of controlled substances. Agribusinesses and manufacturers are aware of the plant’s versatility, with uses in packaging, building construction, clothing, medicinal oils, edibles like protein powder and hemp hearts, hemp paper and rope. What was once George Washington’s strong consideration as a cash crop for his estate, may gradually become the world’s cash crop of choice.
We call any natural polymer, when blended with synthetic polymers, a “bio composite” plastic. We measure and calibrate these ingredients according to the desired stiffness, strength and density of the eventual plastic product. Apart from packaging, manufacturers use these bioplastics for furniture, car panels, building materials and biodegradable bags.
If you disable this cookie, we will not be able to save your preferences. This means that every time you visit this website you will need to enable or disable cookies again.
From the segment of temperature control technology, one temperature controller from the Tempro basic series will be presented at the FIP, plus a single-circuit and a dual-circuit appliance from the Tempro plus D series. The features of auxiliaries from the Tempro plus D series are their comfortable touch control units and optional extras such as utilisation-controlled pump regulation with EcoDrive. In addition, WITTMANN BATTENFELD France will show a selection from the WITTMANN portfolio of flow controllers. A WFC 120 flow regulator will also be on display. The WFC is an appliance to control both flow quantity and temperature. It comes with a maintenance-free flow measurement unit.
Finally, WITTMANN BATTENFELD France will provide tangible evidence of the WITTMAN Group’s expertise in dosing technology by showing a volumetric Dosimax MC Balance blender and a Gravimax primus 14 blender with real-time weighing.
With the American hemp industry on the verge of a revolution, hemp packaging is primed to take over a significant part of the global packaging sector. The political, economic and environmental incentives for companies to adopt bioplastics are legion. Its lower cost lends to its allure as well. Consumers and agribusinesses are following suit, making the choice to be environmentally-conscious. By 2030, it is estimated that 40% of the plastics industry will be bioplastics.
This message is for Author Vishal Vivek. Mr. Vivek, I would like to speak with you regarding how we can work together to bring hemp into the global marketplace and protect and reward the people doing the work. Please send me an email or text so we can arrange a time for a phone conversation. Thank you! Duane Stjernholm Co-Founder and Operator Colorado Hemp Processing Cooperative 303-525-2611
Moreover, WITTMANN BATTENFELD France will also demonstrate its expertise in micro injection moulding by showing a MicroPower 15/10 specially designed for this type of application live in action. With this machine a micro retaining ring for medical miniature tubes will be produced from PC with an 8-cavity mould supplied by Wittner, Austria. This product has a part weight of only 2 mg. The machine comes with a rotary unit, an integrated WITTMANN W8VS2 robot and a camera for complete parts inspection. Following removal and camera inspection, the parts are transferred to transport containers, separated according to individual cavities.
Vishal Vivek is the CEO and Co-Founder at Hemp Foundation. Hemp Foundation’s mission is to fight global warming, plastic pollution, deforestation and wild species extinction through promotion of hemp in fashion industry and at the same time provide jobs to marginalized communities of artisans and farmers in rural Himalayan villages and give them global reach.
Thank you very much for this great article! I would love to talk to you Mr. Vivek and ask you some questions as I am currently writting my Bachelor thesis ( at ZHAW Switzerland) about how hemp could be used for packaging material. It would be very helpful to get in contact with you (sent you a request on LinkedIn). Kind regards Dominik
The robot receives its energy supply directly from the DC intermediate circuit of the EcoPower and also returns any surplus energy derived from axis deceleration to that circuit. On this machine, a crinkle box made of PP will be manufactured using a single-cavity mould supplied by the Austrian company Haidlmair. The power supply for the machine will come from ultra-modern ecological salt battery technology on sodium-nickel basis supplied by innovenergy. The battery has a total capacity of over 45 kWh, more than sufficient for continuous operation of the machine during an entire 8-hour trade fair day. To compensate the injection moulding machine’s short-term load peaks, additional electrochemical capacitors known as super-caps are used to complement the sodium-nickel storage units.
Composite plastics comprise organic polymers like hemp cellulose, as well as an addition of synthetic polymers. They also have reinforcement fibers to improve the strength of the bioplastic, which are also either organic or synthetic. Sometimes, we blend hemp cellulose with other organic polymers like shellac and tree resins. Inorganic fillers include fiberglass, talc and mica.
Manufacturers incorporate these ingredients into existing manufacturing processes for regular plastics, such as injection molding. Thus, we can apply bioplastic ingredients to similar plastics applications, such as packaging, paneling, medical equipment and more. New technologies aren’t necessarily needed, so companies and manufacturers do not have any reservations about its viability as an industry.
We can only mitigate the plastic pollution in oceans, landfills and elsewhere, with the use of biodegradable bioplastics; otherwise, animals, humans and plants are getting adversely affected by imperceptible microplastics that pervade vast regions of the Earth. With hemp bioplastics, we use the cleaner, renewable matter of plants to conserve the planet’s sanctity. We can expect this new technology to continue to light the way for other nations, societies and companies to build upon this sustainable plan.
In addition to the robots and auxiliaries connected to the machines on display, a number of stand-alone solutions will also be shown at the FIP.
Fossil fuel-based plastic polymers are non-renewable, highly pollutive and dangerous to ecosystems, due to their lifespans. They are some of the most destructive inventions of man, but thankfully could be held back by this crop. Industrial hemp upheld countless industries through human history and now is making a comeback. After existing in relative obscurity in the U.S. due to false connotations with the psychoactive properties of its cousin, it is now back in business.
At the FIP Solution Plastique 2024 in Lyon to be held from June 4 to 7, WITTMANN BATTENFELD will present ultra-modern injection moulding technology, automation and auxiliaries to trade visitors.
The legal ramifications of the European Green Deal and the American Farm Bill of 2018 have created a microcosm where the sustainability discussion has turned into corporate initiatives for crops like industrial hemp, which are a source for bioplastics and numerous other products. The smaller carbon footprint of industrial hemp plays its role in shaping consumer demands towards a greener future.
With the world in a state of major change due to the coronavirus outbreak of 2020, the focus is back on packaging and delivery. In this volatile area, perhaps the industry can learn a few new tricks, instead of suffocating itself in old traditions and superficial opportunism. The permutations and combinations of bioplastic technology can serve a swath of packaging applications. We must thoroughly explore this technology.
Very informative read here. What I’m wondering is would it be possible to have large drums for use in manufacturing, that would hold a variety of different liquids. Has there been much investigation/ research done for this? Would love to hear your thoughts. Michellebrady47@hotmail.com
Multi-component technology expertise will be shown as well, by the production of a bottle opener made of PC and TPE on a SmartPower B8X Combimould, using a mould supplied by FKT Formenbau und Kunststofftechnik, Germany. The SmartPower B8X 120/350H/130S is presented as an insider solution with a W918 robot from WITTMANN and a conveyor belt integrated in the production cell. The robot takes the prepared metal parts from a magazine and places them into the mould, where they are insert-moulded with polycarbonate. A rotary unit subsequently turns the resulting base bodies into position and passes them on to the second station, where they are over-moulded with TPE to provide them with a better grip. The finished parts are then deposited on the insider cell’s conveyor belt.
Greetings Sir. I sm the cofounder of Tradewinds Hemp est 1990. We have allways featured biodegradable plant materials in our packaging as a proponent of full circle sustainability in all our work. We have projects and consulting relationships in the Us several other countries and Indigenous comunities, focused on sustainable development in agriculture and related manufacturing. We are always looking for new development partners and collaborative relationships with like minded forward looking groups and individuals. Thank you for all youre work. Please feel free to contact me. Richard Kiyak-Boughton Tradewinds Hemp Green Goddess Organics Tara Pharm rickkb88@gmail.com 541-543-0624
GETTING A QUOTE WITH LK-MOULD IS FREE AND SIMPLE.
FIND MORE OF OUR SERVICES:
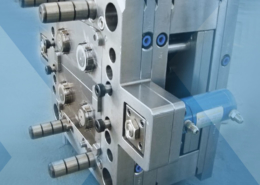
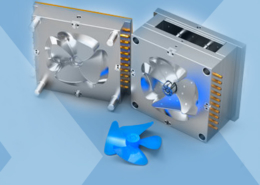
Plastic Molding

Rapid Prototyping
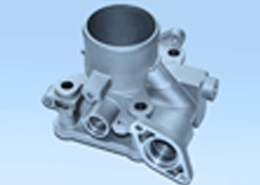
Pressure Die Casting
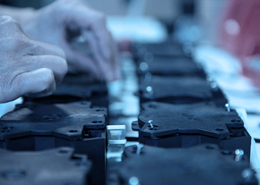
Parts Assembly
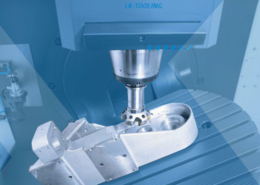